Can’t cool living space: AC ducts in unconditioned attic

I’m looking for some advice for a solution to a problem I have struggled with for awhile now.
I live in a 2 story home and our main living area in on the top floor of the house. Our garage and fully finished daylight basement is on the lower level. On our main level (2nd story), the house has always been difficult to cool below 76 degrees during a hot summer afternoon and often will not cool down to our desired 72 degrees until 10pm or so at night after the attic has cooled off. We just had a new evaporator put in our AC unit which is the largest residential unit available. We have 12 foot ceilings, and several can non IC rated can lights (which I know is an issue). Our attic has varying levels of insulation and the weak spots are under the attic floorboard which has been nailed down making it difficult to remove. I was able to remove some areas and discovered R-19. Living in AL, I realize this is not enough. However, other areas are a good R30 or so. I have 2 PAV’s which run constantly with my AC ALL day which I keep on 75 degrees during the day. The HVAC is in the attic so moving it is not an option, however, should I disconnect my PAV’s, seal the areas I can access and add more blown insulation or should I spray foam the rafters? Ironically the prices i’ve been quoted are close and the spray foam option was only $2k more for a conditioned attic. The companies that quoted sealing my top plates, etc would not remove the floorboards, so I’m thinking that would be a waste of money since there is very little insulation under those. Another option I thought of would be to lay batts of insulation over the attic floor in addition to adding more blown in the uncovered areas. Would that help? I’m cautous over spray foam as I’ve heard about the health hazards and installation nightmares that leave “fishy” odors in the house….any advice appreciated!
GBA Detail Library
A collection of one thousand construction details organized by climate and house part
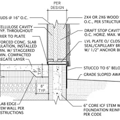
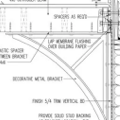
Replies
If moving the HVAC is not an option, then you probably need to convert your attic into conditioned space. Keep in mind that your insulation R-values are only part of the equation and that air sealing is likely a bigger issue, including around those can lights that need to be isolated from your insulation asap. Here's an article to read about how to make sure your do this conversion properly: https://www.greenbuildingadvisor.com/article/creating-a-conditioned-attic
You'll notice at the end of the article that on occasion it is more cost-effective to abandon your existing duct work for a new system, perhaps a few minisplits, than making the attic conversion. If your current ceiling is not well air-sealed and insulated however, that work would still need to be done.
Another thing to look at are the ducts themselves. Are they properly sealed? If not you can be loosing a lot of cooling power, and energy and money, there. This article may be helpful to make sure that work was done or if not, to make sure you get it done right: https://www.greenbuildingadvisor.com/article/sealing-ducts-whats-better-tape-or-mastic
Great Info, Thanks for sharing !!
A comment on style: A bit of white space between paragraphs makes it a lot easier to read.
>"I have 2 PAV’s which run constantly with my AC ALL day which I keep on 75 degrees during the day. "
Powered Attic Ventilators (PAV?) usually make the problem worse by depressurizing the attic, sucking conditioned air up through all the leaks in ceilings below, and may be the entire reason why the system can't keep up. With leaky can lights and other large leaks in the attic floor even stack-effect can create infiltration drive, but powered attic vents can amplify that by orders of magnitude. Turn them off now, and never turn them on again. The attic will get hotter, but since you don't live up there who cares? Without the ventilator-driven infiltration the system may be able to keep up with the upper floor load.
If that alone doesn't quite do it...
Whenever an oversized cooling system isn't keeping up with the sensible load it's worth assessing the duct design and implementation first, to see that the supplies and returns are properly balanced, and that the ducts and air handlers aren't leaking. An unbalanced or leaking duct system on a not-so-tight house can deliver a high parasitic infiltration load whenever the air handler is running, pressurizing some rooms, depressurizing others.
Both the ducts AND the attic ceiling plane have to be meticulously air sealed even if the duct design is adequate.
Of course converting the attic to a sealed conditioned space mitigates against those issues, but doesn't prevent air handler driven infiltration. For a duct system to pass Energy Star certification the room to room pressure differences may not exceed 3 pascals (= 0.012" water column) under all operating speeds, and with the interior doors open or closed. If there are doored off rooms with no return registers it may be necessary to make return paths. Using partition wall stud bays as "jump ducts" to common areas can work, providing more sound & light privacy than opening up the space at door thresholds, etc.
If the duct design checks out and the upper floor ceiling is as tight as you can make it, and it's been brought up to R38 it should be fine. Failing that, for relatively low money as a DIY, painting the roof deck with a silvery "radiant barrier paint" and installing PERFORATED aluminized fabric type radiant barrier on the underside of the rafters will lower the peak temperature of the attic by at least 10F and the direct parasitic load on the ducts & air handler would drop.
How many tons of compressor?
What size evaporator coil?
What is the floor area of the attic?
What is the total floor area of conditioned space served by that AC system?
Here's the unit I have from 2010
XC21-060-230, Air Conditioning Condensing Unit, 16.5 SEER, 5 Ton, 2 Stage, R-410A, DLSC Series
the new coil is american standard, not sure on the size, but it's cooling much better than before when the previous one was leaking coolant.
The attic Floor area is about 300 to 350sq feet.
The conditioned space of the living space with this unit is approx 2200 sq feet.
there are 2 return vents in the hallway, but no supply vents, and that area of the house stays a bit warmer than the rest of the rooms.
Thanks!
>" ...5 Ton, 2 Stage..."
------
>"The conditioned space of the living space with this unit is approx 2200 sq feet."
That's a ratio of a ton per 440'. Figure at most a ton of that is due to the parasitic loads of the ducts & air handler being in the hot attic, leaving 4 tons for cooling the house, which would be a ton per 550'. Most houses that size have a load to floor area ratio of about a ton per 1300'. Ponder this graphic for awhile:
https://www.energyvanguard.com/sites/default/files/styles/panopoly_image_original/public/square-feet-per-ton-air-conditioner-sizing.png?itok=vsJxOobH
>"there are 2 return vents in the hallway, but no supply vents"
So how does the air get from doored-off rooms into the hall?
What is likely happening is that the flow is restricted, pressurizing the rooms with the supply ducts, decompressing the hall with the common returns. Even without the attic fans running the pressure is driving air from the rooms through all the leaks in the ceiling into the attic and out, and pulling air into the hallway space by whatever paths it can find. With the attic fans running it moves even more air from the conditioned space up to the attic. Using "the great outdoors" as part of the return path increases the total load substantially, and restricting flow through the rooms with the supply ducts reduces the cooling capacity received.
This can be substantially mitigated by leaving all the doors open during the day, but eventually it would be good to build some appropriately sized return paths from each room into the hall space. Rooms that share a partition wall with the hall space can utilize stud bays in the partition walls as ducts, with a grille near the ceiling on the room side of the partition, and another on the hallway side of the same stud bay. If the cross sectional area of the grilles is at least as big as the ~50 square inches of a single stud bay and the supply registers aren't any bigger than that the pressure difference should stay pretty small. In extreme cases it may require using two stud bays.
A door cut that size would be big enough to toss a small cat through, but if the door is really the only reasonable place to make a jump duct, the retrofit solution reviewed in this bit o' bloggery is better than nothing:
https://www.greenbuildingadvisor.com/article/an-easy-retrofit-for-return-air
A low-impedance air return path like a jump duct reduces the air handler induced pressure differentials, while providing reasonable light & sound privacy. It may not hit the 3 pascals max to hit Energy Star levels, but you're probably looking at something like 15 pascals (0.06" water column) with the doors closed right now. (With a $100 two port manometer of the type used for measuring static pressure drops on duct systems you can probably verify that. Most only have 0.01" resolution, so it won't be super precise, but anything over 0.01" pretty much fails Energy Star, and 0.03" fails Energy Star by more than 2x.)
Try disconnecting your attic fans. Or reversing 1/2 of them so you aren't depressurizing the attic.
A blower door test + air sealing (including ducts) will help. After that, a Manual J will provide much more information about where the heat is getting in and help with deciding what is cost effective to change.
Jon R, how do you reverse them? I disconnected them per advice from others, but the attic gets up to about 125 or so during the heat of the day now and hardly any air movement.
Thank you all for the advice! I've heard so many varying opinions on the PAV's, so I had them repaired a couple of years ago. All of the HVAC companies said they are a must. Based on your advice I have disconnected them and I will see if that helps some.
The AC seems to struggle late in the day and into the evening when the heat gain has made it's way through the ceiling.
As far as the lack of sufficient insulation and gaps under the attic flooring (it's about 350 sq feet), what's the best way to address that? There are about 8 can lights (non IC) under those boards as well, so several spots where there is no insulation.
should I:
1. Go to the expense and headache of ripping up the floor boards that are nailed down, seal and insulate under? (this will leave limited access to my HVAC Unit in the attic.
2. Bite the bullet and spray foam the rafters creating a conditioned attic? (I have heard many mixed reviews on spray foam, ie. health hazards, voiding termite bonds, etc)
3. Or would sealing all other accessible areas, adding blown insulation, and laying fiberglass batts over the attic floor work? I realize their is an airspace under the boards where i found very old and worn insulation bats from 1990.
thanks again
ryan
Don't insulate without doing all the air sealing work first.
Be sure to seal the duct boots to the ceiling gypsum, often do-able from the conditioned space side with combinations of caulk &/or can-foam, sealing over the caulked gap with housewrap tape. Seal any seams in the duct boots and any accessible ducts with duct mastic, and seal all the seams in the air handler with purpose made foil duct tape. Seal the electrical and refrigerant line penetrations of the air handler with HVAC lineset tape.
If the can-lights are accessible from above, with a large enough cardboard box to provide 3" of clearance (sides and top) it's possible to seal the seams of the box with housewrap tape and seal the box to the ceiling gypsum with can-foam or polyurethane caulk. If they're under the floorboards it may be easier to replace the fixture from below with an air-tight insulation contact version and seal it to the ceiling gypsum with can foam, or cut just the section of floor board above the light fixtures to use the cardboard box technique, or replace with a air tight insulation contact version from above.
Find and air seal all plumbing stack, electrical, and flue penetrations of into the attic too.
When you've fixed all the obvious leaks you may be able to find more with a large window fan blowing out of an upstairs room depressurizing it and, using an infra red camera to spot where the hot attic air is coming in, or going up in the attic with a smoke pencil to see where the air is flowing in.
Have you verified the return paths for all rooms with supply registers yet? This is important, and usually not very difficult to fix.
All of those measures are worth doing, even if the roof deck is eventually going to be insulated.
With the attic floor and ducts air sealed it's fine to go ahead and install ~6" or more of blown cellulose insulation over what's already there, including blowing on top of the floor-boards, which should be adequate for bringing it all up to IRC code minimum performance for US climate zones 2 & 3 (= all of AL). As a DIY with a rental blower that would cost $150-300 (depending on whether you get a "free" day of blower rental with only 250-300lbs of cellulose). A pro would have to charge you about twice that just for tying up the equipment & crew for the afternoon (varies with local market).
Even with R38+ on the attic floor there may still be value in reducing the heat flux from the roof deck whenever the ducts and air handler are in the attic. A 500 square foot roll (48" x 125') of perforated aluminized fabric radiant barrier is less than $75 at box stores, and will reduce the peak attic temperatures. As a DIY this will usually be cost effective whenever the ducts and air handler are in the attic. If the plan is to insulate at the attic floor with blown insulation, installing the radiant barrier prior to blowing the insulation saves time and effort that would otherwise have to be put to installing chutes to keep the insulation from contacting the roof deck.
Silvery radiant barrier paints run about $75/gallon in 1-gallon cans, $250-300 for 5 gallon buckets. A couple gallons would cover the roof deck. On it's own the silvery paint isn't as effective as aluminized fabric type RB, but it would measurably enhance the performance of radiant barrier on the rafter edges. If it's an either/or situation, raising the R value of the attic floor to R38+ has a higher value and better return than enhancing the radiant barrier with low-E paint.
Or...
The more expensive is to insulate at the roof deck. A 2" shot of closed cell foam on 500 square feet of roof deck runs about a grand in my area if using climate damaging HFC blown goods (R12-ish), or about $1300 if using far more benign HFO blown goods (R14-ish). Depending on the pitch of the roof deck you may have less than 500' of coverage to deal with.
With 2 x 10 rafters that would sufficient room for R30 rock wool under the rafters, held in place with perforated (and ONLY perforated type) radiant barrier for a total of R42-R44. With 2 x 8 rafters there would be enough room for R23 rockwool, for R35-R37 total. If they are only 2x6 rafters there would still be enough room for R15 fiberglass or rockwool, yielding R27-R29, which is still way better than the leaky low-R attic floor. The insulation on the attic floor can remain in place except where it would have to be moved. At box store pricing R30 would run about $650 or more depending on the pitch of the roof deck.
Thank You Dana. I really like your idea of insulating the roof deck with Rock Wool (although, I've heard in a carcinogen??). Lowering the attic temp would be idea, so I will look into that. I'm cautious on spray foam as I still feel the jury is out. All of the contractors around here want to use open cell, which I've heard can cause all kinds of issues with a roof deck.
Adding a bunch of additional inches of blown-in cellulose attic insulation to an unfinished attic is one of the single easiest energy efficiency projects a homeowner can do (much easier than doing blown-in walls or replacing windows). The only proviso is that you have to buy the all-borate variety of cellulose - for some unclear reason they sell other varieties that smell of urine.
You'd have to work around your HVAC, which would complicate things, and at least a few of the floorboards will need to be removed temporarily (or permanently if you decide to make the insulation taller than the floorboards), but still...
A 5 ton AC unit for a moderate-sized home is extreme to the point that it can not just burn extra energy due to short-cycling, but also make cooling the house *less effective*. Different parts of the system need to be tuned to work together. You may want to look at more in-depth work with tuning the system and your home than we can assist with absent some in-person instrumentation. Particularly pay attention to your overall ventilation strategy, and to how leaky particular ducts are.
Check out https://www.youtube.com/watch?v=sKO3fO3SH_I for an illustration of a house with oversized AC that's not cutting it because of all the air leakage.
Keep in mind that insulated areas average out their heat transfer by what's called a harmonic mean. For a wall composed of 1 square meter of Assembly A and 1 square meter of Assembly B, the overall assembly AB will have a combined R-value of 2/((1/Ra)+(1/Rb)). The numbers for equal-sized panels are the same as just taking the mean R-value. The numbers for one panel being much larger than the other, though, is very different than an area-weighted-simple-mean. That means that a small weak spot in a well-insulated wall/ceiling passes a disproportionately large amount of heat.
Deleted
Thanks for the info. Yes, it appears that this unit is over sized, and perhaps the ductwork is not sized properly either. The entire house is 3400 sq feet, and the area that this 5 ton unit cools is prob 2400 sq feet or so. However, there is not any short cycling, it's all very long cycling until later in the evening when the attic is cool. The cost to run this unit seems a bit high as well.
Just because it's not short cycling doesn't mean it's right-sized. Measure the duty cycle.
It's likely that a ton or more of the AC load is related to air handler driven infiltration and the ducts & air handler being located in the attic.
The duct sizing relative to the air handler can checked out by measuring the static pressure drops with a dual-port manometer. If some or all of it is flex duct that's flopped all over like a ball of mating snakes it's worth re-commissioning them stretching them fairly tight and straight to reduce the static pressure drops.
My guesstimate is that low-E paint might result in a 2F drop in your summer afternoon 2nd story temperature.
Thanks, Jon R, I'll stay away from the paint.
Why stay away from the paint?
A 2F drop is fully half the way from the current 76F and the targeted 72F indoor temperature.
If it's an either/or situation, a full radiant barrier +/or more fluff on the attic floor is better than the low-E paint + fluff or low-E paint + RB, but it's still a pretty cheap upgrade when done as a DIY.
But all the radiant barrier & insulation work is secondary to air sealing the ceiling plane, decommissioning the active attic venting, and getting serious about recommissioning the ducts by sealing & balancing them, and MEASURING the pressure differentials.
Dana - I mis-read Jon R's comment, I thought he was saying that the paint would only drop the attic temps by 2F. Yes, I agree it would be worth it for an interior drop of 2F. I've been doing the air and duct sealing and I'm already noticing a difference.
You're doing it in the right order- air sealing, duct sealing, and duct balancing/ jump ducts to mitigate against closed-door back pressures limiting flow fall under the heading "Commissioning the duct system".
Improving the R-values comes next, followed by radiant barrier &/or low-E paint if needed.