Building Science Deep Retrofit Detail

Feel free to challenge me on this subject if you wish. I was reading the debate and discussion attached to one of Martin Holladays blog entries about ‘Deep Retrofit’ details. In the discussion following Martin Holladays blog entry, John Brooks asked a very simple question – where do you define the drainage plane on the Building Science Corporations detail? Well, I agree with BSC’s initial response. The piece referred to as ‘metal flashing attached to furring strips’ does not need to do anymore than is shown in the BSC’s detail. It’s purpose is to shed out any condensation that may form on the back of the siding material. I remember when in Ireland we began to place polystyrene (and later polyiso) insulation batts into our masonry cavity wall construction. All of the young architects is school were asked to swallow a complete mis-interpretation of the cavity wall construction. We were all asked to draw our details showing the DPC (damp proof course) over window lintels, going from the inner wall leaf to the outer wall leaf. This meant that with insulation in the 4-inch cavity, the architectural draftsman or woman was asked to show the DPC cutting through the cavity insulation. We were all told at architectural school this was to transfer water from the inner leaf of the wall construction to the outer leaf. Beep! Problems.
As one architect who worked in an actual construction company later informed me, if you get water on the inner leaf of your construction, you might as well give up. Because you wall is finished anyway – you have no way back. He informed me, this fairy tale about transfer of moisture from the inner leaf to the outer leaf was nonsense. His architectural details over windows always showed a proprietary cavity tray installed on the outer leaf of the cavity wall. Its purpose he told me was to shed out any water which may condense on the inner face of the outer leaf of the construction. His analogy always was to imagine a water fall, on the inner face of the outer leaf. He informed me, this exaggeration was only that, an exaggeration. He told me, for 90% of days in the year, and depending on the orientation of the wall, it might be bone dry and therefore the cavity tray is redundant. But why go around the building site, and have different rules for different walls. It would only confuse the contractor, and would be impossible to manage.
So you can take it, that in 95% of situations the moisture that forms on the inner surface of the outer layer of construction can be taken care of by ventilation and evaporation. It is just that unlucky 5% of cases, where a river of water can actually occur – on certain days of the year – when the air is saturated with moisture, and over the cold nights the air sheds all of its water content on the inner surface of the outer layer. Nowhere in the above, do we need to consider this notion of water on the inner layer needing to be transfered via weepholes or anything, to the outside. As my friend from the building company told me, if you have water on your inner leaf, inside the insulation, the wall is already destroyed and there is no come back from that. He also told me, it is useful to have wings, or dams to close the ends of your cavity trays. Because, you can stop the water travelling down the back side of the outer layer, doesn’t mean that water if sufficient in quantity (that 5.0% case of the ‘river’), cannot find its way horizontally into someplace else. So the stop-ends, or dams at the end of the cavity tray are necessary to prevent that horizontal escape of the water.
But as architects and designers we all have to get away from this notion of transference of water from an inner to an outer leaf. In real life, that simply isn’t the way to go. I think the Building Science Corporation have figured that one out already – fair play to them. But the problem is, the poor training about water management has been taught to successive generations of architects. So that false science is lodged in the system, and you meet it time and time again.
GBA Detail Library
A collection of one thousand construction details organized by climate and house part
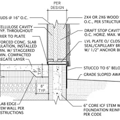
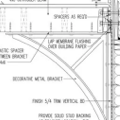
Replies
Sub-note: Sets of drawings What Martin's blog entry highlights more than anything I believe, is the difference in a discussion provoked by a graphic representation, versus a discussion provoked by an article. They are quite different, and as someone who was trained and worked as a job architect on many projects here in Ireland (recently getting into the field of deep retrofitting myself - thinking about the tax credits, or grants as we use here), I understand the unique nature of a debate about a graphical representation of construction.
The whole reason that we as architects issue a set of detail drawings to a site contractor, is that we hope it will kick-start his brain working in the right way. In other words, the contractor will begin to parse out all of the different activities that must happen in sequence, in order to end up with the right detail. The sequence of operation is non-trivial. It is a bit like snakes and ladders. You choose the wrong sequence and you end up sliding back down the snake. You choose the right sequence and you are on the ladder to achieving a good project.
The difference between a good contractor and a poor one, is the difference between knowing how to find the ladders rather than the snakes. A good contractor is worth his slice of the deal, if he can organise that. But as architects and designers who issue detail drawings to the site, it should not preclude us from thinking about the sequence of operations as we draft our details. It is difficult sometimes as a young architect to be allowed to visit real building sites, to observe the kind of teamwork that goes on, and how the main contractor is able to synchronise operations. Inevitably, the young architect is used as a drafting machine by his boss - and that results in a young designer doing an awful lot of detail drawing, without due consideration to the reality of what is happening.
Sub-note: I know that Phil Kaplan and Chris Briley are delving into the subject of the 'Deep Retrofit' of late in their 'Design Matters' podcast series. With no shortage of reliance on A-Team music either, I observed.
As I look at the Building Science Corporation detail of the head of the window - and you understand my brain operates in such a way as to understanding 4-inch masonry outer leaf, 4-inch cavity with insulation and 9-inch inner masonry leaf - there is one other remark I wish to make. There was a huge fight in Ireland about insulation in masonry cavity walls. Because the theoretic U-factor of 0.27 w/m2k (R-20) or earlier compliant U-factors of 0.35 w/m2k (R-16) for the entire masonry cavity wall construction hinged around a physical impracticality. That the insulation in the 4-inch cavity, usually a 2-1/2 inch batt of polyiso, was pressed tight up against the inner 9-inch masonry leaf. In real life that is impossible to achieve. Because the mortar between the blocks of the inner leaf conspire against you. As you build up the wall, the mortar between the blocks squishes out, and that pushes the insulation batt away from the face of the inner masonry leaf. So that theoretical R-20 is maybe an R-10. We have a lot of papers produced by people such as Mark Siddall, Joseph Lstiburek and John Staube which talk about convection currents in wall construction.
But here is the point I wish to make. You take a look at the Building Science corporation detail in Mark Holladay's blog entry about 'Deep Retrofits'. Those furring strips which are installed outside the polyiso foam, are bolted back into the timber frame construction. Martin provided a link in one response to Thorsten Chlupp's article: "Installing Exterior Insulation in Cold Climates." Of course that is the thing with timber frame construction. You guys in north America can screw your insulation tight to the inner leaf of your construction. In Ireland and the United Kingdom, where we use masonry cavity wall construction, both the inner leaf and outer leaf are constructed at the same time, by the same brick or block-layer. We don't have any bolts to compress our insulation tight against the inner structure layer. Therefore our R-values are only theoretical and in reality we do not achieve them. But in timber frame construction, your R-values are much closer to the theoretical R-values. You guys can come along, much layer and install your cedar shingles, or your horizontal sidings, and only leave a 'ventilated cavity' which is an inch or less. In fact, in many cases in north American construction, you most likely have a different tradesperson to install the timber structural frame, the insulation layers and the external siding. In Ireland and the UK, there is the one brick or block layer trying to do all try at the one time, and maintain some degree of 'quality control'.
One mention I should have made - I was looking at some excellently rendered 2D details of eaves by John Brooks, in one of Martin's blog entries. I guess, the point I would like to make is, details need to be looked at in 3-dimensions, preferably using freehand paper and pencil. One architect who I had a great deal of confidence in, because his 3-D detail perception was razor sharp - used to always refer to drawings on cavitytray dot co dot uk. There are a range of cavity tray products, from A to Z, with brochures on the website, and for their display of the 3-dimension-ality of the weathering problem, they are hard to beat.
Even though the cavity tray details refer to masonry wall (with 4-inch cavity) construction - the same techniques of 3-dimensional representation, could be employed to show a builder the sequence of assembly needed to weather any timber-made geometry.
Brian's description of interior flashing issues with cavity masonry construction may give North American readers a hint as to why construction costs are far higher on the other side of the pond. Just a quick note for North American readers: in the UK and apparently in Ireland also any wood frame structure is referred to as timber frame. Parallel note to Brian: in the US timber frame refers only to heavy timber construction, generally 6 x 6 framing members and above - or 150 mm x 150 mm if you prefer. Platform frame construction using 2x material (the norm) is often called stick-built if there is a desire to differentiate from the much less common heavy timber frame. I'd add, Brian, that even the best details from North American practice are extremely hard to transpose to Irish/British conditions.
James says,
Thanks for spotting that vocabulary difference. That it why it is so important to have people who understand the language on both sides of the Atlantic. Otherwise, we could get into major confusions. In terms of massive timber frame sections - It is well worth GBA readers having a google for Paul Leech's Navan Credit Union building case study article in Construct Ireland magazine. Paul Leech's goal was to build a passively cooled multi-storey office building in Ireland, from timber slabs and thick timber sections. The use of large as opposed to skinny timber sections, having to do with the fire engineering of the office building. Paul Leech had to go outside of Ireland for many of the engineering knowlege and skills to make such a project possible in Ireland - and many of the materials came from outside of Ireland also. He admits that freely, the travel miles on raw materials was too high. But nonetheless, it is a very interesting project.
James, thanks for pointing out the 'stick frame' term to me also - I've heard it now, on quite a few of the podcasts. That is the amazing thing about the audio medium, as opposed to reading text. With the podcast, it is likely myself learning to speech french - north American, construction talk, is a whole different language. Not all to do with the Imperial system either.
Joseph Lstiburek though talks a lot at building science corporation about the 'glass chin' of modern construction techniques. I think that Mr. Lstiburek has cut his teeth on many a speculatively built multi-storey hotel project. Where the construction is reduced to the ultra-thin metal sections and sheetrock with some fibreglass in the middle. We still do an awful lot of heavy material construction in Ireland and the UK. A lot of it very, very draughty also. Architect Joseph Little recently commented on the 'standard practice' in Ireland - where the national electricity utility installs the meter boxes straight into the outer masonry leaf. What hope of doing airtight-ness have you? And that box can never, ever move. It's permanent, almost. GBA website's 'Green Basics' section has a nice piece on 'Integrated Design' I hope to get around to reading sometime. BOH.
James, & All,
The Lead Development Association's 3-part series of flashing details also - if you can ever get your hands on it. I sincerely doubt anything in north America could best it. The thing is, in the British Isles, we have buildings that are hundreds of years old now, using that technology - and the lessons from the Lead association guys' 3-dimensional drawings, are still top notch.
Speaking of language differences, I don' t have a clue what you're taking about Brian. "Leafs"? "Snakes and ladders"?
I can convert metric to IP, but I can't seem to convert your "Irish" to American English.
Robert,
You wouldn't be the first. BOH.
Ok,
Let's guess
Leafs would be like layers?
Snakes & Ladders= Can of worms?
BOH= ?
I'm guessing a leaf is a wythe.
Martin is correct, leaf = wythe.
Snakes and Ladders = Chutes and Ladders (board game)
Here's a couple others for good measure:
US 'stucco' = Brit 'render' or 'rendering'
US 'rendering" = Brit 'artist's impression'
Brit 'stucco' = US 'gesso plaster' ?
Corrections welcome. I've been away from the auld country for a long time.
Brian - it may interest you to know that I haven't seen a lead flashing in decades, except maybe on a historic restoration job. It's probably illegal, like lead in paint. Aluminum (aluminium if you like) is the standard here, at least in the SE. Plus peel and stick composites. Flashings around windows have only recently begun to approach the complexity of British practice with the introduction of exterior insulation + drainage plane techniques which are beginning to be adopted mostly in the northern US as a fix for thermal bridging problems. Yet to take hold here in the Carolinas.
When I first started practising in the UK a 2" cavity between masonry wythes was standard, with maybe an inch of insulation tacked to the inner 'leaf' with plastic buttons slipped over the metal wythe connectors. By the time I left for the US it had grown to 3". Sounds like 4" is now the norm, I assume the insulation has crept up to 3" while retaining a 1" drainage cavity. Add the thickness of the masonry on both sides and you have by general US standards (though not by R. Riversong's) an enormously thick exterior wall. Combine that with the tiny lots and the high cost of construction and you'll understand the miniscule residential room sizes over there.
James,
A few more I've collected over the years:
Loft lagging = attic insulation
Pipe lagging = pipe insulation
Sarking = asphalt felt or roofing underlayment ("sheet material placed under the roof covering material, during the construction of a roof, to provide reflective insulation and/or additional waterproofing")
For those who read French, here's a few terms I've gathered over the years:
Énergie solaire thermique = solar thermal energy
Brise soleil = sun-shading device
Chauffe-eau solaire = solar water heater
Capteur solaire = solar panel or solar collector
L’accumulateur solaire = solar storage tank
La prime = the subsidy
Énergies renouvelables = renewable energy sources
Frein-vapeur [ou peut-être pare-vapeur?] = vapor barrier
Efficacité énergétique = energy efficiency
Pose = installation
écran à l'air [écran pare-vent?]= air barrier
polyuréthane giclé = sprayed polyurethane
L'amélioration thermique et énergétique des batiments résidentiels = Thermal and energy upgrades of residential buildings
La photovoltaïque = photovoltaics
Photovoltaïque intégré au bâtiment = building-integrated photovoltaics
Des toits solaires = solar roofs
Système solaire photovoltaïque en toiture = photovoltaic roofing system
L'éolien = wind energy
pare-pluie = WRB? drainage plane?
Les murs avec écran pare-pluie (les murs pare-pluie) = rainscreen walls
Avant-toit = roof overhang?
Maison saine à consommation énergétique nette zéro = Net Zero Energy Healthy Housing
Petite hydraulique = Micro hydro
Pompe à chaleur = heat pump
L’alimentation en pellets de bois = fueled by wood pellets
Chaleur verte = green heating
L’hydrogène et la pile à combustible = hydrogen and fuel cells
Chauffage à distance = district heating
Echangeurs de chaleur = heat exchangers
La rénovation basée sur l’efficacité énergétique et les sources renouvelables = energy retrofit work
l’isolation thermique = insulation
Le test blow-door = blower-door test
Apologises all btw, I wasn't conscious of the fact that a 'brick leaf' was such a weird concept to readers in north America. I guess when I think about it - calling something a brick leaf, is a lot like saying a steel handkerchief! ROFL! Anyhow, you will see plenty of representations of our cavity wall construction at cavity trays dot co dot uk. The main point being, is that cavity trays 'add value' by producing a product, where they went to considerable bother to understand and interpret the 3-dimensional nature of the weathering problems. This is universal, whether it is stick frame, timber frame, brick leaf construction or otherwise - weathering operates in three dimensions - so one has to endeavour to understand the problem in three dimensions.
Thanks to John Brooks for raising the question - when Robert Riversong asked me to explain, it still didn't dawn on me, that he genuinely didn't know what a 'break leaf' was - or that he had never heard of 'snakes and ladders' board game. Wow-wee! Now I rate the Mars discovery robot project's chances even worse than before! Imperial measurement systems aside. When we can't even talk about 'snakes and ladders'.
James, I'm certainly aware of the environmental considerations with the using of lead on buildings. But as one architect said to me recently on some detail I was doing - lead and stone go together - like a horse and carriage. I think he is right.
Above 4-inch cavities between wythes (masonry leafs), the entire system begins to fall apart. Think of all the trouble you begin to have where windows or doors puncture through both wythes and cavity. The window or door has to be structurally supported from the inner wythe - otherwise it would fall into the cavity space. So, we haven't figured out what to do at the moment. We will probably convert to using SIP framing to beef up the inner wythe with R-value. Still have a 4-inch cavity with some insulation and have a brick outer wythe to make the building look like a regural brick building from the outside. But as I well note from Lstiburek, Holladay, Straube and so on - the 2-inch foil faced polyurethan board outside a sheet of plywood or OSB, is not sufficient to push out the condensation point away from the sheeting.
James is right about the tiny lots and miniscule residential room sizes. All true Robert. But don't forget the poor glazing orientations also, lots of shading from neighbouring buildings, and lots of thermal mass to heat up. That is why air ventilation heating systems don't operate as well as they do in north American lightweight construction. Warm based central heating systems, fuelled by gas or oil boilers 'match' the heavy weight construction. In other words, it takes a good while for the water central heating system to get going - and the masonry is slow also to heat up - so they match one another. It never gets too cool outside in cities in Ireland either. You can come home in evenings and afford to wait for the heating system to come up to full throttle. In other climates where it is 30F outside every night when you arrive home, you need a lightweight construction and air ventilation heating system which gives you instant thermal comfort.
Martin says,
That's what we are always told Martin.
But, real roofers like yourself (ones who work in the British Isles), know the real reason for sarking felt is to avoid negative suction pressures given the gales we get in from the Atlantic ocean. The nearby gulf stream has the advantage of giving us constant mild weather - sometimes at December 21st, it can be like a spring day - but when it blows, it blows. The slates roofing material would be whipped off the roof due to the negative pressures which can develop in the roof attic space. So you can think of sarking felt really, as a kind of early attention to detail, to airtightness - to outside weather environment. Not so much for thermal performance - but from the point of view, of roof slates durability.
I had noticed the term "sarking" on a UK website
It was called Sarking Board and I assumed that it was a "racking board" and an Air Control Layer.
On the same site I noticed that they assigned time values to the roof and wall assemblies.
Very interesting.
The service core seemed very common too.
I will dig up the link and post it.
Here is the Link
http://www.natural-building.co.uk/PDF/Pavatex/090216_Technical_Manual_PASSIVHAUS.pdf
THe site is UK
The product seems to be Swiss
The website that I just mentioned was one of the sites that gave me the notion that modern European Light Frame (Stick Frame) construction was more vapor open than the trend in the US
and BTW I still don't know what BOH means
The NBT Homepage
http://www.natural-building.co.uk/
Brian
no need to separate your links with "dot"
we do this with email addresses to avoid "mining"
no need with weblinks
Just paste it or write it into the comment and then we can click on it.
John,
Sometimes the spam filter stops me dead, in adding the URL's. If I have time usually I try to include them, but I only grabbed 5 mins this morning to write a reply and get it posted. On the snakes and ladders, if you don't write the sequence of operations for the contractor on your architectural details - sometimes the contractors use the wrong sequence, and you slide down the snake. If the builder uses the right sequence, you can achieve performance in all aspects of construction, and you are on the ladder up to success. For instance, if you are building multi-storey residential construction - the sequence I would specify on my drawings (or perhaps as part of the contract), would be to install glazing vertically. I.e. Finish block-by-block, rather than floor by floor. If the glazing contractor finishes block by block, it gives greater time back to the interior trades to spend more time getting it right. On ther other hand, if the glazing is done horizontally, across all blocks at the same time, then the interior trades are compressed into a mad couple of weeks at the end, to get their work done. But it applies to little details also. You really have to the right sorts of contracts to implement this. Normally the relationship of the architect to the sub-contractor is so distant, the architect has no influence at all on the sequence of building operations, in details, or in the over program management. Chapter five of Amory Lovins book Natural Capital has a good indication of what I mean - where you move to more integrated kinds of construction. AutoDesk have a lot of great webcasts do do with their Navisworks software - which can link to the project schedule and look at the four dimensional aspects of construction. Builders are aware of the fourth dimension, because time is money for them. But green architects need to insert themselves in that loop also, if possible, through different contractual formats. It is a challenge, because in my multi-storey residential example, the glazing is installed horizontally, for health and safety reasons, to do with levels of scaffolding being reset differently for masons/glazing gangs. And the fact that construct at the top of a multi-storey block might be still ongoing, as the windows are being installed lower down. If a main contractor wants to aim for green standards, the program needs some attention.
The sarking layer of bituminous felt is used in the British Isles in the absense of any roof sheeting. We don't use roof sheeting over here. We only use rafter framing on top of the masonry walls. One being attached to the other by means of metal straps. Engineers here in the British Isles believe, there are a lot of structural reasons for the roof sheeting on north American stick framed construction. I know you guys have to comply with sheer wall regulations and so forth. But there is always some bit of margin added structurally too, for risk of earthquakes. Especially in the west coast I imagine. In Britain we put the bituminous sarking felt straight down on top of rafters, or trussed rafters. When you don't have a sheeting element to your roof, as I said, you need to deal with the negative suction pressures. Hence the use of those bituminous felt membranes to stand in for sheeting. Because of the masonry wall construction, there is no great problem with shear stresses carried up to the roof structure. It is only a case of holding the lightweight roof frame onto the masonry walls by means of those metal straps I refered to.
Joseph Little on cavity wall construction - masonry inner and outer leaves (leafs). Spam filter blocks it.
joseph little architects dot com, slash documents, slash 'cavity wall paper' dot PDF.
BOH (Brian O' Hanlon).
Suggestion to Green Building Advisor - a couple of articles here and there, which look at the wrong or right ways, you can sequence the execution of a project would be interesting. For all of the attention to technologies and materials themselves, in the real world projects have to be constructed within a maze of dfferent constraints. To do with availability of different specialists at different times in the construction program, and the difficulty of having too many trades all bunched up together in small spaces. Sometimes to achieve quality, you have to spend a little more money to induce a sub-contractor to arrive earlier - do a little bit of work - and go away again, until the bulk of the job is due to be done. These little considerations can make a lot of difference.
A while back we got our carpenters to spend a bit more money to install a sold plywood baseboard, so that WC's and sinks could be installed by the plumber through pre-drilled holes. I think we got the carpenter to install the plywood base board - then the plumber pre-drilled the holes. Then the tile contractor installed the tiles. And then the plumber installed the sanitary ware - through the pre-drilled holes, and the plumber thereby didn't break any tiles. So everything did well out of it - and all it relied upon, was some clever coordination. Anyone who has worked in the HVAC industry knows all about projects, where the wrong contractor took the lead in a job, and it put the entire sequence out of order. It happens, and when it does some aspect always suffers. When it comes down to airtightness of the envelope, and installation of insulation - it would be nice to read a couple of GBA articles on this.
My understanding of the sarking is rather different from Brian's. It's nothing to do with wind uplift, though it does have everything to do with those rain-heavy gale-force winds bearing in from Atlantic blowing water into the gaps between the tiles or slates. The sarking is a WRB, nothing more. It's draped rather loosely over the rafters so that there's a gap of an inch or two under the horizontal nailing battens that hold the slates and dressed into the gutter at the bottom of the run. Thus it provides a continuous drainage plane to carry blown-in water safely to the exterior before it can do any damage. In the rare instance when solid sheathing is employed over the rafters the roof must be counterbattened to preserve this drainage plane. Slates and tiles have been used for centuries before the introduction of sarking in the last century, their weight was ample to resist wind uplift even in extreme conditions - an unsarked roof actually has fewer wind pressure issues because it is so very air-permeable. You might lose a slate or two during a bad blow but this was due to the roof being 'nail-sick', i.e. the securing nails being rusted out. I have seen older roofs actually secured with oaks pegs, more durable than steel nails but very labor intensive. Stainless steel nails now eliminate this problem.
Back to the sarking: a few drops of water blown in a dispersed pattern into the roofspace was not such a huge problem when there was no insulation up there and the ceiling finish was traditional plaster on lath. The plaster would get a little moist and then dry out: Robert's hygric tolerance in practice. This all changed with the introduction of fiberglass insulation and paperfaced plasterboard, neither of which is water tolerant to any significant degree.
By the way, North American readers should note that you do not walk on a roof constructed in this way. The tiles/slates are brittle and very easily damaged by foot traffic. You work off a hooked roofing ladder, usually supplemented by full ground-bearing scaffolding at the eaves, even for a relatively minor repair and always for a full re-roofing job. Yet another reason for high construction costs. On the plus side, such a roof will easily last a hundred years before it needs re-nailing, and even then the vast majority of the slates will be directly re-usable. Across the pond, asphalt shingles are generally reserved for dog-houses and garden sheds.
By the way, Brian, solid sheathing does indeed supply racking resistance to the roof structure but this is nothing to do with the materials forming the walls underneath. Roofs over masonry walls require this bracing just as much as framed walls do, in British practice with non-sheathed roofs this is supplied by engineered struts applied diagonally under the rafters.
John: BOH = Brian O Hanlon.
Another one lost in translation from BOH:
US 'baseboard' = UK 'skirting board'
UK 'baseboard' = US 'I have no idea'
The point about coordination of subs though is well taken. Most construction professionals, at any scale and in any country, will have their horror stories about a following trade ruining the best laid plans etc. This is especially true of the still-developing technologies of building green.
James,
There's no reason for the Irish or British to get proprietary about slate roofing -- there's plenty of slate roofing in the U.S., at least in the northeast.
When I worked as a roofer, my company did a lot of slate roof repairs. All of the slate roofs I worked on in Massachusetts had solid copper nails. They're a little soft, but they should easily last the required 100 years.
Most of the slate roofs I worked on lacked "sarking." As you point out, a few drops of water now and then won't hurt an attic, as long as you don't put any cardboard boxes of junk up there.
Pennsylvania, Vermont and Maine all have slate quarries.
Thanks James
Doh(Homer Simpson reference)
JOB
John O' Brooks
I was kind of hoping it would turn out to be "bat outa hell," although I'm not sure what Brian would have been flying from at such a high rate of speed.
James says:
I've look at some many site construction photos of passive homes built in the US now - and also, PV solar or collectors being installed on pitched roofs in the US - and it never fails to crack me up, when I watch this roofers walking on top of roofs, standing up. You would never, ever do that where I come from. But here is the thing right - and this is exactly my point about north Americans and European green builders conducting a conversation - when you think about installing collectors and PV arrays in Europe, the designer has to consider the health and safety aspects of design under new legislation. I.e. The installation, operation and future maintenance of the building design has to be considered. What happens if a solar collector gets broken? Do we wait for scaffolding and slating ladders to happen? Heck no. I think, as part of the green building drive, and in tandem with the new H&S responsibilities, we aught to look hard again in European at sheeting boards on our roofs nailed on top of our rafters.
BTW, the base board I talked about to mount sanitary ware, is what we would call a plywood 'ground'. For instance, if you do stud wall partitions and have to mount a hand rail, you would normally install plywood sheeting again where the hand rail is. It just means the carpenter has something to nail into, known as a plywood 'ground'.
In the case of plumbing and sanitaryware - the danger is that a plumber will yank the copper pipe and to fit his sanitaryware - and if the tiles are already on the studwall & sheetrock, then the tiles will chip and break. So the idea is to spend the price of the plywood to provide 'grounds' for the plumber. That way he can tug at his pipes and stuff, to get the sanitaryware fitted, and the tile contractor doesn't have to return and fix broken tiles.
The idea of allowing the tiler to work before the sanitaryware goes in - is that the tile contractor doesn't waste his time trying to fit little weird tile shapes in and around the sanitaryware. He simply tiles a plan wall, and provides the holes for the pipe upstands and projections for the plumber to work with after. It saves both trades time and money - and it saves the main contractor a good deal of headache running around doing quality control and chasing people. I often say this to green builders here in Ireland, but they rarely believe me. My company changed the sequence of operations of many, many trades - for one reason or another.
It is like Formula One racing, and an efficient pit crew that knows how to coordinate properly. When something goes wrong - I really goes wrong - and you can find yourself out of the race, because of one wheel nut that wouldn't come off.
Evidently, British "baseboard" = U.S. "blocking."
Martin, thanks for the corrective about slate roofs. I was not trying to suggest that they're unknown this side of the water, but rather that many US readers will be unfamiliar with them. Points up, once more, the importance of regional variations within the US. Down here residential roofing is asphalt shingle or metal, pretty much exclusively, I only know a couple of roofers I'd trust with slate - if I could ever get a client to pay for it. I believe that clay or concrete tile is common in FL & SoCal, probably elsewhere too.
Blocking is a very good word, a very good word indeed. You guys have the timber/stick framing traditions and all the great vocabulary to go with it.
In fairness though, you have to go to Scandanavia in Europe to find anything like the same style of construction of timber housing stock, you see in the United States. It is all to do with availability of materials. Our timber in Ireland grows way too fast, with the rings spread too far apart to make decent construction lumber out of it. You need the big mountains with the snow covered caps to get the really good pine lumber. The northern latitudes etc.
My pet theory is that Scandanavian and possibly German techniques left Europe and literally spread all over north America. In the British Isles, our stick framing was only a business venture that was re-introduced in order to grab some market share off of the concrete industry. The timber and concrete sides have been going hammer and thongs here in Ireland for the past twenty years. With the concrete side losing more percentage points of market share steadily throughout that period.
As I said, even when we do stick frame - we still cover it up in brickwork masonry. Anyhow, timber as a material is so new to these parts, none of the architects here know how to detail it correctly to use as a cladding on the outside. What James says about slate material in his neck of the woods - I would say about timber cladding over here.
To John O'Brooks: I'll admit that BOH had my mind searching for some traditional Irish parting salutation for a while. It rested briefly on 'Best Of Health' before realizing the obvious.
One more Britishism: I had folks puzzled early in my US career when I referred to formwork as 'shuttering' and poured-in-place concrete as 'in-situ'.
But I never before came across 'hammer and thongs' as in Brian's last post on either side of the Atlantic, though it's an evocative image. The village blacksmith meets The Village People?
Sturdiest roof I ever saw in construction was in Rome in the mid '70's. A minor palazzo 'in restoro' across the street from my pensione was outfitted with a sloping concrete slab (poured 'in-situ', yes, at about 2/12 pitch, didn't see it being installed unfortunately) and traditional Roman tile (natch) was being loose laid on top. The slab was used to form the eaves detail over top of the stuccoed masonry of the original wall - no wood left in the final construction whatsoever. That was some serious capacitive insulation up there, well-suited to the climate I think.
To BOH:
You don't need snowy mountains and northern latitudes to grow good pine lumber. The commonest construction lumber in these parts is Southern Yellow Pine, much of it grown straight and tall in lowland plantations as far south as Georgia and South Carolina, where summer temps hit 100°F and winters seldom bring a hard frost. The lumber from these trees is of excellent quality. I once shared your perception of the pine family as a northern tree but the indigenous pine forests of the southeastern US are a sight to see. In the eighteenth century the British Navy came to N. Carolina for its ship masts, also for resin from the pine forest to tar its hulls.
Most of the "King's Pines" were in New England, marked with a triple blaze and reserved for the Royal Navy. Many colonists cut the trees illegally and then blazed smaller pines with the "King's broad arrow", and the first colonial flag was emblazoned with a white pine in defiance of King George.
I watched one of the last of the King's Pines being felled and hewn into a mast in Charlemont MA a dozen years ago, to be sent to England as a gift for a tall ship recreation. It had 80' of clear stem.
But it was the Hemlock tree that became the symbol for the people's revolution against the new colonial elites, with a sprig decorating the hats of the Regulators, as the members of Shay's Rebellion were called. They tried to stop the foreclosures on farms and eliminate the onerous debt and taxes imposed on the commoners following the supposed "revolution" against British tyranny.
This populist uprising against the legislators and bankers of the "free" colonies inspired the Constitutional Convention to reexamine just how much democracy we could really afford. It is, perhaps, for this reason that I build with Hemlock. It is the people's tree.
James,
Someone in forestry business in Ireland recently told me, our imported stocks of pines, we were growing for years and years in this country - were of a runt variety. He showed me several examples, and after I while I began to get the idea. It is like dog or horse breeding. Lets just say in Ireland, we had been breeding a horse that was never going to win any race. But perhaps we used the excuse of our climate. I remember way back in the early 20th C, a lot of donkeys were imported for use on farms in the time before mechanisation. Same thing again, they were unsuitable for the application of farm work. Though very large and strong, the Spanish animals were impossible for farmers to manage. We have had a lot of swings and rounadabouts in terms of building materials and elsewhere. Bad luck I guess.
On this:
A conservation expert from Ireland recently asked a fellow expert in Rome, when did the conservation of a certain building start. Expecting an answer of maybe 10 or 20 years ago. The Italian told him, about 50 years after the building in Italy had first been constructed. Which was about four centuries ago. The Irish expert was making the point to us, that in Italy and other countries with old building stock, the process of conservation was pretty much constant throughout the life of the building. Stewart Brand made a BBC television documentary series a while back, in which he expressed similar views. I was interesting to hear Martin talk about slate roofs in the north east also. I am sure one will find old building stock, almost anywhere in the world.
BOH,
Don't blame the Irish climate -- blame the English. Aren't they the ones that cut down the glorious oak forests and laid bare the Irish soil, subjecting it to erosion and degradation?
Martin,
Of course those are those factors also. Only yesterday, the argument was presented about government policies down through the years in Ireland. I didn't know this, but in the early 1800's, there were a lot of roads and bridges built. By the middle of the 19th century, the population of the island was climbing to 8.0 million. It has never been anything like that ever since. Emigration began after the famines of the 1840s. It was all wrapped up and inter-twined with Tammany Hall politics on your side of the pond.
To be honest Martin, I am not sure if it was left to the responsibility of the Irish natives - that they would not cut down the forests themselves. Or that, the presence of the English had not a positive effect on the island - from the point of view of retaining and planting new stocks of deciduous hardwoods. The whole subject with regard to English colonisation is a trully vast and complex one. But it is interesting today, from a government and administration point of view - a lot of intervention into the market seems to be occuring. With incentives to preserve equatorial forest land through carbon trading, incentives for high performance windows, and as Wolfgang (Dr. Feist) reflected upon in an interview, the huge subsidy for PV solar power generation in his home country. The theory of financial engineering in this area is becoming trully large and multi-faceted.
As Wolfgang would say himself, we need to be careful when these financial innovations are used inter-changeably. With acres of forest, window specifications, solar PV in-feed tariffs etc all being juggled around by policy makers. I am sure, many weird and un-predictable outcomes are possible from all of that synergy. Wolfgang I believe, must be fighting to preserve the original conceptual integrity of his work. In the hope it will stay intact in one piece, as a body of knowledge useful to further generations. Thanks to Mr. Riversong above for the excellent piece of north American history. Physicist David MacKay's invention of the 60 watt lightbulb per person per day unit of consumption offers a lot of scope - when we get to the stage where we try to compare one technology or solution with another. See his website, Without the Hot Air. I would enjoy reading a blog sometime soon, of the GBA response to Dr. MacKay's work. Until then. BOH.
BOH said:
Sorry, forgot to finish statement. We are in the middle of providing 'stimulus' to our flagging construction industry through state funded infrastructural projects at the present in Ireland. The point was made by someone, it happened over 150 years ago, the construction boom was being supported while people lived at subsistence levels. BOH.
From the CLAM bluehouse blog entry of May 11th 2010.
Exactly the same idea I was referring to for doing tile finishes in bathrooms, before the sanitary ware was installed, rather than afterwards. The bluehouse people refer to their plywood 'grounds' as 1-inch backing/bed for the sheetrock.
http://clam-bluehouseblog.blogspot.com/2010/05/air-sealing-details.html