Advice: can’t afford a “building science”/PGH GC for new construction

Hey all,
My family is beginning a new construction project. We’re contacting architects + GCs in the metro area, and getting a really high price-range discrepancy between the local, non-“building science” GCs and the energy-efficient-focused GCs. Local people are saying they can build houses, where depending on the finishes, start at $220-250/sq ft. The cheapest energy efficient GCs say they *start* at $400/sq ft.
I’m mind-blown by this difference. I’m familiar with the work of these local GCs, I’ve been in homes they’ve built and they’re nice custom homes. As far as I can tell (which isn’t a lot), they do nice work and aren’t cutting (too many?) corners.
Anyways, I’m trying to figure out if there’s a way that I can get a building-science-minded architect and give the plans to a local builder that has no experience doing anything more than code requires. I’m scared that we’ll end up with an expensive, leaky, mold hazard, unintentionally rotting home.
If I knew enough about building science, I’d say I can just supervise the project, but I’m too ignorant.
Any advice about PGH type of improvements that can be architected for “normal” GCs to build that will be 1. worth the increase cost, and 2. is something they’d be able to do without investing much time learning about building science?
Edit: I’m located in MA!
GBA Detail Library
A collection of one thousand construction details organized by climate and house part
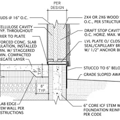
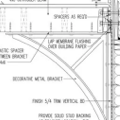
Replies
Where are you located?
I think many aspects get subjected to overthink.
1. For exterior walls, go with either double/stagger stud or exterior insulation. Both are well proven and relatively easy, the details are worked out.
2. Get the house energy modeled to size heating appliances and work out other details.
3. Get a mid construction blower door test to help pinpoint air leaks.
4. Most importantly, keep the design simple vs complex.
There is no reason why a PGH should cost $100/sf more than a "standard" build. I have several houses locally that are modest 3 bedroom ranchers that are hitting passivehouse levels of air-tightness, the builder figures the extra details cost about $3000 all in.
Depending on the local builders, a "standard" build may be very good.
Located in MA.
Thanks for the suggestion of exterior insulation. Is that something an PGH-aware architect should design, or a non-PGH-aware builder can easily figure out for themselves?
Also, is there a risk to the building being airtight if the builder does not usually build airtight homes? Is there increased chance of them mishandling something such that it turns into a moldy mess?
Wow, only $3000 extra is crazy, thanks for sharing. Really good for me to here because I keep hearing from people that "energy efficient is sooo much more money".
You need to talk to the builders and tell them what you want and see how responsive they are. The thing to look out for is guys who are used to doing things a certain way and won't budge from that. It's just a recipe for unhappiness trying to get someone to do something they don't want to do. You can't be there all the time and a lot of the details are hidden. When I was interviewing people for my most recent house I had a very frustrating discussion with one guy, I kept saying I wanted to make it highly efficient and he kept saying, "the new codes are really strict, you don't have to do anything more."
I think the most you can hope for is someone who says something like, "I'll do what you want if you provide me plans." What he is in effect saying is he'll do it but doesn't want to take responsibility, by working off of plans the blame falls on someone else if there are problems with inspection or down the road.
Yeah, there are a couple of GCs that say they'll do whatever I hand them. But they're lacking context and don't necessarily understand the motivation behind the decisions or the consequences of deviating from them. So I worry about how easy is it for the builder to accidentally introduce a mold-problem if they mishandle a tiny detail.
I feel your pain! I was in the same boat and refused to pay an enormous upcharge just because I wanted extra insulation with detail to sealing. I couldn't find anyone in my area to build to my demand and I refused to pay the current price for a conventional, leaky, cheaply built house with low performance products. It has been my lament for a couple of years. I had no choice but to build myself. This was a painful prospect because I am not a builder and I am employed full-time. Many days can't make a single bit of progress. The thought of installing triple pane flangeless windows intrigued and almost scared me. Although I am not a builder I somehow manage to reach my goals regardless of the challenges I set forth to achieve. Progress is very slow and many times very frustrating but I find the experience equally rewarding. There are times when I feel like I'm not making any progress for weeks on end but then I look back at how far I've come and it's all worth the effort. I started building in May and I'm still not done siding, but I know it won't take much longer. Little by little, nail by nail, piece by piece, my goal is to create a watertight weatherproof insulated exterior and finish the interior as I am able and time allows. I decided to live in a barn and off of rainwater for a year to make ends meet and enable my venture which you may not willing or able to do but I guess my message to you is a message of encouragement if you have moderate building skills and can find time to think about doing the build yourself.
Feel free to follow along as I complete my build: https://www.youtube.com/watch?v=ZnVxPy4OwLU
We are doing the same. We couldn’t find anyone who was willing to get us what we wanted so we are GC-ing the whole construction. We are still hiring subcontractors and trades for things we cannot do such as electrical, plumbing, siding, but we did a lot of the work ourselves - capillary break on the footing, under slab insulation with poly, air sealing top/bottom plates/electrical outlets, gaskets on all exterior penetrations. Also since we are in charge of subcontractors, it’s easier to dictate our specs to them than GC, plus we are in charge of sequencing/scheduling things in order they supposed to occur, which is a big plus. I won’t lie, even after we told the trades how we wanted things installed, there has been still few really bad mistakes that we needed to undo/redo, etc. For example, the siding contractor who installed our windows calked all bottom flanges when I was not looking, so I had to undo all of them. It has been a lot more work than we ever anticipated but we wouldn’t change a thing.
Wow, I admire both of you. With very young kids and my spouse and I both working full-time jobs, I don't think we can pull off GCing our own house, but in theory would love to do that.
Doesn't surprise me in the least.
I live in an affluent area of New Jersey and I suspect 1 out of 100-1,000 "general contractors" could have executed my build.
The selection bias that comes from talking to people here is that we tend to focus on the question "What is the up charge for an otherwise completely competent and capable builder to execute BS/PGH details?" That $number is relatively small. In the real world, however, the question you're actually asking is "What is the up charge for a barely-able-to-keep-their-license, seat-of-their-pants builder to execute BS/PGH details?" And the answer for that easily explains the $100/ft^2 premium.
Exterior insulation is really very easy and fairly foolproof. I had my builder build what he normally builds, then we added the window bucks and insulation.
He hasn't said where he's located. Where I am, asking for exterior insulation is equivalent to asking to help launch a satellite into space.
Exactly. Where we are, people don’t install exterior insulation. On that rare occasion when they do, it’s only a rigid foam and we wanted Rockwool ComfortBoard. All contractors we interviewed looked at me like I have two heads. One proposed to cut the exterior mineral wool and insert it between the furring strips :-) He didn’t get the job.
egg2,
Getting your architect to use efficient but conventional construction assemblies and details most contractors are familiar with would be good start. Things they haven't done before, or that disrupt the regular sequence of construction, are always going to be problematic. So choices like where the air-barrier will be, or of a wall assembly that requires completely different flashing of any openings, are best done with the contractor's skills and experience in mind.
That’s a very good point. We asked our architect to include raised heel in the attic for more insulation, and our conventional framer had no choice but to execute that. Yet, he had issues with California corners (we only got some framed as California corners and some I don’t even know what he was thinking). But starting with a good architect is excellent advice.
+1
Designing in the PGH details so no matter how it will be built you end up with better than code min.
Along with raised heel roof trusses another simple change is going with 2x8 24" OC framing with R30 HD batts instead of 2x6. This adds a bit of lumber and insulation cost but it is standard build detail. Much easier to build for any trade that is not used to double stud or exterior insulation.
It is a shame this is so hard. The details you have to get right are not that hard but seem to be a challenge.
For example, there is a new build down the road from me that I notice while walking the dog. Looks like somebody tried to design it right but even then are not installed improperly.
Simple things. Somebody knew what they were doing and flashed the window sill properly, peel and stick with a flap of tyvek under the bottom section it so it can go over the house wrap when installed. The house wrap people come along and wrapped the whole house in house wrap, right over this flap instead of under it and over the whole peel and stick. So now any water leaks get nicely channeled between the house wrap to the sheathing bellow.
To make the problem worse, they tried to do a good job by wrapping the sides and top of the rough opening with peel and stick. On the top, the peel and stick want right over the house wrap instead of under it creating a reverse lap. Any water leaking down the house wrap now gets nicely channeled between the peel and stick and framing. The peel and stick they used is vapor closed, so any water leaks have nowhere to go and will stay there.
Into this they than installed some pretty nice tilt and turns. Once it is all covered up nobody will see it. If the siding install isn't perfect, I'm sure the new owners won't even know until they have issues a couple of years down the road.
Such a shame, it would have taken less effort to get it right than what was put into getting it wrong.
You have just described 98% of the construction in the US.
MOST things are done incorrectly. And even if you hire the subs, when you ask/tell them how you want it done, at least 50% of the time they nod in agreement then do it exactly like they have done it for 30 years. Unless you can stand there all day and supervise, you won't get it done like you want.
Your best bet is to find a small and smart builder willing to learn. They are few and far between.
Whatever you do, YOU need to hire an independent firm to do the blower door test. And write a specific ACH the builder must achieve into your contract. Depending upon how long you plan to keep the house, I'd also hire a firm like Energy Vanguard to design the HVAC and then get someone working for you to inspect the HVAC install to confirm it is per specs (the builder and the building inspector won't do this). I'd also hire a waterproofing consultant if you don't know what to look for.
What part of the country are you in?
Thank you! We're in MA.
I don't know what the prices will be but I would speak with manufacturers of prefabricated panels or prefabricated homes that are focussed on PGH and energy efficiendy. Bensonwood is one example but you could also ask them for other companies.
https://bensonwood.com/
I heard an interview with the owner and he said that they are part of such a small community that they don't compete but rather support each other.
Denpending on the company, some (I understood) actually offer intall options. I don't want to cause you to waste your time but I am a big believer in pre-fab.
With a site build, you end up having a longer process with lots of time to change your mind. With pre-fab, so much more of the detailed planning goes on up front and while the initial price looks higher for prefab, my opinion is that site build just offers to many unknows that often end up driving up the price. In a time of higher inflations, you are price protected to a larger degree with a prefab.
It is not for everyone, but it is an option to consider.
Thank you so much, this is a great idea. I love the idea of prefab panels and having the experts assemble the envelope, leaving just the interiors to my GC.
I'll reach out! I hope it's affordable.
I would talk to all of the companies to get information on cost. Also ask them what you can do from a design perspective to keep costs down (e.g. keep roof really simple, build a box meaning a rectangle or square.
Also, remember that you get much better up front planning (most often) with a prefab that saves you money over site build and it saves time - which is really money in this inflationary period.
Site building often leaves many “unplanned “ and one example is plumbing and electrical details.
Don’t underestimate the cost of the finishes both exterior and interior walls and roof.
You can get really good casement windows without buying European windows.
Having vinyl siding is simple but durable (except heavy hail).
A metal roof is nice but … a typical asphalt 3tab roof, ice shield around the edges, having a good underlay, 5/8” cdx deck and all taping seams of decking and screwing decking, using hurricane ties on the trusses.
Thank you!
I was looking at their wall assembly example, and it honestly doesn't look that promising to me.
Interesting, what about it concerns you?
For the passive house assembly: https://bensonwood.com/passive-house/ ("the website")
https://storage.pardot.com/747593/1662483792iaKfjcnQ/Tektoniks_Enclosure_Systems_2021_Modified.pdf ("the PDF")
On the website, the example configuration is quite vague. This is to some degree a good thing; it means that there's some allowance to design to the site conditions.
However, if the purpose of going prefab is to save money, incurring additional design fees is not congruent. There are well known examples of assemblies that work in all climates. That said, maybe these are ignorant assumptions, and actually the cost of design fees is less than paying for an overbuilt assembly if you are in a milder climate, or paying for excessive operating costs if you are in a more severe climate.
On the website and in the PDF, the default configuration uses OSB as an air barrier which has been shown in the past to not be consistently airtight, depending on the production run. Most of the time it will be fine, but other times...you will have to go back and adhere a membrane to it. OSB is cheaper than plywood though.
On the website and in the PDF, the default configuration shows another insulated service layer because of where they've chosen to locate the air control layer in the assembly. This is not congruent with saving money. Now, one reason why they probably put that service layer in is exactly because of what you described "the experts assemble the envelope, leaving just the interiors to my GC" -- the GC has to try that much harder to disturb the critical parts of the envelope when running services.
In the PDF, the PHlex wall is specified with SIGA Majvest, which relies on a physically microporous structure, i.e. millions/billions of tiny holes to achieve vapor permeability, whereas there are other products use solid ("monolithic") materials that transport moisture via diffusion.
This is not to say that microporous membranes are bad! The key is, why would you specify a microporous membrane on your more expensive assembly, and then confusingly, use a monolithic diffusion membrane such as the fluid applied membrane on the ZIP system on your less expensive assembly? And if the image in the PDF reflects SIGA's branding accurately, why would you put a mechanically attached membrane, which are generally less durable and forgiving, on your more expensive wall assembly, especially when it's something that will be riding on transportation? https://www.youtube.com/watch?v=P51q0XdZ1WA this guy had issues with falling pine needles causing leaks in his mechanically attached monolithic membrane. Will the panels hold up to things like lightweight road debris?
Finally, one theme that seems to ring true across a lot of prefab factories is this approach where they put an air control layer inside, and then basically shove a cavity of dense pack cellulose which may or may not be load bearing outboard of the air control layer as the exterior insulation. I speculate (probably out of ignorance) that there are two reasons for this: 1) it holds up in shipping better than something like foam, mineral wool, or wood fiberboard exterior insulation and 2) it's cheaper than using any of those as exterior insulation.
And then they put an insulated service cavity inboard of the air control layer, and it really starts to look a bit like a double stud wall where the load bearing wall is outboard instead, and with extra steps. It's obviously not exactly equivalent, but that's the impression I get.
The question is, do the cost savings of building these types of assemblies get passed on to you? Or are they doing this because they know your average local GC couldn't build you something better, and so they're taking profits where they can because you're basically a captive audience? I hate to be so cynical about this, but it's weird to see marketing materials espouse the latest and greatest in building science and then come up with objectively less forgiving assemblies.
The biggest differences I can see between what they've done and what your average contractor may or may not be able to do:
1) detail the water control layer correctly (whether it's ZIP or Majvest)
2) detail the air control layer correctly (the inboard OSB)
It seems like you were pretty confident a local contractor could do these two things--have them build you a double stud wall, while understanding that this is one of the least forgiving high R-value assemblies if you mess up either of those two details. Also note: double stud walls aren't bad! They are just heavily insulated enough that if bulk water gets in from the outside, or air carries water vapor into the insulation cavity from the inside, it might take a very, very long time to dry out, which is a problem when your structural members are also inside that cavity. There was some controversy over whether or not a double stud wall might also have internal condensation issues after several years, but I don't know what the consensus was on that.
Finally, if something does go wrong: who pays to fix it? The prefab factory or your GC?
BTW, I really hope someone comes along and corrects me, because I am definitely not a professional, nor do I have a lot of experience.
There are many definitions of green building, but for carbon emissions, avoiding a fossil fueled heating appliance in MA is the most impactful change you can make, especially if it's a heat pump paired with renewable energy, either on-site or off.
Paul,
What is currently the generation mix for your grid electric provider.
Thanks,
Doug
It's about average: around .7-.8lbs/CO2 per kwh if I remember correctly. Since I'm in PJM, that makes sense, it's an extremely large grid operator. It's maybe 25% coal, 40% gas, with the balance being nuclear/wind/solar/etc. I buy wind and solar energy (for a discount even!), so it's a bit moot.
From the EIA:
"In 2020, total U.S. electricity generation by the electric power industry of 4.01 trillion kilowatthours (kWh) from all energy sources resulted in the emission of 1.55 billion metric tons—1.71 billion short tons—of carbon dioxide (CO2). This equaled about 0.85 pounds of CO2 emissions per kWh."
Since the most efficient gas appliance can only get to ~115lbs/MMBtu, a heat pump using the average pollution rate only needs a COP of 2.17 to match the best possible gas appliance. I think I'm closer to a COP of 3 with a not especially efficient heat pump which is about 28% cleaner than the best gas appliance so it's not really close anymore. Obviously, as more coal retires, the gap will widen even more.
Great information, thank you. Hopefully the greening of the grid becomes a priority with climate impact statements from electric providers readily available. I think most people want to do the right thing when upgrading or choosing new equipment, we need reliable information in advance.
For sure! The math strongly favors heat pumps now - it's borderline fraud for any furnace/boiler to be labeled "high efficiency" anymore.
You may also want to look at a "building science" option that is very very simple and can be built in any climate with a 2x4 wall.
If you have not already, you can read about "the perfect wall" here.
https://www.buildingscience.com/documents/insights/bsi-001-the-perfect-wall
You can see an example on this Youtube video (there is a series), but this uses some materials like ZIP and self adhering membrane that are not necessary for the perfect wall. You will see that the design of the house is super simple.
https://www.youtube.com/watch?v=hTwq-qUnr9I&list=PLDYh81z-RhxgCk1qJD6AJktVHZH7-BLSR
As you alluded to, a big part of what you want is an air-tight envelope and as someone else suggested you can address this with a blower door test mid-construction. You can choose to havea an exterior air barrier (including roof/ceiling) and have the blower door test once the sheeting is completed and windows are installed.
Where I work (Portland, OR), I often see that same price difference, except conventional builders are in the low $300/sf range, and high-performance builders are $500+/sf.
Some moves that were pretty successful on a recent project that we wanted to get some high performance features on from a GC who didn't have a lot of high-performance building experience:
Walls: 2x8 @ 24" w/ dense-pack cellulose. This was a small boost in performance, while allowing construction to be very conventional.
Roof: Doing R-60 instead of R-49 in an attic is easy
Air sealing: We had initially specified using taped sheathing as the air barrier, but we ended up doing Aerobarrier https://aeroseal.com/aerobarrier/ and I think that's a really good system for a contractor who doesn't have a lot of air sealing experience to achieve good airtightness. We did aerobarrier after drywall due to scheduling reasons, which makes the drywall the air barrier, but you can also do it after rough-in to make the sheathing the air barrier.
HVAC: specifying high performance heat pumps and an HRV is pretty straight forward. You need to work with the GC and mechanical subcontractor to make sure the duct routing is all in the conditioned envelope, but mostly it's doable with conventional subs.
Windows: specifying a better-than-code window is straightforward.
The other thing to take a look at, is to make sure that your architect includes construction administration in their contract. Talk with them about how to best manage the construction process. Share your concerns. How many site meetings make sense? What's the process for reviewing questions from the contractor? What are the key details that the architect, contractor and subcontractor should talk through on site? The architect's work doesn't have to (and usually shouldn't) end with handing the contractor a set of drawings. This all costs money, but if you're trying to get a high performance home from a conventional builder, it's probably money well spent.
I will also recommend AeroBarrier. I recently had it done, it was $3500 for a 4400 sf house, we did it after insulation and drywall but before trim and paint. It got the blower door down to 1.4 ACH50 on a house where I just couldn't get the framing contractor to care about air sealing when I wasn't looking.
This is great advice.
Brendan, thank you so much for the thought out and detailed reply. I'm taking this to heart and I'll try to do it all.
If it helps, having the air barrier as inboard as possible in a cold climate is probably the most ideal.
I am in Mass as well and my challenge now is to figure out exterior insulation. Here is how it is coming:
I just rented a uhaul to obtain 2" reclaimed polyiso boards for cheap in Framingham, then I looked up fasteners for them and found a product from Kamco Supply Corp called Windlock 2" Wind Devil Plastic Washer with 2 3/4 inch aluminum screws. Finally I am planning to get zip system r6 and some 1 inch polyiso from Beacon Roofing Supply and some Rock Wool Comfortbatt from Concord Lumber. And some additional screws of different lengths.
It just so happens that you can't go to Home Depot and get the best products or the best prices on this stuff and so your contractor is unlikely to spend as much time as I did to determine where to get the components needed.
Basically what I am suggesting is that you might be the materials needed then for your wall construction (maybe I could make a few "kits" and send them around) and then that becomes a real thing not a pie in the sky architect's design.
wish me luck however, this is my first attempt at exterior insulation!