Analysis paralysis – addressing crumbling mortar under sill plate

Hello everyone, I was hoping to gather some opinions about my sill plate situation.
I live in Guelph, Canada. Began tearing out the old basement of my 1958 poured foundation brick faced home. The goal is to install interior weeping tile system with dimple mat against the walls up to exterior grade, and then insulate with 2 inches of EPS and a stud wall of Rockwool. I already spent a dusty couple days air chiseling off a layer of parging covering the concrete walls, which then revealed the topic of discussion: the sill plate is a 2×4 embedded in some kind of mortar, presumably for leveling. There doesn’t appear to be any point where the sill actually rests on the concrete foundation, the mortar leveling plane ranging from 1/4″ up to 1″ or so. The sill itself is in excellent shape.
So what’s the problem, you ask? Well, the mortar is quite crumbly in some places. And in others, is almost completely gone. I think overall there is enough integrity left in the mortar layer that the sill isn’t about to shift, but still it is something to address now while everything is out in the open.
From what I’ve read scouring the internet, my best option is as follows – and if you dont mind, weigh in here: Use metal shims from my local metal shop under where joists sit on the plate and scrape out the grout. Then ever so gingerly slide in some sort of capillary break, most likely just the standard pink foam, though I am intrigued by deck joist tape? Then, repack the rest of the gap with hydraulic cement, remove shims after the grout dries and pack those areas too.
I also thought to just shim, remove grout, spray foam the gap as a capillary break, and just leave the shims in place. Done and done.
Another less intense idea I had is to just clean out any loose stuff and just repack with hydraulic cement and carry on. The issue here is it doesn’t address the capillary break situation. From what I’ve read though I shouldn’t be too concerned? By covering up the plate with EPS I won’t be losing a path to dry since EPS is fairly permeable, there is still a path to dry to outside, my foundation extends past the soil more or less over a foot, and I have two foot roof overhang. The area around my house under the overhang is always dry, even while it rains heavily. And the interior dimple mat won’t be going as high as the sill plate, so that doesn’t really affect anything.
I don’t know, I tend to get bogged down by the smallest things. What is everyone’s thoughts? Like it’s been said, this is the time to do it right! But at the same time, it would be so easy to just patch with cement and check in a few years to see if moisture is accumulating behind the EPS.
GBA Detail Library
A collection of one thousand construction details organized by climate and house part
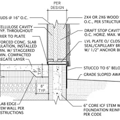
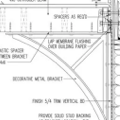
Replies
billstyles,
My suggestion would be to remove several feet of mortar at a time, slightly jack up the sill (about 1/8") and insert a strip of Pt lumber with membrane or laminate underneath as a capillary break. Any gaps between pieces can be filled with canned foam.
Hi Malcolm, nice to chat with you after reading your posts for so long! Thanks for responding. That is a very interesting idea. Attaching the membrane before sliding in the strip would make it a lot easier. What are your thoughts on compression of the wood strips? The thinnest I can find in pressure treated wood is 1/2" plywood or 5/8" normal wood?
What are your thoughts on leaving in the metal shims under each joist connection and just spray foaming the gap? There will be at least 2" of foam insulation against the wall so I'm not terribly concerned about the metal causing cold spots. That would by far be the easiest method.
Thanks again, looking forward to your response!
billstyles,
Compression shouldn't be an issue, any more than it is for the existing bottom plates above them with the grin in the same orientation. But what I am suggesting is labour-intensive. You would have to rip all the shims from PT lumber on a table-saw to get the varying depths.
Maybe your plan to use metal shims is easier and better - especially as you point out, my concern about thermal bridging isn't really a factor if they are foamed in. You may also have to place shims next to the anchor bolts to keep them effective.
I hadn't thought about sill-plates bedded in mortar for decades - but then remembered it was the standard detail when I first started out in the mid-80s. No pt lumber used either. I'm glad your are in good shape, I hope the rest of the buildings I designed with them are too!
Good luck with your project.
Hey if there is one thing I'm good at it is manual labour!
Maybe I will go with the metal shim idea...good call on minding the anchor bolts! Too bad the shims aren't as readily available in Canada as they are in the states, it seems you can almost get anything from Home Depot there. Perhaps I'll meet in the middle and do PT shims.
Hopefully having a path to dry to the exterior is enough for the sill, only time will tell. Thanks for your responses, they are very much appreciated. Stay tuned for more questions, I'm sure they will arise!
billstyles,
The main threat to the sill-plate is from moisture coming up from the concrete. Once that path is closed off I don't think you need to worry.