Execution of the BSC double stud wall

(Zone 7 Northern Wisconsin – 2000 square foot house – 2 story simple box design)
After reviewing many different wall systems we settled on the Building Science Corporation Double Stud Wall: https://www.buildingscience.com/documents/enclosures-that-work/high-r-value-wall-assemblies/high-r-value-double-stud-wall-construction
We chose this wall for its high r-value to cost ratio–it seems to be the least expensive option for a high r-value wall. It is easy to build, finish on the exterior and seems very durable.
As I’ve been receiving insulation quotes, some challenges have been brought up with the execution of this wall system, mainly, that in order to dense pack properly we’ll have to divide up the bays so they can be dense-packed 2 stud bays at a time. Additionally, that the process of blowing cellulose in is going to require a lot of air to escape, so we can’t full assemble the wall and insulate afterward. We either need to:
1. Put air-permeable netting on the outside, insulate, then enclose the outside with the fiberboard and weather resistant barrier OR
2. Finish the wall and holesaw both insulation holes and air escape holes and later tape them up
Does anyone have thoughts or experience on executing this wall system and best practices?
Does anyone want to try to talk me out of this wall system towards a different high-r-value wall assembly?
Thank you from Wisconsin.
GBA Detail Library
A collection of one thousand construction details organized by climate and house part
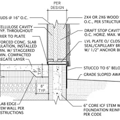
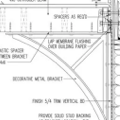
Replies
If you really need to push the cost down, and cellulose is adding too much extra labor, you could use a 2x4 wall, 3.5" gap, 2x4 wall, you could insulate it with 3 layers of 3.5" fiberglass batts (maybe running the batts sideways in the gap). I haven't used this technique however, just repeating things I've read on GBA, so grain of salt and all that :)
Hopefully some cellulose experts will chime in with thoughts about your cellulose questions!
I'll try to talk you out of it! I realize that blown in cellulose
in walls is on everybody's pop favorite hit list today but
there is a far more rational way to construct a double
stud wall - We're going to put a really good air/moisture
barrier in the middle so it can dry to both outside and
inside and then insure that the surface of that moisture
barrier always remains above the dew point!
Outer stud wall - ordinary 2x6 with batts (mineral wool?) -
then fasten 2 or more inches of polyiso to the inner face
of the 2x6 studs - then construct a 2x4 inside wall against
the inner face of the polyiso. The inner 2x4 wall becomes the
service cavity and sheet rock hanger - the polyiso (Foil Faced)
is the air/moisture barrier and is protected from physical
damage by both inner and outer walls and from R-value drop
by the insulated outer 2x6 wall - YES! you do need to tape
the seams on the inner side of the polyiso and seal it to the
floor and ceiling with some combo of caulk, tape, or spray-on.
With 3 inches of polyiso the total wall thickness will be 12
inches (stud face to stud face). The "whole-wall" R-value will
be around 36. Want more R-value? Fill the service cavity with
batts or blow in for around R-45, Or increase the thickness
of the polyiso, and/or use 2x10 for outer wall. With this wall
design at 12" and the service cavity filled, the inner foil
surface of the polyiso will remain above the dew point for any
temperature difference (delta T) between interior & ext. less
than about 88f(49c). (and int humidity levels less than 50%,
which is normal when it's this cold).
In other words, it would have to be colder than about -18f(-28c)
to reach the dew point in the wall. If it commonly gets colder
than this where you live you need a higher R-value (thicker wall).
Emphasize commonly here - many days/nights, not just a couple
every few years. Live in Fairbanks? 6" of polyiso and a 2x10
exterior wall (over R-70) might be appropriate.
CAUTION! Do not even think about an insulated 2x6 interior wall
(service Cavity) or placing extra (fiberous) insulation between the
interior wall and the polyiso - although it's a cheap way to raise
the total R-value, it would also lower the temp at the interior
foil surface of the polyiso - likely below the dew point. NOTE!
just leaving the inner 2x4 wall empty will keep you above the dew
point for nearly any outside temp (-70f(-57c),no problem) but
the lower R-value will increase energy use unless you add more
polyiso. There just ain't no free lunch!
There are some unstated assumptions here, of course, such
as a working heating/cooling/vent system, good choices for
exterior siding, sheathing and rain screen, a preference
for living at normal temp/humidity levels, etc.
Know that materials cost of 3"polyiso (R-19) instead of say
3.5"Roxul(R-15) in a double wall will add around $1000 to a
2000 sq. ft. house (2019).But, then subtract the cost of
the now unnessary vapor retarder and add peace of mind.
Why fumble around with fragile vapor retarders, exterior foams
vunlerable to insects and/or fire, awkward and labor expensive
siding instalation over foam, or, worse, insulation prone to
settling over the years? If you live in a climate harsh
enough to justify double wall construction -this is about the
best compromise available with current technology.
Last, consider that with this wall design it becomes possible to
erect the outer 2x6 wall and then complete a weather tight house (as
one big empty room - no interior walls). Then do all the rest of
the work inside, out of the weather, including finishing the double
wall because the inside 2x4 wall of the double wall is mearely another interior wall! Although, not every contractor will like this construction sequence.
Every time a discussion comes up about double-wall construction you post this same advice, and every time I ask you if you have used this design, or seen it used - and never get a response.
I'm not trying to be difficult - it sounds interesting - but I'm curious as to how you deal with the difficult transitions at floors, rim joists etc. I also wonder what the advantage is of the mid-wall foam over a smart membrane, or a layer of sheathing?
I agree with Malcolm. I’ve seen you post this same info, and it looks like copy/paste. If you want to promote this wall assembly, why not write a real article about it with some pictures. Submit the article to Martin, maybe he will publish it for you on GBA. If there are real merits to the assembly you propose, you’ll get some comments on it that may even help you to improve your idea.
Bill
Probably the easiest way is to install netting to subdivde the walls into section. This way the wall can be packed in one shot. Similar to how it is done with the Larsen trusses:
https://www.greenbuildingadvisor.com/article/all-about-larsen-trusses
I doubt it would add much labor cost since you will already be installing netting on the interior anyways.
PS. Just check the wall you want to do and it is with a middle plywood layer. This makes things complicated, maybe it is a decision you need to make weather this detail is worth the cost. There a lot of simple double stud walls out there.
Michael, I'm from Appleton, WI and have been in the building trades for 40 years (off season when not guiding on big walls) and doing deep energy retrofits for 10. Lifetime member of MREA. But, I still haven't been part of a double wall build and would love to help if my work load isn't too great. You can get hold of me at https://kuennllc.com/
Cheers and good for you!
Malcolm Taylor:
I 'm just an old retired gummer these days but back in the day
I designed, built and lived in three double wall houses. Lived in
them for over 26 years in total - all in the mountain west at elevations
above 7000 feet. Being the owner, designer, general contractor and
living in them gave me enough time to observe performance and
think it through. The designs used included 2x4 walls both sides with
fiberglass batts in the gap horizontal as suggested above by Brendan
Albano , 2x4 & 2x6 with both fiberglass and mineral wool, Larsen truss
walls and a small portion of one house with foam between the walls. All
worked well, my wife and I loved living in them. They are much quieter
than standard construction and having yearly heating/cooling costs near
zero for 26 years really adds up. Some are easier to construct than others,
the easiest of all for me was the one described above with polyiso in the
middle, unfortunately I didn't think this up until nearly finished with the last
one or I would have built them all this way - if I still had pictures or plans I'd
share them with you but it's been more than 15 years since we sold the last one
and retired to sunnier climes.
Thanks for replying. It's an interesting idea and I wanted to explore the implications of the design. What would be useful is to compare it to many of the similar ones people propose or have built.
The shortcoming I see are:
- Unless it's a one storey built on a slab, unlike designs where the outer wall is continuous and the inner one load-bearing (like the BSC ideal wall), it doesn't address the weakness of insulating and air-sealing at the floor levels.
- It incorporates a substantial amount of foam - something double-walls typically can avoid with0ut incurring an energy or robustness penalty.
- I don't see what advantage the foam offers over walls that also have a mid-wall air/vapour barrier made of plywood or membrane.
Isn't it in essence just a conventional wall with interior foam, which then has a service-wall built on the interior. If so, why not just strap the foam?
- Sequence of construction makes it perhaps friendly for owner-builders, but difficult for those contracting out the work.
What I like about it:
- The air/vapour control layer is safely buried (but not at the floors).
- Easier to build and detail than exterior foam, and allows a much thicker layer without added complications.
- Relies on a conventionally framed basic shell, which then gets modified by the improvements.
And in WI, we can get very good condition used Polyiso for about 14 cents/sq.Ft.
Paul,
A board-foot?
Michael,
The BSC double stud wall is awesome. It keeps the air barrier in the middle of the wall where it belongs. It uses less lumber than a Larson Truss wall (which is more of a triple stud wall). And it achieve high r values without foam.
But, I personally believe that a normal double stud wall would be cheaper and easier due the complications you described. The other complication for the BSC double stud wall is the foundation detail. (What does the outer wall rest upon? Or does it hang from trusses?)
Anyway, there are two articles I have read that may be helpful as you think through the insulation dilemma.
1. Rochester Passivhaus:
https://rochesterpassivehouse.blogspot.com/2016/03/construction-update-2.html?m=1
They insulated from the outside through a wrb.
2. ecocor site built Passivhaus: (see attachment)
For this house, Chris Corson writes the following, regarding insulating the outer cavity:
"The weather forecast included a chance
of rain and snow, so to avoid having the job
interrupted, I decided to fill the I-joist cav-
ities from inside the shell — even though
that meant cutting holes in our OSB air
barrier, which we had just meticulously
sealed and tested. But I figured that it was
better to go around and retape all the holes
in the OSB than to have our insulation
guys trying to work from outside the house
on ladders and staging. "
For my own double stud wall house, our insulation crew had never dense packed such a thick wall. They figured it out however despite no dividers between studs. I opted for dense pack fiberglass because I feel it is less likely to settle if they didn't get the density quite right.
Good luck!
Malcolm Taylor:
Some thoughts on your shortcomings: I think the majority
of residential housing today is built with platform
construction (I don't have statistics to prove this), not
with balloon framing. With platform construction (for
multi-story houses or slab on grade single story) there
is no problem with air sealing at the floors it's the
same as double walls with batts or blow in insulation.
Balloon construction is inherently more expensive and
requires special detailing for fire protection on
multistory. There may also be a stack effect air
circulation problem in the so-called continuous outer
wall with balloon framing - probably better not to find
out the hard way after living in one for a few years.
Here is the advantage over walls with a mid-wall air/vapor
barrier. Lets look at the temperature differentials across
the wall in fairly cold weather. Assume a 2x4 inner with a
5" gap and a 2x6 outer (structural) all filled with batts or
cellulose - also assume the air/vapor barrier is fastened to
the inner surface of the 2x6 wall. The reason for this assumption
is that it is really difficult and time consuming (read expensive)
to fasten it to the outer surface of the inner 2x4 wall and
achieve real air tightness (this is why contractors would like
to build the interior wall first when double walls are specified).
So back to temperatures - Assume interior of 70f & exterior of
-20 - total gradient 90f - whole wall assembly R-value will be
approx. 45 (we are ignoring R-values for air films, sheetrock,
rain screens, etc here - only considering stud face to stud face
and rounding off to +- 1).(also assuming 25% wood in the walls &
3.5 per inch for the insulation) no reason to get any more precise
than this here I think.
The percentage of insulation interior (2x4 wall + gap)
to the air/vapor barrier will be 29/45 or 64% therefore the
temperature at the air/vapor barrier will be 70-(.64*90) or 12f.
Looking at a dew point calculator on the Web we see that with
50% humidity interior the dew point is 50f - even if we assume
a much lower humidity, say 25% the dew point is still 32f. So
the choice is spend the money necessary to construct the air/vapor
barrier on the exterior surface of the inside 2x4 wall, spend
an unbelievable amount of time an effort trying to make the surface
of the Sheetrock air tight and vapor impermeable or spend a small
amount extra on foam inside the wall - foam inside the wall is cheaper
and way easier to construct.
Why not strap the wall? Because then you start to run into the problems
with large numbers of long strong expensive fasteners through the
strapping and the foam. And it reduces the service cavity to the point
where nothing bigger than electric cable can be used (no extra fiber insulation - if you want it, will fit). Those long strong fasteners
conduct heat like crazy reducing the R-val of the wall - I have never
run the calcs but I have seen talk on the web about this claiming
that the nails and fasteners through exterior insulation reduces its
R-val by more than 30% - true or false??
User...182,
- Take a look at the outer-framing on the BSC wall and the detail Michael posted below. It is still platform framing, but with the floor system inset. Sometimes the second floor subfloor is carried out to add stability.
- I'm not arguing against a mid wall air-barrier. What I wonder about is what advantage using foam for that yields.
- I take your point about an inner-wall rather than strapping. That's how I prefer to frame basements too.
- For a one storey slab on grade house, I'd certainly consider your wall.
Thanks for the feedback everyone.
I'll first say that the primary interest in my post is for help on the order of execution on this particular double stud wall with the exterior of the interior wall having the OSB sheathing and being the air-barrier. On top of that, I do (still) welcome people who feel compelled to talk me out of it, but it is hard to see a more economical and proven wall system that achieves my objectives better than the double stud wall...
We had originally settled on the double stud wall as it seems to be the most economical way to achieve the high r-value we desire. A few other reasons we had settled on that wall:
- I am interested in keeping the air barrier on the inner 1/3rd (or so) of the wall. For my climate, that seems to be a best practice.
- Trying to stay away from foam for a variety of reasons, but mostly have been interested in a wall that breathes and the above air-barrier positioning (and I don't like foam)
- Want to keep a separate service cavity for electrical, etc. This cavity could also be insulated, but is separate and you don't have to finish air barrier detailing around electrical boxes, etc.
- Want to address thermal bridging, of course.
- Solid substrate on the exterior - IE: I like 2x6 walls with 4" of exterior mineral wool, but I don't like the fudge factor that will happen when screwing cladding strapping on the outside.
Per Rick's most recent comment, I have attached the foundation detailing my designer had intended. The only barrier we're running into is the order of assembly and how to properly insulate this thing without cutting big holes in the air-barrier to do so. The dividers between studs should be relatively easy to address.
Rick, I'll review the attachment you sent. Thank you.
The only other wall system that I've found very attractive are the ones put out by Bensonwood... Like this: https://bensonwood.com/building-systems/panelized-enclosures/#wfb-walls. With a service cavity, air-tight barrier on the inside, 2x6 or 2x8 standard framing being universal and then exterior Gutex wood fiberboard, it seems like an excellent option... Just not sure how economical this option would be. Anyone have experience with this one?
Michael,
You end up with a well performing wall. The only downsides I can see are needing two layers of sheathing, and an awfully wide foundation.
- Some builders (Like Lucas Durand, Thosten Chlup) have eliminated the outer layer of sheathing, which is easier to do if you are including rain-screen strapping.
- You could cantilever the outer wall and reduce the foundation width to 10".
But if neither of those things bothers you I'd stick to what you have.
One thing you might also consider is running the second storey subfloor out to tie the two walls together.
Take a look at Stephen Sheehy's blog. He insulated a double-stud wall with a mid-wall air barrier:
https://www.greenbuildingadvisor.com/article/framed-walls-and-air-barrier-membranes-for-a-pretty-good-house
Rick,
If you can build the outside wall without a top plate, you should be able to dense pack in two stages, do the main floor from ground level and the 2nd story from the attic (similar to how it is done here http://www.greenhomebuilding.com/articles/larsentruss.htm ).
You can dense pack with the sheathing on but fiberboard tends to bulge, might be better to go with netting which can be rolled flat.
P.S. I don't think it is worth the cost to dense pack your service cavity. If you are paying for the labor, getting batts installed in there would probably be cheaper then an extra round of dense packing. Also give you a slight bump in center of cavity R value (R14 for mineral wool vs 13.5 for dense pack).
Akos- that is a great idea! Thanks for sharing
A really high percentage of those participating on this site
seem to be enamored with the idea that filling a wall with
blown in cellulose is superior to most other insulation options.
Because this comes up so often (especially with regard to
double wall construction), I thought I'd pose a provocative
question or two.
First have you watched the following video? It's rather
long and not particularly exciting.
Alaska's First Net Zero Energy Homes Performance Update
https://www.youtube.com/watch?v=Xen_VWyDezY
The part that is pertinent is approx. 1h 19m 45s in and
shows the settling problems encountered by Thorsten Chlupp
with his house in Fairbanks - note that he went to extremes
in attempting prevent settling in these walls including
careful control of density and actually leaving the walls
open at the top in the attic with feet of extra cellulose
piled up over the top of the open walls so that if settling
occurred the extra would refill the wall cavity.Guess what!
After about one year thermal imaging shows extensive settling
at random locations in his wall - it's a multi-story wall.
Thorsten is a strong advocate of blown in cellulose but
even so earlier in the video he notes that it is not
appropriate in all climates.
Still think that this is the best available today?
Actually, I really admire his work up there and have no
problem with cellulose in attics - but this result
indicates that no amount of careful will guarantee no
settling in the walls! Other insulations are not known
to have this characteristic.
Last is your belief in the "GREEN" of cellulose so strong
that you're actually willing to risk it?
Many of us are enamored with cellulose-filled double stud walls because they are simple to build and they work. To the best of my knowledge there are no documented failures. We are all looking for better ways to build, and I have first-hand experience with the Ecocor system (I used to work there) and it is indeed a better way to build. But it's not faster or less expensive than double stud walls. As soon as we start seeing actual failures, or a lack of raw material drives prices up, it will be easier to focus on other solutions. Or if affordable, dense, vapor-open waterproof exterior insulation with a low global warming potential becomes readily available, many of us will likely shift toward continuous exterior insulation.
I didn't watch the whole video, just the part you referred to, but it sounded like he said that was the first time he'd tried it and since then he'd adopted a higher density fill? That's also a fairly tall wall, and settling is far less likely at the 8-9ft wall heights typical of most residential builds.
I'm no expert, but from what I've read it seems early cellulose dense packs were done in the 3.5 lbs/cuft range regardless of cavity depth. Now it's recommended for deep cavities (like 12") to be filled to 4-4.2 lbs/cuft. This was validated by accelerated aging simulation in Europe using temperature and vibration cycling of wall assemblies. I don't have the document handy, perhaps someone else could post a link?
Exactly. The first wall he ever tried to dense-pack. A 24" thick wall at that.
This public service message is brought to you by the fiberglass manufacturer's association. 'cause glass is better (tm).
I feel like I'm getting more suspicious as I age.
The old cliche "In God We Trust all others are required
to submit data" really apply s here! Assertions by
cellulose manufactures, installers, and home owners
are not valid data. What's needed is thermal imagery
for several thousand walls that have been in use for
five or six years in a large variation of locations.
Without the data you're whistling past the graveyard.
But you have to give Thorsten credit - he really tried.
It certainly takes those pioneering spirits to try and try again until we get things right. I've done a pile of research on the good old cellulose filled double stud wall, and it seems most if not all of the issues have been thoroughly studied and solved. The detailing is more of a concern than the design at this point, which is true of most established wall assemblies.
#8 & 9
Malcolm, it's actually cheaper. Last time he gave me the 8'x4' x 2.2" (with the tar paper outer skin) for only $4 per, so 12.5 cents a sq. Ft. He seems to always have a supply. Roofing company so it's inner protected layer and he separates good vs so so.
Paul,
It's great from both an ecological and financial perspective that there is a well-established market for used foam, but I'm not sure it makes sense to compare the cost of differing approaches using second-hand prices for one of the options.
It distorts the analysis the same way it would to compare building assemblies without including labour because you intend to do the work yourself, or your friend will do it for free.
The second problem is: It is unclear from my reading of our code that second-hand foam can be used in new construction. It may be, but it certainly isn't straightforward .