Analysis Paralysis in new build wall

Building our new “forever” house just outside of Chicago (zone 5a). The architectural wall build plan was designed and approved in 2023 using 2018 ? codes. The village has grandfathered the build into the older code versus 2024 code. Gosh I hope I am code correct. Regardless, the plan calls for 2 x 6 16 on center. Inside to out plan: drywall, cavity filled with paper backed R21 fiberglass fill, 7/16 OSB, Tyvek then siding. After exhaustive researching on GBA, FHB, Building Science…. I have yet to find an affordable solution with the GC that provides a better just as affordable wall assembly while meeting the detailing capabilities of a midwest “old school” team. The siding is Nichiha vintage wood (not used often on residential in the midwest) and they allow 1″- 1.5″ exterior CI at max per their technical advisor. The budget is important but I want to maximize the control layers and have most every layer outside. Curently looking at changing Tyvek for Zip R6 but the price went up tremendously and very few installers here are familiar with the detail involved. I am wracking my brain here trying to find a solution that works for our zone that can achieve a better R value affordably within the constraints of an old school builder and his team. Thank you in advance for any suggestions you offer. BTW, dummy down your responses since the torch for this build has been passed on to me as the wife to manage it all. I can’t be the only one out there looking for support.
GBA Detail Library
A collection of one thousand construction details organized by climate and house part
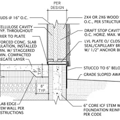
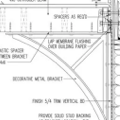
Replies
If you are not in the land of exterior insulation, the install cost will mean that there simply never be an ROI for it.
One thing that effects the durability of any painted siding is adding a rainscreen. This doesn't have to be much, even something as simples as 3/8" strips of plywood nailed to the studs work. This provides a capillary break and some additional drying capacity which greatly increases the durability of any painted finish. As a bonus, it also adds addtional drying capacity to your walls.
If the rain screen is out of the budget, I would look at least specking one of the drainable house wraps.
Also if the cost delta is not too large, plywood is a better sheathing material, worth the extra cost.
As for your wall, the simplest upgrade is go to 2x8 studs 24" OC with high density batts. This has about the same assembly R value as the 2x6+R6CI, slightly more expensive insulation about the same lumber cost. About the only thing your framers can complain about is the 2x8 don't come as pre-cuts for 8' and 9' walls, unlike exterior rigid, the rest is all standard build. You can even keep the studs at 16"(drops the assembly R value a bit) if it make the trades happier.
“since the torch for this build has been passed on to me as the wife to manage it all”
If you are already managing it and having to coach your builder on the latest practices, at what point does it make sense to be your own GC and save the 20-30% markup? You would definitely be able to afford the Zip R6 then.
I think the suggestion by Akos is a very under appreciated and very under utilized solution. I just checked my local Home Depot's website and a 2"x8"x8' board is $1.04 more expensive than a 2"x6"x8' board. A 2"x8"x10' board is actually $0.18 CHEAPER than a 2"x6"x10'. Maybe that's an unusual situation, but the overall cost difference in stepping up from a 2x6 to a 2x8 is very small (compared to Zip-R, exterior insulation, staggered 2x4 wall, etc...)
The real beauty is you don't have to explain / train / convince your contractors on how to construct exterior insulation and flash it properly. They can build it just like regular. You can't buy factory window or door jambs for a 2x8 wall, but you have the same issue with a 2x6 wall using exterior insulation. It's not difficult for your interior trim carpenter to add a short jamb extension on the inside.
Sometimes the simplest solution is the best solution.
My two cents... The best of luck with your build.
I'm just a hobbyist but my thoughts:
1) This statement is curious. "they allow 1″- 1.5″ exterior CI at max per their technical advisor" That should depend a lot on the exact design and products used. To make that statement, they must have a specific type of exterior insulation and attachment method in mind.
2) Changing Tyvek to R6 would also change the entire characteristics of the wall (the location of the vapor barrier.)
3) Agree with others that you should look into a drain wrap product. Tyvek makes one.
4) Agree with others that going to a 2*8 wall may be a good solution. Doesn't add a lot to the cost and it's very simple for the crew. Honest question for the hive mind: Is a staggered stud 2*4 wall on 2*8 plates an allowable option? 2*4's at 16" centers on the inside and outside (staggered though so you'd end up with a 2*4 every 8" and would probably use full 2*8s around windows and doors) Blown-in insulation.
5) I'm concerned about your air sealing. Where is your air control layer and what techniques are you planning on using?
6) What is your insulation strategy for your foundation/basement and attic? You might find it's easier to upgrade the envelope in those locations.
2x4 staggered on 2x8 plates does get you a thermal break at the studs and would be a step up from the 2x8 x 24. Not sure the extra cost in 5A warrants the labour increase to frame it though vs 2x8@24" center. The framers would be scratching their heads at door/window framing if they have not done this before.
Steve B does his blurb here: https://www.youtube.com/watch?v=e3BAp68TeVI
It's not totally under appreciated.
It should be the green community political priority to move to deeper framing where material can actually meet R values. Change code to make walls and cathedral ceiling fit insulation that exists and is not creative, furring, unknown, or calls for questionable spray foam. Done.
Then you can rigid foam exterior all you want...if you want. Or don't even consider it because you don't have to.
Just one home owners opinion. I just can't imagine all the solutions are better than deeper framing from a green perspective and structural one too.