Choosing a Ducted Air Source Heat Pump

Hi All
Looking for a sanity check on pursuing ducted ASHPs as the sole heat source for an on-going renovation of a 1915 home south of Boston (climate zone 5A). The home was previously heated with an oil boiler & HW radiators. We originally intended to install ducted ccASHPs with the intent of pursuing MassSave rebates, and just received the Manual J calcs from the HVAC contractor’s 3rd party consultant with a higher heat load than anticipated.
The home is 2-story 2,400 sf, with unconditioned and uninsulated basement with ~2′ thick fieldstone walls and vented attic with R-30 cellulose over the existing plaster ceiling. Exterior walls are rough sawn 2×4 with 3/4″ plank sheathing with old house wrap and cedar shake cladding. Exterior windows are being replaced with Jeld-Wen W-2500. Wall cavities are open for removal of old knob & tube and the intent is to insulate all exterior walls with R-15 batt. Existing plaster ceilings will remain throughout. We’re not interested in ductless, and given the constraints we’re working with, the only opportunity to locate air handlers & ductwork is in unconditioned space (in basement serving 1st Fl and in attic serving 2nd Fl).
The Manual J shows the entire house with a 5.5 ton heating load & 2.5-ton cooling load. Broken down by floor, the Manual J shows 1st Fl with a 3.2-ton heating load & 1.5 ton cooling load, and 2nd Fl with a 2.3-ton heating load & 1-ton cooling load. These loads seem high based on square footage, but it’s admittedly an old leaky home. The Manual J inputs appear to be reasonably accurate but I’d appreciate feedback. The inputs that I’m mainly questioning are the infiltration classification and whether we can improve upon that to reduce the load calcs in a meaningful way.
We’re interested in Mitsubishi units, however MassSave’s Heat Pump Qualified Product List doesn’t include single-zone hyper heat units, so that leaves us with the option of using an MXZ-C unit to serve both air handlers, or foregoing the rebate and using single-zone NAHZ units, or some other alternative altogether.
Based on the calculated loads, the MXZ-C option appears to require an MXZ-8C48NAHZ2 coupled with an SVZ-KP36NA, SVZ-KP24NA, and a branch box. The MXZ-C unit is on the MassSave list, so it appears to be eligible for a whole home rebate and has a better turn-down than the single zone units of equivalent size.
The builder’s HVAC contractor shared the Manual J (attached) but hasn’t otherwise been forthcoming with proposed solutions or feedback.
I’m not sure if I’m overlooking a better option, or issues with the Manual J, and any feedback is appreciated.
GBA Detail Library
A collection of one thousand construction details organized by climate and house part
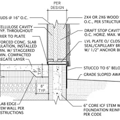
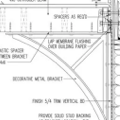
Replies
Often Manual Js fail when it comes to infiltration, which is more or less a total guess without a blower door test. Can you give us a sense of how many annual oil gallons you use? And is that oil heating domestic hot water as well as central heating?
Unfortunately I don't have info on oil consumption because the home was purchased this past year. If I look back through my records I may be able to figure out who previously delivered oil to the home and I can try contacting them to see if they'd be willing to share prior delivery records although that may be a long shot. The old oil boiler did serve domestic HW and heating. Moving forward domestic HW will be via gas fired tankless. If it would be fruitful I'd try to have a blower door test done now, but at this stage of work the exterior walls haven't been insulated or boarded and and windows haven't been replaced, so it doesn't seem like the info would be especially useful.
Based on the above I know this effort entails some guesswork... maybe a lot of guesswork... I'm just trying not to miss the mark entirely and end up with a grossly oversized or undersized system and the consequences that would result.
The oil supplier should be able to tell you if you can track them down, I’m sure they’ll want the chance to get your business. If you look at the pie chart, 45% of the heat loss comes from humidification and infiltration, so it’s a wild guess. Infiltration drives humidification needs (which wouldn’t necessarily even need to be met on design day I think?), so it’s a huge unknown currently. Could you wait a few months and a see how the oil boiler does?
This sounds like a major reno. In this case the most important detail to get right in terms of comfort (and energy efficiency) is air sealing. If you look at your loads, about 1/2 of it is infiltration, duct losses and humidification. If you fix the the air leaks, move the equipment into conditioned space, you half the size of the heat pump you need to carry the place. It would also cost 1/2 as much to run, so it is a pretty quick ROI.
Ideally you can wait till the new windows go in but you can do lot of the air sealing of the house as is. Older houses have a lot of ugly details which make for big air leaks, you can sort these out with the windows as is. What you want is to find a contractor that does blower door directed air sealing and get them into the house before the walls are insulated or drywalled. You want to get the place as tight as possible while everything is nice and accessible.
Looking at the floorplans, you have some interior walls on the main floor, there is no reason not to use these as a duct chase for feeding the 2nd floor. From here most of the ducting can run through the 2nd floor joist space to each room. A couple of small bulkheads here and there and you can get all the ducting inside and out of the attic. Air handler and ducting in the attic is the last thing you want with a big reno like this. HVAC guys like to install air handlers in the attic but don't like to service it there, any money you save on install you'll spend on extra operating cost plus maintaince down the road. Ducting to the basement would also allow you to use a single air handler for the whole house and save some extra cost.
Part of HVAC is ventilation, now is the time to think about how you would get fresh air into the house.
If I’m doing the math right, the manual J is assuming ~330 cfm of infiltration. That seems high? What do you think Akos?
Yes and no. That puts the house at about 20ACH, definitely possible with older balloon framed house with leaky windows. Not likely with a house after an interior reno and new windows. Feels like somebody had their finger on the scale and wanted to come up with 60000BTU heat loss which is suspiciously close to 1 ton/500sqft.
I’d much rather see a blower door test than a manual J at this point.
I’d avoid air handlers in unconditioned space in your climate. A semi-conditioned basement can work with air sealing and rim insulation for ex. With an attic installation you are looking at lower output and efficiency due to losses— in both heating and cooling.
Sounds like you are insulating from inside with walls open? If so I’d opt for dense pack cellulose over batts for the reduction in infiltration.
Be cautious about spec’ing hvac equipment to meet incentive requirements rather than building/human concerns. I’ve seen some unfortunate outcomes when we’ll-intentioned gov. programs skew client decision making.
Thanks all. Air sealing and a blower door may be possible in the short term to better establish infiltration before equipment is finalized, but based on the schedule the decision will need to be made on equipment prior to window replacements. With that in mind, what would the approach be to equipment sizing based on improved infiltration numbers and old leaky windows awaiting replacement?
Akos - There are in fact a couple gable ends with balloon framing. The prior owner had attic air sealing & insulation done via MassSave but I don't know how impactful those efforts were.
Norm - Yes, insulating from inside. I'm with you on spec'ing for incentives vs needs, which is why I mentioned foregoing incentives altogether if that's what it takes to get to the right outcome. I'm just trying to navigate my way to that outcome and appreciate all the feedback so far.
I put all of the same Manual J inputs into BetterBuiltNW to get a back of the napkin idea on how the number *might* be influenced by infiltration reductions alone. The Manual J I received shows a heating load of 66,000 BTU with infiltration @ 0.95 ACH and the BetterBuiltNW calc I produced shows 63,000. As the infiltration ACH reduces from 0.95 to 0.9, 0.8, 0.7 the heating load reduces to 61800, 59100, 56500. All other things being equal, that still seems to imply that the equipment listed in my first post would still likely be the appropriate selection, but based on the feedback so far it seems like I'm misguided in that broad assumption and the back of the napkin changes to the numbers.
Deleted
The infiltration could be anything at this point (.5? .4?) and drives a lot of decisions. It also opens up other design options too! Smaller equipment means smaller ducts, means potentially fewer duct losses, means smaller equipment…
In addition, it can mean a smaller heat pump with backup heat - either resistance or gas. This can allow you to have a better sized AC unit without giving up much on heating. The gas could come in handy if you are short on amps, another constraint. As you tighten and install new windows, the hybrid system can become 100% electric.
In new air tight homes builders will often have a blower door test done before insulation, while the sheeting is still visible from the inside. This allows them to identify any major issues before closing up the walls.
It might be worth talking to a company that does blower door tests locally to find out whether they think they can add value while the walls are open. If they say yes, be cautious and ask for details on how they can identify where the worst air leaks are.
I agree about tracking down the oil supplier to ask about prior oil deliveries. But also, it would be good to know if the boiler is designed for a set amount of BTUs. If it was delivering a max output of 100,000 BTU/hr for heating and hot water, this will also be a guide post.
I also agree to avoid putting the air handler in the attic. If ever the drain for A/C condensate clogs you will have water coming down from above. All other reasons mentioned I also agree with.
We're in the Boston area, and have the MXZ-8C48NAHZ unit with 2 air handlers (30k and 24kbtu). They've been great in general, and have been our primary source of heat for 3 years. Our ducting situation is the same as the OP's, and we used Aeroseal on the basement ducting and our contractor 100% replaced the attic ducting with better insulated runs (and sealed them). They provided a duct leakage report.
We worked with Flemming Lund to do a blower door test and IR scan to identify problem areas--he's great, and it would be well worth his time to get you started. https://www.infrareddiagnostic.com/service/blower-door-testing
We used his report to target areas (including duct/return sealing), and went from 8.72ACH50 to 5.94ACH50.
For reference NC44_, jwasilko's 8.72ACH50 prior to air sealing, is roughly 55% less than the .95 ACH your original manual J used. If you had similar final infiltration to jwasilko's 5.97ACH50, that'd be 70% less than the original manual J.
One of the biggest sources of air infiltration in these old homes is the solid wood plank used for sheathing. The gaps make the walls very leaky. A flash of spray foam can significantly reduce this leakage without costing too much. There aren't many other ways to economically reduce the leakage through the walls. Pay special attention to joist areas - balloon framing has lots of unusual bypasses for cold air to follow. Include blocking at each stud bay and at each floor level. This improves fire safety as well as helping to reduce 3D airflows. You semi-conditioned basement can also be a big source of infiltration, and the stack effect pulls this air up into the house. If you are in a high radon area, the stack effect will pull radon out of the ground and up into the house as well. A couple inches of spray foam on the walls and sill/band joist area along with some sort of air/moisture membrane on the floor will make the basement more pleasant year 'round and will also reduce infiltration substantially. This post sounds like I'm a spray foam junkie, and I'm not. It's just that the weird configuration of air leakage pathways in these old houses makes it hard to seal without spray foam as the primary solution.
I agree fully. There many risks associated with the insulation of spray foam and I avoid it as much as possible but in this case the Flashing of spray foam may be the best strategy for air sealing the envelope/walls.
It would be a bad idea to create a vapour barrier by using too much foam and then putting a poly vapour barrier behind the drywall. You don’t want 2 vapour barriers in these old walls that have been able to dry so well in the past xxx years because of the ample air entering and exiting the wall assembly.
Plank sheathing is very hard to seal up. A layer of SPF is one option as Peter proposes, the other one is dense packing. Either way you go, adding in the blocking is very important, impossible to air seal without this.
With older building, before you do any insulation make sure there is a WRB outside the sheathing. Without a WRB, there is a good chance an insulated wall will fail. Lack of WRB is common on older houses and you can run into trouble with mold and rot especially around openings.
Find somebody to do a blower door test. They don't cost a lot for what you learn. Mine came out at 15ACH. Gives me a good baseline and a number to compare to when we're done and applying for rebates.
I appreciate all of the great feedback, it's been very helpful to wrap my head around this. Blower door testing is obviously the best approach to eliminate the guesswork at before/after numbers so I'll pursue that and see where I land.
In terms of air sealing & insulation, spray foam doesn't appeal to me, but the efficiency of air sealing with a very thin layer is intriguing vs what may be an otherwise exhaustive effort to seal the old plank sheathing. It's also leads me back to another dilemma related to the wall assembly. We'll have the opportunity to tackle the wall from the exterior side when the cedar shake is replaced, but 2-3 winters will pass before that happens, and I'm mindful of the risk of trapping vapor and wreaking havoc in the wall cavities. Mineral wool batt with a smart vapor retarder is appealing, but I'd be interested to hear whether anyone thinks that is not a good approach.
Peter you raise a good point about radon, and installing a radon mitigation system is yet another fun issue to tackle, with average levels via multiple at home kits coming back around 3.5 pCi/L... renovating this old home is certainly not without its challenges.
Hello NC44, I am going to back away from my suggestion to use spray foam directly on the exterior “sheeting “. You are very correct about being cautious about trapping moisture in old solid wood walls.
So from confirming HVAC loads to talking about air sealing the stud bays.
I thought of this video from a few years back.
https://youtu.be/jhoQ_f9ZnzQ
After listening, consider this:
The dimple board creates an air cavity. The air barrier in front of the dimple board (to the inside) will serve one of 2 functions depending on how you insulate. With spray foam it allows you to keep the air cavity not only on the front of dimple mat but also on the back. If you use Roxul, it gives you an air barrier with the extra step of taping. You would need to use tape specified by the air barrier manufacturer.
If you take this approach, hopefully you could afford a high quality air barrier product, not one made of plastic with holes punched in it
If you do this, the building inspector has to be in agreement before you start. It might look labor intensive but it will be a true air seal and let the exterior dry. Going back to fix mold later is also very costly and bad for a family’s health.
I have never tried this method before so I can’t truly vouch for it Renovations are never easy and lots of difficult decisions accounting for so many factors. One step at time.
This video also talks about same type of problems with old houses and mold risk, but a different solution because there is no sheeting on the exterior.
https://youtu.be/VHPS5HC7VYw
You have to be careful with on-line content like this. Lot of times, companies pay for their product to be showcased.
Dimple mat is fantastic for what it was designed for, drainage outside of a foundation. Over time, manufacturers have been trying to find other uses of it in buildings. Some mostly benign (dimple matt underlay for flooring in basement). Dimple matt in walls falls into the bad idea category in my book.
Dimple matt is a true vapor barrier. Lot of Matt's work is down south where moisture movement is from the outside in, so a vapor barrier outside the wall is fine. In colder climate, this can create issues unless combined with spray foam. Any other way and it is a risky assembly.
In the case of the OP, with cedar shakes there is most likely tar paper for WRB, so the wall doesn't need an interior rain screen. This means any insulation can work.
A thin flash of spray foam won't trap moisture. Close cell SPF is about 2 perm/inch, so a 1" flash will still allow for moisture movement. 1" ccSPF is also more than what you need for condensation control inside a 2x4 stud cavity which further reduces moisture risk.
Provided there is an exterior WRB, I think the best insulation and air sealing would be to dense pack the walls with cellulose. Cellulose also has hygric buffering so it can help redistribute moisture inside walls, it is also the greenest insulation product. If the OP decides to re-side and install exterior insulation, cellulose will work great with any type of exterior insulation.
I have dense packed an older balloon framed house. This (along with some new windows and air sealing) took it from 20ach@50PA to 8ach, it turned the place from an icebox where you could not sit near outside walls or windows to a perfectly comfortable home. It also dropped the heat loss by about 60%.
Akos - You're correct on the WRB. I was speaking with the builder this morning, who not surprisingly is of the opinion that I'm overthinking everything, but he confirmed that it's tar paper.