Compact unvented roofing assembly: Vapor barrier options

Hello GBA Community!
Long time reader, first time poster. We are still in the early planning stages of a home that will be built in the greater San Antonio, Texas area (Climate Zone 2). My question is about the roofing assembly vapor barrier.
We are planning on constructing what Joe Lstiburek calls a “Compact Unvented Roofing Assembly” in this article <https://www.buildingscience.com/documents/digests/bsd-102-understanding-attic-ventilation>.
See Figure 7 for details. This is because we would like to expose the wood decking for aesthetic reasons. The only twist is that we plan on having both exterior rigid insulation (as the article shows) as well as interior spray foam insulation between the true roof sheathing (most likely OSB) and another layer of false sheathing which will be 1x’s strapped across the underside of the rafters to make a nice exposed roof effect while adding some insulation value.
After reading Mr. Holladay’s article about the dangers of using open-cell spray foam on the underside of the roof decking, I am thinking that we will need to use closed-cell spray foam to reduce the likelihood of interior moisture reaching the underside of the roof sheathing/OSB https://www.greenbuildingadvisor.com/article/open-cell-spray-foam-and-damp-roof-sheathing
With that in mind, it seems that the best choice for a WRB on the outside of the roof sheathing would be a relatively vapor-permeable product since it will not be allowed to dry to the inside because of the closed-cell spray foam. Most of the recommendations I have read so far suggest very tight, vapor-impermeable products such as Carlisle WIP 300HT (0.02 perms), PolyWall AlumaFlash (0.014 perms), etc. However these individuals are also usually dealing with a different type of roofing assembly. So my questions for the GBA community are as follows:
1. Am I thinking correctly about the need for a vapor-permeable WRB on the outside of the roof sheathing since the interior side will have closed-cell spray foam?
2. Do you have any recommendations for a vapor-permeable WRB material? My preference would be a peel-and-stick product.
3. Is there a better solution to prevent interior moisture from reaching the underside of the roof decking that would still allow drying to the inside? Thus, avoiding the need to use a vapor-permeable WRB on the outside of the roof sheathing?
I thank you in advance for your time and look forward to your responses! Please let me know if I can clarify anything for you.
GBA Detail Library
A collection of one thousand construction details organized by climate and house part
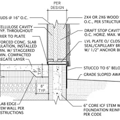
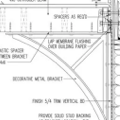
Replies
Hi Matthew -
The beauty of Lstiburek's compact roof assembly is that it's a "perfect" assembly: the air and thermal control layers are completely to the exterior so that everything to the interior of those layers pretty much sees the same conditions you as occupants do.
I would not modify the assembly; build it as shown in Figure 7. And that assembly includes roofing paper as the roofing underlayment, which is vapor permeable (in BSC's Building Materials Property Table, 60-minute two-ply roofing paper is 11 perms, vapor open - https://www.buildingscience.com/documents/information-sheets/building-materials-property-table). It's true that asphalt roofing shingles exterior to the underlayment represent a Class II vapor retarder (about 0.3 perms), but the idea is that if enough solar energy hits the roof cladding, it will dry out the moisture-sensitive materials to the interior.
Peter
Peter,
Thanks for the response! I can understand the reasoning behind putting all of the insulation and vapor barrier on the exterior of the sheathing. And by not needing any closed-cell spray foam on the inside I can avoid trapping moisture in the assembly altogether. The downsides to that method I was trying to avoid were twofold: 1) that would require extra thickness of rigid foam on the outside and prevent utilization of the rafter bay cavity space, and 2) I now have to rely on the decking boards to be the primary roof sheathing instead of a more common material with less seams such as OSB or plywood.
Both of these negatives are non-critical, but I was hoping to get away with some non-structural veneer boards as the underside decking that would be left exposed. Also, there are sections of the roof that will not be exposed from the inside and in those areas I will opt for the simpler and cheaper OSB/plywood options which means now my roof sheathing has mixed materials. But again, these are non-critical issues so maybe I just need to accept them and move on.
Let's assume I stick with this plan for the sheathing; I can then use a vapor-closed, peel-and-stick WRB directly on top of the sheathing. On top of that will be a certain thickness of rigid foam. Then, instead of a layer of roofing paper or the need for another sheathing layer, since we plan on installing a metal roof, I would think I can simply install furring strips which are screwed through the rigid foam and sheathing and attach the roof to those furring strips. Am I thinking about that correctly? I'm assuming the only reason Mr. Lstiburek's system utilized the second layer of decking and roofing paper is because of the asphalt shingles?
Thank you again for your time, it is much appreciated!
-Matthew