Basement insulation

We just bought our first home. The basement is mostly finished, except for a side room that contains the furnace, washer, and dryer, and some storage space. We’d like to finish that room and put a small office at the end.
My general plan is to install XPS foam against the concrete, then frame a stud wall against the foam, and finally install drywall. The room is already pretty small, so I’m trying to minimize the width of the wall if at all possible. I could get R13 batts, which would meet code, but from what I have read I still need some sort of vapor barrier between the studs and the concrete.
First question: How thin could the foam be in order to provide the proper vapor barrier? Would 1/2″ be too thin?
Second question: The previous owner painted the concrete with some sort of waterproofing paint. Is that going to be problematic with my above plans? Wondering if I should try and remove it, or if it is fine as is.
Thanks!
GBA Detail Library
A collection of one thousand construction details organized by climate and house part
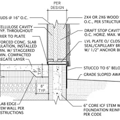
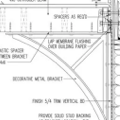
Replies
You don't need a vapor barrier; you need an air barrier. In particular, don't build a basement wall with a dedicated vapor barrier in it. If minimizing the width of the assembly is important to you, you may be better off not building a stud wall. 3" of scrupulously-taped Thermax polyiso insulation will give you R-18 or so and require no drywall to cover it. To get close to that with thin XPS and a batt-filled stud wall, you would need 1" of scrupulously-taped XPS (R-5) and a 3.5" stud wall filled with mineral wool (R-12.75 taking into account a minimal 15% framing fraction). Then of course you have to drywall it. This stud wall will be more materials and labor-intensive than the polyiso-only wall, which you won't have to drywall. Of course if you want to drywall it anyway, there's no reason why you couldn't. In this case, it might be more cost-effective to use 4" of XPS instead of hunting around for Thermax, depending on your local prices.
Cory,
It's a good idea to install a layer of rigid foam on the interior side of your basement wall. That fact that most types of rigid foam are effective vapor retarders or vapor barriers is good in this application, because you don't want any moisture to diffuse from the damp concrete to your interior.
But the main reason that it's a good idea to install rigid foam on the interior of your basement wall is because you need insulation. Not only is this a good idea -- it is a code requirement in most U.S. locations.
However, 1/2 inch of rigid foam only provides between R-2 and R-2.5. That is insufficient to meet minimum code requirements. In Climate Zone 3, you need at least R-5 insulation. In Climate Zone 4, you need at least R-10. And in zones 5 through 8, you need at least R-15 insulation.
For more information on this topic, see How to Insulate a Basement Wall.
Thanks for the responses!
@Nathaniel no stud wall would certainly be thinner, but would also make it more difficult to install outlets, hang shelves, etc. Assuming I go with the stud wall, it sounds like 1" rigid foam would be a sufficient barrier?
@Martin the code requirements in my area are R10 (foam) or R13 (batts). I figured I'd install R13 batts in the stud walls to meet code, so the rigid foam is only being used as a vapor barrier.
Cory,
The rigid foam in the wall you are describing is not just a vapor barrier. It is insulation that separates the humid indoor air from the cold concrete. The rigid foam is there to reduce or eliminate the chance of condensation. If I were you, I would install at least 2 inches of rigid foam. If you install less, the wall may be OK -- or maybe not. It depends on the indoor relative humidity.
The actual climate makes a difference on how much of the total R needs to be foam exterior to the fiber on a studwall, to avoid wintertime condensation issues at the foam/fiber boundary on the above-grade portion of the wall.
A very rough guide would be to use the prescriptive values for above-grade walls found in the IRC:
http://publicecodes.cyberregs.com/icod/irc/2012/icod_irc_2012_7_sec002_par025.htm
The "whole wall" thermal performance of an studwall 16" o.c. with R13 cavity fill is about R10 after calculating the thermal bridging of the studs, which is why continuous R10 foam is considered a suitable alternative According to the IRC 2012 R13 or R10 c.i. is the code min for US climate zone 4 basements:
http://publicecodes.cyberregs.com/icod/irc/2012/icod_irc_2012_11_sec002.htm
That means half-inch XPS (the prescriptive for zone 4 ) WOULD be enough, but just barely enough.
A better solution with even less thickness would be to use 1" EPS (R4) or polyiso (R6) and a 2x3 studwall insulated with compressed R13 batts (R10 @ 2.5"), which has a "whole wall" performance of R11 (if 1" EPS) or R13 (if 1" polyiso.) If you used unfaced R8 batts or split unfaced R19s into 2.75" thick batts for the 2x3 insulation you'd get R10 whole-wall performance with 1" EPS, meeting the code minimum, or R12 for the polyiso.
With the thicker foam/thinner batt approach you end up with a much larger fraction of the center-cavity R being exterior foam, which gives you a lot of dew point margin, which lowers the mold risk considerably.
Since the studwall is not structural, there is no need to double-up the top plate, which would only introduce more thermal bridging, and lower thermal performance.
With any studwall resting on an uninsulated slab, it's good to put at least an inch of EPS between the bottom plate and slab as a thermal & capillary break.
Code minimums are one thing, but it can be financially rational to install more. See Table 2 p10 for a good starting place on the financial rationality discussion:
http://www.buildingscience.com/documents/bareports/ba-1005-building-america-high-r-value-high-performance-residential-buildings-all-climate-zones
Those are all "whole assembly" R-values, not center-cavity. Note that they are suggesting R15 for climate zone 4 (where R13 / R10 c.i. is code min). To hit that with a foam + studwall approach would take 1" EPS and a 2x4/ R15, or 1" polyiso + 2x4/ R13. Either would have sufficient dew point margin. It's probably cheaper and better to go with the EPS and R15 batts. While you can get R15s in both fiberglass and rock wool, the latter wicks less moisture, should any liquid water get into the cavity (and it's more fireproof.)
If your heating fuel is more expensive than the national average (say $3/gallon heating oil or $2.50 propane instead of buck-a-therm natural gas) there may be a long term rationale for something a bit more than an R15 whole-wall performance for a basement, but not a lot more.