Capillary Break Materials

I’m wanting to retrofit a capillary break between my house foundation and mudsill/rimjoists. I’m curious what kind of materials will work as a capillary break?
I’ve read in here that Bill Wichers prefers 1/32 hdpe sheet but I am having a hard time finding it. Anyone know where 1/32 hdpe sheet can be purchased? Or have links?
I’ve also read on here that flashing can be used as a capillary break in retrofit situations. Are there any metals not to use? I think I’ve heard aluminum will degrade concrete overtime. Also is there a certain thickness of flashing that is necessary or will any basic flashing work?
GBA Detail Library
A collection of one thousand construction details organized by climate and house part
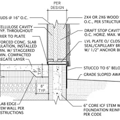
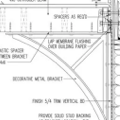
Replies
I use HDPE sheets similar to this for moving appliances and cabinets: https://www.homedepot.com/p/SHAPE-PRODUCTS-24-in-x-36-in-x-100-in-White-HDPE-Sheet-2-Pack-HDPE-2436100WHT2PK/323280182. A little thicker than 1/16" but I think that's probably what Bill was referring to.
Aluminum trim coil will eventually corrode if in contact with concrete. Copper or lead would be safe from corrosion. Any thickness will work, though for a retrofit you'd want it stiff enough to slide into place. The downside of using metal is that it's a thermal bridge.
Thanks for the reply Michael!
Is that .100 thickness too thick for under the mudsill/adjusts the house height too much or do you find it works fine? I ask because I only have certain sections of my house that are accessible to do this capillary break retrofit work. In other words, I don't want my house to get out of level with certain parts having a .100" sheet underneath. Or am I overthinking this?
It's not something I've done myself, but I've jacked up enough structures to say that making space for 1/10" material is not substantially different than making space for 1/32" material. In fact, 1/32" HDPE would be pretty floppy, and since the idea vs. using rubber or butyl sheets is that the HDPE is fairly rigid, I'd go with the 0.1" material.
One lesson about dimensions, from my carpentry days: I was on a crew, worrying about how some finish materials were laying out, and stressed about bringing it up to the foreman, who had plenty of other things to worry about. I decided that I had to let him know. He listened to what I had to say, his face got a bit red, and he growled, "You're bothering me for 3/8"?! That was a long time ago but I still think of it anytime I'm worrying about small dimensions.
It's not always a good dimension to reference, though. On the next project, a 3-story new home, I was promoted to foreman, and the foundation had been poured with a 3/8" dip in the middle of one wall. I decided that I wasn't going to be bothered with 3/8". And we fought that 3/8" all the way to the ridge.
1/32” HDPE works, and it’s often (but not always) cheaper than 1/16” HDPE sheet. Either works, but 1/32” is a bit floppier if you have to shove it in place against obstructions. I usually get the stuff from Laird Plastics, which is a commercial plastic supply house with many locations in the US. If you are near one of their locations, ask if they have any “drops” of suitable size, since they’re sometimes available cheaper than full 4x8 foot sheets. “Drops” are basically leftovers from them shearing full sheets to size for other customers. I recommend you have them cut the material for you too, typically into 4 foot long strips of sufficient width to fit the space you’ll be using it in. They cut the material with a shear, so they’ll make nice clean straight and square cuts much more easily than it would be for you to cut the material yourself if you don’t have access to a sufficiently big sheet metal shear. I don’t think they usually charge to cut the material like this.
Note that I prefer black HDPE for this application for best UV resistance, but any color will work. I don’t usually use anything thicker than 1/16” here, since I find that works well, it’s pretty cheap, and it’s readily available. You could use thicker material (0.100” is a little shy of twice as thick as 1/16”, which is 0.062”), but it won’t cause any problems. You’ll never notice a difference in terms of leveling the structure or anything like that. This is rough framing stuff where even a 1/4” isn’t usually an issue. Wood will squish a bit too if there are small variations from place to place, evening things out. This isn’t finish carpentry work where you’re trying to get your miters tight or anything like that.
Bill