Air Sealing Electrical Boxes While Allowing Future Wire Movement

I see a lot of Q&A threads about air sealing electrical boxes, so apologies for starting yet another one, but I haven’t found any that address this particular question.
I’ve done enough old-work electrical that I’ve been frequently annoyed by having basically no slack to work with at the junction box. When installing my own wiring, I therefore try to leave a decent amount of slack in a service loop that can be pulled out of the wall for future work (e.g. needing to re-strip the ends, getting a light fixture down to a comfortable working height, etc). I’ve installed a number of interior electrical boxes in this way, but am now discovering the importance of air sealing, thanks to GBA and am looking into how to air seal my junction boxes. I have not yet installed drywall. I see comprehensive solutions like the Box Shell, but I’m worried that it would lock the wires in place, preventing any future movement. Even if movement was permitted, it seems like it might then tear a hole in the air seal that wouldn’t be easily reparable. It would also perhaps stymie future efforts to fish new wire. I see many other products recommended: putty pads, manual foaming, firestop caulk, firestop foam, etc. Does anyone have experience with these materials and advice on one that would remain pliable and be easily restore if disturbed? I’m thinking maybe a silicone gel that I could apply from the outside now, but could also be used at wire penetrations on the inside of the box if the wires were disturbed in the future or I discovered air leaks with a blower door test (or for all the existing junction boxes in my house that I’m not reinstalling right now).
In the future, perhaps I’ll select junction boxes that have screw-on attachments for wires with gaskets rather than the “easy push” romex openings in the cheapo plastic ones.
GBA Detail Library
A collection of one thousand construction details organized by climate and house part
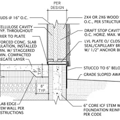
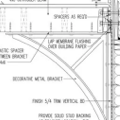
Replies
gcmn,
Another reason that having the exterior sheathing as the primary air-barrier may be the best choice when possible. Then if you have to pull more wire from the courtesy loop (which I agree is a good practice to include), the worst that happens is you disturb the insulation a bit.
Any caulking around the wire where it enters the box should be pretty easy to pull though or remove if you need to.
> Another reason that having the exterior sheathing as the primary air-barrier may be the best choice when possible.
Came to make this point. Unsurprised to find that you already made it!
No doubt that a conscientious builder can make an interior air barrier work, but I find it to be far more fussy.
My exterior has way fewer penetrations than the interior side of my exterior walls. Furthermore, if you're doing an interior air barrier on a two story house, you need to think about the interstitial space between floors as well. You need to air seal your plates, your 2nd floor rim joist, etc.
Additionally, if your interior air barrier is anything other than drywall (i.e. you're using an interior membrane as the air barrier), cutting a new hole in it down the road makes it hard to preserve that barrier layer (and the average contractor is not going to have any idea they should try to). Whereas with new exterior holes, the average contractor is at least going to try to squirt a bunch of silicone around it. And I still posit that you're more likely to add a new hole inside than outside.
Patrick,
Maybe it won't be necessary in time, but right now I wish there was some effective way of marking the sheathing as the air-barrier. Around here, using it as that is so rare I doubt any builder I know would be worried about patching holes in it.
Similar to caulking is duct seal putty you apply from the inside of the box where the wires enter the box.
Duct seal will not make an air seal that is reliable over the long term. Duct seal dries out over time and fails to adhere. I wouldn't trust it here.
Canned foam works, but tends to not allow any movement of the wire in and out, so if you slide the wire (such as by pulling in some slack to reterminate), the seal will fail. It can be difficult to reseal reliably, because of the irregular surface you get after tearing the foam.
Caulk works, but will need to be resealed if you slide the wire. I like the red silicone high temperature caulk, which is different from the red intumescent fire stop caulk. You do NOT want to use intumescent caulks here.
Putty pads word, and can be resealed after moving the wires -- for a time. Eventually the putty pads loose their "stickiness", and won't let you reseal things reliably. Note that putty pads are usually intumescent materials, and should ideally be used on the EXTERIOR of the box only.
I usually use a combination of canned foam, silicone, and putty pads. I used canned foam where I have limited access, since I can let the blob expand and hopefully seal. Caulk is easy to get a reliable seal with IF you have good access to the site needing to be sealed. Putty pads work great if you can get around behind the box. I like using white fiberglass "hard boxes" since they are easier to air seal (no extra holes).
Bill
The NEC says that cable has to be secured within 12" of a junction box. I had always assumed that distance was measured along the cable, that you couldn't have more than 12" of cable between the staple and the box. You're saying your inspector will let you have a loop of cable between the staple and the box?
The usual interpretation is that the 12" be measured along the wire, but it's pretty common for inspectors to just look at the distance from the box. Most of the time, a loop that looks "too big" will fail. If you form a sort of "Z" shape that isn't excessive (i.e. run flat along the framing a bit, then up and back a bit, then straight into the box), you'll usually pass OK as long as you have a staple within 10-12" or so from the box. A 2 foot loop probably won't pass, and would be a bad idea anyway, since it will flop around in the wall and be a problem for the drywall guys.
Personally, I don't see much need for big slack loops. I strip back enough jacket to leave enough wire to comfortably reach out of the box (supposed to be about 6", but I've never seen anyone actually check this at inspection time), then don't worry about it. It is exceedingly rare for people to rework this stuff down the road. If you do want to leave some slack in the jacketed cable within the wall, a simple "Z" like I mentioned with around 6-8 inches of slack should be fine for one entire rewiring of the box, with a full "pull it in and strip the jacket back" type of operation. I can't see anyone ever needing to do that more than twice.
Remember that if you replace a device (switch, receptacle, etc.), you don't usually need to do anything with the wire -- just remove it from the screw or clamp of the old device, and reuse it in the new device. You don't usually even need to restrip the wire. If you do need to restrip, it's about 5/8" of wire to do that if you cut the old stripped part at the jacket, and then strip fresh. It should be VERY rare to need to do anything beyond that in any case.
Note that I said "screw or clamp" on the device. That means DO NOT BACKWIRE, EVER. Backwire is asking for trouble... The kind of trouble that can start fires. Don't do it. Use the screw terminals, or, better yet, get "spec grade" devices and use the very much nicer screw-driven clamps on those that you can "backwire", but with a proper clamp driven and held by a screw and not just a cheapie spring terminal.
Bill
DC,
You are looking for another 6" of slack. That's pretty easy to do with the staple about 6" from the box.
Bill,
I think the idea gained traction when boarders started using roto-zips. It's pretty common to find nicked wires when you go to do your finished electrical.
This is on my wife's she-shed, which was insulated on the outside.
Overzealous drywall crews are certainly an issue! Using STEEL mudrings can help with this, since that gives their bit something to follow that the bit can't eat into. The other thing to do is to form the wires into a loop (usually an inverted "U" shape) within the box, and push it as far towards the back of the box as possible prior to the drywall crew's arrival. The handle of a screwdriver works well for this. I prefer to strip the outer sheath of the cable AFTER the drywall guys arrive too, which means that sheath provides a little extra protection for the actual wires instead until the box is ready to terminate.
The electrical crew should probably instill some level of fear in the drywall crew too, to help protect their wires. Maybe a "we think a few of those might be live, so be careful" comments might do the trick :-D
I'm not a fan of big loops like in your pic. In many areas, that would probably fail inspection. It's pretty much at the discretion of the inpector from what I've seen.
Bill
Agree that a loop like that would fail.
What I could see doing if you wanted to leave some slack is to secure the wire normally, but make the tail in the box longer than normal. Coil the tail and stuff it neatly in the box. After drywall, when you're installing outlets, instead of trimming the cable shove the excess back through the knockout and into the wall. The purpose of securing wires is to protect them until the drywall goes up, once the walls are closed in there's really nothing that's going to harm a loose wire.
When people talk about a "courtesy loop" I don't think they're envisioning repairing a nicked wire, it sounds like they're thinking about being able to move the junction box in the future. I'm not a big fan of that kind of "future-proofing" because nothing is harder to predict than the future. If you knew what you wanted down the road you'd do it now.
DC,
Why? It has less that 12" of cable between the staple and box.
I'm not an electrician, but including courtesy (or service) loops is part of the electrical apprenticeship program here in BC, and I think that the 2018 amendments to several province's electrical codes mandated them. The purpose is specifically called out as a way of dealing with the need for more wire in the box in the future.
Here is a neater version than mine from I believe the apprentice's handbook
From what I can Google about the CEC it seems that the section that requires loops -- 12-510(4)-- only applies to fixtures with an integrated junction box. To replace those fixtures you need to remove the box and it makes sense that you'd need slack for that.
The requirements for placing and securing wire are all about protecting it from damage. Unless you've got rodents, wire doesn't really get damaged in use, it gets damaged in construction. The goal is to put the wire so that it's in a place unlikely to get damaged, and in a predictable spot so people know to avoid it. The goal in fastening is to keep it in that spot
The second picture is neater, but that first picture doesn't look at all to me secure. In particular, it looks loose enough that the drywaller could hook it and pin it against the stud, and then put a drywall screw through it. Low voltage wires tend not to be well secured and drywall guys nail those all the time.
DC,
The first picture is from an unusual situation. The interior finished wall surface is birch plywood, and is already in place. The boxes and cable for the shed were done from the exterior. It was inspected and approved.
I think this is a good example of the differences we see in the practices and codes across the regions in North America. You would be hard pressed to find a house in BC that was wired in the last five years that doesn't include them. When we say "this wouldn't pass inspection", we should probably add "here".
Malcolm, that multi-gang box is more what I was describing as "OK" with the "Z" shape loops. That's more than is usually left here, but maybe not everywhere. I do work mostly in the commercial world, where everything is conduit (and MC cable), and it's not practical to leave "courtesy loops" in conduit :-)
The general rule is that the loops shouldn't flop around, and shouldn't be such that the "sides" of the wall (drywall, etc.) are keeping the loop within the wall. Another way to say that is that the loops should support themselves entirely within the stud bay even without the drywall or other wall surfaces installed over the studwall. You should be able to look down the side of a roughed-in studwall and not see any of the wiring hanging out beyond the edges of the studs.
Big loops that I've sometimes seen people advocate for accomplish little if anything, but do complicate construction, add some volt drop (albeit not much), are make the wiring more prone to movement and brittle fracture related connection failures if heavily loaded.
While it's normally not much of a concern in residential buildings due to the relatively small amount of current available at the service, there is another reason why wiring needs to be properly secured and it has to do with what occurs during fault conditions. Commercially, the forces can break things, due to the electromagnetic forces involved under short circuit conditions. This is why the PANEL, and not just the BREAKERS have a fault current rating in KAIC -- for the PANEL, the fault current rating has to do with the ability of the panel to CONTAIN a fault without physically breaking.
What happens with a loop of wire under fault conditions is that the electromagnetic forces tend to make the wire snap around, or pull together in a bundle, depending on what kind of current flow you have. With heavily loaded (not shorted) wires, you get a sort of "buzzing vibration" of the wires. This can potentially loosen the electrical connections. If you have a plastic box with a really crummy cable clamp, a larger courtesy loop could potentially be a problem in such a situation over time. The far better holding cable clamps in metal boxes should be much less of an issue here. I don't think this vibrating wire is likely to cause all that many failures in practice, but it is another thing that actually does happen under certain situations. Running a lot of electric space heaters would be the most likely scenario I can think of where this could ever get close to being an issue though.
Note that large coils of wire cause localized heating. You won't get enough of that here from a courtesy loop, but this is the reason why you're not supposed to leave your extension cords coiled while using them.
Bill
Industrial, commercial and residential electrical. Mostly in AB and BC. Courtesy loops have always been a thing up here at least since 89 when I first started. If you are worried about having some extra slack and disturbing the seal, I would go with a deeper box or a 4 inch square box with a mud ring. That way you could get a few extra inches in there and not have to worry about pulling more cable through from the stud cavity and then somehow repairing the seal.
Deleted
Thanks everyone for the discussion here :-)
I think having a small loop is totally compatible with having the wire stapled within 12". That gives you 12" to play with! When I'm talking about having some extra slack, I mostly mean for ease of working on the box in the future, not moving it elsewhere (I think future proofing too much for that would indeed get you into trouble). I've probably over-compensated from having to wire a receptacle basically while it's in the box because the wires are 60 years old with deteriorating insulation and stretched taught. I've got some loops here that I'm thinking about going back and shortening. Bill, I like your rule of thumb that the wire should be supported without leaning against the sheathing or drywall.
Also interesting info about loops causing issues under fault conditions. I hadn't thought the EM forces would be sufficiently large to matter there.
Note that I think some of you are talking about things being done in the order of running wire, installing drywall, and then adding fixtures. I already have the fixtures installed here before drywall, partially because I'm living in this space while working on it and having no outlets for months would be pretty tiresome. I agree that if you aren't installing fixtures till later, you can probably just keep some slack in the box and then shove it into the wall once drywall is up.
But regardless I still think leaving the ability for the wire to move around a bit and being able to restore the air seal if it's messed with is valuable. I've got good access all around the boxes right now (they're even variable depth so it's pretty easy to move them forward and get to the backs).
Based on comments here, I think I'll go with a high-temperature silicone caulk that I can apply from the outside for now and then if I'm doing future work on the boxes I can restore the air seal by caulking from the inside. And in the future I'm going to pick electrical boxes with fewer holes!
"t's understandable that you want to ensure air sealing in your electrical boxes while also leaving room for future wire movement. It's a balance between efficiency and flexibility.
When it comes to air sealing products like putty pads, manual foaming, or firestop caulk, their effectiveness may vary, but many of them are designed to be somewhat pliable and can be reapplied if needed. I'd recommend consulting with a local electrician or an ottawa electrician who can provide advice based on your specific situation and local building codes.
Getting expert advice ensures that your electrical work is not only air-sealed but also meets safety standards and allows for future adjustments.