Are my minisplits modulating or short cycling?

Hello- first of all this site has been an incredible resource. I did most of my own research in adding 4 mini splits to my 1940’s home. It was primarily for AC and heat for the shoulder seasons as we really enjoy our 1 pipe steam heat (although older boiler). I went with 2x Fujitsu (not XLTH) condensers with 2 heads each. A 12k per floor (open kitchen area, top of stairs, attic playroom), and 7k in the master.
Home has been retrofitted with new windows, open cell in the rafters, blown-in in the walls, etc…so definitely on the tighter side for it’s age.
AC worked great during last weeks heat wave (Boston). We’ve now been dropping in to the 40s at night so I’ve been messing around trying to get the heat to be consistent. With a combination of adjusting the offset temp sensor setting, changing the set temp set point, and fan speed, it’s kept the house exactly at 71 over night and day. Upstairs might be 1 degree higher at times, and living room at the opposite end from mini split maybe a degree lower. I have 4 ecobee sensors positioned around so I can get consistent temp readings.
I’ve been reading in to short cycling, run times, and am not sure if I’m cycling or not. Sounds like this can only really be fixed on these units with a wired thermostat. The air temps at top of unit are maybe a degree higher than room temp- not a huge swing.
All the units exhibit this behavior:
Low cfm running all the time (sensing temp)
compressor kicks on
heat starts coming out/fan comes on
Heat for :30s-1 min
heat tapers off
back to low cfm
Repeat every 5-10 min.
From everywhere I’ve read,it seems they should be running for longer times?
There is a setting for “high insulation”, not sure I qualify for that.
Or is this just a drawback with mini splits during shoulder seasons?
Thanks,
Kevin
GBA Detail Library
A collection of one thousand construction details organized by climate and house part
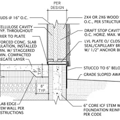
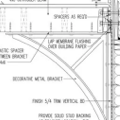
Replies
The 2-ton 2-zone Fujitsu compressor has a minimum modulated output of ~7000 BTU/hr @ 47F, ( http://www.fujitsugeneral.com/us/resources/pdf/support/downloads/submittal-sheets/24RLXFZ.pdf ) and even higher when it's warmer out (which it has been for most hours of the past week.)
When the heat load is less than ~7K, it's going to duty-cycle the compressor no matter what, and the average efficiency is pretty lousy. The described cycling behavior sounds like it's something like a 10-20% duty cycle, but if you extended it to 10 minute cycles the temperature overshoots would be large. When it's only on the order of
You may also be able to reduce the number of compressor cycles by turning one head off entirely, and letting one (usually the lower floor head) carry the whole house load, and just tolerate the floor-to-floor temperature imbalance.
I'm not familiar with Fujitu's "High Insulation" mode, but it's definitely worth trying. "High insulation" doesn't have a well defined meaning, but average home insulation levels in Japan (where this thing was designed) are well below the retrofit measures you've described. I suspect in that mode it would automatically deliver a higher temperature hysteresis for longer on & off times, and maybe intelligently only sample the air temperature after a significant off period rather than continuously, which would be good for operational efficiency. As described on p.34 (PDF pagination) of the the manual:
"10) Heat Insulation condition (building insulation)
Heat insulation conditions differ according to the installed environment.
Standard insulation "00" allows system to rapidly respond to the cooling or heating load
changes. High insulation "01" is when the heat insulation structure of the building is high and
does not require system to rapidly respond to cooling or heating load changes.
When High insulation "01" is selected;
Overheating (overcooling) is prevented at the start-up.
All room temp. control settings (Function 30, 31, 92, 93) will reset to No correction [0.0°F
(0.0°C)].
(... Factory setting)"
https://portal.fujitsugeneral.com/files/catalog/files/DTR_AS115E_01--ASU9-15RLS3_H1.pdf
So it sounds like you'd have to tolerate the temperature number not matching your eco-Bee measurements, and just bump it up and down to stay comfortable, but it'll probably cycle less.
Thank you for this information Dana. Very helpful.
Is my minimum modulated output determined by my compressor or the heads? I have 3 heads attached to 2x 24k compressors currently in heat mode. Wouldn't my min output be 14k? I did a manJ myself, not sure how accurate it is but I came up with 30K cooling, 55k heating for 1800 sq feet (ignoring the finished attic). Not sure what that translates to per hour in 40 degree overnight temps.
Of course it's 75 degrees now so I'll have to count how many times it cycles per hour the next time it gets cold and I'll update this thread. I like your idea of only running the downstairs unit at night.
I had tried high insulation mode briefly but it wasn't keeping it warm enough over night but that was before I had figured out how off the set points are. I'll have to give that another shot. The one unit needed an 8 degree offset.
The process to set these functions on the remote is so awful.
Fujitsu should really team up with the Flair Pucks, Sensibo, Air Patrol etc to allow 2 way communication between the thermostat pucks and head unit. That way it's not just on/off, adjust temp etc but would really allow it to modulate properly. Do you have any experience with any of these?
Thanks again.
The Fujitsu "high insulation" mode doesn't affect short cycling at low load conditions, as far as I know. The only effect that it has is during defrost cycles. Many mini-split heat pump systems automatically ramp the compressor up to ~full speed after a defrost cycle in order boost indoor temperature quickly after a bunch of heat was lost and not replaced (presumably) during the defrost cycle. With efficient enclosures, however, these defrost cycles hardly show up as a blip on the radar in terms of interior temperature...so ramping the compressor speed to "give me all you've got Scotty!" after defrost is completely unnecessary. With the "high insulation" function engaged, the post-defrost ramp is lessened...though, it's still overkill for all of the houses I work on, for example. Fujitsu really ought to set up their systems to follow their normal sequence of operations coming out of defrost, where the compressor ramps up to ~20% on start-up and the system then decides to slowly ramp up or down from there.
What you're seeing with your own system is typical for Fujitsu and Mitsubishi, and perhaps other MSHP manufacturers. The control logic should be improved by the mfr's, but there's nothing you can do, except manual on/off during these kinds of days (as mentioned by Dana) to improve efficiency.
Thanks John. I experimented switching it to high insulation mode last night and didn't really notice a difference either, so that makes more sense. It looks like I was getting 10 cycles per hour (:45-1min on, 4.5min off). I have a toddler and my wife works from home so we need to keep the house around 71 24/7. I did only use the downstairs unit last night and that worked fine although it only got in to the low 60s last night.
Here's a solution I am thinking of: a combination of Sensibo remote/thermostat, ecobee wireless sensors, and IFTTT (web based triggering system). It would go something like this.
Set minisplit to 80 degrees, but lowest fan.
Use average of ecobee wireless sensors for room temp sensing (or just the sensibo remote, but that has to have line of sight to unit).
Create recipe in IFTTT "If ecobee temp drops below 71, turn on mini split". If rises above 73, turn off split"...or switch to AC mode!
This would limit cycling to the homes' actual heat loads, force longer run times, increase efficiency. Unfortunately IFTTT only works in 2 degree increments so you might have to put up with a bit wider temp swings. You'd also hear the beeps a lot.
You could also set triggers like for todays 80 degree forecast, so "if today's temp forecast is above 75 degrees, turn off unit".
Lots of possibilities.
Or just buy a wired controller and hire an electrician...
Just my 2cents, thanks!
"Is my minimum modulated output determined by my compressor or the heads? I have 3 heads attached to 2x 24k compressors currently in heat mode."
Unless you have a VERY large ductless head, the minimum output limitation is at the compressor. When only one head is calling for heat, it'll be taking 100% of the compressor's output, and would have to ramp up to well above the head's minimum modulation level rather than modulating with the room load when the load is less than the compressor's output.
I'm now understanding that you have TWO 24K compressors, two heads per (4 heads total)? At 6.8K per compressor the minimum output at +47F would be 13,600 BTU/hr, and when it's in the 50s out it'll be 15K+.
It's sometimes better to go with a single compressor to support the 3-4 heads rather than two. The minimum output of a 3-ton 4 head Fujitsu AOU36RLXFZ is 11K @ +47F, which is a bit more modulation headroom than the 13.6K of a pair of 2-tonners.
Since I only have one unit on the first floor I’m going to try and get by heating with just that unit/compressor and hope the heat rises evenly for the next couple weeks.
Any ballpark cost for this to run in this cycling mode? If it’s 2.3kwh, and It’s heating for 10 minutes per hour, is it effectively 1/6 of 2.3kwh (not including head fan etc). @$.20/kwh that’s roughly $2/day running it 24/7?
Just trying to compare to my boiler usage.
In a low-duty-cycle on/off cycling mode you should still be able to get a COP of 2.8-3 (but not it's steady-state 4+ ) when it's 45F or warmer outside. For rough comparison purposes assume it's about 10,000 BTU of heat per kwh of power consumed (a bit less than a COP of 3). It's as-used efficiency might even go up once it's cold enough that it's hitting more than a 50% duty cycle and modulating a bit, even though the steady-state efficiency would be slightly lower at the lower outdoor temperatures where there is enough load to do that. Most decent ductless systems running a high duty-cycle at +45F would deliver a COP of 4 or better at or near it's minimum modulation level, but that drops to about 3-3.5 when it's 30F outside, and ~2.5 at mid to high speed at 20F outdoors. The details will vary with model, manufacturer, refrigerant charge levels, outdoor dew point etc. At 45F+ there are no defrost cycles to speak of, but the power burned during the long standby intervals adds up to a real as-used efficiency hit due to lack of load.
For the boiler you'll have to figure it out by source-fuel BTU content x efficiency, then discount it for distribution & standby losses, as well as residual electricity use for pumps & controls, etc. It's not a simple thing to model, but measuring the duty cycle of the burner in a similar way would be a good start. The type and size of the boiler matters too (a LOT). A right-sized modulating condensing gas boiler would have very little standby loss, whereas 3x oversized cast iron oil fired beast maintained at 140F lo-temp could be spending more than half of it's energy in standby + distribution losses.
Every day the hour by hour oad profile will be different, so the real comparison should be simply normalized to dollars per million BTU ($/MMBTU). Assuming a low-duty-cycle ductless operating in temperate outdoor weather delivers 10,000 BTU/kwh at 20 cents/kwh it's $0.20 x 1000,000/10,000 = $ 20.00 MMBTU.
Buck-fifty/therm gas burned at 95% efficiency in a mod-con boiler would be $1.50 x 1,000,000 / 95,000= $15.79 / MMBTU, a bit more when you factor in the pumping and distribution losses.
$2.75/gallon #2 oil burned at 85% efficiency in a high mass boiler costs $2.75 x 1,000,000/(0.85 x 138,000)= $23.44/MMBTU if it were running at least a 30% duty cycle, but at a sub-10% duty cycle the high standby & distribution losses brings it closer to $30/MMBTU, sometimes more.
Hi Dana. Thanks for these details, very helpful.
I have a 192k input nat gas steam boiler, with 152k output (82%). It's old and qualifies for MassSave early replacement (whatever year cut off that is).
Here are a couple additional data points that I've come to from ecobee run times.
In October with an average of 12 HDD per day (base 65), I averaged 1.45 burning hours per day...approx 280K BTU, or 11,600 BTUs per hour. With long off times I imagine pickup/pipe losses of 25% or more. That would put me at around 8500 BTU/hr or less depending on the day, so I think that verifies your point to the short cycling at 7,000 BTU/hr.
For comparison in dead of winter- In January with 40 HDD/day, I was averaging 5.17 burning hours - ~1,000,000 BTU/day - 41,000/hr with 14 cycles per day. Again, not heat loss but boiler burning time. House is 1812 sq ft not included basement and semi finished attic space.
Rough math here: 82% boiler nets 82,000K BTU per 100,000. Take another 33% off for standby losses in the shoulder seasons might leave 55K net? (1,000,000/55,000)*$1.50 = $27 MMBTU?
I'll test this Fall using just the (1) 10K head heating the first floor. When it can't keep the second floor warm enough we'll switch over to the radiators. Unless you can think of anything else I should consider?
So, the mid-winter heat load rough-calc...
With 5.17 hours/day of 152K output the burner put 785,840 BTU/day into the heating system, on a 40 HDD day.
That's 785,840 / 40= 19,646 BTU per degree day, which (/24=) 819 BTU per degree-hour.
Boston's 99% outside design temp is +12F at Logan Airport, but most locations inside of 128 further from the water would be a bit cooler- let's call it 8F.
The presumptive heating/cooling balance point (the HDD base) is 65F, so with an outside design temp of +8F you have 57F heating degrees.
So the implied heat load (including distribution & standby losses) at +8F outdoors can't be more than (and is almost surely significantly less than, given the oversizing factor and sub-25% duty cycle even during the colder months ):
57 degrees x 819 BTU per degree-hour = 46,683 BTU/hr.
If that were real it would be pretty high for a tight 1812' house: 46,683 / 1812 = ~26 BTU/hr per square foot. Most reasonably tight 2x4 framed houses will come in around 20 BTU/ft @ 0F (65 heating degrees) if the foundation isn't insulated, closer to 15 BTU/ft @ 0F with an air tight and insulated foundation. I'd hazard that your true load is under 40K.
Is the boiler room nice and toasty warm during the dead of winter? It's often the warmest room in the house with old steam systems, and an indication that the heat load on a fuel use calc is going to be quite a bit higher than a Manual-J.
Each AOU24RLXFZ (non-XLTH) is good for 24,000 BTU/hr @ +17F. It's highly likely that a pair of them will be able heat the whole house even at 0F outdoors, if you have enough capacity in the heads. The ASU12RLFs are good for 13.5 KBTU/hr as long as the compressor is keeping up, a 9RLF is good for 10.2K, and each 7RLFs are good for 8.1K. You've mentioned two 12RLFs and a 7RLF, which adds up to ~35K of heat output.
Even if the fourth head is another 7RLF (did you say what it was?) that would put you at 43 K BTU/hr, which I'm pretty sure a pair of AOU24RLXFZ would still just about keep up with @ 0F outdoors.
Don't be afraid to run them all winter- the as-used efficiency of the steam boiler with all it's distribution losses is pretty lousy. It might be cheaper to run the steam boiler when it's under 20F outside (or cross over at some other lower temperature) but the binned hourly mean temperature for January in Boston is closer to 30F, which is a reasonably efficient operating temperature for the AOU24RLXFZ : https://weatherspark.com/y/26197/Average-Weather-in-Boston-Massachusetts-United-States-Year-Round
At 30F you have 35 heating degrees below the 65F base, or a heat load of a bit less than 35 x 819= 28,665 BTU/hr. That's PLENTY of load for a PAIR of 24RLXFZ, but only a bit more than half the max capacity of two of them at 30F. That's near the the sweet spot- even with both systems running they should both be modulating comfortably and nearly continuously at low to mid-speed at the average wintertime outdoor temp, delivering an average COP in the ~3 range until the load is so low that one or both compressors are cycling on/off quite a bit. You'll only have to back off shut one down during the shoulder seasons.
Another data point that falls out of the crude heat load calc: At +47F you have 18 heating degrees, for a load a bit less than 18 x 819= 14,742. The min modulated output @ 47F is 6100 BTU/hr, or 12,200 BTU/hr for the pair. That's means at 47F still enough total load to keep both modulating most of the time at very high efficiency, so when the outdoor temps are starting to be consistently below 47F (roughly the beginning of December through half-past March, give or take a few weeks on either end) running them both will be efficient than running just one, assuming the heat load is reasonably evenly split between the two.
Ouch! Here I thought I had been doing a decent job improving my envelope (new windows, blown in for walls on first floor, open cell in rafters) to overcome my old boiler. Pipes are insulated, I increased the main venting, a nice even heat throughout the house...and I'd hate to give it up.
That said this opened my eyes a bit. I ran your BTU/degree hour calc with some more recent data from January and I came up with 725 BTU/degree hour. Ecobee only stores data for a month and I lost a bunch of data so this was the most recent.
1812 sq ft are the 2 main floors. There is an additional 230 sqft finished playroom in the attic (with the 4th 12k head) that has a radiator, but is usually never on...kid is too young and I use the office maybe once a month so I just turn it on as needed. Brookline, MA location.
Basement is almost 1000 sq feet, unfinished, 1/2 above grade with a bunch of replacement windows at one end. It also has 2 radiators on the ceiling which are turned off. The boiler room/basement is definitely not 80 degrees over the winter, I'd guess a warm 70.
I think the true radiator EDR I measured is down to 303 sqft. We lost a couple rads in reno, and basement and attic are turned off. That puts me closer to 72k (303*240) + whatever pickup factor is used these days with steam, I've seen zero to 33%. Regardless well under 100K for the radiators independent of any heat loss calcs. So I'm at least 2x oversized.
I digress...back to the splits. First floor head is 12K @ 875 sq ft (office addition off the back not included). Top of second floor hallway is another 12k @ 575 sq ft / 2 bedrooms, and a 7k for the master @ 230 sq ft. The attic is 230 sq ft and also has a 12k head (rarely used).
So, what would the 12k+7k on one condenser, and the 12k on the other condenser cost me to heat my home for the whole winter? From 9/14/16-9/14/17 I used 1492 - (12*22=264 domestic heating) = 1228 therms for heating.
Thanks again for all your help, Dana. This has been incredibly insightful.
Kevin
If the basement foundation walls aren't insulated and is coasting along at 70F without the radiators is a HUGE heat leak. A typical 100 year old fieldstone foundation has a whole-assembly R value of about R1.5-2, (a U-factor of U0.33 to U0.50) a typical poured concrete foundation of the era an R1-R1.5 (U0.67- U 1.0). Assuming a 25' x 40' rectangle (=1000 square feet) you have 130' of perimeter, and if half is above grade call it 4' of exposure, for 520 square feet, less say 70 square feet of windows & doors is 450' of above-grade wall. Assuming a best-case U0.5 (lowest heat loss) , and a (70F-8F=) 62F delta from indoors to out, just the conducted losses out the basement wall would be:
U0.5 x 62F x 450'= ~ 14,000 BTU/hr
With the better data using 725 BTU per degree-hour and 57 heating degrees the whole house load @ +8F is ~41,325 BTU/hr. So the basement wall losses would then be roughly 1/3 the whole house loss(!).
If you leave the boiler off it'll be a lot cooler than 70F in the basement, and those losses will go down to something like 45-50F on a +8F day, for a delta-T of ~37F instead of 62F, and wall losses of U0.5 x 37F x 450'= 8,325 BTU/hr.
That means the mini-splits would only have to support a peak load of 41,325 - 8,325= 33,000 BTU/hr
For 1800' of space that's now about 18 BTU/hr per square foot- still implying an uninsulated basement. If the basement walls were insulated with R10 of continuous foam (code-min is now R15), it would cut that 14K loss to about 3K even with the basement cruising at 70F, not 45F. With the walls insulated and air tight with the boiler heating the house the duty cycle on the boiler would drop, but the temperature in the basement would probably rise by at least 3-5F, making the basement the warmest place in the house even without the basement radiators running. So if insulating and air sealing the basement peels another 11K off the load (probably will), the boiler would see a load (some of it parasitic) of 34,000 BTU/hr, but the mini-splits would only see a load of 28-30,000 BTU/hr, which would be more like the ~15 BTU/hr per square foot expected range.
As clearly beneficial as insulating the foundation is when half of it is above grade and there's an oversized boiler in the basement, under current programs I don't believe work that would would be subsidized through MassSave.
Sanity check: 725 BTU/degree-hour is (x 24=) 17,400 BTU per degree day. If you burned 1228 therms @ 82% efficiency it delivered 0.82 x 1228= ~1007 therms or 100,700,000 BTU of heat into the house, which at 17,400 BTU per degree day implies a 100,700,000 / 17,400 = 5787 HDD season, which is a credible number for Brookline. The weather station KMABROOK33 in Brookline logged 5283 HDD65 in the 12 calendar months beginning 1 June 2016, which is within 10% of the 5787 HDD65 estimated by fuel use. Some of that annual gas use probably went to hot water &/or cooking (?), and 82% combustion efficiency is probably a bit optimistic. The cooling/heating balance point might be a few degrees away from 65F too. Either way it's the right ball park.
Assuming you heated solely with mini-splits they wouldn't have to deliver the full 100,700,000 BTU into the house, since they won't be keeping the basement warm. Size-wise the mini-splits are in the range which should hew reasonably closely to the published HSPF of 9.50 BTU per watt-hour (= 9500 BTU/kwh) as a seasonal average. It'll be higher than that during warmer weather, lower than that during cold snaps, but averaged over the season that's roughly the right range. So if it were to deliver the whole 100,700,000 BTU it would use 100,700,000 / 9500 = 10,600 kwh / year. But if you don't heat the basement to 70F it'll probably fall somewhere between 8000-9000 kwh/year. Assuming a (probably worst case) 9000 kwh and 20 cent electricity, that's ~$1800 /year, or about the same as using the beastie boiler (with basement losses and all) with buck-fifty / therm gas. The state average residential gas prices last winter were in the $1.30 / therm range. If that remains true this coming winter, even with the lossy basement it's likely to be marginally cheaper to heat with the steam boiler when it's below 20F outside, but also likely to be marginally cheaper to heat with the mini-splits when it's above 30F outside when the as-used efficiency would be well north of 10,000 BTU/kwh and the basement losses would be much smaller. When it's 40F+ outside the mini-splits will likely deliver more than 13,000 BTU/ kwh, which would very clearly cheaper, even without factoring in the basement losses.
Estimating the exact financial crossover point is difficult, since the model of the house and the basement losses are far from perfect, nor is the mini-split efficiency model across load and outdoor temperature going to be perfect. But from both a local and global emissions point of view the mini-splits are going to be significantly greener even at the average regional grid generation mix, and MUCH greener if you under contractor a 100% renewables power supplier.
Sorry for the late response- been a busy week. It sounds like my old boiler really is wasting a lot of energy with it being old, and grossly oversized. It's nice to have some data to back that up, so thank you. If I downsized to something more in line with my radiators it would probably be around 85k output, with an AFUE of 82%. I think we are being overly generous rating my 30+ year old system at 82%, but yes all that heat ends up within the envelope somewhere. I imagine that would make running the splits from an economical perspective much harder, considering it's a toss up right now.
That being said, with the weather dropping into the 30s later tonight, my single 12k unit is running much better. With it 48 degrees outside right now, it is running at medium fan for 12.5 minutes, low fan for another 2, and then sensing temp for another 2.5 minutes...so 87% duty cycle? @ ~13,000 BTU/hr that would put it around 11.3k BTU/hr @ 48F? We came up with 725 btu/degree hour (17*725) which would put it at around 12.3k heat load, include the basement and lossy pipe system? That's a pretty close ballpark.
If it did this for 24 hours, would it cost me (11.3/13)*.20 cents *24hr = $4.10, maybe a bit less?
Thanks again Dana.
Kevin
You would need to sub-meter the mini-split to know how much power it's actually using. The power draw varies (a lot) with the load. But it sounds like it's running reasonably long and efficient cycles. That should improve to near-continuous modulating cycles as the load increases.
Steam boilers have to be sized to the radiation in order for the system to work properly. A steam boiler right sized for your radation is still going to be way oversized for your actual loads, but it will work more efficiently than what you have. Whether its worth putting money into it vs replacing the steam system with something else is an open question with no easy answers.
Thanks, that makes more sense.
I thought maybe with the early replacement boiler program through MassSave ($1800) I could get it swapped out for a reasonable cost...but that is quickly escalating towards $10k+, plus installing a new chimney liner, etc...
Sometimes it's cheaper to replace it with a right-sized hydronic (pumped hot water) system than it is to upgrade a steam system. If the radiators can be reworked for hydronic use (sometimes it's easy, other times not) and they're big enough to deliver design-day heat at the lower temperatures of hot water vs. steam (usually the case) it's preferable to yarding them out to be replaced by fin-tube baseboard. With hydronic systems you can use condensing boilers or condensing water heaters, which will improve the efficiency by large amount.
This takes quite a bit of analysis to figure out, but doing most of the analysis yourself leads to better insight and better decisions.
If the foundation isn't air sealed and insulated it might still be a better bang for buck to take that on first, before replacing the boiler or the entire heating system.
That would be quite the project I'm sure.
You mentioned that spray foaming the basement would drop the house load almost 1/3 on design day. Could I net a 15-20% savings on fuel with my current boiler by doing instead?
The answer is "probably yes". As a point of reference:
The above grade exposure on the foundation at my place averages about 24", not half the total basement height. The basement is about 1500' total, 300' of which is an addition where the foundation was poured in an R17 ICF, the rest was a circa 1923 foot-thick poured concrete wall below grade, stepping to 8" thick above grade. You probably have roughly twice the amount of uninsulated above grade foundation exposure that I started out with, and probably about the same U-factor. The low temp heating system (~125F water max) & low mass boiler in my house has nowhere near the standby & distribution losses to the basement of a the typical 1-pipe steam system.
After installing 3" of reclaimed rigid polyiso (~R15-R17) on 95% of the old foundation walls, foundation sill & band joist, and sealing up the most obvious stuff (without benefit of blower door testing) the average temperature of the basement in mid-winter rose from mid to high 50s F to the mid 60s F, and net fuel savings was a bit more than 15%. The coldest the basement gets down to now is ~63F during the spring shoulder season when the ground water is still cold (most of the slab isn't insulated) and the heating system isn't running much (delivering lower distribution losses to the basement.)
The odds are that with 2" of HFO blown 2lb foam (~R13-R14, though code-min is R15 it may not be worth bumping it to 3") you'd get a bigger fuel-use reduction than me. Just how much depends on how air-leaky your basement is, and how much a continuous foam-over seals it. Replacing or adding storms to any single-pane basement windows would also be rational. Your boiler & steam plumbing's standby & distribution losses are at least 2x mine, and may be more than 5x mine, and your above grade foundation wall area is roughly 2x mine.
The difference between your house from the average uninsulated basement is the greater total area of exposure above grade, and your somewhat higher idling temperature in the basement. More area + bigger temperature difference = bigger heat loss.
In a mid-winter infra-red image your house probably looks like a rocket firing up on the launch pad , with a huge orange glow down below, much cooler IR emissions from the insulated house above kind of like Marc Rosenbaum's former house prior to insulating the basement, only with much taller stripe o'f orange than his mere ~12-15" of exposure:
https://www.greenbuildingadvisor.com/sites/default/files/images/Rosenbaum%20-%20thermogram.jpg (see: https://www.greenbuildingadvisor.com/blogs/dept/guest-blogs/basement-insulation-part-1
Large heat losses from uninsulated basements & crawlspaces are pretty common, since only recently have building codes begun to require foundation insuation.
http://www.rrso.ca/images/basement_new1.png
http://techno-fandom.org/~hobbit/hse/log/23728/IR_1764-ne-close.jpg (see: http://techno-fandom.org/~hobbit/hse/log/23728/foundex/ )
http://naturalgasefficiency.org/files/2016/01/IR_BasementWall2.jpg
http://naturalgasefficiency.org/files/2016/01/IR_BasementWall_Outside.jpg
https://www.fairfaxcounty.gov/energy/energyactionfairfax/images/insulation_and_foundation.jpg
Care to add yours to the gallery? :-)
Unfortunately it seems many builders & local inspectors in MA seem to think it only needs to be insulated below grade, putting a few inches of foam on the exterior only up to grade level, and leave the much lossier above grade portion of the foundation uninsulated. Why the concept isn't sinking in remains a mystery, but I see many new houses being built that way!
I came up with around 30% of the 1000sqft as above grade. There are definitely a good amount of leaks between the single pane foundation windows, old door, outside faucet piping, etc. I was probably a little high on the winter temps down there, it has to be more in the low 60s. The basement losses are probably closer to 1/4 than 1/2 but regardless I've got a lot to do down there to tighten it up.
Someone at work might have an IR camera I can try out this winter and I'll be sure to post it here if I can locate one.
Thanks again Dana.
I'm a bit confused- you have 1000 square feet of foundation wall area, with about 30% (300 square feet) of foundation wall that is above grade? I was reading it as 1000 square feet of basement floor area. I assumed the floor is all below grade.
Is it a walk-out basement, with 30% of the basement/foundation wall fully above grade?
The simple U-factor calculation is for square feet of above-grade exposed wall (not floor) area. My crude calculation was an estimation for 450 square feet of wall, not counting windows & doors, or below-grade wall losses. If the exposure was only 2.5', not 4', it would be something like 275-300 square feet of wall area, if my guesses on the house footprint were close. (Go ahead and measure it- why guess?) A better description of the foundation construction (including thickness & material etc) will make a difference in U-factor too. Or you can just assume that it's a big heat loss & air leak (which it is), and worth fixing.
If you're in an estimation & calculation mood, a tight wood framed single pane has a U-factor of about 1.0, a steel framed basement window is closer to U1.2, almost 4x the heat loss of a U0.32 code-min window. Even a cheap sub-code clear glass vinyl double-pane comes in about U0.50, a real improvement! A solid 2" exterior door has a U-factor of about U0.5. A thin paneled door about U0.75-U0.85. Replacing it with a foam insulated steel door runs U0.25-U0.40.
Hi Dana. A little update from using my splits for heat for the month of October.
1) It's really hard to keep a set point in a shoulder month like we've just had in MA, I'd say almost impossible at least with the Fujitsu brand without a wired controller. I'm a tech savy guy, I've got 4 ecobee sensors logging temps, a Sensibo IR remote so I can control the 1st floor split from my phone, IFTTT to turn the unit off so it doesn't blow past setpoints, etc. I'd check the temps from work and adjust as needed. Countless adjustments to temp offsets in the function menu, switching back and forth from standard/insulation mode, and I couldn't find any real setup where it was set it and forget it. Maybe a day or two would be steady and then if temps dropped I'd wake up to a cold house and have to over compensate for it. I was only using the 2 main 12k splits, 1 on each floor (to test your theory of a 30k heat load).
Yesterday it seemed to not really be heating much during the day, falling to almost 65 when I'm aiming for 70, so I reset the insulation mode to standard, and cranked the unit up to 88 before I went to bed. I also raised the 2nd floor hallway unit a couple degrees just to compensate for the coldest night of the year.
I wake up at 4am and the entire second floor is a perfect 70 (without master unit on). Downstairs is 65. That unit is running 30 seconds on, 1 min off and really not putting out much heat. With almost 1000sq feet on the first floor, 28 degrees out, and 1000 sqft of uninsulated basement that is probably in the 50s, I feel it has finally hit it's limit. The 2nd floor unit then hits defrost mode which was quite jarring, so I powered them both off, and turned on the boiler and we're nice and toasty at 72.
7am I turn on the kitchen unit again to see what type of heat I can get at 28 degrees- it blasts super hot air for probably 10 min on full blast before it his the defrost cycle. I can't imagine running them like this would be very efficient, on top of the annoying sounds.
I've added a floor plan with unit locations, as well as thermostat sensors (red dots), along with their temps from 9pm to this morning. It was 35 degrees last night and dropped to 28 by this morning.
Does this seem like normal behavior for this type of set up? Would a wired controller on the first floor solve any of these issues? I think you mentioned sub 30 degrees might be the crossover point for the boiler, but I can't imagine using these as primary heat even at these temps.
Thanks for all your help. Again, these were installed primarily for AC but I'm trying to make these work if and where it makes sense for heat. If I can't get steady temps I can't imagine an average homeowner making it work. Maybe I was just sold the wrong brand.
Hi, I had similar problems with a Fujitsu 15RLS3. I ended up installing the wired remote thermostat and this solved the short cycling problem. I still needed to change the set point temperature to higher in the cold winter periods to achieve a target temperature on average in the first floor than in the warmer shoulder periods. That has more to do with lack of insulation in my walls than anything else. Short cycling was gone though with the wired thermostat. The install was very expensive, I wondered if i could have done it myself ...
Thanks Matthias. Did they have to take apart the unit to hook it up? From the limited manuals I've seen, it looks like they have to disassemble the unit and install a new controller board. That would be out of my comfort zone. If it's just running the wire and hooking up to the terminal I could probably do that myself.
I couldn't believe it was short cycling with such a large heat load. Really frustrating. How often do you need to change the set point?
In my case, no need to install new motherboard. The unit shortcycles because the standard sensor is in the unit itself, hence too close to where the heat comes out and my unit is installed a bit in a corner, so the area around it gets hot fast, but the house is cold. The remote thermostat solved that problem. I change the temperature setting once a month maybe as the season gets colder I Set it higher, but it depends how variable the weather is day to day ...
After having the boiler running for 12 hours, and the temps being a little milder around 45, I decided to turn the 2 main splits back on. I set them both to 76 and had the boiler set to 69 as a back up. They both modulated very well and the boiler didn't kick on at all overnight, so it kept the house at least 69-70 degrees. It was probably 35 in the morning, and we were going to go in to the 20s so I switched them off knowing they'd be going in to defrost cycles.
I wonder on start up if there is some sort of baseline setting that is recorded, because they behaved much better than before. Would a unit that started up with say a 70 degree outside temp that dropped to 40 degrees behave the same as another unit that went started at 50 and went to 40. Would cycling the power every could days change the way it works?
I'll probably continue with the boiler as the main heat and use the splits in addition for the 35-55 degree outdoor temps. This is automated with IFTTT and Sensibo.