Finding Contractor for Exterior Rigid Foam Installation

Hi everyone,
Thanks for taking a look. I really appreciate all the great information I’ve learned from this site and forum.
I live in Nashville Tennessee climate zone 4.
What should I do if I can’t find a builder who can install rigid foam? I have asked several and it seems to be a pain for most because of the subs being unfamiliar with it.
I haven’t seen a single home in the last few years we have been looking use exterior rigid foam insulation. I would prefer this system rather than double stud wall. Anyone know any builders in Nashville they would recommend? Any referrals?
Any other ideas, in terms of wall systems that might achieve similar results?
zip sheathing is gaining ground in Nashville. I’d rather not use OSB because of water fears (not confident in trades here doing an immaculate job) And I’d rather especially not use Zip R insulated sheathing, as I don’t like the idea of one product doing three things in which a failure in one component of the system could cascade into a catastrophe.
Thanks for taking a look. I appreciate any help and advice you all have
Amer
GBA Detail Library
A collection of one thousand construction details organized by climate and house part
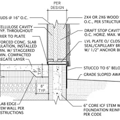
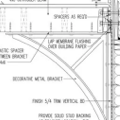
Replies
If you are not in an area where exterior rigid is mandated by code, you'll have a hard time finding anybody to install it.
Since you are in a milder climate, I would run your design options through something like BEopt and see what assembly R values make sense. My guess going much above a 2x6 wall with HD batts is not going to save you much energy costs.
If you do want higher R value assembly, your best bet is 2x8 24" OC walls. The lumber costs are a bit higher but the rest of the details are standard house build.
Akos,
Thanks for taking the time to respond. I was hoping that given that folks are building in FL with rigid exterior foam, that might be an option for us here in Nashville. But FL does have much warmer weather so maybe it just makes more sense there.
Although I am not a fan of zip R, do you think it makes sense here, in a mild climate where we can’t get exterior rigid foam?
Concerns with zip R would include:
Sheathing outside the insulation
OSB and water damage.
Installation concerns with overdriven fasteners, staples, poor tape adhesion, J rolling etc
Makes me prefer standard plywood sheathing.
I will have to check out 2 x 8 walls to see how where it gets us in terms of R value.
Thanks very much for responding!
Amer
The "sheathing outside the insulation" is something Huber has tested, and they have design specifications for that. You absolutely have to follow their nailing schedules if you need the shear performance though. No exceptions.
Everyone seems to think Huber is using a better grade of OSB in their Zip product than the usual stuff in the lumberyard. If you do have any moisture intrusion issues, I think Zip will hold up better in comparison to "regular" OSB. That said, any sheathing needs some protection from bulk water so you should really be addressing this with your WRB and trim details regardless of what sheathing you use.
There have been some reports on GBA of severely overdriven nails in Zip products, but I wouldn't put that down as a fault with Zip. Overdriven nails are a problem with ANY sheathing (or anything else for that matter). You can blow through plywood and have problems too.
My own personal preference is for plywood on the exterior, but if I were to go with OSB I'd be most comfortable using Zip. Exterior rigid foam will help with air conditioning too since all the same benefits apply (reduced thermal bridging, etc.), but heating dominated climates tend to have the most to gain with insulation in general. If you go with Zip-R, it's the thickest two versions that people have the most concern with in terms of the structure (shear strength), if you keep with the thinner versions there is less of an issue.
Bill
Bill,
I agree. I prefer a thicker plywood especially the familiarity the trades have with it.
I think a thinner zip R (3 or 6) would be good compromise if I can’t get the GC to do a external rigid compromise. I’ll have to learn about the nail schedules and compromises to rack strength.
I actually wondered how well the zip R does with thermal breaking? I know that some of the GBA posters think the thermal break is overhyped by Zip....any thoughts?
I don’t see why zip-R would be any different from regular rigid foam installed on the exterior. Rigid foam installed with either product is “continuous insulation” and covers all the studs. It’s this insulation over the studs that reduces thermal bridging. R6 of Zip-R or 1” of polyiso over the sheathing (also R6) accomplishes the same thing so there should be no performance difference between the two.
Bill
I used a lot of my Zip scraps as stepping stones in the mud bog that was my construction site. After months of water soaked ground contact I did not see any evidence of swelling or delaminating.
Huber who makes the zip sheeting also make the Advantech OSB subflooring that is rated for months of water exposure so I am not surprised.
My general contractor could not get his normal siding sub to install my Zip with 1 inch of exterior foam topped with vinyl siding in zone 4. The general and his trim carpenter did a lot of the siding.
I came very close to using Zip+R but at the last moment I backed out, I could not get past the weaken structure.
Walta
Walter,
I know it’s anecdotal, but it’s nice to hear that zip can stand up to that abuse.
It’s possible we might go the zip R route if I can’t get anyone to do exterior rigid foam. I do like the idea of taping and having a good air barrier.
Did you do the roof with zip as well to have a continuous air barrier?
What is the consensus on zip R and it’s ability to function as a thermal break? How much more efficient is it than regular zip or plywood? Does it have a reasonable ROI in zone 4?
Huber roof sheeting is the one Huber product that never appealed to me. What is the advantage? The roof is watertight fast I think not felt paper is faster than applying tape to the joints. Most every brand of shingles requires roofing felt so you get no cost savings. I want a vented attic not an airtight attic. It scores a zero for me.
As a thermal break an R is an R weather it is inside or outside of the sheeting does not matter.
The only real way to measure return on investment is to computer model your home with a free program call BEopt. The program considers your local weather your interest rate your guess at inflation and you local costs per square foot. And lets you see what several walls will cost to build finance and operate over time. Hint the very best wall and the code minimum walls often end up about the same ROI the sweet spot in between. If you model your house be sure to find and watch the training videos expect to invest about 20 hours in this. This tool is great when it is time to pick what SEER AC to buy.
https://beopt.nrel.gov/home
Please be smart build a vented attic and keep the HVAC equipment and ducts out of the attic. And say no to cathedral ceiling.
Walta
Unfortunately, we didn’t say no to a cathedral ceiling. Our great room has two stories and lots of windows to boot.
Whether or not the ceiling is vented, the hvac equipment has a closet on second floor assigned for this purpose. Any ducts needing to travel through the attic will Be in a conditioned space (have already spoken with designer about this)
I worry that cathedral may be complex and not amenable to venting. Martin Holladay has recommended that complex roof lines should stay away from vented designs. Perhaps I am underestimating or overestimating how complex our roof line is
Today article on GBA seems to have been written to and for you eagleeyes.
https://www.greenbuildingadvisor.com/article/greening-up-vs-green-from-the-start-mechanical-systems
Walta
What type of siding are you planning for this house?
What windows?
In US climate zone 4A just about any reasonably rainscreened siding would be sufficiently protective of OSB sheathing, but could be an issue with stone or brick.
>"What is the consensus on zip R and it’s ability to function as a thermal break? How much more efficient is it than regular zip or plywood? Does it have a reasonable ROI in zone 4?"
ROI?
It's hard to make a SHORT-term ROI argument even for IRC code min, but on a lifecycle basis 2x6/R20 + 2" of exterior foam can still be rational, if there were someone in your neighborhood to build it.
Take a look at this bit of lifecycle/cost analysis from a decade or so ago, in particular Table 2, p.10:
https://www.buildingscience.com/sites/default/files/migrate/pdf/BA-1005_High%20R-Value_Walls_Case_Study.pdf
Since that time energy costs have gone down (in inflation adjusted terms) and equipment efficiencies (of heat pumps anyway, not fossil burners) have gone up. Even though the sweet-spot then was for R25 "whole wall" in zone 4 (essentially a 2x6/R20 wall with 2" of exterior EPS or 1.5" exterior polyiso), if using a correctly sized better class heat pump it's reasonable to shoot for the R20 (whole-wall) recommended for zone 3. That's pretty easy to meet or beat with 2x8/R27 cellulose (recommended) or R30 rock wool in the cavities, and 24" o.c. 2x8 framing.
When BA-1005 was first published rooftop solar cost about 3x what it does today, and if you have net-metering spending extra for ZIP-R has less of a rationale than putting that money into rooftop PV, and heating/cooling with decent modulating cold-climate type heat pump. Even though a cold climate type isn't essential for capacity reasons in your area, for comfort and efficiency the more sophisticated vapor injection scroll compressors do much better, well worth the up-charge.
Dana,
Thank you for taking the time to reply.
Definitely agree on ventilated rain screen system. Made sure designer accounts for that
Siding will likely be primarily brick and fiber cement. Smaller sections of the front will be stone
Windows primarily mix of double to triple panes. Not really what the mix will be, but can safely assume Atleast 50% will be triple paned, and whatever SHGC the designer suggests
I will have to take the time to digest the link and respond to that. I think the main point is I don’t want to be in steep part of the making a difference curve where small changes help a lot, rather than the far end of the curve where large expensive changes are needed to make small incremental gains in efficiency.
Agree. We are already planning, but the house may not be ideally situated for solar. We have lots of trees and more importantly the neighbors have lots of trees.
I need to do more research regarding heat pumps etc. I have no idea what vapor scroll compressors are.
Thank you for taking the time! I know I only have one crack at this and appreciate the help getting the small details correct
Amer
Have you considered EIFS (aka synthetic stucco)? We were having the issue in our market where installing exterior rigid insulation was very expensive due to lack of familiarity for the subs. We found a local sub for our GC that specializes in EIFS, typically used in commercial settings, and we are now having that installed. It is saving us thousands of dollars. We are using BASF Senergy channeled adhesive CI design. EIFS is super common on hotels, chain restaurants, strip malls and the like. It is also common for retrofitting old masonry buildings. The big challenge is connecting the residential GC to a commercial sub. In our case, it has been a great match and is working out well.
The historical problems with EIFS in residential construction have largely been solved by the modern installation methods. I our case the EIFS installer is putting on a full fluid applied WRB over our plywood sheathing and using an adhered EPS foam (no penetrating fasteners) with a channeled adhesive that creates a rain screen drainage plane.
BurkeHouse,
I hadn’t considered stucco. And had not heard of synthetic stucco! I didn’t realize such a thing existed. Does it come with other sidings like brick or stone?
We don’t see too many stucco homes here in Nashville. That sounds like a solid system though.
Thanks for taking the time to reply. I appreciate it.
Yes it can mimic all sorts of claddings including brick, stone and metal. Take a look around at BASFs EIFS website and you'll see there are lots of options. Chances are you've seen a lot of EIFS without knowing it. It's really popular on the Las Vegas strip for emulating stone buildings.
Take a look at two builders from the Nashville area. https://www5.eere.energy.gov/buildings/residential/results?organization_type=1&org_state=TN&commitment=all&locator_facet_submit=13+Builders
Maybe they can work for you or lead you in the right direction.
If you have the money for plywood over OSB, do it. I proffer not to specify Zip-R, for too many reasons.
I've designed hundreds of custom homes in the Southwest, were you do stucco or stucco, and almost all of my projects are with exterior foam, over a WRB, over sheathing (Plywood or OSB). In many cases, since I spec rigid foam on the outside, EIFS is a great choice, but IT MUST BE INSTALLED OVER A 3D WRB, and you must hire an experienced installer.
You should be able to save money with the EIFS system, since it comes with the rigid foam anyways, and those guys know how to apply it.
Hi Armando,
Thank you for taking the time to respond!
I checked out those builders. Neither seems to have much of a web presence or portfolio. But I think a phone call might be more productive.
Indeed, I do prefer plywood myself. If the EIFS system can work with brick and stone and fibercement exterior, I think it will be worth checking out. I will try to see what I can learn about it. Part of my hesitation would be residential contractors may not have the bandwidth or connection to these subs, but worth a try.
Thanks for looking that up.
Amer
Just a comment on Zip vs plywood from the last house I worked on...Granted it's in Marine 4 on the edge of a rain forest in the sunny PNW. The Zip had to be left outside in a really wet winter and survived though there were some mushroomed edges here and there. Much better than standard OSB. After this, the roof got plywood and was covered with a synthetic underlayment. That ply turned black with mold while the ZIp and Advantech did not show any mold at all. Kinda the opposite of what everyone always expects. ...although a friend's house down the street had to get a full reroof after ten years because the standard OSB roof sheathing was disintegrating.
Andy,
That’s good information. I appreciate it.