Closed-cell spray foam wall assembly

I know this has been circled about many times, but I couldn’t find any conversations that were closely related to my issue. I am an architect working on a project that was intended to be passive house, but due to costs and other issues has been down graded a couple of times. Working with a CM we ended up with a wall assembly I am questioning a little bit.
It ends up as folllows:
Metal Siding on,
Roofing felt on,
2″ atlas nail board (osb with poly iso R-9 panel) on,
Zip sheathing taped and sealed on,
2×8 wall framing w/
5-1/2″ of closed cell spray foam w/
5/8″ gwb.
Climate zone 6
My concern is, will this assembly be able to dry out as necessary? I read other posts but none have similar depths of spray foam.
Thank you in advance!
GBA Detail Library
A collection of one thousand construction details organized by climate and house part
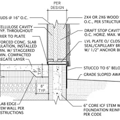
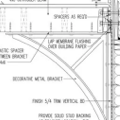
Replies
Philip,
There are several problems with this proposed assembly.
First of all, it rarely makes sense to use 2x8 studs.
Second, this wall includes the classic foam sandwich -- with closed-cell spray foam between the studs, and polyiso on the exterior side of the OSB sheathing. The OSB in this sandwich can't dry to the interior, and it can't dry to the exterior. That's a no-no for a new wall.
Third, thermal bridging through the studs makes the use of closed-cell spray foam (which is expensive and environmentally unfriendly) inadvisable for between-the-studs uses -- save your spray foam for other uses where it makes sense. You want an insulation like cellulose between your studs, not spray foam. In all cases, the best location for foam insulation is on the exterior side of the sheathing, where it can be continuous, not interrupted by framing.
Fourth, you haven't paid attention to the ratio of the insulation on the exterior side of your sheathing and the between-the-studs insulation (although with the foam sandwich problem, the ratio issue is overshadowed in this case by other problems).
For more information, see these relevant articles:
How to Design a Wall
Combining Exterior Rigid Foam With Fluffy Insulation
Martin, Thank you, This is what I assumed, and am wondering if applying a layer of dimpled tyvek or some breathable layer between the zip sheathing and Atlas panel would provide adequate airflow to allow moisture to move and dry at the layer our air and weather barrier?
It has been a difficult V/E process and this has been overlooked for sure!
Philip,
My advice is:
1. Switch to 2x6 studs.
2. Don't use closed-cell spray foam between the studs. Instead, use cellulose.
3. Choose a nailbase panel that is thick enough to at least meet the minimum requirements for rigid foam over 2x6 walls in Zone 6 -- that is, a panel with a minimum R-value of R-11.25. If the design team has a higher R-value goal for walls than R-11.25 nailbase would provide, choose thicker nailbase.
How about:
Metal siding
1x4 fir strips screwed in with six inch screws to studs in wall to attach siding
2.5" EPS foam (innie windows)
Tyvek drain wrap
OSB with taped seams, caulked stud bays
2x6 studs 24" oc
Filled with dense pack cellulose
Open cell foam in the mud sills and in the first/second floor plate area?
You will need to tape the seams of the foam too. It should provide a killer wall at a reasonable cost if there is money for proper air sealing and foam installation and the needed attention that such a siding and trim package deserves.
In zone 6 the actual wintertime performance of a 2" polyiso nailbase panel is more like R7, due to derating curves for polyiso at the low average temp through the foam.
Using 5.5" of cellulose or open cell foam and switching to a 2.5" nailbase panel would have the same thermal performance as the 5.5" of closed cell foam between the studs and a 2" nailbase panel, at a far lower cost (and at far lower environmental impact.) Open cell foam is blown with water instead of HFC245fa, and you'd be only using 1/4 the amount of polymer in the cavity, though you'd be adding ~33% to the polymer used in the nailbase panel. Polyiso is blown with pentane, which isn't as benign as water, but more than 100x lower impact than HFC245fa. HFC245fa has a 100 year global warming potential about 1400x that of CO2, pentane is 7x CO2. The production process for HFCs are much higher impact in several ways (other than mere climate issues) than simple hydrocarbons like pentane.
A 2.5" nailbase panel is almost but not quite sufficient dew point control at the sheathing for an ~R20 cellulose or open cell foam cavity fill, in zone 6, but a 3" nailbase panel would be plenty.
Using foil faced polyiso and furring without the nailbase is actually easier to air seal.
A 2x6 24" o.c. cellulose studwall with 3" of exterior polyiso comes in at a U-factor of about U0.032, a "whole wall R" of a bit over R30 after factoring in the thermal bridging of all framing. If you went all out with OVE framing and got the framing fraction down to 15% it would only add about R1 to the whole-wall figures, or a U-factor of about U0.031.
If Net Zero Energy is a design goal you'd be pretty close to being able to do it, but it's probably "worth it" to go with 4" of exterior polyiso, bringing mid-winter performance to the U0.026-U0.28 range.
If against all reason you're going forward with 5.5" of closed cell foam, it would have to be installed in three separate lifts of no more than 2" per pass, with a curing/cooling period between passes. This is both an installation quality and fire hazard-during-curing issue.
It gets complicated, doesn't it? Dana, I have noticed over many posts that you mention the global warming potential of closed cell spray foam. You may be interested to know that there are alternatives. We spray a line of water blown polyurethane foam products ranging from half-pound to two pound density with excellent performance.
Well,
We are on track of getting the spray foam out of the wall and switching back to cellulose. The CM was getting better pricing for the closed cell spray foam over cellulose... Either way, it is out. We are maintaining the 2x8 framing, this allows for the electrical rough ins to have less of an impact on the insulation depth, and makes it easier to install. We are going for a 3" poly-iso panel on the exterior to keep the sheathing dry...The CM is strongly against using z-firring and/or firring strips based on the number of times the trades have to touch the exterior assembly.
With the zip sheathing and insulated panels, they can button the building up very quickly and have work on the interior an exterior at the same time.
Thank you all for reaffirming my concerns, it helped the conversations with our CM.