Aerobarrier Insulation and Zip System Sheathing

All, thank you for reading. My builder is planning on using aero barrier. It’s an expensive belt and suspenders approach. I’m fine with the costs. We aren’t planning to use zip anymore as a just zip board costs 70 dollars a sheet at the moment. It occurs to me that if we were to use aero barrier and zip/zip R aero barrier it might be a bad idea as it is pretty limited in vapor permeability. I might be setting up a vapor barrier sandwich. to make matters even more complicated we had just planned on using a combination of open cell for cavity insulation any thoughts. Or gotchas here?
GBA Detail Library
A collection of one thousand construction details organized by climate and house part
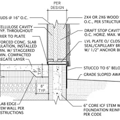
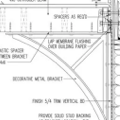
Replies
Amer,
It would be better to use tape, caulk, and gaskets to seal the house during construction. Before it is dried in, you can order a blower door test and seal any remaining significant leaks. Aero barrier should not be necessary.
Steve,
Thanks for responding. I will definitely be asking lots of questions and making sure that plenty of taping, caulking, and gaskets are being used as the primary air seal method.
I think we will def do a blower door score before the aero barrier. When is a good time to do this? I’m not sure when before dried means exactly?
Thanks for looking
I don't think that a "vapor barrier sandwich" is a concern. The Aero barrier doesn't apply a uniform layer to everything, it's just directed to the cracks.
Perfect, this is what I was thinking about. This makes sense. Thanks for responding
The way I see it is if you are dragging your contractor kicking and screaming into building a tight well insulated house dropping the zip and adding aero seal you may be giving them permission to build the same sloppy Leakey house they always build even after they bumped up the labor hours to cover the extra air sealing work you requested.
In the end as long as the house has a blower door test at close to 1 ACH50 it does not matter how they did it. I do not see the point and going to crazy extremes to get very low ACH numbers.
What are you replacing the $70 zip with $50 OSB? Has the price differential changed much seriously I do not know?
Any plan that requires spray foam I see as an act of desperation from someone looking for an easy answer with little regard for the cost in dollars or to the environment.
Walta
Don't specifically pay for aerobarrier.
Pay for a specified air tightness measured in ACH at 50 pascals, AND measured by a third party working directly for YOU. In the agreement that specifies the performance criteria, also come to agreement on the total volume of the house and make sure your third party agrees with that volume. Total volume is critical in calculating actual ACH, and you don't want to find out too late the contractor measures it differently. Also make sure your third party agrees what opening can be sealed off during the test. ie sometimes the contractor wants to put a temporary seal at the bath exhaust, dryer vent, attic access door, etc. That significantly improves the house air tightness.
However those temporary seals won't be there during normal operation, and some blower door companies won't let you do that because it skews the results.
If you are concerned about environmental issues, also agree on no spray foam, or no closed cell spray foam or whatever your comfort level is. There are some new spray foams that are supposedly very environmentally friendly but there are few contractors who apply them.
After that, how the contractor gets to your specified air tightness is a means & methods.
Hah good luck finding a contractor these days who will submit to those terms ….housing prices up 20per cent over past year and they are backed up two years!
> Pay for a specified air tightness measured in ACH at 50 pascals, AND measured by a third party working directly for YOU. In the agreement that specifies the performance criteria, also come to agreement on the total volume of the house and make sure your third party agrees with that volume.
Can’t argue with the approach, but wow I wish I lived somewhere where even a single contractor would bid to work on these terms, let alone a handful.
At least in NJ, the only way to get decent performance residential construction is to be prescriptive about the materials and assembly. Ask even a decent contractor to hit an ACH number and they’ll just walk across the street to the myriad of other customers who are waiting in line and don’t have such esoteric concerns.
Our builder is a gem.
I talked to multiple custom home builders before stumbling onto this one. I talked to several and I interviewed them GBA style. Afterwards they checked their schedules and found they were too busy.
I subsequently stumbled onto our current builder. He was already using rain screens, blower doors, mini splits, air sealing etc. He is thoroughly ahead of the curve for my neck of the woods. He was very excited to build a house that be air tight. I think he was stoked to have a client who wanted the things he had to fight for with other clients. He wants to use efficient windows. Most home owners want to spend money on countertops and cabinets, rather than meticulous water drainage. The list goes on
Yes, he does some things differently than GBA, but he’s open and receptive to suggestions and that’s super helpful.
If he's that conscientious, then getting a well air sealed house without aerobarrier will be easy.
Note that "belt and suspenders" is not a fitting analogy for this case. Aerobarrier works by filling leaks. It does nothing if you don't have those leaks in the first place. Taping and caulking is the belt. In order for the areobarrier to qualify as suspenders in the analogy, it needs to be doing something regardless of the condition of the belt at the time of install.
This is a fair point. I will ask him if we can do a blower test after the framing and windows, and see where we are and if we need the aerobarrier
we will find out how meticulous they are with taping and caulking and gaskets. As the builder, I’m sure he has plenty of subs working for him. As implied above, the subs much like the contractor, will only put up with so much. It’s much easier to go down the street and work on a spec house in which the builder is less worried about efficiency and more worried about his bottom line dollar number. A home where sloppy, cheap, and fast beats meticulous, expensive and slow.