Any thoughts on this wall assembly?

I’m remodeling a house near San Francisco (climate zone 3) and am considering the following wall assembly. From the inside out:
– 5/8″ gypsum board
– 2×4 studs 16″ OC
– 1/2″ plywood sheathing
– Henry VP100 Blueskin as WRB and air barrier
– 3″ nailbase (2 1/2″ polyiso, 15/32″ OSB)
– 3mm Stucoflex WaterWay drainage mat
– 3-coat stucco (over lath and building paper)
The 2×4 framing and 1/2″ ply are existing and can’t be altered… although the framing could potentially be furred inward for a deeper cavity, but at the cost of interior space, which is already tight. The stucco as cladding is required by the City – stucco was on the existing building and needs to be replaced in kind. Interestingly, the nailbase actually will cost less than an equivalent thickness of rigid foam alone, and solves multiple issues, among them removing the need to attach foam with battens, and giving the stucco a firm, flat substrate.
Does this seem like a reasonable assembly, or is there something else I should be considering?
Thanks for any thoughts!
GBA Detail Library
A collection of one thousand construction details organized by climate and house part
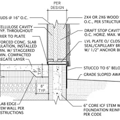
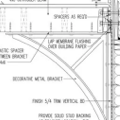
Replies
Eric,
A few random th0ughts:
- Any reason for going with 5/8" drywall over 1/2"?
- While you have the existing plywood sheathing exposed, consider re-nailing it at 4" oc. That increases rigidity a lot. You might take the opportunity to do a few other seismic improvements at that point too.
- Having the WRB behind exterior foam can make sense, but not when you use nail base. Rather it might be better to tape the OSB or plywood layer as your air-barrier and move the WRB out to where it can protect the OSB.
Good luck with your renovation!
Eric,
If you take Malcolm's advice about the WRB location, everything else looks good -- you'll end up with an excellent wall.
Hi Eric -
Great wall assembly as discussed. I have worked on several projects over the years in your neck of the woods and just some key observations:
1. really mild climate with low-grade heating but for extended heating season. This means that air tighness is still important even though it is a relatively mild climate.
2. your low-grade heating comes about the same time period and span as your precipitation. While that means heating while wetting and the forgiveness this imparts, get the water management details right for a really long-lived structure.
3. You did not mention the building code but I am sure you are aware of how tough your building code is, especially given the goal of net zero for all residential new buildings by 2020. Quite a bit of paperwork to add to all the other aspects of performance that you need to work out. https://www.energy.ca.gov/2015publications/CEC-400-2015-032/appendices/forms/CF1R/
Peter
Thanks all for your thoughtful comments!
5/8" drywall is pretty standard here. It seems to be easier to get really flat than 1/2", which is important with the smooth wall finishes which are common. And maybe it gives a little more thermal mass to the building?
Structurally, this is essentially a new build, so we've done a lot of seismic improvements... I should buy stock in Simpson Strong-Tie! Sheathing edges are nailed at 4" OC minimum, 3" OC into 3x framing on the lower floor.
We have already applied the Blueskin to the sheathing, partly because we wanted to get the building weather-tight as soon as possible given that it seems like it's never going to stop raining out here this winter. Since the WaterWay rainscreen mat is also a WRB, I was going to carefully integrate that to flashing at the window and door openings to keep the nailbase dry... does that seem sufficient?
And yes, Peter... our energy code does add a bit of paperwork! But with this wall assembly, triple-pane windows, and 14" of cellulose plus 3 1/2" of rigid foam on the roof, we're doing OK... 41.9% better than our Title 24 requirements. Space heat and hot water will be from a Sanden SanCO2, and we'll have around 8kW of PV... more than the house needs, but my wife and I both drive EVs. We hit .7 ACH50 on the last project, and I'm hoping to beat that on this one.
Thanks again all for your thoughts... it's truly amazing to be able to post questions and get such thoughtful answers!