Adding Flooring Over Uninsulated Slab

I’m renovating a room in my 1957 ranch built on a slab foundation (at grade), located in Massachusetts, climate zone 5A. Given the age of the house, I’m making the assumption there’s no insulation or vapor barrier below the slab.
The current floor is carpet, subfloor, 2×4 joists, slab foundation. I plan to replace this with an engineered hardwood floor.
My plan for the new floor: 6mil poly vapor barrier, 1.5″ xps, a second layer of 1.5″ xps rotated 90 degrees and glued to the first and seams taped, 3/4″ plywood floated over xps, a second layer of 3/4″ plywood rotated 90 degrees and screwed to the first, underlayment, 3/8″ engineered hardwood nailed to subfloor. Spray foam insulation applied along the edge. See attached detail.
My Questions:
1. Is the poly vapor barrier needed and what’s the proper way to terminate it at an existing wall? Is there reason to be concerned that I might drive moisture that enters the slab toward the wall/sill plate?
2. I’m planning on two layers of xps because 3″ xps is harder for me to acquire. Other than additional labor, are there reasons I shouldn’t take this approach?
3. Due to the presence of water piping in the slab, I’m not comfortable securing the subfloor through the foam into the slab with tap-cons. The plan is to float the subfloor on the xps. Will this work? Do I risk squeaky rigid insulation noise?
4. Any other advice or observations are greatly appreciated.
Thank you all for you expertise and advice!
GBA Detail Library
A collection of one thousand construction details organized by climate and house part
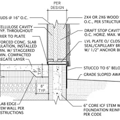
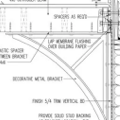
Replies
I'll give your post a bump. Have you measured the slab moisture level, or taped a square of poly to get a rough idea of how wet or dry it might be?
I suspect the experts will say that the poly vapor barrier is more belts and suspenders than necessary given the twin layers of XPS. (Have you check for reclaimed foam? It is much cheaper generally.)
From my DIY perspective, I think the floating floor approach will be fine. Have you thought-through transitions (doorways, stairs, etc.). Let's see what the community has to add.
It is a monolithic slab or a slab captured inside a frost wall perimeter?
If it's a captured slab, it's not a big deal to remove it and replace it after adding insulation if you wanted to go that direction. dusty and annoying demolition, but we have a project where we're doing that right now and it went fine.
If it's a monolithic, I have a minor concern that the any plumbing near the edge may run into temperature issues. If it's monolithic there is probably five to eight inches of slab edge exposed to the air, and if the plumbing is close to that edge it may be a problem after you isolate the slab from the interior temperature.
To address your questions:
1. I would install the poly. It's cheap insurance and means you need to worry about the XPS seams a lot less. I would probably tape it to the sill plate instead of up the framing, since the sill is (hopefully, maybe) isolated from the foundation properly, and may be pressure treated while the rest of the framing is not.
2. I agree on using two layers of XPS, 3-inch thicknesses are harder to come by.
3. I don't have any experience with floating these kinds of layers. I've heard of it being done successfully, but personally have the same concerns that you do.
It is gonna have a 4 foot frost wall in Mass
staggered I would think is as good or better than rotated
you can locate water pipes and if there are many, their days might be numbered. My 1970 house had several that had been re run, apparently due to corrosion, so we eliminated most of the copper in the slab
Modern adhesives are pretty amazing, eliminating the poly would enable adhesives to bond everything. urethane adhesives seem to not affect foam