Advice on an old house’s insulation plan

Hi All,
I’ve been soaking up the knowledge here on GBA for the past few years in preparation for insulation my house. This week I finally made some calls, and today I got a quote back from a contractor. I wanted to get some insight before I pull the trigger on this project because I have a few concerns.
Some background: I’m in climate zone 4, in the mid-Atlantic. The house was built around 1900, balloon framed, stone foundation with an original slate roof. Siding is building paper->1×8 sheathing->cedar shingles-> vinyl siding on top of that. House has zero insulation except for some old worthless batts placed sporadically in the attic by a former owner. We got a score of 8,000+ on the blower door test for an 1,800 sqft house… Maybe I should go live outside instead- it’s a lot cheaper and just as warm.
After pouring over this site and others for far too long, I was certain that I wanted dense pack cellulose in the walls given its capability to handle fire, insects, and moisture. Further, my wife and I plan on finishing the attic eventually, so I wanted to move that area inside the building envelope now while we’re insulating the rest of the house to maximize the rebate program through our utility company.
That was my intention, but here’s what the contractor came back with:
1) Open cell sprayfoam straight on the roof deck (1x8ish skip sheathing, actual 2×6 rafters). Specs say ‘Random Fill’ to 8.5″ @ R-30
2) Open cell against the gables. 3 1/2″ to R-13
3) ‘Top plate’ install rigid foam ‘fan-foil’ and seal seams
4) Exterior walls get drilled and filled for fiberglass
-Needless to say, I’ve got some concerns. First, open cell foam directly against a slate roof sounds like a disaster. Where will the water go if (when) the roof leaks? How will slaters change out a busted slate that’s stuck to foam? I told them to spec me baffles that can drain to vented soffits but am waiting on a response.
-Next, does open cell foam need a vapor retarder or barrier in my climate zone? It gets quite cold here in the winter and I imagine all of the warm interior moisture finding its way to the cold roof deck would be a bad thing. They didn’t seem concerned when I brought that up, and I could be way off base here.
-Lastly, given that it’s balloon framing, I though cellulose would do a good job of reducing air movement in the giant chimneys that are my exterior walls, but they quoted fiberglass. To be fair, some of the plaster is in poor shape and the contractor was worried about blowing the walls out, so I get it. Will fiberglass do OK in place of cellulose? Anything I should worry about with that?
Sorry this got so long but there’s a lot of detail I want to get right. It’s a lot of cash for us and, more importantly, I don’t want to do damage to the house.
Any insight is appreciated!
GBA Detail Library
A collection of one thousand construction details organized by climate and house part
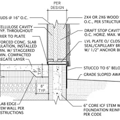
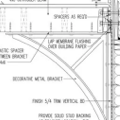
Replies
DIY opinion: guessing you'll get more pro opinions too.
1. If you have 2x6 rafters and want to finish that space eventually, how will the contractor achieve 8.5" of insulation depth? Are they going to fir down the rafters? If so, will you still have the head height needed to finish the attic? If you can only achieve 2x6 depth and are installing an air/vapor barrier anyways, why not consider a batt product that offers a higher R value (mineral wool)
2. What possible advantage does open cell foam offer for the gable ends, other than the contractor is already there and can spray more square footage? Surely a batt product here is adequate. I assume you need to add outlets or other penetrations at a later time, to finish the attic and I assume it will be easier to retrofit in the presence of batts than sprayed foam.
3. Presumably you have knee walls height balloon framing in the attic (otherwise, I can't imagine you have the head room to finish the space). Or do you actually have top plates at the level of the attic floor? What is the contractors plan to block the balloon framing air travel pathway? It sounds like he wants to use rigid foam for that? #3 in your list? That seems like an odd solution. Why not install actual wooden blocking? Is there something I don't know about moisture management in balloon framed walls?
4. If you have this much air traveling through the house, I would be very concerned about blowing fiberglass into the cavities. While the industry generally regards blown fiberglass as safe, are you certain that your very leaky house won't allow the fiberglass to enter the house or ducting (you don't say what heating system you use)? A lot of people are pretty sensitive to fiberglass, especially as it degrades. I would personally be opposed in my own home. However, be aware that if your roof leaks into those balloon framed walls and you fill them with cellulose, you could create a very moldy situation. I'd be confident of the plan to prevent moisture intrusion into the walls.
VB over open cell foam: my understanding is that code requires a vapor barrier over open cell foam. Given you have skip sheathing over slate, I'm guessing the roof is well ventilated and condensation would be unable to linger above the open cell foam. I'm curious to see what others say here.
Thanks! Great points and questions.
1) I've asked in my follow up email, but I'm not sure yet what their plan was on that 8.5". Maybe to totally encapsulate the rafters? I guess I could forget running electrical at that point hah. I can fur out the rafters an inch, but that's about it because the joists will need to be sistered to be safely used (and meet code) so that's taking up most of our headroom.
2) None that I can see, other than less work for them and more $$. It would air seal pretty well, I guess, but there's other ways to do it. Essentially the depth of insulation I can put on the gable is infinite so there's no need for foam, especially given the cost of materials. That said, if they have the foam gear up there already it might cost more in labor for them to change gears into doing batts, but that seems like a stretch.
3) The wall cavities were very poorly capped at some point with 2x4s at the attic floor level. It's intermittent as well, so in some places it's wide open, others have a cap, still others have some batts laying on top... not great. The air movement is truly impressive in those walls.
4) Great point about fiberglass getting into the house, I hadn't thought about that. Fiberglass suffers the same mold risks as well, correct? This is what has me the most worried.
Up top, foam rafter baffles will extend past the cavities (which will be blocked one way or another) to vented soffits creating a drainage plane in the event of a leak. I think that plus foam ought to provide decent insurance, assuming it's done correctly.
Vapor barrier is code in climate zone 5 and up if I'm reading it correctly, but we're right on the edge of zone 5. Honestly, mid-Atlantic weather can swing from Georgia heat in the summer to upstate New York snow in the winter all in one year, it just depends.
I should also say that my original plan was to cap the walls at the top with solid fireblocking, then firefoam around them. Install standoffs in the rafters of 1" for airflow and then use recycled poly-iso cut and cobbled with foam to vented soffits. Let a contractor drill and fill the walls after that and call it a day.
With the energy rebate it's essentially the same cost for someone else to do the work vs me spending several weekends doing it myself. My better half would rather have it knocked out in two or three days vs two or three weeks, which I understand, so here I am :)
Ccruic,
For a balloned framed house retrofit I went with:
-cellulose in the walls
-blocking at the end of joist/celing bays at each floor sealed with spray foam
-spray fomed in blocking at the top of each wall cavity in the attic
-spray foamed rim joist in the basement
For the roof, went with vented assembly with batts and interior vapor barrier. OC spray foam with a vent space above would work just as well and might be cheaper to install than dealing with non-standard stud spacing of older construction.
It was a night and day difference in comfort after the insulation upgrades. You could actually sit near windows and exterior walls.
With balloon framed house, you really need to focus on air sealing. Most of your losses are from air leaks, insulating the house (or insulating with a highly air permeable insulation) would save very little energy.
Don't forget to check your flashing details around doors/windows. These are typically non existent in older houses, leaks there would definitely cause moldy insulation down the road.
Thanks Akos, glad to hear it worked out well for you. Reducing air movement is my main goal, and I don't think dense packed fiberglass would do a good job at that, but I can find little info on the web about to support that. Good call on the flashings as well- it's certainly on the spring to-do list!
>1)" Open cell sprayfoam straight on the roof deck (1x8ish skip sheathing, actual 2×6 rafters). Specs say ‘Random Fill’ to 8.5″ @ R-30"
Bad idea, for all the reasons cited. Use some strips of 1" foam board tacked perpendicular to the skip sheathing as standoffs for an air barrier (could be 1" - 5" of cut'n'cobble, if you like). With 5" of reclaimed 2lb roofing polyiso in the rafter bays (~R28) and another 2.5-3" of continuous polyiso on the interior (~R14) the center cavity R would be north of R40, but it would likely meet current IRC code on a U-factor basis.
>"2) Open cell against the gables. 3 1/2″ to R-13 "
That would be fine, but below code-min, even if it's actually full-dimension 4" deep 2x4s. An inch of foam board on the interior under the wallboard would bring it up to current IRC code, if desired. To protect the plank sheathing interior has to have at least a class-III vapor retarder (standard interior latex on wallboard works) to use either open cell foam or fiber insulation in the wall cavites. Foil faced polyiso detailed as an air barrier would be a class-I vapor retarder. If the finish interior is going to be deferred, using a fire rated polyiso (eg Dow Thermax) would be prudent.
>3)" ‘Top plate’ install rigid foam ‘fan-foil’ and seal seams "
Sounds like they want to use foil-faced fan-fold foam as the top air barrier for the balloon framing which is fine as long as it's done in such a way that it can dense-packed.
>4)" Exterior walls get drilled and filled for fiberglass "
That's fine if the fiberglass is dense packed to 1.8lbs density, but not great if going with 1lb density, which isn't very air-retardent. Be very specific about density, especially if fiberglass. 1lb fiberglass won't settle over time, but it doesn't tighten up the walls very much. Cellulose is still very air redardent even at 2-2.5lb "2 hole method" densities, but in zone 4A shoot for 3lbs to avoid settling within the cavities over decades. Lower density cellulose can be topped-up in a decade if it settles leaving voids at the tops of the stud bays and it won't settle much thereafter, but it's better to just start out at a reasonable density.
I've seen 2-hole method cellulose in a 2-story balloon framed in zone 5A that was still perfect when the interior was gutted for rehab more than 25 years later, but I've also topped up (and dense packed) over 2-hole method cellulose in a similar house only 2 miles from that other house only a dozen years after the initial installation. Clearly not all cellulose insulation contractors are the same.