Air Sealing Priorities

Hi All,
The floor plan for our new build is nearly done and I’ll be sharing it on here for feedback when it is. In the meantime, I had a question about air sealing. We’re going to keep the attic within the conditioned envelope and we will have a detached garage with an open breezeway, which I think eliminates two of the biggest problem areas for air sealing (per https://www.greenbuildingadvisor.com/article/getting-the-biggest-bang-for-your-air-sealing-buck)
We haven’t settled on the assemblies for above-grade walls and the roof yet but whatever we do should be sealed reasonably well – it’s probably going to be Zip-R taped by a crew that’s very familiar with it, or Prosoco Cat 5 over OSB if the cost delta isn’t insane, which would keep things even tighter.
Are there any other things I need to worry about re: air sealing? Thanks!
GBA Detail Library
A collection of one thousand construction details organized by climate and house part
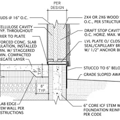
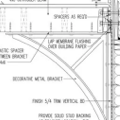
Replies
Matt R loves Prosoco. But then you go to the weather barrier video test he visits at the TX University, he says he liked the results of the liquid weather barrier that was 70 mils thick and didn't like the 15 mils options at all. Cat 5 isnt' 50 or 70 mils. Heck, I don't have a clue what is. https://www.youtube.com/watch?v=RvZK89oqO1I at 2:20 he starts bagging on any option we have for fluid applied.
I almost did Cat 5 myself to simplify. But this stopped me.
Here's one where I don't understand what Matt R wants us to use. It's not adding up.
I would pick Tremco’s fluid-applied system, which includes the ExoAir 230 product for the main body of the wall, along with the Dymonic 100 product for detailing. The Dymonic 100 polyurethane-based detailing product scored excellent results in the Walsh Construction wingnut testing, surpassing nearly every other sealant tested. And the ExoAir 220, a sister product to the ExoAir 230, was the only WRB that passed the UT Durability Lab’s nail sealability test (ASTM D1970). Had they actually tested the 230 product I’m sure it would have passed as well. The ExoAir 230 product can be sprayed with a standard electric airless paint sprayer, which is a big win for me wanting to do all of this work myself. Some of the other STPE products such as PolyWall’s BlueBarrier product required the larger gas spraying rigs which can run north of $10k to purchase. Of course, you could always roll the product as well, but I was planning on purchasing an electric sprayer anyway to paint the inside of my house. And I think the sprayed finish results in a more even coating, especially around the hard-to-seal areas such as penetrations and inside corners.
Selecting a conditioned attic increases your conditioned space and its surface area so you will lose more energy if you manage to get the same R value. Getting the same R value almost never happens because spray foam is almost the only option. The facts are spray foam is the most expensive way to but an R of insulation. Spray foam is the least green way to buy an R of insulation. Spray foam is the riskiest way to but insulation in that installation does not always go well and in the event of a fire the smoke will kill you.
In short covering the flat ceiling with cheap fluffy insulation will likely cost half as much with twice the R value over a smaller area.
The way I see it a conditioned attic is poor choice and only reason to consider one is if you insist on putting your HVAC equipment and ductwork in the attic.
Walta
We are comparing quotes for 12" of spray foam in the attic vs. cellulose in rafters + XPS on exterior. The attic is the only place in the home we're considering using spray foam - agree that it's expensive and, with the wrong blowing agent, isn't particular environmentally friendly, but that's not what I'm concerned about.
Martin's written multiple articles here with quotes from JL on the importance of insulating an attic if you're running ducts through it, and he also provides some alternate pathways, like dropping the 2nd floor ceilings by 2 feet and having a dedicated chase. We don't want dropped ceilings in the hallways, and I'm not confident our contractors would do a great job air sealing an attic floor, either.
Spray foam in a new build means somebody didn't do their homework. It is expensive, not the greenest insulation and if done wrong near impossible to remediate. In no way does it make the house "better" that can't be done with a bit of upfront design, regular building techniques and a bit of attention to detail. Conditioned attics only make sense if it will be finished down the road.
" where does all the 2nd floor ducting go"
It goes into the floor joists. Spec floor trusses with a duct chase for simple ducting. If done at design, this is pretty much free and you don't need any spray foam in a house. If there is a dedicated air handler, it can go into a small utility closet on the 2nd floor (you want an air handler that can do down-flow). Easier install, cheaper to service and filter changes are a breeze.
Thank you for the reply - your second paragraph was very helpful. I'll talk with the builder about floor joists with a duct chase as an alternative. Am I right in thinking the chase is basically within the attic, and then the attic floor is the top of the chase?
It's early days for our HVAC design, but I'm pretty sure we're going to have a dedicated dehumidifier, not sure if we're doing one air handler for both floors or two separate units. Builder prefers two, I don't know which route is better.
Nope, the 2nd floor joists. All the ducting for the 2nd floor can be run inside there.
You can get roof trusses with a duct chase as well if you want to run ducts up there, I find running along the floor joists easier. That is pretty much how it is done around me.
Ah, got it. Is there any way to access the ducting short of pulling off drywall?
If you don't want to drop the ceilings -- make them higher to start with. It's a new house.
With trusses, you can run all the ducting through there, no need for any bulkheads.
Doesn't it look weird to have the second floor of the home noticeable taller than the first floor from the outside?
One of my floors is about 20" thick, about the only spot you notice it is going up the stairs. There is no way to see this outside the house.
Just even out the window placements of each floor so the difference is not noticeable. Which means your second floor windows will probably be a different height above the floor than your first story windows.
Makes sense. Thanks!
Bumping to ask for related input: my enclosure consultant and a second consultant I spoke with (both of whom are notables in the field, if you post here you probably have seen/listened to them both on various podcasts and youtube vids related to building science, they work on residences WAY more expensive than mine as well as commercial + government buildings) strongly recommended a conditioned attic for running ductwork vs. an unconditioned attic and ductwork elsewhere.
Their preference for this approach is that they have seen people fail to properly air seal attics over and over again, whereas laying XPS on a roof is straightforward (and roofers are comfortable/capable of doing it). It's fine for people on here to say "just spend time getting it right," but when the crews on the ground don't have time / interest / ability to do it right, isn't it sensible to consider an alternate approach?
Ignoring any issues related to cost, if it's easy for roofers to tightly airseal and insulate the roof with foamboard and tape on the outside combined with cellulose in nets against the rafters on the inside, and it's difficult to find crews to do proper airsealing for all the penetrations in the attic, doesn't it make more sense to just turn the attic into conditioned space?
I don't think you'd see much difference in practice between an air sealed roof and an air sealed attic floor, UNLESS you used spray foam. Spray foam has one big advantage here: it air seals as it's applied, and you build up a thick enough layer (trying to hit your R value target), that it's unlikely you'll not have a good air barrier when you're done. This means the spray foam helps to cover for carelessness on the part of the insulation contractor, since the air sealing happens regardless of how carefully the other parts of the project are completed.
You could do the same thing with a flash and batt attic floor, although my prefence is to just do a careful job of air sealing. I'd be interested to hear from your consultants if they prefer the sealed attic roof line due to it being less prone to careless contractor problems, or if there is something else to it. My own preference is to go with a vented attic, and the ductwork in the basement/crawlspace/interior soffits. Vented attics are pretty robust in other areas.
At the end of the day though, there are always tradeoffs, so it would be interesting to hear what set of tradeoffs your consultants thought was the overall best combination. Discussions like that can help everyone to improve things.
Bill
They 100% prefer a sealed attic roof line because it's less prone to careless contractor problems. I've got a spreadsheet with multiple assembly options for above grade walls, below grade walls, roof, etc, and we're going with the things that are easy for contractors to get right and are PGH-level, not the gold standards or the most expensive or anything like that. Their goal is to help us build a tight assembly with the lowest risk, given that poorly-built tight assemblies cause many more problems than adequately-built leaky assemblies.
They're of the opinion that roofers are used to putting down sheathing and underlayment, and that adding a layer of foam in between is something they're well suited to doing. You end up with sheathing, 5" of foamboard, another layer of sheathing, underlayment, and then the shingles/steel/whatever on top. Air sealing is done w/ tape at seams, which they say (and seems to make sense to me) is easier than going through a poorly-lit attic and ensuring you've foamed every intrusion on the floor.
They're also fine w/ us doing whatever we want with the build, but their recommended best practice is to insulate on the exterior of the roof. Exterior foam isn't the cheapest option, but it's the safest.
You have to be careful with exterior insulation. Unless you are in an area where it is code, getting trades to do a non standard build even just for walls will add a lot of cost.
I have yet to find a residential roofer that will install exterior rigid. The folks that do torch down flat roofs will install polyiso but that is about it. You might have better luck with your framer if they are willing to install nailbase panels over the roof deck.
Air barrier at the roof line can work well when you don't have overhangs. Zero overhangs are hard on siding, so I would only do this with metal. Once you add overhangs, getting air barrier continuity from roof to wall becomes complicated, in most cases you are back to spray foam at least at the eaves.
Air tight ceiling is not too hard provided it is planned for up front. You want a membrane air barrier for the ceiling that can be installed so you can do a blower test before any drywall goes on. This doesn't require a lot of extra work or materials but you do need a GC that is willing to install it and test/fix any major air leaks.
I don’t think k you’ve mentioned what climate zone you are in? If you are in the South a conditioned attic is preferable because of the greenhouse effect. Walta’s post #3 is correct about more surface area along the roofline versus the attic floor but you have to also look at the temperature delta. Because of the greenhouse effect a vented attic will always be warmer than the ambient air temperature. In the North this is a good thing and reduces heating loads, in the South it is a bad thing and increases cooling loads. Both surface area and delta temperature are in the heat flow equations. And a conditioned attic is way easier to maintain air seal from electrical light penetrations as your advisers mentioned.
Kristof Irwin has a whole podcast episode about this for Southern climate zones.