Compromise Solution for Insulation of Attic with Kneewall

I have a 1941 1.5 story house in Seattle (climate zone 4C) with the top half-story sitting between knee-walls creating three attic spaces. I set out to remodel the kitchen on the main floor, which sits partially below one of these side attic spaces and in the process opened up access to it and removed the existing insulation from the exposed section. I’m now trying to figure out how best to reinsulate the space. From my reading here, fine homebuilding, building science, etc. I’m pretty convinced that the current insulation and venting was done “wrong”. Similarly, the work plans I’ve gotten from insulation contractors seem to be wrong. I’d like to not do further things wrong, but I’m not currently in a position where I can really rip off my roof or redo *all* of the attic insulation, so I’m trying to come up with the best solution that doesn’t require doing that, but also hopefully moves things in the right direction.
To make things a bit more complicated, the rooms between the kneewalls also have closets that extend further into the attic followed by another kneewall. I’ve attached some diagrams of the main floor, top half-floor, and roof side-view that hopefully help explain things.
The kneewalls and rafters are 2×4. Prior to my intervention, the kneewalls were insulated with faced batts of what looks like mineral wool. There was rigid foam blocking in the joist cavities below the kneewall. The lower attic spaces were filled with blown cellulose. Based on exploration with an endoscope, the top attic space also has mineral wool batts. On the south side of the roof only, there are smartvent (brand) baffles at the drip edge. A ~2” strip of the roof deck was cut out to expose the baffles on the other side (picture attached), but as far as I can tell, only the sides of the baffles were exposed, not the actual openings at the ends (?!). There are 4 box vents slightly up the slope of the roof in the lower attic spaces behind the shorter kneewalls. There is a continuous ridge vent, but there are no visible baffles connecting the lower attic spaces to the upper one. The gap between the roof and the ceiling of the half-floor rooms is filled with the same mineral wool batts. There are solar panels on the south face of the roof. There is no hvac ducting in the attic. There will soon be a range hood exhaust duct running through there, but I will properly seal and insulate it. There is also a sewer vent pipe for the main floor bathroom running up through the SW section of the attic, which is not currently insulated.
I happen to know the history of the home and know that the roof was installed 12 years ago, including the smart vents and the ridge vent, the blocking under the kneewalls and the blown cellulose insulation were added 6 years ago and the insulation people, concluding there was no attic venting, added the box vents. The solar panels were installed shortly afterwards.
So with all that background out of the way, let’s get to the actual problem (though I suspect readers of this forum will have already spotted a few). Based on what I’ve read, if I were replacing the roof or building I would move the edge of the thermal envelope to the roof line and add external polyiso rigid foam insulation above the roof deck. But I can’t really afford to do that right now. As far as I can tell, I don’t currently have any real venting in the attic, since the drip edge vents don’t actually open up into the space, the box exhaust vents are way too low (and have no intakes) and the path between the ridge vent and the lower attic spaces is blocked by insulation. Also, my kneewall insulation isn’t air sealed (the facing doesn’t seem sufficient). Then again, things seem to have been OK. The half-story gets a bit hot in the summer, but there’s a heat pump mini-split cassette up there and it isn’t unbearable. My total energy bill (all electric) for the last year was around $300, so it’s hard to justify an expensive intervention based on a cost analysis. I think there might be a little bit of organic growth on the rafters, but it isn’t black mold and I think it’s mostly just cellulose fluff. Then again, the idea of putting things back incorrectly (especially paying someone to do it) really grates on me.
The insulation contractors proposed R21 (i.e. oversized) unfaced batt insulation on the knee walls, R49 unfaced batt insulation on the attic floor, and 60” baffles to protect the drip edge vent (that I’m not sure is actually doing anything). They also mentioned adding foam to exterior penetrations (the bid is also for the kitchen walls, so it’s not clear if they’re counting the kneewall junction box in this). This is only for the attic space above the kitchen. The rest would be left alone. It sounds to me like they’ve completely neglected air sealing on the back of the kneewall and above the batts in the attic floor. My understanding is that cellulose is not technically an air barrier, but does block a lot of convection, but unfaced fiberglass batts are going to be awful. Also no mention of blocking in the joist cavities below the kneewall (I removed the old blocking).
Ok so I think these are my basic options other than redoing everything:
1) Properly insulate the attic above the kitchen, leaving the thermal enveloped boundary at the knee wall. I think this would likely mean appropriately sized batt insulation (and I’d prefer mineral wool) on the kneewall covered by rigid foam, rigid foam blocking below the kneewall. Batt insulation in the attic floor joists seems fine, since they’re currently accessible, but would I then need to cover the attic floor with an air barrier? I’m worried in that case about trapping moisture, so perhaps it’s better to do blown cellulose again in the attic (also seems simpler to have the whole attic floor using one type of insulation IMO). I’ve got ICAT-rated recessed light fixtures I’m going to install and I can foam any other attic penetrations in this space. I would need to resolve the attic venting in some fashion. I think the box vents are probably unhelpful and I should instead ensure that the drip edge intake vents are actually working and then somehow get baffling to run all the way up to the upper attic space.
2) Move the thermal envelope boundary of *only the attic space above the kitchen* to the roof deck, putting rigid foam under the rafters and then augmenting it with air and vapor permeable (likely rockwool) insulation to reach the appropriate R-value. I think I’d need to get at least 20 of my r-value from the impermeable layer, but I’d probably go with 4.5” RMax polyiso at R31. Also this requires insulating the gable wall, I guess again with rigid foam plus rockwool, though it’s not clear to me where to put the air and vapor barriers in this case. I guess I would need to add insulation and air sealing between this attic space and the adjacent one on the SW side of the house that is still full of loose cellulose. Rigid foam again? Similarly, I would need to air seal above the kneewall where the mineral wool batts sit directly between the finished ceiling and the roof deck. This option is somewhat appealing because it seems like it moves things in the right direction. It also gives me a bit of additional storage space. If at a later point I’m working on the SW side I can similarly “upgrade” that section. It does seem quite unconventional though. I haven’t seen anything talking about a mixed roof deck/attic floor thermal envelope boundary. This would also require ensuring that the drip-edge vent here is not functioning or providing baffling so air can flow over the rigid foam. Would attaching the rigid foam to the bottom of the 2×4 rafters actually make sense here to leave that cavity for air flow? I’d also need to decommission the box vent. There are no ducts up here, so this leaves the space without real conditioned air. I could add some mechanism for exchanging air with the adjacent room, but actually running a duct up there from the air handler would be basically impossible.
3) Similar to (2), but for the whole S side of the attic. I still have better access to the SW side now than I will when I close up the attic, and I could probably vacuum out the remaining cellulose and get some decent-sized pieces of rigid foam up there. This is more work, but perhaps having a whole side of the attic in the thermal envelope is less weird than only having one corner.
Just let the insulation contractors do whatever and then redo everything with roof-deck exterior insulation when the roof needs replacing in a decade.
None of this really resolves the lack of venting in the lower north attic, but perhaps that’s a fight for another day.
I’d really appreciate any advice here. Part of me wishes I’d just never looked into how to do this properly so I could remain blissfully ignorant…
I’ve read a bunch of articles and posts on this subject, but not linking them because apparently links cause the post to get stuck in moderation.
GBA Detail Library
A collection of one thousand construction details organized by climate and house part
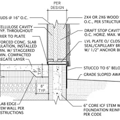
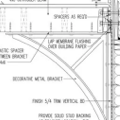
Replies
Following up here, mostly for posterity since it seems no one wanted to engage with my wall of text :-D
I decided upon further reading that the insulation contractor's plan indeed wasn't so great. The company who originally did the roof came by and confirmed that the smartvent is installed as intended and actually pointed out that there is a bit of a gap in there for the intake and the box vents are doing ok as an exhaust. I'm still not totally convinced, but absent some empirical evidence I'm just going to go with it. They did agree that the ridge vent with no intakes didn't make any sense and are going to install a couple of intakes at the bottom of the upper attic cavity. I think not the perfect solution, but hopefully good enough for another decade and the price was right.
I got another insulation contractor to come by, but they proposed a nearly identical plan to the first and also confirmed my suspicion that the air sealing they're going to do is basically just the code minimum fire blocking.
So I think I'm doing the insulation myself and go with option 1, more or less. My plan is to install R15 rockwool on the kneewalls with 3" RMax sealed behind it. For the attic floor, I'm going to toss in all my leftover batt insulation from insulating the walls and then blow cellulose on top of it. I'm blowing cellulose into the kitchen floor cavity to help a bit with airborne noise, so I'll already have the machine and such and it's about the same price extra to buy an amount of cellulose that comes with a "free" blower rental as it is to rent the machine for the day. For the same reason, I think I'm just going to keep blowing to 20" (was previously the absurdly precise code-minimum 14.82") and also add any extra to the other attic spaces. When I replace my roof in hopefully more than 10 years, I'll move the thermal envelope up there and turn the attic into a conditioned space.
I will start by saying I hate half story building, spray foam and conditioned attics!
If you have made the choice to buy an OLD half story building your only real hope of stopping the wind from blowing all the heat out of your house is tons of spray foam applied to the roofline. A trifecta of hate.
Walta