Below grade XPS placement, protection, and detailing

I’m pouring a traditional 8″ concrete foundation for a client this week. They planned to have us place 2″ of XPS foam on the outside of the walls for insulation. Once they can afford to finish the basement, they would place another 2″ of foam on the inside of the walls between treated 2x2s and sheetrock over it for the finished assembly.
I’ve attached a rough sketch of the various components.
I’m considering using Colphene ICF waterproof membrane over top of the XPS vs. a direct-to-concrete water based sealer. I’d like feedback from anyone who has used both methods of waterproofing. Wondering if the extra $1k in material cost is worth it or am I just burying $1k in the ground given the vast amount of drainage present.
Since the exterior XPS just terminates on top of the footing in this design and does not encapsulate the footing, how much of a benefit does it actually pass on in terms of insulation?
Would it be better to just install 4″ of XPS (or comparable) on the interior and forgo the external XPS layer?
If so, I would also plan to skip the Colphene and just seal my foundation with a water based coating. Any flag going that route?
Thanks in advance for the feedback.
Much appreciated.
-Nethaniel in Idaho
GBA Detail Library
A collection of one thousand construction details organized by climate and house part
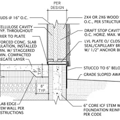
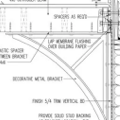
Replies
You can't put 2" XPS between 2x2's since the 2x2s are only 1.5" deep. And it would be a waste of foam anyway, since it's performance is severely undercut by the thermal bridging of the framing.
Assuming a 2" depth from concrete to the gypsum is acceptable, you'd be better off with a continuous layer of 1-1/4" of foil faced polyiso (seams taped with 1.5-2" foil tape) held in place with 1x4 furring (=0.75" thick) through-screwed to the foundation with TapCons. That way you'd have an unbridged layer of R7 between the furring and the concrete, keeping the furring warm & dry (no need for pressure treated), and the air-gap between the foil and gypsum adds another ~R1 of thermal performance, from the radiation barrier effect and trapped air films. 1.25" is a standard product thickness from multiple polyiso vendors, but not often seen in box-store type outlets. Even 1" continuous polyiso would do better than 1.5" of XPS thermally bridged by 2x2s, and if there is any moisture wicking up from the footing into the foundation walls the 2x2s would take that on, transferring it all to the wallboard, since it can't dry into the XPS. The amount of moisture you'd wick with TapCons is near-zero.
Polystyrene (EPS or XPS) has a lower kindling temp than polyiso, and it melts into a puddle of burning liquid. It's much safer to use polyiso on the interior, since it's foil facer delays ignition, the foam itself has a higher kindling temp, and it chars in place rather than melting even when fully engulfed in flame.
Don't forget to extend the rigid board to the top of the foundation sill, and over the top of any concrete ledge between the foundation sill and interior concrete plane, and insulate the band joist too.
It's better to put the foundation waterproofing on the concrete, not the XPS. The XPS is fairly moisture-tolerant to the levels found in well drained soil, but the foundation still needs waterproofing.
The XPS stopping at the top of the footing does leave a thermal bridge, but it's between the ground temp and interior temp, not the outdoor extremes. Extending it down the side of the footing doesn't change it much. But the full foam under the slab that turns the corner isolating the slab from the footing is a significant thermal break, and if that's continuous with continuous interior wall foam it's pretty good.
XPS is one of the least-green insulating materials out there due to it's HFC-soup blowing agents, the predominant component of which is HFC134a (automotive AC refrigerant), which has a global warming potential about 1400x CO2. EPS and polyiso are blown with pentane, at 7x CO2. Even from a total cost point of view you might be better off doing the 8" wall with an 2.5" + 2.5" EPS insulated concrete form, which would have comparable thermal performance to 4" of continuous XPS.
But if you do that, either put up the interior gypsum right away, or paint the EPS with intumescent paint so that it's not a hazard between the time it's installed and the time that the basement gets finished.
Great idea with the polyiso and furring strips. I'll definitely recommend that route for the interior.
Based on your advice, I'll forego the expense of the Colphene, just apply a sealant directly to the concrete and apply the XPS last on the exterior.
I'm confused about this line "...over the top of any concrete ledge between the foundation sill and interior concrete plane"
Could you clarify?
Also, given your input, why not just run my external XPS down below frost depth (30" here) vs to the top of footing?
Nethanial,
Q. "I'm confused about this line: '...over the top of any concrete ledge between the foundation sill and interior concrete plane.'"
A. I think that Dana was referring to the fact that your concrete foundation wall is 8 inches thick, and your pressure-treated mudsill will be 5 1/2 inches wide. That usually leaves 2 1/2 inches of exposed concrete at the top of the foundation wall.
Nethanial,
For a discussion of the pluses and minuses of interior vs. exterior basement wall insulation, see this article: How to Insulate a Basement Wall.
Is the blowing agent for the "green" Dow XPS that is advertised on the board as having "zero" ozone depletion formula actually true? Or, are they being deceptive with words since zero ozone depletion doesn't necessarily mean no greenhouse gas emissions?
Michael,
The problem of ozone depletion at the upper layers of the atmosphere is an entirely different problem from the problem of global warming gas emissions.
You guessed correctly: the Dow marketing materials are obfuscatory. Blowing agents that damage the ozone layer have been illegal for years, so all insulation manufacturers comply with those requirements. All XPS sold in North America is manufactured with blowing agents that have a high global warming potential.
For more information on this issue, see Avoiding the Global Warming Impact of Insulation.
If they used a blowing agent that depleted the ozone layer it would be in violation of the Montreal Protocol, and would be considered contraband in signatory countries. So yes, it's true, and so what? Simply delcaring "We are compliant with current regulations." isn't exactly the same as being environmentally friendly.
Ozone depletion is a serious, but completely separate issue than greenhouse gases. When the world agrees to stop using high global warming potential blowing agents for foams the manufacturers will have to re-adjust, and would then be crowing about how nice they're being to the planet for not producing illegal products, I suppose.
Such blowing agents exist- there are a handful of HFO1234_ _ blowing agents that have been tested and are commercially avaiable, but none of the big players in the US have made the move. The HFO1234-variant blowing agents have global warming potentials under 5x CO2. They are modestly flammable (like pentane, the common blowing agent for EPS and polyisocyanurate), but aren't particularly hazardous in this application. These HFOs are also being used for automotive AC refrigerant in the EU, which has banned the use of HFC134a for that application. CO2 is also being used in Europe for both as foam blowing agent, and as a refrigerant gas. It (curiously) has a global warming potential of only 1x CO2. :-)
Martin,
Thanks for the clarification on the insulation placement. Very helpful.
All,
Not interested in the discussion about blowing agents in this post, but I'd certainly appreciate suggestion/feedback/answers to the questions posted.
Cheers,
-N
The blowing agent is a long term performance issue, not just an environmental discussion.
As XPS loses it's blowing agent over 4-5 decades it's performance gradually drops to that of EPS of the same density. The R5/inch 1.5lb density blue-board eventually depletes to about R4.2/inch. So 2" XPS is really ~R8.4 for the long term, but they are allowed to label it R10 based on the average performance over a presumed lifecycle (IIRC, 25 years.) Hot off the presses it's performance is higher than R10 for the first couple of years.
Foams blown with pentane lose the blowing agent within weeks, and are labeled at the fully depleted R value, which is stable over time. There is some inflation of foil-faced polyiso R based on longer term depletion, since the foil facer slows the loss of the blowing agent. In your application 2" polyiso at 1lb density might be labeled R12 (or sometimes even R13), but in 50 years it'll be more like R11.5. The performance boost of the foil facing an air gap will always be there unless the aluminum becomes severely corroded. It's still the right choice for the interior side foundation wall foam.
EPS in thicknesses of a few inches will be fully depleted in the first year after manufacture, maybe even the first month. Thick blocks of EPS manufactured at a few feet of thickness are something of a fire hazard in the first months, since they are still outgassing significant quantities of pentane. Type-II (1.5lbs density) EPS is usually cheaper per R than 1.5 lbs XPS too, and in applications where you don't need the lower vapor retardency or thinner profile (such as under slabs) it's perfectly reasonable to substitute EPS where XPS was specified. But don't use polyiso under slabs, or in contact with soil, since it's mildly hygroscopic, and will take on groundwater over time, taking a hit in performance.
I was able to source a 2.5" graphite coated EPS foam (Insulfoam platinum GPS) to clad the house from footing to truss all within the budget. Now I'm trying to figure out the best way to attach it to the vertical concrete walls. It needs to hold on well enough to apply Colphene ICF waterproofing membrane before we backfill in a couple days. We tried a water-based adhesive, but it took over 1.5 tubes to create a bond. This would be much too expensive on the whole foundation.
I'm thinking of trying large plastic washers with Tap-cons next. This would require more labor than I'd like as well as necessitating a generator on the site.
Any thoughts?
Nethanial,
You may want to consider the use of specialty fasteners like Hilti IDP fasteners or Rodenhouse Plasti-Grip PMF fasteners.
For more information, see How to Insulate a Basement Wall.
Great to hear about increasing availability of graphite EPS. Looks like they license BASF neopor.
I'm not convinced that waterproofing needs to be outside the foam, and if things don't stick to this foam, maybe it would stick better on the concrete.