Flat-Plate Heat Exchangers for Hydronics

This is a spin-off of a recent question about air-to-water heat pumps and whether glycol is necessary. It would seem one way to reduce the amount of glycol needed would be to use a heat exchanger to separate the inside and outside loops, and only use glycol in the outside loop. I’ve never used one, and I’m curious if anyone here has.
A quick Google tells me that a 20-plate heat exchanger like this one:
Water-to-Water Plate Heat Exchanger 20 plate for Outdoor Boilers
is rated at 80,000 BTU/hr and is only $130. The last time I bought propylene glycol I paid $26/gallon so it would pay for itself very quickly.
It seems like the only potential drawback is if there is a loss in temperature. With heat pumps the name of the game is temperature delta, so if the water you’re getting out is significantly cooler than the water going in that’s a drawback. But from what I can read good ones only have about a 1F temperature drop.
Thoughts?
GBA Detail Library
A collection of one thousand construction details organized by climate and house part
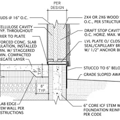
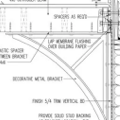
Replies
You also would need another circulator pump and isolation valves. Another $250 or so. Alternatively, one of the water heaters with a built in heat exchanger could do the trick (second link below). I don't think they are as efficient as the plate exchanger, but no additional pumps to worry about. A second advantage I see to a heat exchanger would be you could go to a much bigger buffer tank without a big glycol upcharge. This may offset the slight temp loss due to a heat exchanger. I think you need about a 40% mix in colder climates, so it adds up quick!
https://outdoorboiler.com/collections/pumps/products/copy-of-outdoor-boiler-circulator-pump-standard-1-6
https://www.mbtek.com/products/stainless-80gal?currency=USD&variant=11679592382507&utm_medium=cpc&utm_source=google&utm_campaign=Google%20Shopping&gclid=CjwKCAjwx7GYBhB7EiwA0d8oe8tCbejxDulKP21coKf7Thf3UYoZ94sUbva7vJfY7M9LBGOHnC_sOhoCxKMQAvD_BwE
I'd be curious about your thoughts on a Taco XPB for a situation like this. https://www.tacocomfort.com/documents/FileLibrary/X-Pump-Block.pdf
It's more expensive than the flat plate heat exchanger the original poster mentioned, but also incorporates the necessary pumps, and seems to be a good setup for a "two isolated loops" system. It strikes me as a pretty elegant solution, though I've only discovered it recently and don't know about drawbacks it might have.
I only came across it in researching the possibility of using the SANCO2 system. I'm not a professional, and only have done way too much reading in preparation for my own house.
It is a neat setup. From what I can see, it's all the components you need to do exactly what the OP mentions, in a package deal, including controls. Deal might be a stretch though... They are around $2000. It's one of the reasons I wouldn't go with a SANCO2 system, they require the xblock for warranty if you want to do radiant heat. The cost of it is too much to justify what it is in my opinion. It may be more DIY friendly since all the control is self contained, and it's compact. It could be very good if you are retrofitting a system where just a water heater existed before and you wanted to add on a radiant portion of your house. Which is basically what the SANCO2 is setup to provide.
I kind of asked the question to help with my own thought process. Putting this response together with my own post #7, I kind of get the feeling that it's not worth doing if you don't do it right, and doing it right is expensive -- in the ballpark of $2k for instance.
The companies that are serious about this will give you charts or calculators that allow you to figure out what the ΔT will be for a given flow rate and BTU/h. And they will tell you the pressure drop for a given flow rate for sizing pumps (you need two). What you will find is that that 80,000 BTU rating is for a huge temperature difference between the two sides, e.g. 60 F, and a brisk flow rate that incurs substantial pumping energy loss. There are cases in which they are useful, but getting a low temperature drop and a low pressure drop will mean buying a big, expensive one, at which point more glycol is probably cheaper.
You'll need to oversize the plate HX by a fair bit from their nameplate rating to get decent temperature drops. I use a 200k rated unit for my indirect running at 20k and even with that there is a bit too much delta T.
The other problem is the flow rates are hard to balance. If you want good delta T on both sides you have to get the both flow rates spot on, if you over-pump one side the mean temperature will be about the same but you'll run much lower delta T.
Getting the delta T right is doable with fixed flow setup, the only way to do it with variable flow is with a delta T circulator (ie Taco VT2218). Thinking about it some more, I'm wondering if over pumping the whole setup on both sides might be slightly higher efficiency. This would reduce the outlet temp on the heat pump for a small increase in pumping losses.
For something like this, I think what would make the most sense is a two coil indirect tank. Run the ATWHP into the lower coil, space heat through the tank and DWH pre-heat from the upper coil. This way no extra pumps or controls are needed and you also get a buffer tank.
I think there is some advantage to having a separate tank for DHW. All of the heat pumps run quite a bit more efficient at 100*F vs 120-130*F, so you can use a 3 way valve to have the HP run at 130 for your DHW and at 100 for your radiant. Either way, you are buying two tanks. If you have a low temp radiant system at least. You have the advantage that your radiant only tank can switch over to cooling when desired too. If you need the the hotter water for both, then just combine with a dual coil tank, saves space in your mechanical room too.
I think no matter which way you go, you'll need a booster to bring the DHW up to proper temperature. Assuming a heat pump booster, if the pre-heat is outputting 90F or 120F water, the overall energy cost is close enough to not matter. The extra tank is never worth it. Actually, neither is the pre-heat unless you get it for near zero extra cost.
With a heat exchanger there are three rules:
1. The leaving water can't be hotter than the hottest entering water
2. The leaving water can't be colder than the coldest leaving water
3. The heat flow on each side has to be the same
If you want to have the same temperature delta on both sides you have to have the same water flow on both sides. So let's say you've got water entering at 100F and 120F on the two sides, and you want it leaving at 120F and 100F, the only way to achieve that is with both sides having the exact same GPM. This is important because with a heat pump keeping your temperature deltas up is the name of the game.
In our discussion about different buffer tank plumbing approaches it became apparent that there are benefits to having the heat pump feed the heating sources directly, rather than through a buffer, so that the hottest water coming out of the heat pump goes directly to the heating sources. If you have the heat exchanger going into a buffer tank is lost. So the arrangement I'm thinking of is heat pump direct coupled to heat exchanger, and output of the heat exchanger going to the heating sources and then into the buffer, and the output of the buffer being the input to the heat exchanger.
In order for that to work optimally the water flow on both sides of the heat exchanger has to match. What becomes tricky is that the flow through the heating sources varies depending on the demand for heat, and the heat exchanger is feeding the heating sources directly. So there needs to be some way of matching the flow.
If the heat pump has a constant flow rate then a constant flow circulator on the heating side could potentially do that. However, the heat pump I'm using, Chiltrix, has a variable flow rate depending on temperature and demand. So that's where I come to a dead end.
You can use the Taco Delta T circulator to match the flow rates. Set it up to keep about the same delta T as your heat pump and should adjust the flow automatically as it ramps up and down. If I remember correctly the CX has a relay output on the circulator which you can use to turn the Taco pump on at the same time as the built in one.
There is generally no issues with feeding into a buffer tank as long as you can avoid mixing. If the flow rate is small enough and the tank is big enough the water will stratify. If you put 120F water into the top of the tank, you can draw the same 120F water out a couple of minutes later. There is some initial mixing if the tank is cold but a tank will very quickly stratify. I've definitely seen this with my indirect. 5GPM is a lot though which might mean a pretty big tank.
I think I need to do some modeling. If your thermostats are calling for all hands on deck because it's five degrees below your design temperature outside, you don't want to be limiting flow artificially to maintain a delta, you want to be pumping as much water as possible so you're moving as much heat as possible, delta be damned.
OK, I did some modeling. Basically it quickly became evident that with a flat plate heat exchanger you always want the flows on both sides to match as evenly as possible. The maximum temperature delta possible is the difference between the inputs on the two sides. With equal flows you get that delta on both sides, with unequal flows the side with less flow gets that delta and the side with more flow gets something less. So the amount of heat being transferred by the heat exchanger is reduced. Also, on both the heat pump side and the radiation side the bigger the delta the better.
I'm using a Chiltrix heat pump, which has variable flow. It has a voltage output that is scaled to the current flow, it's meant to be used with a second circulator inside the house if the internal pump can't provide enough. I'm going to read up on it and reach out to Chiltrix and ask if that output can be used to match the flow through a heat exchanger.
I agree with oversizing the heat exchanger. I've sized these a few times for economizer systems on large chilled water plants at work. What these systems do is run water from the cooling tower through the heat exchanger to cool the building chiller water system directly without needing to run the chiller ("chiller" is analogous to "compressor" in a residential A/C system). The end result is significant energy savings when the outdoor temperature is cold enough for the system to work. Sometimes conditions are right that the heat exchanger can pre-cool the water entering the chiller, which reduces the load on the chiller. It's all a BTU and flow rate game, which is usually programmed into the energy management system that runs the cooling plant. These heat exchangers are pretty massive, about the size of a midsize enclosed U haul trailer.
Anyway, the basic rules are BTU flow from one side to the other, which is dependent on a combination of flow rates and thermal deltas. Lower flow means more temperature change, higher flow won't get the temperatures of the two "sides" as close, etc, assuming a constant BTU transfer. In the cooling systems, we use the heat exchanger to keep the really nasty cooling tower water (which is open to the atmosphere in the cooling tower) seperate from the treated water in the indoor chilled water pipes. Other common uses are to seperate potable water from heating water, and to keep differently treated water loops seperated.
Glycol is only needed when there is a risk of freezing, but keep in mind that "glycol" often also includes corrosion inhibitors, which you still need to keep your piping and associated components from rotting away. Heat exhangers are great if you have something like that economizer system I mentioned that only runs ocassionally, or any other system with very different water systems on the two "sides". I don't see any reason why you couldn't use it the way you want to. The small temperature drop isn't much different from a run of pipe, and doesn't usually contribute much to total system losses. Note that you can insulate heat exchangers too, which can sometimes help.
Bill