EPS, XPS or Polyiso for exterior rigid foam?

Last week I got some great information from this board on my “Taping seams of roof sheathing” question. There was some thread drift there and we started talking about exterior foam and someone suggested I use Polyiso instead of XPS for my exterior foam.
I took that advice and started to look into Polyisocyanurate. I had previously written it off because I had “heard” it was twice the price of XPS and three times the price of EPS. However when I called up my insulation vendor I was shocked. It’s a little cheaper and provides a higher R value per dollar than XPS. Here is what my quote was:
2″ Polyiso 4×8 foil faced sheet (rmax thermasheath) 2.5lb density is R-31.1 – $33.64
2″ XPS 4×8 sheet 2.5lb density is R-10 – $34.99
2″ EPS 4×8 sheet 1.0lb density is R6.4 – $14.52
Cost per R for Polyisio, XPS and EPS is $2.53, $3.49, $2.26
I’m in a mountainous and snowy climate zone 6. My wall construction is interior latex paint vapor retarder, 2×6 stud cavity filled with BIBS, OSB, Tyvek, continuous insulation, then a mix of stone veneer, eifs stucco and siding on the outside. Obviously each exterior layer will have a drainage layer between the continuous insulation.
This leads me to a few questions
1) Why would anybody use XPS instead of Polyisio?
2) The R-31.1 is apparently an aged value. How much can I expect this to change due to the temperature effects and further aging?
3) How dimensionally stable is polyiso and are there any issues with installing siding over the top of furring strips?
4) In last week’s thread there was much discussion about vapor permeability of the continuous insulation. Foil faced polyiso is obviously impermeable but I think I might be able to get it mesh faced which will increase the permeability to 2ish. I think with R-13.1 I will exceed the code requirement of ratio of exterior continuous insulation to interior stud bay insulation. Therefore I should not have a condensation issue on my sheathing, right?
I really like the idea of using polyisocyanurate exterior foam it checks a lot of boxes: it’s better for the environment, it meets the code ratio for exterior continuous to interior insulation, it has better fire retardant properties. My installer says it is harder to work with than XPS or EPS because it doesn’t break like those do, so maybe I’ll expect slightly higher installation costs.
Am I missing anything in my considerations?
GBA Detail Library
A collection of one thousand construction details organized by climate and house part
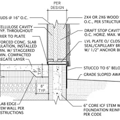
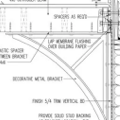
Replies
A follow up question: Looking at the foil faced polyiso permeability does it make sense to get rid of the Tyvek and use the polyisio taped seams as my WRB? That way I can have "outie" windows providing minimal exterior window sill for snow to settle on?
Most of the time EPS and polyiso are about the same 8-10 cents per square foot per R, and XPS is usually a about 11-13 cents per R-foot. Your price comparison is consistent with the trend.
There may be some typos in your table. At 2" most Type-I EPS is about R7.6-R7.8, not R6.4. At 2" most foil faced polyiso runs about R12-R13, not R31.
Most polyiso takes a performance hit when the average temp through the foam layer drops below 40F or so, the performance of XPS and EPS increases monotonically with falling temperature. When it's relatively new XPS may outperform polyiso over a winter when used as exterior sheathing, but as XPS ages, losing it's climate damaging HFC blowing agents it eventually drop to the performance level of EPS of similar density. (EPS has stable performance over decades, XPS does not.)
Cutting 2" EPS is pretty easy using a 4-5" taping knife sharpened on the sides and a straight edge, but anything with a facer still requires a bit more care in cutting. Type-I EPS is often a PITA to deal with, since it usually comes with facers, but is TOO easy to break.
From a fire-safety point of view polyiso has a bit of an edge, with a somewhat higher kindling temperature and the fact that chars in place when burning, unlike EPS & XPS which melts into a puddle of flaming polymer.
Steve, I'm glad we steered you toward polyiso in your thread last week. To add to Dana's response:
1. The only good reason to use XPS is that it's readily available. That's it. There are various types of EPS and polyiso that do everything as well or better than XPS, but they can require special ordering.
2. Assuming you mean R-13.1 for 2" polyiso, that may be true for Thermax, which has a proprietary formulation, but other types age to R-5.6 or R-5.7/in, or about R-11.2 total. You can accept manufacturer claims for higher values if you want, but I would not believe them. Here's a free article that covers the basics, with some links to GBA-Prime content for further reading: https://www.greenbuildingadvisor.com/blogs/dept/musings/cold-climates-r-5-foam-beats-r-6. (And here is a Fine Homebuilding overview of rigid foam that I wrote: http://www.finehomebuilding.com/2018/01/08/get-right-rigid-foam.)
3. Polyiso is fairly dimensionally stable, but does move a bit, so the best installations include multiple layers, all seams offset and taped, but depending on the situation it may not be critical. For exterior polyiso I spec an acrylic tape rather than foil so it has more "give." The assembly you propose is one of the most common in high performance construction. More info here: https://www.greenbuildingadvisor.com/blogs/dept/musings/how-install-rigid-foam-sheathing.
4. You can get polyiso with fiber facings. Here is one company near me that does that: https://www.hunterpanels.com/. But there is very little drying through 2" of polyiso foam so I would just make it thick enough and choose details that make exterior drying not critical.
Even with derating for temp 2" of polyiso will outperform 2" of EPS on the exterior of a 2x6/R20 type studwall in zone 6. Take a look at the curves on page 2 of this bit o' marketing fluff from Dow:
http://msdssearch.dow.com/PublishedLiteratureDOWCOM/dh_098a/0901b8038098a015.pdf?filepath=styrofoam/pdfs/noreg/179-00263.pdf&fromPage=GetDoc
Bear in mind that they took a worst-case higher density fiber faced roofing polyiso example that was only rated R5.2/inch @ 75F for that curve, not R6+/inch foil faced goods. (Most new fiber faced roofing polyiso is about R5.6-R5.7/inch @ 75F, not R5.2/inch.) Move the curve up by about R0.5-R1 to reflect the reality of typical foil faced wall sheathing polyiso.
Type-II EPS performs about R0.1/inch worse than the gray "Mineral Wool Batt" curve, Type-I EPS performs about 0.3/inch worse.
So when it's -10F outside 70F inside (an 80F delta-T) , with R20 in the cavities, the warm side of the polyiso will be about 20F, the cold side about -10F with a mean temp through the polyiso of about +5F. Even the crappy roofing polyiso in the curve would be delivering R8.6 at that temp, but foil faced goods would be at R9+. Type-I EPS would also be delivering a bit over R9 at that temp, Type-II about R9.5.
At +15F (a typical zone 6 mean temp for the month of January) the warm side of the foam would be about 32F, cold side 15F for a mean temp through the foam layer of 23F. At that temperature the crappy roofing on the Dow chart at 2" is delivering about R8.8, but foil faced goods would be delivering about R10, Type-II EPS would deliver about R9.5, and Type-I EPS would be good for about R9 or a hair less.
Averaged over a US climate zone 6 heating season the 2" foil faced polyiso or even R5.6/inch fiber faced roofing polyiso would still do substantially better than Type-II EPS, even if it does slightly worse during the coldest hours of the coldest days.
From a dew point control point of view it's the seasonal average performance that matters. At 2" it'll still be enough for dew point control if foil faced, but could be marginal if roofing foam. If EPS it will need to be at least 2.5". If XPS it has to be derated to R4.2/inch from a dew point control to have any margin after 50 years of service, which would also mean 2.5".
Awesome response guys. You did find my typo on polyiso but I think my number for EPS was correct per my supplier. I wrote it down as 2" of EPS = R6.4 - only a 1lbs density though instead of 2.5lb like he quoted on the XPS and EPS.
On the general topic of "don't believe the manufacturers data" I have nothing else to go on. I talk to my insulation installer and he quotes numbers that match what the supplier of the materials quotes that matches the manufacturers data which is "apparently" tested to standards. If all things are equal I have to go with the published data otherwise I'm pulling numbers out of thin air. I'm sure manufacturers all inflate their data by using only the best quality control foam and the most favorable test conditions but if they are all doing it then it averages out?
The chart that Dana linked to from Dow appears to be optimistic compared to the modelling done in Michael's link. Michael's link suggests a 30% increase in heat flow during the coldest month when using 2" Polyiso over XPS. Again it comes down to ur discussion last week about having the correct ratio of exterior to interior to prevent condensation.
So 5.5" of R-4.18/inch BIBS + 2" of R-31.1 Poly ~ R=36 with a 36% ratio exterior to interior insulation.
Using a worst case 30% reduction of Polyiso (I know the 30% was relative to XPS which gets better R in the cold) the 2" of Polyiso become R-9, making the whole wall R-32 which is a 28% ratio. There are other factors but even so I'm probably still going to stick with the 2" of Polyiso over the XPS because of the other benefits polyiso has. Looking at a weighted average based on the number of days colder than 15F I suspect I'm probably in good shape over all because the warmer days will allow drying to the inside of my wall.
With respect to going with a foil faced polyiso or a mesh faced polyiso to allow water vapor passage it seems that 2" of polyiso is fairly vapor impermeable by itself so I'm not making my assembly worse by having the polyiso be foil based and I assume the joint sealing tape would stick better to the foil than raw polyiso.
What about the diurnal dimensional stability of the polyiso when compared to eps or xps? With plenty of expand contract cycles it worries me about the edge sealing tape being fatigued and eventually peeling. As much as I want to do two 1" layers of polyiso with the seams overlapped and taped I don't think I can afford it. I had a quote of $13,000 just to install (no polyiso quoted only the fasteners included) 1 layer of polyiso, apparently $2000+ on that is in fasteners. I think I need about 170 sheets. The installer said the county requires x number of special fasteners per sheet (I think x was 18 IIRC). I argued that the fasteners just need to temporary until the furring strips are installed and he agreed but apparently the county does not!
Thanks to you both for those links. There is a lot more reading and understanding I need to do, particularly on the trimming of innie or outie windows with exterior foam but that's for another discussion.
Steve
All three major foam types--EPS, XPS and polyiso--have a lot in common but behave differently with changes in time and temperature.
"Foam Control Tech Data" here shows typical EPS R-values for the different types and densities available: http://www.foam-control.com/. The numbers are similar to those in ASTM C578, the standard specification for polystyrene.
Testing is done via ASTM C518 methods, which are somewhat flexible when it comes to sample sizes, and do not take into account what happens to the blowing agents over time. For that you need ASTM C1303, which tests the product at either 90 or 180 days, depending on ambient temperature during aging. The foil facing on polyiso retards evaporation of the blowing agents, so 180 days (or 90 days) may or may not be long enough for an accurate measurement. Feel free to trust the manufacturers' claims, or the common understanding in the building science world that a safe value is R-5.5 to R-6 at best, declining in cold temperatures. (Yes, I buy and read ASTM documents for fun.)
I'm not sure about the diurnal dimensional stability but I think it's pretty small. (I haven't bought ASTM C1289 yet.) Over time the panels can shrink a bit but I've never heard of tape failing.
> I'm not making my assembly worse by having the polyiso be foil based
If R values were the same (but they aren't), then 2+ external perms is better than ~0 perms of foil faced. But once you avoid mold, there isn't much point in dryer.
Steve: look for reclaimed foam. It's way cheaper than new. For less $ you can install more foam and save the planet at the same time. XPX, EPS and polyiso are all widely available as reclaimed stock.
The study at https://buildingsciencelabs.com/wp-content/uploads/2017/06/Long-term-Polysio-Movement-and-Thermal-Performance-Study.pdf monitored 2 different types of polyiso for dimensional and thermal stability over 6 years and the conclusions are less positive than I had hoped for. definitely like Michael's suggestion for the more flexible acrylic tape to better accommodate shrinkage. Hopefully the foil facing, as well as changes in formulation since 2009 make today's polyiso more stable in both respects. Bummer about your county silliness Steve, because those offset seams of two layers create about the best insurance available if shrinkage does cause tape failure and/or gaps. The vertical seams will all be held firmly and covered by the furring strips, but the horizontal tape seams could be questionable long term. They shouldn't see driven water at the back of the rainscreen gap, so should be able to dry if minimal moisture did enter at a failed tape joint, but I'm considering adding an extra tape layer on the top half of the horizontal joints on the outermost iso layer as insurance towards >50 yr performance. Any thoughts from the pros on this? Zone 5 CA, avg 59 in of rain/yr.
Good idea on the reclaimed foam. I checked my local craigs list last night and there is a place that sells 1.5" and 2" reclaimed polyiso foam. How do I know what I am buying is good and not (how did Dana put it) crappy roofing polyiso or so old that it's thermal resistance is not up to the latest standards or all escaped from aging?
It would be really nice to use two layers of 1.5" polyiso for my application. I wonder if that $13,000 would double for installation of two layers rather than the quoted 1 layer.
I've not fully got to grips with window trim and water management around the windows with exterior foam. I was trying to minimize the thickness of my exterior foam (to make it easier for my contractor to trim windows). What are the implications of going with 2 layers of 1.5" foam instead of 1 layer of 2" foam wrt window trim?
Steve, I would start by asking them if they have details on the foam they are selling. One place near me sells factory seconds; on a current project of mine the polyiso will be brand new but the branding will be smeared, at half the price of new. The owners were ok with that. In other cases the foam may be chewed up. Another thing to watch out for with recycled polyiso are the differences in dimensions; I've heard of people struggling with shimming every piece of furring due to dimensional discrepancies.
As for window install details, that's a big discussion on its own. Try starting with a GBA search--it comes up regularly. The newest cool kid on the block is ThermalBuck, but personally I usually prefer to seal the window flanges to the structural sheathing and use exterior extension jambs. But it depends on the situation.
Mitchell, as for the surface of the exterior insulation remaining water-tight, my approach (and that of other high performance designers and builders I know) is to not worry too much about it, but do provide a high quality WRB at the sheathing layer. If you want to be extra careful you could use more tape, or cover the whole thing with another WRB. Or use either XPS or a higher density EPS, which won't be affected if they see some water.
Roofing foam that has been chewed up by ants or frost damaged with peeling facers, or massively dented/scarred/buckled with missing corners is pretty obvious, and usually priced accordingly. If the stuff looks pretty squared and consistent on the edges it's pretty good.
There are subtle changes with used foam that don't affect performance much, but something to be aware of. The thickness might vary by 1/8" from one corner to the next, and the they may not be exactly 48" x 96" anymore. The good news is it's not going to shrink appreciably more if it's seen a couple decades of service or more.
Some older polyiso from the pre-Montreal Protocol era blown with ozone damaging CFHCs outperforms the newer stuff. Most new roofing iso runs about R5.7/inch- some of the old stuff is R7-ish/inch, even after 30 years of service. But for unknown goods don't count on it for being better than mid-5s from a design point of view. Thickness matters, since the thicker it is the higher the mean temp through the foam layer. From a dew point control perspective in your climate & stackup derate to R5/inch if adding 3" or more, R4.5/inch if it's 1.5- 2", R4 if it's just an inch.
Steve,
GBA has several articles that answer your questions.
Articles on rigid foam include this one: Choosing Rigid Foam
Articles on the cold weather performance of polyiso include this one: Cold-Weather Performance of Polyisocyanurate
Articles on changes in rigid foam R-values over time include this one: Thermal Drift of Polyiso and XPS
Articles on the dimensional stability of rigid foam include this one: Using Rigid Foam As a Water-Resistive Barrier