Compressing R-11 unfaced fiberglass to ONE inch?

Is it possible? The available charts, for R value of compressed fiberglass, do not show 1” as a possibility. They show 3/4” as a possibility for R8, but everywhere I look R8 is so expensive. R11 is an excellent deal instead.
Has anyone tried before? (This would be in a floor, where I might end up with a remaining cavity, under the subfloor, of 1”. Disclaimer: I might end up adopting a different approach, and be left with no cavity after all; yet, it’d be nice to know whether compressing unfaced r11 fiberglass to one inch is a possibility.)
By the way, I’m not very much looking for the additional R5 value (though, at $.42/sq ft, why not?), but for the sound proofing it would provide, and just the very thought that a full (indeed quite packed) cavity under the subfloor is still better than an empty cavity.
Thanks!
GBA Detail Library
A collection of one thousand construction details organized by climate and house part
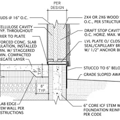
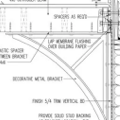
Replies
This is not my area of expertise, but it's my understanding that compressing fiberglass insulation reduces its sound dampening ability.
Thanks! I’ll look into that. My main problem is whether compressing an R11, designed for 3.5”, to just 1” is even possible (or does the fiberglass resist such compression?). The R value might end up being around 5.5. I don’t know about noise reduction.
Maybe at the origin of my question is my surprise that R8 fiberglass be so expensive. It’s really sold for very small projects, and is totally overpriced.
Maybe a better question is what's the best way to soundproof a 1" cavity?
Thanks, DC_Contrarian! That’s a good point. What would you do with a 1” gap under the subfloor? (I guess a related question is whether one should bother?)
By the way, this is the same floor you and I have been discussing. Depending on the approach I ho for, I might end io with a 1” cavity or not.
I think you could probably compress an R11 batt to 1" thick, but I think it wouldn't be the easiest thing to do as part of a construction project.
If your primary goal is soundproofing, there are things that would be more helpful in that regard. A layer or two of homasote above the subfloor and below the finished floor will help. A decoupled drywall ceiling under the joists will also help (use hat channel and one or two layers of 5/8" drywall).
What else is in this assembly that only leaves a 1" gap?
Bill
Thanks, Bill! From your suggestions and comments, I realize that this might be one of those cases where no option is really worth pursuing - maybe, the R11 fiberglass can be split, and then compressed...
I am glad to learn about Homasote, for example, as I didn't know anything about that.
This might end up being just a small cavity on top of rigid foam insulation, which will fill a floor framed above an existing concrete floor (of a porch I am turning into a room). I was thinking that filling up even that last 1" might make for a quieter floor, yet for the sake of the room itself; that is, I don't need to worry about mitigate sounds for some other floor under the new room. This is just a first floor porch, with concrete and then soil under it, being turned to a room.
Usually sound isolation for a floor is to keep occupents of the lower level hearing stuff going on on the upper level. There are two kinds of sound you have to deal with in these situations: regular sounds, such as talking and music, which is carried through the air in the upper level room, and the other is conducted sound, which typically means people walking around (their feet stepping on the floor). It's more difficult to deal with that conducted sound of footfalls. Homasote will help, but the best way to go is to decouple the lower level ceiling using hat channel, and ideally hanging a double layer of drywall too. Minerall wool between the joists will help a bit with talking and music, but won't do much about footfalls.
Since you're building over a concrete slab, presumably with earth below it, why do you want to soundproof that floor? Unless there is someone below it to hear stuff, soundproofing that floor isn't really helpful. If you're trying to quiet down the floor itself (i.e. avoid loud footfalls or provide a bit of softness to the floor itself), the homasote board is all you really need, or one of the foam-style underlayments (Cali Bamboo's Cali Complete product is one example of this type of underlayment).
Note that the rigid foam will also provide a little bit of give, so if you have, for example, a 1/2" layer of XPS on top of the slab below the finished floor, you don't really need any homasote or fancy underlayment -- the XPS layer alone is enough.
Sound proofing can be very detailed, and what you need depends on what you are trying to accomplish. Most people are trying to keep people in one room or level from hearing what is going on in another room or level, so that's my default way of thinking when these kinds of questions come up.
Bill
Thanks, Bill! You got that right, I was just trying to "quiet down the floor itself." I wonder whether the effect of the rigid foam -- of which there will be plenty, that is, approximately 6" -- will be reduced by the existence of a 1" air gap between the foam and the subfloor? If having that gap filled with something makes a difference, then I'll do that, maybe with a 1" layer of foam, or maybe with some fluffy insulation compressed.
Why even have a gap? You could install a T+G or clicklock floor on some plywood directly over the foam -- you don't really need any framing in there.
Bill
@Bill_Wichers, thanks! Indeed, the possibility of just building the 8.5" or so floor, over the existing floor, just with foam (and rim joists all around, forming a box of sorts in other words), suggested by others (DC_Contrarian especially) is one I am very interested in. It turns out that, much unfortunately, doing so would depart considerably from the building permit I received from the township, and I am hoping to avoid submitting a change in plans with them. I know that floors that are just built up, over existing floors, this way has become quite customary, at least among members of GBA. Yet, how customary is going to be perceived by the township's inspector? (Their normal way of proceeding is: Call us when the framing is done, then you install your insulation; in my case, if I have no joists, the floor will be made of insulation...)
One related note, in this JLC article (https://www.jlconline.com/how-to/insulation/insulating-a-sunroom-floor_o), Steve Baczek shows a way of building up a floor with foam, but the height is not 7" (8.5" with subfloor and flooring), as in my case, and he still uses sleepers against the concrete floor (something that would be hard for me to do, given the height, unless my "sleepers" are actual joists of sorts, that is, boards on the edge, whether those sit on foam, and are connected directly to the subfloor, or sit on the concrete, and have rigid foam above them, that is, under the subfloor). That's also why I am hesitant on doing everything with foam alone (plus maybe sleepers to correct a slight slope): In some way or other, I'll need to have my subfloor properly fastened to the concrete floor, or to sleepers, or to joists within reasonable reach for the screws. Where do you think I am confused (as I might still be)?
Do you need to raise it 8.5" to meet an adjoining floor?
Yes. There are approx 7” between the existing floor and the subfloor I want to make the new floor’s subfloor flush with.
OK, here's what you do:
A 2x8 is 7.25" thick. According to my joist span table, #1 Douglas fir can span 14'5" when the joists are spaced every 12 inches. In an earlier post you said the room was 14'6", so at one end you have to add a rim joist to reduce the span by 1.5". With 12" spacing it's no problem to use 1/2" plywood for the subfloor, that will give you a nice solid floor that's 7-3/4" thick, 3/4" for the finished floor and you're at 8.5". Then the question is how to insulate it, I'm thinking the easiest thing may be pouring in loose insulation but I need to think about it, particularly how moisture is going to be controlled. It may be worth starting a thread, "How to insulate a framed floor over a concrete slab."
But this is the right way to do it and you never regret doing things right.
Do check what joist table your locality is using, your contractor will know.
Thanks DC_Contrarian! I’ll check on the joist table for my township.
However, I’d like to modify the modify the “traditional” way of doing it in some way that would mitigate thermal bridging between the concrete/tiled floor and the new floor above. That’s why I have been entertaining the plan of having one or two layers of rigid foam against the existing floor, and the joists sitting on them (that will require some shimming, unfortunately, because of the slope, though that might turn up being way less pronounced than I thought). And that had opened up the possibility of maybe not framing the new floor at all, and just build up with foam. All things considered, at the moment, the assembly I tend to favor would be: 1.5” of XPS (which I have), 2x6 joists, subfloor, flooring. Is they an acceptable variation on your proposal?
Two points:
First, there's not going to be much thermal bridging going on. If that concrete slab is resting on the ground it's not going to get very cold, especially since it's so big. The joists aren't touching the concrete, and with poured insulation there will be insulation between the bottom of the joist and the slab. The joists are probably about R-7, an average of 3/4" of loose fill is probably another R-3, that's R-10, which is probably adequate for slab-on-grade anyway. If you wanted to you could slide foam under the joists -- or spray a layer of spray foam. That may be a good idea for moisture control anyway, I'm still mulling that.
Second, you just can't use foam as a structural component. It's not prescribed in the code. Joists can rest on wood or joist hangers. Foam doesn't have nearly the crush strength. Wood is pretty much the weakest thing that a joist can bear on, and it has a crush strength of about 2,000 PSI.
@SC_Contrarian, thanks! From what you’re saying:
- the 2x8 joists would be held by the joists hangers, but NOT rest on the concerete/tiled floor? That would be quite congenial, actually, especially if it were to turn out that there is a substantial slope.
- if as you explain foam is not structural, how can the option (which we discussed in the other thread) of a fully floating or almost fully floating floor be viable? Is the issue that of the concentrated loads? If so, between the framing with 2x8 joists and, instead, the option of abandoning the idea of framing members supporting the floor you suggested earlier, which one would you favor?
Thanks again!
You get into the issue of 'bearing surface' with foam. If, for example, you had to rest just the end of a joist on something, you are typically required to have a minimum of 1.5" of bearing surface, which is the area of the edge of the joists that is supported, to handle loads. Often you need more than that. Let's say you have 30 pounds per square foot of live load on that 14' 5" joist (which I'm going to round up to 14' 6" here to make things easy), and those are on 12" centers. That means that each joist is carrying 14.5 square feet, or 435 pounds of live load (I'm neglecting dead load here). Each end carries half of that total load, so each 1.5" square bearing surface is supporting about 217 pounds, which works out to about 97 pounds per square inch.
That's the problem -- beefy XPS is rated to 25 PSI, so waaay less than what you need here. That's an issue for regular structure, but for distributed loads, the loading is much less. For a DISTRIBUTED load, the 435 pounds is carried by the entire edge of the joist, which is 1.5" wide and 14' 6" long, which is 261 square inches. now that same 435 pounds works out to about 1.7 PSI, which can be easily supported even by 10 PSI rated XPS. Note that I'm talking about XPS here, but denser EPS with compression load ratings is also useable. In this distributed load case, the use of foam would be acceptable. You could use horizontal 2x4s under the edges of the joists to spread the load out even more, for even lower PSI loads on the foam.
I think it's probably worth a design change on your permit here, but call and ask first. The city might think this is a pretty simple change that won't be an issue. If they think it will be a big issue, then consider framing the floor out as a regular structure.
Bill
Bill, thank you very much! Indeed, this is very clear, and sounds like hood advice — including the advice of asking the township, and see what their response is.
Yes, I'm suggesting that the joists be held by joist hangers. No bearing on the concrete floor.
In the floating floor version, the floating assembly was treated like it was the flooring material. A concrete slab is sufficient support for flooring material, I'm not aware of any restriction on how thick flooring material can be. That said if you need to go 8.5" thick that's thicker than I'd be comfortable floating.
To get that thickness, I think the only viable option is joists or joist-like members. What I mean by "joist-like" is pieces of 2x lumber that are cut so the bottom follows the floor and the top is level. I call them joist-like because they're bearing on the concrete slab and thus not joists. I think you said your room is 32' wide, with joists on 12" centers that's 32 joists, with joist-like you could put them on 16" center and use only 20. With a 2x8x16 costing about $20 these days that's a saving of $240. On the other hand there's labor involved with ripping. Plus you'd have to put something under the pieces to get them up to height once they're ripped. This is where you could use your foam, as Bill pointed out if the lumber is supported for its entire length the foam has enough bearing strength. Cover the entire floor with 2" of foam, rip the pieces so the tops lie level at 7" above the original foam and you're all set. That much foam is probably sufficient for insulation but you could easily pour loose insulation in to fill the cavities if you felt like it. You could also go with 3" of foam and rip 2x6's and save a few bucks on lumber (but spend more on foam).
This assembly is not what's on your permit, you'd probably want to get approval before doing all the work. This would be something to discuss with your contractor, he probably has an idea of what will fly with the inspector.
Thanks DC_Contrarian! I’ll study this carefully, sketch it on paper, discuss it with the contractor, refine the sketch if need be, and talk to the township.
I owe so much to you and others on this discussion — thanks!
Deleted