Carbon footprint of high-performance remodel

Hello, so long story short, I’ve been researching high-performance options for a remodel of my 1920s bungalow in Minneapolis, MN. My current house has basically zero insulation in the walls and minimal roof insulation. In my research, a strategy similar to something that Joe Lstiburek would recommend (specifically enough rigid insulation on the exterior to move the condensation point beyond the wall assembly. 3.5+ inches in my case) would have a very long carbon payback. Basically, the carbon savings from my natural gas furnace wouldn’t justify the carbon cost of that much EPS/XPS/Rockwool for 50-80 years by my math, not to mention the cost on transportation and installation. I’m interested to hear someone else’s take on this to make sure I’m considering the variables correctly. I’m happy to post my math and sources (of which there aren’t many it seems) if anyone is interested.
As an extension of this argument, I’m curious what kind of research and writing has been done when considering super-high performance construction such as passive haus. In new construction what would be the carbon footprint payback time be for a super-insulated R-60 wall? If the extra R-40 of insulation is made up completely of XPS or EPS versus to-code construction (R-20 or 21) what would the carbon footprint vs carbon saving be compared to standard construction? Any referrals to current research would be more than welcome!
GBA Detail Library
A collection of one thousand construction details organized by climate and house part
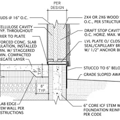
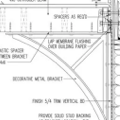
Replies
Doing deep energy retrofits with RECLAIMED roofing foam from commercial building re-roofing or demolition has been a favorite strategy, and is usually at a financial cost savings too. Re-use has extremely low carbon inputs- mostly transportation. The initial environmental hit was typically 20-40 years ago, and re-using it just piles on to the benefit side of the cost/benefit balance.
An exterior layer of 3.5-4" of 2lbs fiber faced roofing foam would deliver R18-R20 average mid-winter performance in a Minneapolis location on the exterior of a 2x4 framed cellulose insulated wall.
Running this search every week or so may dig up some VERY local sources, further reducing the transport-carbon issue:
https://minneapolis.craigslist.org/search/sss?query=rigid+insulation
>" In new construction what would be the carbon footprint payback time be for a super-insulated R-60 wall?"
In new construction an R-60 wall could be carbon NEGATIVE, if using a thick double-studwall with cellulose insulation approach (highly recommended.)
Cellulose insulation in all-wood construction becomes sequestered carbon for the full lifecycle of the building, and has very low carbon inputs after the paper-making process. Since cellulose insulation is never made from virgin stock paper, the initial hit from the paper making process is rightly applied toward the paper's initial use, and only the transportation & grinding/milling process is applied to the cellulose insulation, along with the carbon inputs for the fire retardents used (mostly a mining & processing energy input, with borate-only cellulose.)
https://materialspalette.org/wp-content/uploads/2018/08/CSMP-Insulation_090919-01.png
In Europe vapor permeable insulating fiberboard insulation (also carbon-negative) is used for exterior sheathing is available which can be useful for low-carb houses that aren't superinsulated. In North America the only similar product currently available is MSL's SonoCimat ECO4, in Quebec, (https://www.mslfibre.com/Produits/Fiche/13/SONOclimatECO4 ) but there is currently a factory being refitted for manufacturing similar sorts of products:
https://www.greenbuildingadvisor.com/article/fiberboard-insulation-developer-takes-step-forward
https://golab.us/
At about ~R2.5/inch fiberboard insulation panels are not going to be suitable for high-R retrofits on 2x4 framed 1920s bungalows in Minneapolis, but for more modest performance upgrades it's pretty good, since it's fairly vapor permeable, and doesn't necessarily need to be thick enough for dew-point control at the structural sheathing layer.