Are there decorative surface mounted wiring options?
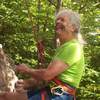
Recently I read an article about heating pipes disguised as skirting boards (baseboards). I seem to remember seeing electrical outlet strips in a lighting store which consisted of a long plastic strip the depth of a plug prong with parallel grooves the entire length. You could push a plug in anywhere along the length and it would work. If there was an attractive option to running wiring inside the wall and making big holes for the outlets, we could have much tighter houses.
GBA Detail Library
A collection of one thousand construction details organized by climate and house part
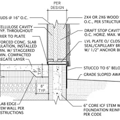
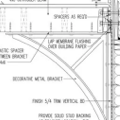
Replies
This is as close as you'll get and still pass inspection:
https://www.bocci.ca/22-series/
Surface mount is hard, about the best look you can hope for "industrial loft".
Those “parallel groove” plug strips you mention are notoriously unreliable and dangerous. I would NEVER use those in ANY application EVER. If you use one of those, you’ll say you “push a plug in anywhere and HOPE it’ll work”, because it often won’t. Stay away from those things!
Back in ye olde days there were actually many options for surface mount wiring, primarily out of necessity: almost no one had wired houses, so nearly everyone had to do retrofit work to electrify their houses. There were wood trim pieces made for wire among all kinds of other things. Nowadays, we have “wiremold”. Wiremold ranges from slightly ugly to full-on eyesore (no offense to the manufacturers), and is usually regarded as a last resort when its impossible to fish the wire anywhere where it would be concealed.
If you need to hide wiring, my recommendation would be use MC cable or EMT conduit, then route slots and find other clever ways to hide the stuff. MC and EMT act as armor for the wiring so that you can meet codes without burying the wiring as deeply in the wall. The trouble spots will be corners since you’ll be limited in bend radius, especially with EMT.
If you want to wire your house with an eye towards air tightness, try to keep most of your wiring in interior walls. Using exterior foam also helps, since it allows an exterior side air barrier which makes interior wall penetrations less of an issue. There used to be a really nifty plastic box specifically made to preserve an air barrier, but it’s no longer available, unfortunately.
Bill
Thanks for the info. I found some of those nifty boxes you mention, but in a remainder box in my local hardware. I bought them all. They're useful where I don't care so much about the decor.
We use some "parallel groove" things to distribute power at work, seems pretty reliable to me. But those are 3 phase, require a tap box to be able to plug stuff in, and are pretty ugly and expensive.
Free information on what we use at on the "open compute project" website.
In all seriousness: Bill, I'm assuming you're in VA, but if you're ever in Oregon it would be great to grab a coffee.
Those three phase systems with “tap boxes” are actually known as “bus ducts” and the “tap boxes” are actually known as “bus plugs”. They are very different from the parallel groove type of plug strips. A vendor I use at work and am friendly with specializes in refurbishing used busduct and accessories and can save a lot of money over new if you are in need.
Bus ducts come in many flavors, but typically have several busbars inside held parallel between insulators. The bus plugs have prongs that engage the busbars securely. Systems like this have readily available bus plugs up to 200+ amps, and the bus ducts are often rated over 1,000 amps. These systems are very common in industrial facilities since they allow for flexibility in placement of large electrical machines.
Datacenters often use a small variant of busduct known as “starline”, which is usually a 225A 120/208Y configuration. I’ve used this before. It’s a good product, but not cheap, and it has some limitations in some facility designs. Like anything else it also has some advantages, so you need to choose carefully when doing the initial design.
I’m based in the SE Michigan area. I have been frequently in the DC metro area, which includes a big chunk of eastern Virginia, although I haven’t been out there in a few years. I very much miss Maryland cream of crab soup. I hope to be back out there this fall to visit friends.
I’m actually in Denver at the moment, South Aurora actually. This is the land of rooftop solar. I have a friend in Redding, CA who I should visit sometime. That’s not so far from Oregon. He reminds me you like to say oreGUN out there as I recall, not oreGON :-)
Bill
You can get plenty tight doing it the same way with the same boxes as we've been using for 60+ years.
Passive tight if you want.
I know. I was just hoping for an easier and better way than with the clunky old boxes we've been using lo these many years.
I was involved with a modular company for a little bit. All their wiring was done in the factory, when you put the boxes or mods together you just connected automotive style clip connectors in the attic. Some sort of modular wire system would be slick where you had prefit sealed boxes with pigtails and quick connectors or a shark bite inspired fitting that would be rated for in wall and the ability to plug the device in like a breaker into the box after drywall.
Problem I have is sealing the wire before device fitout, then the electrician installs the device and loosens the seal while jacking the wires around. I do use exterior sheathing as air barrier and seal all exterior wall wire holes from stud bay to stud bay so I have very little leakage, but I still attempt to seal wire going into the box. We have to seal the box to drywall or use foam gaskets😂 to pass inspection. I prefer the fiberglass boxes, the cheap blue ones have so many holes in them from the start.
Also have tried the putty for wires into box, pretty tedious but worked well and stays pliable. Gun foam is so much faster though. Gasketed boxes will put a slight hump in the wall, not a fan. Tried those Lasco pans that surround the box in the wall, that was a waste of time. Definitely opportunity to solve a problem.
Nils,
If the air-barrier isn't the drywall or interior membrane, why worry?
I'm not worried. But if everything electrical is nailed or screwed on after the gyprock, I won't have to fish any wires through holes, nor would I have to line up holes in the gyprock with studs and wires, and any changes would be dead simple. Miniaturization worked wonders for computers. It is time for a similar upgrade for house wiring. On another tack, why are outlets always one hammer length above the floor? Wouldn't thirty inches above the floor be more convenient?
It just seems like a retrograde way of approaching electrical. Both it and plumbing often used to be exposed on the interior or exterior of houses. Now it is safe and invisibly supplied in the structure. Why bring it out again?
At the risk of cementing my reputation as a curmudgeon, while I appreciate people bringing fresh eyes to the way we build which may lead to improvements, the dislikes for certain things, like drywall, or wiring practices here on GBA, often seem to c0me from a theoretical displeasure not rooted in experience. I've never heard builders who have done electrical work complain about the problems 0f making holes for boxes, or running rough-ins.
Outlets are usually close to the floor because the appliances that get plugged into them are typically floor mounted lights, vacuum cleaners, clock radios etc, where a higher outlet would leave a visible dangling cord, but there is nothing to stop you putting the outlets at any height you want.
Outlets are often a hammer length up from the floor because that is the time honored way for electricians to measure for them — literally using a hammer as a sort of measuring template. Maybe not ideal, but it gets the job done. There is no reason you can’t spec a different height if you want. I like to use around 18” or so for easier reach without getting so high as to cause the problems Malcolm mentioned.
I have to agree with Malcolm here too: most homes require a lot of one-off custom work with EVERYTHING, wiring included. Working with materials like a roll of wire and standard boxes allows for simple and quick field installation wherever things may need to go. Imagine for a moment we had a slick, modular wiring system. That means standardized parts, like 6 foot pieces of track. Everyone who has done field work knows that Mr Murphy shadows you as you work, and will put a vent at the exact 6 foot mark, then a window about 47” from there. If only you had something a little more flexible in measurements than those slick, pluggable 6 foot tracks!
That’s just one example. With a typical 250’ roll of NM cable, an auger bit in a 1/2” drill, and some single gang boxes, you can place outlets and switches pretty much anywhere they’re needed with reasonable speed and not much downside. Need some air sealing? Squirt some canned foams in the top and bottom plates of the walls where any wires penetrate. Boxes can be trickier to air seal, but not too bad if you’re careful, especially if you have the other side of the wall open. Using the fiberglass “hard boxes” I’ve often recommended here also helps.
In this case, there are some good reasons things tend to be done they way they are. Nifty prefab systems usually come with limitations in how they can be installed, and those limitations inevitably limit what you can do with them. A simple roll of wire can be cut to whatever lengths you need, pulled around corners and at angles to avoid obstacles, many other things.
Bill
I go higher too, around the 18” mark, makes a surprising difference without looking out of place. And, just so happens most framing hammers are the right height. Gift your electrician, no faster way to set boxes consistently using the tool you need to install as your gauge.
You can install switches and outlets before drywall.
Why? Boxes wont be exactly flush so you'll have devices too far behind the plane of drywall, electrician would have to snap the tabs off every device and hate you, and drywallers will bitch about nicking their rotozip bits on the top and bottom of every device in every box they cut out, even if devices get taped some will have mud, texture, paint on them. Some will get mudded in and youll have to carve out mud to adjust.
Unless you like dealing with PIA situations put a few temp outlets in the bath circuits and wait.
You should install devices (switches and outlets) last, ideally after painting. The usual order is to do the rough electrical shortly after framing is complete, but before drywall. This allows boxes and wiring to be easily installed. You push the wire into the back of the boxes so that it’s out of the way for the drywall guys. Drywall guys come, put the drywall up, and router around the outline of the boxes.
At this point, some people install devices, but then the painter tends to slip on stuff and that looks bad. I like to install devices after painting, which keeps devices and cover plates clean, and saves the painters time since they don’t have to remove cover plates or mask anything.
The plaster ears are there to keep devices even with the level of the finished drywall so that the plates sit properly. If you install the devices before drywall, those plaster ears get in the way. Without plaster ears, you need to use the little shim pieces to bring the devices up flush which is a fussy and time consuming process.
If you need a few power outlets during construction, just temp in a few beaters around the site in easy spots like the first box on a feeder from a panel. The crews can use extension cords from those several temp outlets. After painting, take the beater outlets out and put in the permanent ones. I’ve done this myself many times.
Bill
I’ve used this before for networking/video cabling. It’s kinda decorative:
https://www.legrand.us/wire-cable-management/raceways.aspx
I think the Panduit LD series raceway is much easier to work with, and better appearance (smoother finish). I still avoid it like the plague for residential work though, even having installed miles of the stuff commercially.
Fish wiring in walls wherever possible. Use string, a weight, and a wire coathanger. Cut diamond-shaped holes in the drywall to work through since they’re easier to patch later, and give more work room with fish rods compared to square holes. It takes practice to get good at it, but will allow a MUCH cleaner installation.
Bill
Thanks for the link. It is exactly what I was looking for.
Nils,
It's worth remembering that you can't run Romex wire in conduits, so you will need to work out how to transition from it to un-shielded wire going from each circuit to the raceways.
The raceway guys make transition pieces to go between EMT (or anything else really, it’s just a slim “box” with a knockout on one end and a raceway fitting on the other) and the surface raceway. Those fittings are the proper, and code approved, means of transitioning between surface raceway and other types of cabling.
Wiremold V50 (or V100, I haven’t used it in a while) makes a very compact fitting that gives you an NM cable clamp. You can use this fitting to transition to raceway from NM cable, just slit the jacket on the NM so that only the inner conductors (which are equivalent to THHN) are inside the raceway.
You’re generally only permitted to run NM inside of conduit or raceway for short lengths such as providing physical protection to the NM cable on vertical drops from a basement ceiling to a wall-mounted receptacle box. You’d never want to run NM inside of conduit or raceway for any distance anyway, it’s WAY too much work trying to pull NM cable inside of either.
Bill
I find surface mount wiring hideously ugly in most rooms of a home. This photo is from the manufacture likely showing the product at its best.
I also found buying the parts it to be very expensive in per foot costs.
I did install over 40 feet in my workshop. It is the best option when you have no wall cavity to hide in and you expect to be adding new circuits at some point.
Walta
I have only one short run of surface mount in my house. Luckily it is 14' in the air and unless I'm looking up it is not noticeable.
Even them I'm still bothers me every time I look up, I can't see ever putting up with a full house wired with surface mount.