Cz-3 comparison of 1/2″ closed cell + r13 batt vs 3″ open cell

Inquiring around, it seems the most popular insulation option offered in my area (Memphis, TN cz3) is 1/2″ closed cell foam plus r13 fiberglass batt for 2×4 walls. I don’t much like batts because they always seem pinched in the wall around pipes and wires, etc. I have heard fiberglass performs better with some compression, though? I was told it was worth about r15 in this configuration for about $1.60 a square foot.
GBA Detail Library
A collection of one thousand construction details organized by climate and house part
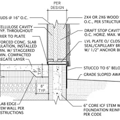
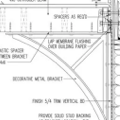
Replies
Compressing fiberglass batts gets you more R per inch, but less overall R value. What this means is that if you "squish" an R13 fiberglass batt by 1/2", you might go from R3.7 per inch (at full depth) to R4 per inch when "squished", but this is now getting you only R12 total, since it's not thick overall. You will NEVER get more than rated R value from a batt by squishing it. 1/2" of closed cell spray foam (ccSPF) is around R2.5-R3 or so, so the ASSEMBLY of that plus the compressed batt will likely get you up around R15 or so TOTAL.
Open cell spray foam (ocSPF) with a full fill will probably get you around R13 or so with a full fill, which means overfilled and trimmed flush with the edge of the studs. This will probably actually outperform the closed cell + compressed batt though, because no one is going to get a perfectly even later of ccSPF, they're going to have thick and thin spots, and it doesn't average out mathematically. That fiberglass batt isn't going to be perfectly installed, either, so the ocSPF assembly and the ccSPF+batt assembly are likely to actually perform about the same in practice. If you really want to use spray foam, I'd go with the cheaper of the two options.
Personally, I would skip the spray foam step altogether. You don't need to apply spray foam to the back of sheathing to "air seal" the sheathing -- the plywood is already an air barrier. You only need to seal seams and gaps to air seal, not the entire surface of anything. My recommendation would be to skip the spray foam completely, and air seal the "old fashioned way", with caulk and canned foam. Use mineral wool batts in the walls if you want good R per inch, since mineral wool batts in 2x4 walls will give you R15, and it's easier to install them well compared to fiberglass batts. For the attic, air seal the same way, with caulk and canned foam, then blow in at least code minimum amounts of cellulose (which may be R49 in your area now, check current codes).
I've never liked the push to use spray foam as an "upgrade" for air sealing, because it adds a lot of unnecassary costs. Air sealing with caulk and canned foam is much cheaper, and performs just as well if done with some care.
Bill
Thank you for your thoughtful reply. I will investigate mineral wool some more. I asked about it and I actually got a price for it, but everybody acts like it's a weird request. I like the idea of leveraging what is already there.
I have mixed feelings about foam because isn't it rather flammable and toxic? I understand mineral wool is very safe and not flammable.
Mineral wool is basically spun rock fibers, it won't even melt until several thousand degrees. Mineral wool is pretty fire proof, and is even used as a fire blocking material commercially.
Foam can burn, but usually includes some fire retardants to limit that. If it does burn, yes, you do get toxic fumes, but I consider that a bit moot, since if your house is on fire, all kinds of things will emit toxic fumes while burning (wire insulation, plastic plumbing pipes, upholstered furniture, etc.). If you want some extra fire protection, step up to 5/8" drywall instead of the usual 1/2" stuff use in residential structures. 5/8" drywall is the commercial building, is specced for all kinds of fire rated assemblies, and will give you a much more solid feeling and quiet wall assembly. I only use 5/8" myself, with a few rare exceptions (usually difficult to access spaces).
I'm surprised people would think mineral wool is "wierd" -- it's even stocked in all the box stores. It's an excellent product, and very easy to work with. It installs pretty much the same as fiberglass, but tends to fit better since it isn't as compressible. You do usually need a vapor retarder with it if you're not using exterior rigid foam though.
Bill
Our market is a bit unimaginative, it seems.
I read that osb is 2 perms at 50% rh and 12 at 85%. I am considering applying zip tape along the seams under the tyvek. Is beyond that important? I am largely trying to use what I have within the budgets I already have right now.