Best way to insulate floor of addition on piers

I’m in Washington, DC (zone 4A). I am putting an addition on an existing house. DC has an aggressive tree protection law, it is illegal to harm a mature tree in construction. There is a poplar with a 36″ diameter near where the addition will go. An arborist has told us we can build the addition but it has to be on piers, possibly helical piles. He thinks the soil will stay moist, but if not we will have to install an irrigation system.
So my question is what is the best strategy for constructing the floor to insulate and protect against moisture. Is there any way to thermal break to connection to the piers? The practicality of construction is also an issue, the floor surface of the addition will be as little as 18″ above existing grade (which we can’t change due to the tree) so there’s the question of you get in there to build it. We are looking at making the rest of the house significantly better than code minimum in terms of energy efficiency.
Thanks.
GBA Detail Library
A collection of one thousand construction details organized by climate and house part
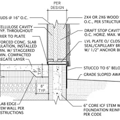
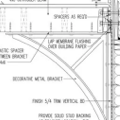
Replies
Hi DC Contrarian.
There is a lot you can do to air seal and insulate these floors, but as you noted, the pier itself is the tricky spot. Other than installing continuous insulation above the subfloor, I'm not sure what you can do to break the thermal bridge at the pier connection. Maybe others will have some ideas for you. In the meantime, check out these articles, if you haven't already.
How to Insulate a Cold Floor
Insulating a Wood-Framed Floor Assembly
Deleted
Also, I've heard from a number of people now about irrigation systems being the cause of wet sheathing, rot, and mold. Perhaps you will install a drip system, but if you install sprinklers, perhaps an extra layer of water protection around the lower part of your addition wall would be worthwhile.
DC,
With an addition that close to grade I'd suggest a couple of things.
- Consider dropping the beams. That does mean an interruption of the continuous insulation, not only at the piers, but for long strips, however it is offset by not having a large areas without batt insulation in the floor system - and allows what I'm suggesting next.
- Build the floor system in manageable modules (say 10ft x 10ft) upside down. That way you can add continuous insulation (except at the beam locations, which get blocking instead), sheath and seal the underside, rather than attempting this work crawling underneath. The modules get flipped, the joist cavities filled with batt insulation, and the subfloor installed.
Thanks Malcolm. Interesting idea with dropping the beams. I'm not sure what you mean about blocking over the piers. What I'm thinking is a piece of horizontal foam over the beam, bridging the foam on one side of the pier to the other. So beam is on the cold side of the floor, the only thermal bridging would be the joists where they cross the beam. If I use I-joists that would be pretty minimal. The fluffy insulation (I'm leaning toward blown-in cellulose but I'm persuadable on that) would also be less thick over the beam, by the thickness of the foam. If I decide that's a problem I could make that piece of foam thicker to compensate.
I think I can get away with a single beam which makes the detailing more manageable. The other end is going to be a ledger against an unheated crawl space.
One question is how to sequence the building. It's going to be platform construction so the floor gets built first, then wall, roof and doors and windows last. So I have to either keep the floor dry until the rest of the building is built, use insulation that can stand to get wet, or do the blow-in after the building is dried-in. If I do the blow-in last I have to leave an opening in the subfloor over each joist bay, which is a pain with tongue and groove subfloor and the walls resting on the subfloor.
One thing I'm thinking about is using Zip-R for the bottom of the floor assembly for better air-tightness and water resistance. I'm not sure I would be able to tape it though.
DC,
I was suggesting that you put a block on top of the beams the same depth as the insulation so that you could run it over top of the beams and still have a bearing point for the joists. We may be describing the same thing?
I've done the flip-floor thing a few times, but never on project larger than one panel. I'm in the midst of one now which is 10ft x 12ft, and as we are in the rainy season here in the PNW I've covered the subfloor with a pond-liner from Home Depot, which was only $120. With foam on the bottom, and batts in the cavity, it's pretty important that the floor assembly be dry when it is initially installed, as it has a pretty limited capacity afterwards.
Malcolm,
I’m also unclear about your description of blocking over the beam. If the joists cantilever past the beam, blocking is necessary vertically between the joists, right?
But it sounds like you are describing a detail to solve the problem of discontinuity of the air barrier at the beam. Do you mean that the blocking is laid flat beneath the joists (in plane with the rigid foam and sheathing) and taped to continue the air barrier?
I like that idea better than the thought of taping the sheathing to the beam. Of the numerous articles and Q&A posts addressing/discussing floors built over pier and beam foundations, this is the first time I’ve heard of this idea. Please elaborate.
Thank you,
Aaron
Aaron,
I'm trying to think of how best to maintain as much continuous underside insulation as possible, have a continuous sheathed underside, and at the same time be able to flip the floor.
Something like this?
Malcolm,
What factors would be used to size the blocking? And how would the joists be connected to the beam? Hurricane ties would have to pass through the foam and sheathing; do you see that as problematic? Or would you use a different attachment method?
I read a Fine Homebuilding article not too long ago that featured a crew building the floor for an addition over a pier and beam foundation. They built the floor frame, used material lifts to raise the floor and attach sheathing beneath the joists, and then set it back down in place. Unfortunately, the article did not delve into details of how they handled the discontinuity of the air barrier at the beam, nor did it describe the attachment method for joists to beam.
https://www.finehomebuilding.com/2019/07/09/air-sealed-and-on-piers
Thanks again,
Aaron
Aaron,
I saw that article too. Scared the hell out of me. No way would I want to work on a floor system temporarily suspended over my head.
The minimum width of the block would be the code mandated minimum bearing for the joists - here the would be 2" - but if the depth of the insulation were m0re that that I'd imagine you would want to increase the width for stability.
If the floor were being built upside-down, the block could get fastened to the bottom of the joists with structural screws or nails depending on the depth, and once the floor was flipped the blocking could be nailed or screwed to the beam between the floor joists. Remember that if there was no block, the code would only require three toe-nails as a connection between the the joists and beam, and no provisions for uplift, so no hurricane clips.
I look at the assembly as having the subfloor as it's primary air-barrier, with the foam and sheathing underneath as secondary ones, meaning a bit of discontinuity there isn't as important.
Malcolm,
One more question if you happen to see this. For the 10' by 12' building you mentioned, how did you determine a size and span for the beams? I'm familiar with the beam span table in the IRC section for decks. Other than consulting an engineer, how would one go about sizing beams for a small shed building of this size? Thanks again.
Aaron,
Just saw this. Our code has span tables for beams and joists used for all framing, not just decks, based on loads.
That said, for a 10' x12' outbuilding, beams of either 3. 2"x10" or 4. 2" x8" will work fine.
Maybe SIPs for the floor?
it is illegal to harm a mature tree in construction.........So how do you get wood to do the construction?
You import it from some place that doesn't have a tree preservation law!