Fiberglass over spray foam?

Hi everyone. I have a notorious Cape Cod style house in central NJ. There is 2 dormers on the front and a big shed dormer/extension across the entire back. Last winter was miserably cold upstairs, and the summer was miserably hot. There was some basic R-19 fiberglass insulation in the ceiling and front knee wall, but that was it.
We just spend (a lot) of money to have a company come in and redo everything. Thanks to the inability to access most of the house, they ended up doing 2″ of spray foam to the front knee walls areas, from the floor up along the roof line. The knee wall is now part of the interior envelope of the house. For the slopes they dense-packed cellulose to R19, and for the attic flat they did cellulose to R52.
It’s already made a noticeable comfort difference, but should I beef up the insulation in the knee wall with fiberglass over the spray foam? 2″ of spray foam is only R12. The only problem is any substantial amount of fiberglass, like R21, is 5.5″ thick. I already have 2″ of spray foam in there, and the bays are only 5.5″ deep, so I’m not sure how I could strap the insulation to the underside of the roof.
GBA Detail Library
A collection of one thousand construction details organized by climate and house part
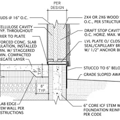
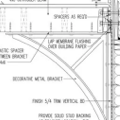
Replies
Matt, in your location you should be able to install up to R-27 on the interior side of the foam and still have condensation control, extrapolating IRC prescriptive values, but lower than R-27 is safer to prevent moisture accumulation. Or get the spray foam company back to apply another inch, and add up to R-40 at the interior. You can furr the rafters down to get more space for insulation. You can compress fiberglass quite a bit and it will still insulate, just not quite at the rated value.
Michael covered the fiberglass questions well.
Is there any venting in your roof assembly? Either soffit, ridge, or gable? It sounds like at least part of the roof is unvented dense packed at R19. If this is the case, you should understand that there are some moisture risks to the unvented assembly and how to mitigate them. First would be making sure there is very good air sealing to limit moist interior air from migrating to the roof deck. A blower door test would be valuable if it has not been done. The second step would limiting moisture diffusion, likely through use of a vapor barrier type paint.
Which side of the knee walls was the spray foam applied to? Directly to the back of the drywall? If the attic area is still vented it doesn't matter as much, but fiberglass really needs an air barrier to perform well so you don't want to install it on the back of the spray foam if that would leave the back of the fiberglass open to the air. Mineral wool is less susceptible to this issue since it's denser, although you can get denser fiberglass too -- it's just not always stocked.
There is no reason you can't install some extra fiberglass over the spray foam though, it's done all the time. You just want to do it right. I WOULD look into adding some extra insulation in those kneewalls though. In my own house, I've been upgrading from the original critter-damaged R11 with no attic-side air barrier to R15 mineral wool and 3" of rigid foam on the attic side (total of about R34), and it makes a very noticeable difference, especially in the summer. If you wrap the top plates with the rigid foam that helps with thermal bridging too.
Bill
The spray foam was sprayed directly on to the underside of the roofing deck. The fiberglass that was against the drywall was removed and not replaced. The original setup was faced R19 on the drywall, and that was it. No floor or roof decking insulation in the knee wall. Then the slope and the attic flat were stuffed with R13.
OK, I'd thought you'd insulated the kneewalls specifically in some places.
You can easily add batts between the rafters under the spray foam. You can support it with wire supports.
Bill
No, there is no venting. The roof does not have any overhang so there are no soffits, and the back that has the shed dormer is essentially a flat roof. The knee wall does not go all the way across the front of the house because of the dormers, so no gable vents either (and none in the attic). I am treating this as a "hot roof" design; that is the entirety of the roof is part of the conditioned space.
So at least in my mind, the "flash-and-batt" approach seems likes the easiest, cheapest, and best method?
So the areas with spray foam can definitely be flash and batt as Michael said. Should work well and perfectly safe for those areas.
Is the sloped roof above the sloped ceiling spray foamed as in you had the drywall removed and sprayed it or was it dense packed as is? If it was just dense packed as is, you want to take steps to mitigate potential for moisture issues.
The flat ceiling section may benefit from gable vents if there are none.
The sloped roof was dense packed as is; it would have been a huge mess and cost to remove the drywall. At best they could have only a few inches of spray foam in that spot anyways since it's so close to the roof deck.
The attic flat has a power fan in it but there's barely any room up there. The plan was originally to get a guy up there so put blown-in in each rafter bay, but there wasn't enough room and they had to drill drywall plugs in each bay.
Dense Packed Roofs are known to be risky. There are a lot of articles around, but this one is pretty comprehensive.
https://www.buildingscience.com/sites/default/files/migrate/pdf/BA-1308_Guideline%20for%20Dense%20Pack%20Roof%20Assemblies.pdf
Managing such an assembly involves optimizing air sealing, establishing a vapor barrier (likely paint), and managing indoor humidity levels.
Another post with details on your assembly might yield some useful feedback from others.
Thanks, that is a great article. Thankfully, the parts that are dense-packed have no penetrations at all. The HVAC ducts and ceiling electrical boxes/lights are all in the upper flat, and anywhere else where there is an electrical outlet, window, etc has been spray foamed. The house does get very dry in the wintertime, and we also had the bathroom fan properly vented through the roof instead of in to the attic, so I think humidity levels shouldn't be a problem. I will put down a vapor barrier paint when repaint the drywall. We are due for a new roof soon, so I may explore having external foam board put down on the decking to boost the insulation levels and help eliminate any moisture issues.
Thank you everyone for the help, this is a great site with a lot of good information and knowledgeable people.