Any hydronic system controls with low standby electricity consumption?

I was feeling good about the changes I’m making to reduce the electricity consumption of my hydronic system: a Grundfos Alpha ECM pump that is consuming only 16 W when it’s running, and Taco “sentry” zone valves that use about a watt when on. But I measured the power consumption of controls last night, and it can add up to almost as much as the pump: 3 W for an aquastat, 6 W for a Taco “switching relay” circulator control with one zone on, and 4 W of standby power for the 40 VA 120:24 VAC transformer that powers the zone valves. Standby power with nothing running is 9 W total or 13 W with one relay running, not counting the valves’ power consumption.
My question is whether anyone makes hydronic control hardware with low power consumption. I’m tempted to design my own control system, but in case I don’t live in this house forever, or don’t live forever, it would be easier for someone else to service the system if it used off-the-shelf hardware made for hydronic systems.
Back when pumps used 80 W each and zone valves 5-10 W each, 10-15 W of control power was pretty negligible, but now that we have pumps and valves that use 2X to 5X less power, that control power starts to seem embarrassingly high, especially when you consider that modern electronics can do things that are way more complex using power measured in mW rather than W. Is anyone stepping up to the plate on this, or are they all assuming that nobody will notice?
GBA Detail Library
A collection of one thousand construction details organized by climate and house part
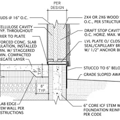
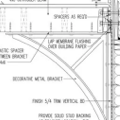
Replies
Charlie ,
What type boiler , emitters are you utilizing and what fuel does it use ? Are these numbers from last year or just from the beginning of this season from the bit it has been on standby ?
The numbers are just instantaneous measures of power draw, not cumulative energy consumption. I disconnected the pumps so I could measure just the power draw of the controls.
My heat source is a water-water ground coupled heat pump. The emitters are a mix of baseboard radiators, Myson panel radiators and one Jaga fan convector. But I think the issue of electric consumption of the controls would be similar for most systems. I didn't actually measure the power draw of the control board in the heat pump--that would be in addition to all of this, but there's not much I can do about that without modifying the internals of the heat pump.
What is your design SWT through the emitters ? What size buffer tank do you employ ?
What HP are you using ? Entering source temp ?
Am also interested in what drove your decision to choose the Alpha as opposed to an ECM Delta T circ . They are both ECMs , yes , but the Delta t pump goes much further towards energy savings as part of a system .
Richard, thanks for your interest in the system beyond the initial question.
* Design SWT is 110 F, but I usually run 100 F in the winter other than cold snaps, 90 in the shoulder seasons. Envelope upgrades that are in progress may allow keeping it at 100 all winter.
* Buffer tank is 50 gallons.
* Entering source temp is typically around 45 F; lowest I've seen is 41 F. 9 gpm.
* Heat pump is a Hydron Module 3 ton unit. It's oversized, but with the buffer tank the oversizing doesn't hurt much.
Yes, I really like the idea of a delta T controlled pump. I'm trying to remember why I didn't go that route--I think I was unsure of whether I'd be able to set it up to work right when I run the system in cooling mode. I probably should have looked into that more before installing the Grundfos. I could move the Grundfos to circulate the water through the heat pump and get a delta-T controlled pump for the circulator to the emitters, but given the oversizing, the hours of operation of the heat pump are a lot less than the hours for the circulator, so I'm not sure that's worth the investment. I'll see what the hours of operation are for the year after our envelope upgrade.
Another control issue on the system is that ideally I'd have some sort of outdoor reset. But I wouldn't want it to heat the whole 50 gallon tank to 110 F just because it got cold for a few hours overnight. I'd like it to base the water temperature set point on something like a 24 hour average outdoor temperature. I haven't seen any products that do that. The other option would be to control the water temperature setpoint based on the thermostat cycling, increasing it if the duty cycle approaches 100%. I thought I'd seen some products that do that but I'm not sure where.
If hours are a concern which I know they are you really might want to think about the Delta t pump . I'll explain . You had to size your pump to flow fluid properly at design . Highest head with one or all zones calling , barring the possibility of all zones sharing a like head characteristic (unlikely) the Alpha will ALWAYS maintain the highest head no matter what combination of zones is calling . If your highest head zone is not calling the zones with a lower flow requirement will be overpumped , as will your highest head zone at other than the 90% design day . You are essentially overpumping and using more energy for 95% of the heating season . When doing this your are also reducing your fluid Delta because the flow is not conducive to heat transfer . Regardless of what others may say , , a lower Delta is evidence that the designed for heat transfer took place . Turbulent flow is not always necessary , the flow that is necessary is the flow that transfers heat the best at a given point in time . What this also does is mixes the buffer tank which we would want to remain stratified and return the coldest water to the heat pump where it can really do it's thing . Retarding heat transfer within the device is also less efficient . Moving water that is giving no beneficial transfer is inefficient . In other words , you will lower your pump on time also by letting the DESIGNED for Delta T take place . Delta T is evidence that heat transfer took place . Baseboard operates nicely on a 20* Delta T as do your low temp panel rads and your coil unit .
If your Delta P pump , which actually never changes pressure as opposed to maintaining a pressure as zones open and close , allows for a narrowing Delta T , there is your evidence that the designed for heat transfer is not being allowed to take place , thus returning fluid to the buffer and possibly the HP that will allow for less heat exchange . The Delta T pump will vary flow rate based on heat transfer characteristics derived from real information at all times the load side is operating . You can actually count on the heat transfer taking place , moving less fluid based on system requirements , and insuring that you are sending colder water back to the point of origin so better heat transfer can be achieved .
This waste of energy is an order of magnitude higher than the standby energy your controls are losing for you .
if you'd like ODR on the system , that is easy . A simple Taco I Series ODR mixing valve can do that easily for you . In the case that you have a quality buffer with good insulation I would advise to let it run to a 110* storage temp . This will hold out the HP for longer periods and insure that when it turns on it will run for a good long efficient cycle and maximize it's efficiency . Storing BTUs is not a bad strategy when you use it wisely .
Richard, thanks for the good description of the advantages of delta T. I absolutely agree that it is a better control method, and that I could get reduced pump power and improve the control responsiveness and precision if I had that. I agree that the delta T directly tells you what you need to know and allows using exactly the pump speed needed. And even a small decrease in pump speed can result in a larger percentage savings in pumping power.
But even if I reduced my pumping power to zero, I couldn't save an order of magnitude more than my control system power. The pump uses 16 W. The standby power is 9W without the pump on, 13 with it on. Given that the 9W is 24/7, the energy consumption is greater than that of my poorly controlled pump.
With old pumps, the pump energy consumption was ~4X that of the controls. Now that some pumps use 2 to 5X less energy, the controls are a much bigger fraction of the energy use. It is small compared to the heat pump compressor or the boiler fuel, but improving it is very low hanging fruit. Designing an efficient wet rotor pump that survives with 180 degree water is a serious engineering challenge. In comparison, designing a relay control system with low standby power is child's play. I am surprised that Taco isn't doing it, given what they are doing with valves and pumps.
On a heat pump system, unlike a boiler, mixing down the SWT is not the best option to do outdoor reset. If you only need 90 F water, producing 90 F directly instead of producing 110 F water gets you a higher COP. So if I were going to do that I'd want to simply vary the aquastat set point, and there are off the shelf controls to do that.
Charlie ,
SYSTEM COP is much more important than component COP . You can turn parts of the system off and only engage them a percentage of the time when the heating system / cooling system is part of the house as a system principle .
You could probably run even lower temps than you are as part of a constant circulation strategy instead of an on / off zone strategy . I would like to learn even more about what you have , I am interested as part of an ongoing study . Please contact me at [email protected] or by phone ,732-581-3833 . I truly am interested in your system and would like to share ideas that could quite possibly benefit you to a nice end result .