Best wall design for Climate Zone 6

I am trying to develop the best all around wall design for a residential addition in climate zone 6, Wisconsin.
I have reviewed many articles on Green Building Advisor and Building Science Corporation’s websites. Attached is a drawing I created hoping to incorporate the best ideas and design practices.
My design intent is the above grade portion of the design is vapor permeable to the outside of the structure. The below grade portion of the design will breathe to the inside of the structure.
Any and all recommendations and suggestions would be appreciated.
Thank you,
GBA Detail Library
A collection of one thousand construction details organized by climate and house part
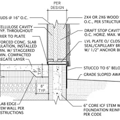
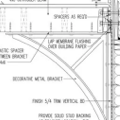
Replies
Looks good, I would skip the SPF though. There are much cheaper ways to air seal the structure and thermal bridging of the studs short circuits the high R value of the SPF. Going with 2x6 mineral wool batts would give you a higher assembly R value and cost way less.
I would also do a load calc on the place with the as proposed assembly to figure out how much of the floor you need to heat. In high performance homes, there is no point in fully heating the slab, you can probably get away with about 1/2 to 1/3 of the floor area. The best is to heat high traffic areas (kichen, bath, hallways, center of room) and underneath windows/doors.
This would be way cheaper if you are going with warmboard and also much more comfortable as the floor will be warm instead of "not cold" with full coverage.
Tile might also not be the most foot friendly finished surface in Zone6. Tile needs to be heated to much higher temperature before it feels comfortable. Just because you have floor heat, it doesn't mean the tile will not be cold as the floor will not need to run hot enough 90% of the time.
Akos,
Thank you for the additional insight. I had not considered the reduction in heating load and the effect it would have on the cycling of the heating system.
My hope in using the ccSPF was to help eliminate condensation on the sheathing, due to its low vapor permeability and high R value. I think if I only go with rockwool inside the stud cavity I will have a condensation problem in the coldest months of the year. Assuming I calculated it correctly, R20 of rockwool inside and R15 of Neopor on the outside estimates the inside sheathing temperature at around 40 degrees F. I am using an average outside temperature of 17 degrees F and an indoor temperature of 68 degrees F.
As other have said, you have more than enough exterior insulation for condensation control, see table 2 here:
https://www.buildingscience.com/documents/building-science-insights/bsi-100-hybrid-assemblies
Even if you are on the colder end of zone6, as long as you do a decent job of an air tight drywall install the insulation ratio can be pushed a little bit.
Akos,
I added an updated drawing below. If you have time, please let me know your thoughts.
Thank you,
Looks good, solid wall.
Make sure your siding fastening schedule matches your stud spacing. Some siding won't work on 24"OC.
I like your high R-value wall and foundation. Some of your choices are expensive compared to alternatives.
Where’s the continuous air barrier(s)? Closed cell foam would work initially but over time, studs and foam may separate some. Could tape plywood sheathing edges or a layer of Neopor, or I guess the wrinkled WRB edges. Consider making a choice that makes it easier when installing the air barrier at windows/doors, depending upon how your windows are installed. Continue the air barrier from the bottom plate or sheathing to the CIP wall, using gaskets, acoustic sealant, or tapes, so its continuous. (Draw a line indicating the air barrier continuous from CIP wall through the above ground wall, around windows, and continue to the ceiling air barrier.) Personally, I’d consider more than a single air barrier if your goal is attain very low infiltration rates. Perform blower door tests during construction to verify you are getting the airtightness levels you seek, and seal leaks found.
Closed cell foam is expensive, has high global warming potential, and occasionally isn’t installed well in the field, resulting in some complaints about smells or indoor air quality. More typically chosen for some tough renovation situations, but in new construction, often Roxul ComfortBatt or higher density fiberglass is chosen, and are less expensive.
Similarly, EPS is chosen instead of XPS as the latter has high global warming potential, and its slightly higher R-value decreases over time to similar to EPS. Neopor could be used since it’s graphite-infused EPS, with same R-value as XPS. You might want borax-infused EPS to minimize termite damage, and consider a copper or stainless steel mesh or flashing to stop insect infiltration at the top of the insulated foundation.
Robert,
Thank you for your thoughts on the wall design. I have found a product called ThermalBuck which is made from EPS. I think it will simplify and improve the installation of the windows and doors with the exterior insulation. Have you ever used it?
My plan on the air barrier is to tape the wrinkle WRB and to tape the outer layer of the Neopor. I will also include copper flashing tape at the top of the foundation insulation. Do you think 4" wide would be sufficient?
Please see my reasonings for using the ccSPF in my reply to Akos above.
Thank you
It appears you don't have to worry about condensation on the inside of your sheathing. On GBA it says 35% is the prescriptive ratio of exterior continuous insulation to interior cavity insulation for a safe assembly in zone 6. Mineral wool R-23 batts vs. R-15 for 3" Neopor is beyond 35%. Or you can calculate exactly with about R-0.68 interior air film + R-0.45 drywall + R23 mineral wool inside the sheathing (total R-24 then derated for studs 24" or 16" o.c.) vs. R-0.6 sheathing + R-10 Neopor+ R-1 drainage plane airspace + siding (total R-12-ish).
I haven't used ThermalBuck but like it, although expensive. Looks reasonable to install and would be very effective in reducing thermal bridging around windows. Typical window bucks do introduce thermal bridging.
The idea of a termite barrier is to eliminate any path that termites could use to tunnel from the earth to your wood structure. Its needed most in the south to avoid damage from aggressive Formosan termites, which would not be found in Wisconsin. You might want to find out the risk of termite damage in your area. Unfortunately a termite barrier introduces a metal thermal bridge at the top of the foundation wall, below your wood frame wall, and adds expense and labor. In your diagram, it would extend from the foundation wall, around the bottom of the sheathing (why is the sheathing dropped lower along the foundation wall?), then between the Neopor and the XPS/dimple mat/stainless steel flashing. Or perhaps the stainless steel flashing could be bent at the top to extend back under the Neopor to be sealed to the concrete wall (if you raised the sheathing upwards, out of the way). Also need to cover top of the insulation between layers of concrete in a CIP wall. I've seen a heavy duty vapor barrier sub-slab product (forget the name) that claims to be termite proof. If effective, seems an easier alternative to metal alternatives. Alternatively, could bury termite bait stations around your building to detect and eliminate, and not incorporate termite barriers in the building itself, though that doesn't guarantee protection.
Robert,
I have updated the drawing to reflect your suggestions. I has dropped the sheathing to cover the foundation to help on air sealing. I read it in an article somewhere.
Thank you,
I see you are attempting to construct a 12" +- wall, at around R-40. This can
also be done with a double wall the following way - 2x4 inner and outer walls
@ 16" on ctr with 4" of polyiso attached to the inside of the exterior 2x4 stud
wall. Both inner and outer walls insulated with mineral wool batts.
This has the following advantages:
1. The foam (polyiso) is in the center of the wall and is therefor protected
from fire, insects and physical damage.
2. The polyiso has foil on both faces and therefor acts as both moisture and
air barrier in both directions and I might add, a better one than any high-tech
membrane you can buy.
3. The mineral wool batts are pretty fire resistant.
4. The 3" of foam you are proposing on the exterior requires long strong
fasteners to be able to .support the siding . These leak heat ( they act as small
round heat sinks) and are expensive and awkward to install.
5. The 3" closed cell you are proposing in the center of the wall is expensive
and environmentally suspect - in addition it has a history of sometimes
causing odor and chemical sensitivity problems.
6. Double walls are generally relatively easy to construct - yours not so much!
This is just the opinion of an old gummer no longer active in the field - I hope
it didn't offend!
Thank you for you assessment of the wall. I appreciate your time and your suggestions did not offend me in the least. I will have to research the double stud wall design. I am not familiar with it. In my case, the structural engineer has the wall designed and I am trying to develop the best building envelope.
As User- notes above, a double stud wall (filled with cellulose) would be cheaper to build and much greener.
There's no reason to use foam above grade.
With such a thick concrete wall?
I have nothing but respect for the expertise of structural engineers. But you don't need one to design a wall unless your house has unusual seismic or other structural concerns.