Best Wall assembly for very likely moisture intrusion

I have a friend that would like to insulate a portion of a large heavy timer framed shop building on their property. The building’s foundation is a series of lock blocks (also know as click blocks I think, and I’m sure it other things as well) on which sits a sort of built up sill plate of laminated 2x material that’s perhaps 8”” tall and 6” deep. The structural posts sit on this with the space between the posts framed out with 2” x 6”. The exterior is board and batten with what appears to be landscape cloth and/or roof underlayment behind it attached to the exterior face of the 2x6s.
The issue is that the foundation blocks stick out past the exterior face of the wall, collecting water which then moves under the wall, occasionally pooling on the interior floor.
My friend would like to insulate this wall as part of turning ~400 ft2 of the -1600 ft2 footprint into a heated wood shop.
anyhow, let’s assume for the sake of argument that stopping the water is not an option at this time (that’s a separate project, no guarantees of success).
The shop is to be heated with a hydronic unit heater served by an existing wood boiler to something like 15C when shop is in use.
I’m thinking 2” of continuous eps on the interior of the wall for the first 2 vertical feet, above which would be rock wool cavity insulation. Wall to be finished with bare plywood, possibly roofing tin over the eps portion. The reasoning is to minimize materials pervious to water, leave a portion of the cavity open to foster air flow, and reduce the thermal bridging of the sill.
my questions:
is it even worth it to insulate the space at all? Boiler heats the house as well and is oversized to the task.
would the typical interior 6 mil poly vapour barrier still be a good idea? If so, down to the floor or stop at the top of the eps?
Is it worth the trouble of attempting to fashion a sort of air barrier in the stud bay against the back of the board and batten siding?
What about a good continuous air barrier with moderate permeability in place of a true vapour barrier?
Just looking for a reasonably well insulated assembly that will not decrease the longevity of the structure.
I think we’re technically in 6B but it’s pretty damp here, I’d say we’re closer to 6C if there was such a thing.
Thanks for taking the time to read through this.
GBA Detail Library
A collection of one thousand construction details organized by climate and house part
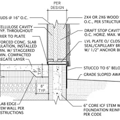
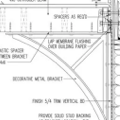
Replies
" let’s assume for the sake of argument that stopping the water is not an option at this time"
I realize this is the opposite of what you want to hear, but doing any of the interior work without addressing the water is a complete waste of time and money. Stopping the water is not hard and a smaller project than your insulation scheme. Get a sheet metal shop to bend you a custom flashing that covers the blocks, pry the bottom of the Board and Batt out with wedges and slide the flashing behind. Trim the bottom of the siding up so that it has at least 1/4" clearance to the new flashing.
Thanks for the input, completely agree.
So, how about instead we assume for the sake of argument that that we plan to do that, along with extending the 2’ eve that’s at the top of the 18’ wall that’s sitting on the blocks, adding a gutter, snow stops, improving the exterior grade and waterproofing the exterior faces of the blocks but are still not confident that the the seams between the blocks and the blocks themselves (coupled with the up hill orientation of the wall) will not still wick moisture up into the sill plate.
Would dealing with the bulk water intrusion allow for a typical wall assembly for the region (siding, air barrier, cavity insulation, and vapour barrier) or would we still want to do something different to foster drying of the sill?
Thanks again.
Here are some pictures of the current conditions.
I expect that if you do everything you describe you will see large difference in how dry the building is. It is hard to give a blanket statement, but I would probably feel OK insulating if you take care of bulk water. The safest path would be doing the eaves, gutters, grading and snow stops, then waiting a year to see how it looks.
I do like the phased, wait and see approach. I’ll need to chat with my friend about what makes the most sense with her timeline.
Looking at those pictures I’m realizing that detailing that lower flashing around the posts that penetrate the wall plane is going to be a pain. So now I’m thinking that adding exterior continuous insulation up the entire exterior wall is another possible appraisal, probably the most expensive materials wise but with labour costs around here might be a wash in terms of overall costs in the long run. I’m also thinking that perhaps a big shed roof extending out 10’ or so from under the current eve would be another option for bulk water control and be a useful place to store materials etc.
Lots of options to price out now I guess…
Thanks again for the advice.