Creating an Energy-Efficient Forced-Air Heating System

I have been trying to figure out my heating and cooling and while I know lots of guys on here seem to prefer heat pumps for everything. I’m trying to figure out the best combination to heat my garage and basement and my upstairs of my new house. The quotes I’m getting back for radiant heat and Mitsubishi’s are beyond what I can afford. Can a forced air system that’s high efficiency be a good system when done correctly? Does anyone have any recommendations as far as how to do this hookup on the system?
GBA Detail Library
A collection of one thousand construction details organized by climate and house part
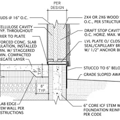
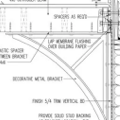
Replies
For your heat source. A lot comes down to what fuels you have available in your home, your climate zone and the size of your house. The best any conventional system can perform is 95 to 100%. Where heat pumps can average 200-400% efficiency.
For efficiently using a standard system.
Look into effectively insulating, and spend extra time and attention to air sealing. A tight house can have savings of 15 to 30% of a regular build. Also, perform a proper heat loss study and do not oversize your unit.
Realistically, for heating equipment only.
The most cost effective system I have found is a decent furnace, paired with a single minisplit to manage heating and cooling, with a dual output thermostat. A decent minisplit will run less than 5000 and the savings are up to 600-1200 power year over electric heat. If you're entertaining A/C at all this is a much better option.
You might want to take a look at some of the articles in our Forced-Air Heating collection.
Radiant heat IMHO is an expensive luxury, but can be very comfortable. If you're careful I think panel rads can keep costs under control, but infloor heat is expensive almost no matter how you approach it.
Mini-split prices are often inflated due to excessive room by room zoning approaches, and the associated over sizing. Going with 1 or 2 ducted units may be more cost competitive. To make an apples to apples comparison a single zone ducted heat pump (like the Carrier Greenspeed) might be more appropriate if the alternative is a single furnace.
Zoning is a luxury that drives up the cost regardless of the tech. But more zones aren't necessarily better.
Compact ducted heat pumps do offer the opportunity to vastly reduce the amount of ductwork since they can be place within the zone and just ducted to adjacent rooms with short runs, rather than long home runs to the basement typical of a furnace.
The Fujitsu compact ducted units have proven themselves to be good performers in a wide variety of climates. Some out of the box thinking like using a bit of resistance heating (like the bathroom floor), or cold corner bedrooms, can help keep the size down and the duct runs short, and the system simple.
But to answer your question yes forced air be very comfortable. Unfortunately because it's the value option, often shortcuts with size and duct design are taken. These shortcuts are going to affect comfort regardless of the heat source. Get it sized right and use multistage/modulation if possible. Even the smallest mainstream furnaces (40kbtu) are bigger than what most reasonable homes need. But some of the modulating/staged ones go down to about 25kbtu. This will give you longer heating cycles with lower airflow rates and more even temperatures throughout the home. If your heat loss is close to pushing you up into the next sized furnace, really scrutinize it, and consider adding some electric heat somewhere (again like the bathroom floor) to allow you to stay in the smaller size range to get access to the low min fire. A 100kbtu modulating furnace might only turn down to 40kbtu which might still be oversized even at min fire.
The term scorched air (short intrusive cycles of hot air), really comes from oversized furnaces, feeding undersized ductwork, with poorly placed stats and a badly sealed/insulated envelope. This is an easily avoided recipe for discomfort even with cheap equipment it's possible to have a high level of comfort and efficiency if care is taken. IMHO, Comfort starts with a good insulation and air-sealling, then comes your system choice.
What’s a good source to find out how to size a furnace I’m doing icf with good quality windows and it’s sealed up nice and tight but everyone around here is still pushing for a really big furnace it seems.
Lastly how do I go about heating the garage and the basement that’s why I had even considered radiant heat it just makes more sense in those areas.
Appreciate your thoughts and comments.
If I remember correctly you’re on a new build, Wiscoguy, in which case a Manual J (and S, and D) need to be done to make sure that you’re properly sizing equipment. It seems particularly important in a high-performance build as the efficiency of the envelope means that the rule of thumb, which is already oversized in a code minimum build, is likely to be waaay oversized.
I had a Manual J, S, D done (remotely) about a year ago for my existing house, and it was really easy, and not particularly expensive relative to the cost of HVAC equipment.
WiscoGuy,
Brian is quite right to urge you into analyzing your heat load. You also need to work toward detailing the basement and garage insulation to your advantage. I strongly recommend underslab insulation of at least R-15 more if feasible. Basement walls to the same levels. Walls and roof insulation preferably R 30+ and R50+. Windows should be U .22 or better.
As to the question of an "efficient" forced air, most of what you need to think about has been covered by Matt and Josh. I can add that a friends natural gas forced air system is a sterling example of top notch design and top notch cost. The ECM variable speed multi level firing furnace and large ducting makes his heating almost invisible. No scorched air, no obvious air drafts and almost no noise. His gas bills make me weep about my radiant cove heaters.
That said, I can't get natural gas to my house and propane fluctuates wildly here. Spot prices one winter were north of $4.50 a gallon. Minisplits were almost unknown here five years ago and the quote I got from the one installer gave me scorched hair.
I ended up with cove heaters. I pay approximately $1600 a season to heat in CZ6B at 8000 ft. I don't have to derate my heaters for blower losses or fuel losses. I didn't spend $30K or so for ducting and furnace installation. I am pretty sure I will not face repairs or maintenance on my cove heaters. I fortunately do not need AC in my climate. You most certainly will. Minisplits will most certainly be the best efficiency as to overall run costs, but system design as Josh noted is critical. Your floor plan will affect the choices greatly. It may be that in your region minis are simply overpriced and a gas furnace with AC coil is the better way to spend upfront. However, you need to know what you are sizing for first. A large cross section duct system and careful sizing will be a big help in keeping the summer mugginess under control.
Your floor plan and how far you take your house envelope will be a major determinate of which system works best. You can't make effective comparisons without knowing how much heating and cooling you actually need. If you need an example of how random some guidelines can be, check out this link -
https://www.mass.gov/info-details/household-heating-costs
According to this overview, resistance heat for a home of 1800+ sf should run $4500. I am heating 2700 plus a basement to 70F. Obviously, my envelope is better than most homes in Massachusetts by quite a margin by this metric. My Kwh cost is about 15.5 cents inclusive of all costs vs 24 cents so $2900 would be the adjusted cost on their chart. Still, it does show how the effort I put into the shell insulation made it possible for me to use the seemingly dumb choice of resistance heat with reasonable success. It really isn't a luxury, it just fits the conditions I built in more successfully than the alternatives.
As for your garage concerns. How do you plan on using the garage? Trying to make a high quality warm space out of the one place with generally leaky doors is problematic. It will be frustrating to you to have just warmed up the place only to have to open the door and go fetch the spouse or kids in February. Most of what makes you feel warm is warm air. If you try to warm the floor, you will find it a pretty big heat sink that is slow to go up after it has cooled. Keeping it warm constantly will quickly reveal the loss rate to be much higher than the rest of the house. It would be unwise to size your systems to accommodate the garage as part of the overall goal. It will be like factoring in a brick against a feather if you do the house load part right.
Thanks for the reply. I keep my boat and many tools and liquids for work that cannot freeze. My other option would be a simple gas hanging heater I only want the heat up to around 45 in there and only for about 4 months.
My house will be insulated fairly well but not conventional it’s an icf build so no air penetrations thermal mass and r23. Windows uvalue .17 floors r15under basement and garage.
Do you have any experience with forced air and zoning a basement system at all? More from a standpoint of cold floors just do to ground temps? Even with the foam I’m worried the floor will feel cold all the time
I agree about the garage heating and even on the idea of forced air for the main house based on what knowledge I can gain. My bigger problem is how do you heat the basement. Do you zone the main furnace even with insulation under the concrete basement are inherently colder spaces. Floor heat in the basement rises to keep the upper floor a little warmer as well.
This is the same setup in my current house it was cheaper to put floor heat in and run it off a direct vent water heater than it was to try to add heat ducts in the basement. It has worked superbly for seven years and actually lowered my overall heating cost despite adding sq footage.
So my major concerns for any system is basement warmth. My fiancée office is there and she works from home happy wife happy life. Also garage has to be kept minimum of 45. The garage will also be icf completely and have no windows so garage doors is biggest heat loss area.
Thanks again for all the input appreciate the posts it really has been helping me reason through all this.
You should use BEopt to help with all the energy related options.
WiscoGuy,
The only experience I have had with forced air ducting in basements involved two mediocre homes in Illinois. Both solved the problem of putting heat into the largely open basements by simply cutting rectangular holes in the main trunk, one each end of the basement, then screwing on adjustable louvre vent covers. Warmer than otherwise, not zoned, so my happy wife upstairs drove the set points. Be sure to check with local inspectors and code before marrying to the idea of hanging a gas heater in the garage. Especially if you have living space above the garage.
FWIW, my current non-forced air situation means I am heating my entire basement with one cove heater that faces my main work bench. I am able to maintain 67F which is workable. I tend to sit and ponder my projects more than complete them, so I do feel a bit cool-ish at times. Once I actually start to work, it is just fine. I have all my foundation insulation on the outside, so the thermal mass effects seems to work to my advantage. Quite useful when it is 90F outside.
The basement slab is on top of 3" reclaimed XPS set over a deep washed rock bed, which has a pre-need radon collection system embedded in it. Any ground water is kept well below any contact with the foam, so the rock helps keep the insulation value intact. Using what too many call "gravel" or too thin a layer of stone for your local water table could allow water to come into contact with the foam and allow much higher conduction to ground temps. If the water gets too high, it will start entering the foam and degrading the R value. Crazy high water will likely get into your slab even if you have good thick plastic between foam and slab. The process of setting screen/rebar and pouring are not gentle arts. Best answer is to have solid drainage to daylight and never let the water get up into things.
Lots of other details come to mind, but to stay more on point I will mention that I put in radiant loops in the basement slab and the garage slab in case I needed them. Five years on, I haven't. The no window 3 bay garage is attached to the house in a way that makes the total wall area about 50/50 open to weather/shared wall to living space. The shared walls are R-30, the exterior walls are R-15 outsulation. ( the same 3" reclaimed XPS) The roof has 6" EPS nail base under a membrane roof.
I generally hover around 40F even in February, the 5" slab does buffer our coming and going which is not frequent, since we don't have kids to cart around this stage of life. The garage doors are nominally R-11 urethane filled Clopays that I find quite good at air sealing between panel sections. We get 50+ winds here, so I divided the doors individually rather than a 16' plus one 7'. I get better wind resistance and less loss from only opening 1 door as needed. I do also have a thermal break of 1" xps at the slab edge - outside apron, which has been very helpful. It also has not broken down nearly as fast as I expected despite our huge UV load here at 8000 ft.
I have successfully brought the garage up to bearable temps to cut tile in the winter using electric blowers. Unfortunately, warm air rises, so most of the warmth nestled in among the trusses. Surrendering the storage space above by dry walling the ceiling may be more valuable to you in keeping warm. You might consider creating a small cubby against a shared wall to keep temp sensitive materials. The insulation on the garage side of such a cubby would create a giant insulated box with one warm side. Double the fire rated sheet rock on the inside.
Returning to the basement, flooring choices can go a long way to temper the perceived cold floor problem. A properly protected slab could take carpet, but the humidity issues in you area will tend to make them a bit risky no matter how good your water control. Cork tile flooring won't absorb much and it feels much warmer under foot than tile thanks to cork's natural properties. I lived in a Meis apartment for a year and learned the thermal value of cork. It was glued directly to the concrete floors. Getting a ducted system to fully mix the air in a basement along with the main house is one of the major stumbling blocks with ducted air systems. For some reason I have not encountered one system that can do it. The basements seem to become the poor sister no matter what.
One thing to note about ICF R-values is NOT to make much of the thermal mass. A study done on three homes in New Mexico did demonstrate some useful effects, but the diurnal temp swings are enormous in dry desert climates. Warm muggy nights in August are what I recall for Illinois and trips to the Dells. It is much too long a discussion to dive into now. Be satisfied with the inherent air control, sound reduction and tornado resistance properties of ICF. They are still a pretty good deal on those counts. If you can still make ICF choices, check out Nudura plus or One series. Nudura Plus puts more foam on the outside, One series eliminates it on the interior side. Each approach has its virtues. Also think now about window details, it can get messy quickly with ICF when someone screws up a measurement.
Try getting bids for the high end conventional heat pumps with variable speed compressor, 2 electronic expansion valves, ECM blower and communicating thermostat of the same brand. The HVAC guy will want to put in strip heat as a backup.
My Rheem HP can carry my house down to about 6° with the strips locked out.
I say get anything you do not want to freeze out of the garage and into the basement. There is nothing green about heated a garage 24/7 it is an unnecessary luxury.
If you have done a good job insulating and air sealing the basement will almost the same temp as the main floor. I say put a small electric heater in the office and use when needed.
Walta
When I say heated it just needs to stay about 40 degrees which if insulated well shouldn’t be to bad really
Lack of air sealing will lose a lot of heat - and air sealing isn't so easy for a garage door. On the other hand, a heated garage closet would be easy and much cheaper to heat. Cars and boats can be made freeze tolerant.