Flash and batt

Looking at doing a flash a batt detail for my exterior walls. Northern Iowa climate zone 6. Here’s my thoughts. 2” halo exterra gps outside the wall with a rain screen, 2” spray foam, 3.5” real wool batt giving me a total r of 37. Or instead of 3.5” batt filling the rest of cavity with real wool blow in for a little higher total r value of 39. Does this sound like a good system? Any thoughts or input would be greatly appreciated. Thanks!!
GBA Detail Library
A collection of one thousand construction details organized by climate and house part
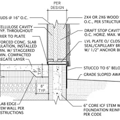
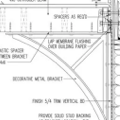
Replies
Seth,
You can try the Halo wall calculator: https://buildwithhalo.com/r-value-calculator/
to test your materials choices. Your R values seem a bit optimistic and I don't think you are accounting for whole wall performance. Not sure if the calculator will accommodate a flash and batt arrangement, but you don't want to do that anyway. You would be creating the dreaded low/no perm sandwich that puts your sheathing and studs at risk of moisture entrapment. I suspect the northern half of Iowa is much like Illinois... long hot humid summers and cold wet winters with super frigid temps occasionally. You have a demanding environment to design for.
One might argue that air and moisture can't get to the sheathing thanks to the exterior and interior foam barriers, but insulation gaps and the framing will still permit moisture migration. Plus all the holes made for lights, vents, etc. The structural elements need to be able to dry to one side or the other of an assembly effectively. Continuous exterior insulation blocks the path to outside, the flash coat of spray foam greatly inhibits the drying path to the inside. Plus the proposed 2" of interior spray foam will ensure the sheathing drops below dew point for a greater band of humidity and temperature conditions.
You can use flash and batt without exterior continuous insulation since the sheathing and framing can dry to the exterior (with proper WRB and cladding choices). The main drawbacks are: spray foam is expensive, usually more damaging to the environment and largely bad economics thanks to thermal bridging from framing losses. The whole wall performance of a traditional insulated stud bay wall is lower than your nominal in bay insulation R values since the framing acts like cooling fins. (Or heating fins) Continuous exterior insulation will provide much better whole wall performance. You will get less freezing corners from framing losses with exterior insulation.
R-10 exterior continuous is a bit shy of the R-11.5 recommended for 2x6 hybrid wall set ups in CZ6 with Class 3 vapor control. With the right interior vapor control membrane and good detailing you may have a viable wall profile. Others can advise better on the best choices.
Even with a good "smart membrane" you may have a possible problem due to the real wool insulation.
The one brand I checked claims R-4.5 per inch or R-24.75 for a 5.5" stud depth. Add dry wall and I'll guess a clean R-25 to back of sheathing. This ratio of interior to exterior insulation will bring your potential winter dew point inside of the sheathing. This elevates your risk even with interior vapor barriers.
There are two viewpoints on the general success of obtaining good interior detailing of vapor and air control for situations like yours. I am of the opinion that adding enough exterior insulation over a self adhered air barrier to allow for Class 3 interior vapor control is preferred.
I know how much time and effort I put in ensuring the exterior air sealing was tight and how little control I could exert over the many trades drilling holes in things inside. The drywall crew was very patient with me, but did make it clear that nuances regarding sealing of edges and electric boxes were on me. Fortunately, I had designed to dry to the interior thanks to heavy exterior insulation. I did not need to fuss with airtight boxes, duct boot seals and drywall sealants on exterior panels. I spent my time getting blocking in place for cabinets and such.
You don't indicate if this is a fresh build or not. If it is a gut rehab and residing there may be other factors to consider before going all in on one form of insulation. Windows, doors and framing choices will all play into your final heating and cooling demands. Balancing the whole design is more than just a wall profile.
I don't think you really gain much here with the spray foam unless you have some kind of particularly difficult assembly to air seal. I would go with mineral wool batts in the walls which gives you R23 cavity fill. R10 on the exterior gets you to R33 for the assembly.
I agree that your R values seem optimistic. I'm guessing you're assuming R7/inch for the spray foam, which is overly high -- R6/inch is more realistic. Note also that you'll never get a perfectly even layer of closed cell spray foam, you typically get a layer that is a bit overly thick at the edges and a bit thin in the middle. With thinner layers, this is more of an issue in terms of relative performance of the material.
I would skip the spray foam, airsealing the "old fashioned way" instead using canned foam and caulk. I would detail the exterior rigid foam airtight too, which gives you a redundant air barrier. Take the savings from not using spray foam and put that savings toward an extra inch of exterior foam instead, to get you up to R15 on the exterior. 3" of exterior GPS and mineral wool batts in the stud bays gets you to about R38 of R value using realistic numbers, and will perform much better -- due to less thermal bridging -- then putting high R per inch materials between the studs.
A smart vapor retarder on the interior will provide some extra insurance against potential future moisture issues in the wall, although with R15 exterior rigid foam, that interion vapor control layer isn't really needed.
Bill