Basement wall insulation below grade

We have a split level house with the basement 3.5 below grade, so have a stud wall 3.5 tall, a ledge, then the above grade wall in the basement. We had to remove all sheetrock and insulation due to some mold which is now remediated. The insulation that was in there was the fiberglass batt. I am wondeing how to best insulate the 3.5 ft below grade wall now. The studs are right up against the block wall.
Can we put foam board XPS in between each stud? Would we fill the full 3.5in with foam board or would just 2 in be ok? Would we want to seal around the edge of the foam/stud? thanks for any suggestions.
GBA Detail Library
A collection of one thousand construction details organized by climate and house part
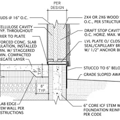
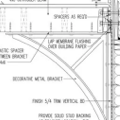
Replies
Jackdaniel,
This article covers best practices on insulating basements: https://www.greenbuildingadvisor.com/article/how-to-insulate-a-basement-wall
Thanks for the article, that is helpful. Do you have any suggestions as far as with a 3.5 inch cavity between block wall and edge of studs, can I do 3 inch foam board (r-15 in mn) and leave the last half open or would it be best to fill that? Also for cavities with electrical wires....split the foam board put half on to half on bottom and fill with spray foam? Thanks again
Jack,
As you probably realize, the old insulation method used on your below-grade wall was flawed, which was why you got mold.
Ideally, the stud wall wouldn't be touching the concrete blocks. Instead, you'd have a 1-inch or 1.5-inch air space between the studs and the concrete blocks.
Whether or not you can get away with leaving the stud wall in contact with the concrete blocks depends in part on how everything looks after you've removed the moldy fiberglass batts. Are portions of the studs black with mold? Is there any sign of rot? If the answer to one of these questions is yes, I would advise you to temporarily remove the stud wall and rebuild it with a gap.
If the studs are dry, sound, and mold-free, you can probably cut corners, and simply (a) install closed-cell spray foam between the studs, or (b) install rectangles of rigid foam in each stud bay, sealed at the perimeter with caulk or canned spray foam. This last approach is called the cut-and-cobble method.
The fiberglass batts were actually pretty fine, the mold we found was on the bottom of the sheet rock behind the base board - the sheetrock was resting on the cement floor and wicked upo any moiture. Once we opened up the walls, we found mold on a few studs that had crept up to the ledge. No rot and mostly dry was eveything. The areas that the mold had crept up, there was a vapor barrier on the back of the sheet rock trapping in the moisture. That vapor barrier did not continue around the whole perimter - it was only in a couple area.
So, I was leaning toward the cut and cobble - question is, if I get the 3in xps and seal the perimeter of each stud bay, is ther any problem leaving that last 1/2 in open, or would I need to by some 1/2 inch xps and fill the entire stud bay. Also how to fit the rectangles around the electrical wires, any special technique or basically just cut each rectangle approx where wire goes through and put half on top of stud bay, other half below and seal gap with foam?
When it's gutted you'll may be able to slip polyethylene sheeting between the stud edges and foundation, which would be at least a partial capillary break, even if you can't get to every last inch of it.
Sometimes it's possible to turn the studs sideways on the plate, leaving 2" of space between the wood & concrete. (Any plumbing or wiring in those studwalls?) Alternatively one can drill a starting hole and use a reciprocating saw and cut the studs to 2"-2.5" of depth, sufficient to flex-slip a couple layers of half-inch foil faced polyiso in there (seams taped), followed by compressed R13. (It might not be possible to flex a single layer of 1" into the space.) Of cours it might be easier to demolish & rebuild the studwall.
If going with a foam + fiber insulation approach the climate zone matters. Where are you?
thanks for your reply - Im on MN- there is electrical wire running through parts - I am wondering the best way to fit xps around those. I plan to sheet rock, then put panelling up on the sheet rock. I was thinking of not mudding the sheetrock joints to allow the wall to breathe some - thoughts on that? I of course will also leave sheet rock half inch off the floor too!
Don't bother putting rigid foam board between the studs- it's impossible to get a perfect air seal, and could even increase the amount of moisture at the stud edges.
If the studwall isn't going to be modified slip strips of polyethylene sheeting between the studs and foundation where possible, then use closed cell spray polyurethane insulation on the concrete, sealing the studs (& poly sheeting strips). In US climate zone 6 (southern MN) a mere inch of closed cell foam is sufficient dew point control on 2.5" of fiber insulation (~R10-R11 for compressed unfaced fiberglass or rock wool sound abatement batts). In zone 7 (northern MN) it takes about 1.5" (R9-ish) for dew point control on 2" of compressed fiber batt (R8-R9).
For more money you can install 3.25" of closed cell foam, which is safe from a moisture point of view, but not necessarily "worth it". With half the foam and much cheaper fiber insulation it's not moving the needle much on thermal performance, and is still moisture-safe. At 1.5" closed cell foam blown with HFCs would run about $1.50 per square foot, foam blown with much more environmentally friendly HFOs would run about $2 per square foot(and deliver nominally higher R). At 3.25" it's twice that. Most HFC blown foam can't be installed in lifts of more than 2" (at $2 per square foot), and that's the most I'd personally recommend here- fill the rest with cheaper stuff, but DO fill it.
Air leakage from the interior is going to raise the moisture content of the studs in winter, depositing moisture from more humid indoor air into the cooler part of the studs. With enough closed cell foam it's not particularly risky, but it's still not great. It's almost never a good idea to intentionally build the assembly to be air-leaky.