Exterior foam for mansard roof with cathedral ceilings

I need a sanity check on the proper application of exterior rigid foam with a complex Mansard style roof.
We just closed on a home built in the 80’s that needs an entirely new roof. The current roof appears to have been installed in 1986 and is well past it’s use by date.
The existing structure is unique and poses a couple of challenges.
The architecture includes a large Cupola in the center, 2 large barrel shaped dormers that taper up the roof and an eyebrow section over the front door with a complex, convex shape.
The interior is a vaulted ceiling with exposed structural trusses and a tight drywall ceiling. (see photo)
Only 2 recessed can lights on the entire upper level, so it appears to be fairly airtight at the ceiling. The roof truss appear to be 2×10’s with R-13 or R-13 in the space between the trusses, above the drywall, appears to include 2×8’s with R13 or R19.
I have zero visibility into the roof insulation, just judging by thermal images. There is only a small 8×8 “attic” space in the entire upper level of the home, and of course it houses an HVAC unit. There are no ducts in the attic.
I am assuming that there is some airspace between the current insulation and the roof deck, per common practice and gravity since it’s 32 years old.
I’m having difficulty finding roofers who understand the concept, much less the execution, of exterior rigid foam over the structural sheathing.
The discussions start with “the roof needs to breath” then I point out the current roof is unvented.
Followed by “we can use some cool roofing shingles, it will do the same thing”.
Then it devolves into adding radiant barriers, covering the entire Mansard wall in peel and stick, etc.
I’m using the detail image found in the detail library (attached) to try and relay the concepts.
Is this detail suitable for adapting to a Mansard roof?
I can’t think of any reason why it would not apply.
I’m asking to have the structural sheathing taped or fluid applied at the seams, staggered polyiso foam of 2-3″, again taped at seams, followed by nailbase, sympathetic underlayment and shingles.
Am I over thinking this or missing something? It just doesn’t seem that complex.
I understand that the roof will be “thicker” than normal and that brings additional fascia detailing. We might even have to get some sort of tapering of a couple of panels on the eyebrow dormer but nothing over the top.
Finally, I know I’ll be replacing some of the roof decking based on the condition of the shingles. I assume since we are using exterior foam, I can just add insulation to the exposed cavities and not worry about any air channel below the structural sheathing given the exterior foam.
GBA Detail Library
A collection of one thousand construction details organized by climate and house part
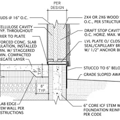
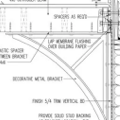
Replies
Jayson,
You're in a tough situation due to the curves on this roof. Adding rigid foam above this roof is a challenge. It would involve the use of multiple layers of thin rigid foam (perhaps 1/2-inch foam) in the curved sections, or judicious use of spray foam in the curved sections, along with custom-made framing members above the roof sheathing to handle the spray foam.
It might be doable, but it's a challenging job, both in terms of craftsmanship and aesthetics. It would also be very expensive.
I think you should replace the roofing using conventional roofing methods -- without any exterior insulation -- and tear out the drywall ceiling. Use closed-cell spray foam on the interior (supplemented by a fluffy insulation) -- in other words, the flash-and-batt approach -- followed by new drywall.
For more information, see "Flash-and-Batt Insulation."
Thanks for the input Martin, I appreciate it.
I'm trying to avoid tearing out the sheet rock due to the complexity of the interior finishes. The sheetrock guys really do not want to replicate the interior barrels and they won't even quote it out, just T&M.
How about using layers of 1/4" sheet foam on the barrel and convex portions or just not foaming those areas at all?
It wouldn't be an insulated as the rest of the space but those details account for less than 10% of the total area so at least I'd be improving the other 90%.
I also thought maybe something like an elastomeric sheet insulation that could confirm to the curve, but the shingles will still need nailbase so it might just make more sense to stuff those cavities full and not try to insulate from the top in those spots.
can you remove the roof sheathing, and existing insulation, and fill with spray foam? seems like it would be cheaper than removing the drywall
The location/climate zone of this place is... ??
With chunks or strips of polyiso of the appropriate thickness cap-nailed to the roof deck as depth guides, an experienced foam installer can put a fairly consistent depth of 2lb foam onto just about any curved surface. With the foam in place 2x4 sleepers can be through screwed to the structural roof deck with pancake head timber screws, onto which a nailer deck can be fastened.
With more environmentally friendly HFO blown closed cell foam it'll run about R7/inch, and code compliance can be made on a U-factor basis rather than R value, to keep the added thickness to reasonable levels. With the pre-existing enclosed cavities & fluff and the extra air films & R value of the vented nailer it probably won't take more than 4" to get there with HFO blown 2lb foam even in colder climates. At the 3" closed cell foam itself is structural, and is it's own weather resistant barrier- no need for peel & stick membranes. (The nailer deck still needs #30 felt under the shingles.)
At $125-1.50 per square foot per inch of depth it's not cheap, but then again neither is a dozen layers of 1/4" rigid foam.
Sorry Dana, you'd think I'd remember to add that.
Zip is 35244 Zone 3
I finally found a roofer who completely understands Polyiso on roof deck, and he's finished the job that Martin started by talking me out of rigid foam.
He says that there is no way to add the rigid foam without a ton of flashing due to the changes in thickness. There is just no way to make it look right with the dormers and eyebrow. So we are back to adding insulation where possible under the decking.
I also had a foam specialist look at it with the roofer, they are concerned they can't get the foam in all of the required areas due to the decking being tied into the trusses blocking access, so I think interior foam is out too.
So given that exterior foam is out, blown in foam is out, is there anything else to consider short of just stuffing as much fluffy insulation as they can in the areas they can access?
I was planning to use Rockwool on top of the current fiberglass for areas where the decking is completely replaced or should I just save that extra expense and add more fiberglass?