Flat roof mid-century house with dropped ceiling
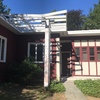
Hello – Thank you for the extensive resources your provide across the various insulation spectrum. I have read these both extensively:
Insulating Low-Slope Residential Roofs
How to Install Rigid Foam On Top of Roof Sheathing
I am in climate Zone4 (westchester NY) and have a 1955 build, flat roofed mid century house which has had a new roof installed (existing decking, +new felt pad+2″ polyiso+EPDM membrane). Yes, I should have gone with 4″.
The walls are concrete block, up to 10ft heigh, and 2×10 joists run across the block creating a 4ft overhang all around the exterior. The soffit this creates has a 1″ vent running around the entire perimeter. The ceiling is framed for a 9″ height (drop ceiling) using 2x6s, leaving about 14″ between the ceiling framing and the bottom of the roof joists. It also had a whole house fan (60″!) in a doghouse which has been removed and roofed over.
So it was historically a cold roof assembly. Which leaked water miserably due to neglect prior to purchase. upon taking down wire+plaster ceiling and stripping the tar and gravel, we found no rot amazingly, so seems the venting was working properly for last 70″ years, though the 4″ batt was disintegrated at this point.
considering we only have 2″ iso on top, and considering the 150+ openings created by the joists-on-bock to the vented soffit, what is best way forward?
1. adding 2″ closed cell right on the underside tongue-groove, 2″ all around in the 150+ openings and down the block wall to ceiling height creating a conditioned interior, then add another 8″ of open cell? Im concerned that we wont get a proper seal between the joists and block wall at overhangs. Also would leave about 19-20″ of conditioned space before sheetrock ceiling.
2. add 12″ + of open cell insulation to really get into all the nooks+crannies of the openings/vents, which would provide some vapor permeation around the ends. this would also enable the foam to continue over the bottom of the joists to assist even more in reducing any thermal bridging (again, only 2″ iso on top). would leave about 15″ of conditioned (if i can call it that with open cell) space between sheetrock ceiling and foam.
3. Just never think about the 2″ Iso on top, consider it lost, and re-create the cold roof assembly but with modern insulation between/around/over the 2×6 ceiling rafters and rely on the seemingly functional venting designed 70 years ago. if so, whats best here?
Additional notes: No Ducting. All mini-split Mitsubishi units and cast iron baseboard heat. There are to be about 30 IC rated can light housings throughout the 1700 sq ft home.
Thanks, apologies for the novel.
Its just such a unique setup im driving myself crazy. but less crazy than a moldy, rotten roof would make me.
-Jon
GBA Detail Library
A collection of one thousand construction details organized by climate and house part
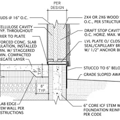
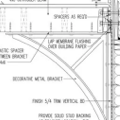
Replies
In zone 4 as long as ~30% of the total R or more is on the exterior it's fine from a dew point control perspective. You have R11.4 (if fiber faced) or R12 (foil faced) foam up top it means you're good for up to R28 under the roof deck before it's a dew point problem.
Some fiberglass R30s compressed to 9.25" in a 2x10 cavity performs at R28 which is good enough if the polyiso is R12:
https://www.energyvanguard.com/sites/default/files/styles/panopoly_image_original/public/owens-corning-compressed-fiberglass-insulation-r-value-chart.png?itok=jq3gsGh8
If you're concerned about polyiso derating or some fiberglass R3os actually hitting R30 at 9.25" (the way they should have all along), a flash-inch of HFO blown closed cell foam on the underside of the roof deck and compressing the batt into 8.25" would give both a reasonable ratio at the foam/fiber boundary, and a sufficiently low vapor permeance to the roof deck to protect it from wintertime moisture, while still providing a drying path. In that stackup you'd have:
R12 polyiso + R7 HFO blown polyurethane = R19 outside the fiber . Even if derated to R5/inch for temperature, the you'd have R17
R17 is sufficient dew point control for up to R40 of fiber on the interior. R30 rock wool batts designed to fit perfectly into 7.25" framing bays (2x8s) could be snugged up to the flash foam and you'd be golden. It would be R49 (labeled), but even if performing at R47 due to polyiso derating would still meet code on a U-factor basis due to the continuous polyiso thermal break over the rafters. Alternatively R39 fiberglass compressed to 8.25" would perform at about R32, still plenty of dew point margin. To keep it from shedding fiberglass stapling PERFORATED radiant barrier to the underside to compress the fiberglass into the cavities would still offer a drying path, and add another R1 to the overall performance of the assembly. (Perforated radiant barrier typically runs ~5 perms, about the same as latex paint, and won't create a moisture trap.) A bit of pillowing would be fine- even at 11.25" of loft an R39 only performs at R37, not enough to over-run the dew point control.
In my area a 1" shot of HFO blown foam runs about $1.40 per square foot if only doing ~1500 board-feet.
Even with rock wool or fiberglass batts + radiant barrier that has to be cheaper than 12" of open cell foam, or a 2" closed cell + 8" open cell solution.
Jon,
Dana gave you good advice. You are going to end up with an unvented roof assembly that follows the rules provided in this article: "Combining Exterior Rigid Foam With Fluffy Insulation."
So your most important job is coming up with a good detail to seal the soffit vents (and to prevent air leakage above the top plates of your exterior walls). Cantilevered rafters are bad news when it comes to air leakage -- but use a lot of closed-cell spray foam, and do the best you can.
If you don't have blocking between the rafters above the top plates of your exterior walls, you'll have to install blocking (either 2x10 blocking or rigid foam blocking). Then seal everything up with closed-cell spray foam to limit air leakage as much as possible.
Don't forget to insulate the walls between your dropped ceiling and your rafters.
Thanks to you both Dana and Martin for those poignant responses.
Ideal situation is another 1" iso on the underside of the roof decking, but what about the area between rafters and top plates of exterior block wall? wouldn't i need 2-3" there to create a vapor barrier? Am i trying to provide a vapor barrier there on the sides? At some point the sides become the top therein! I guess a better understanding on thermodynamics would come in handy on my side.
could i just use 14" of open cell foam there with 2x10 blocking (set back so the foam runs from roof decking to top of and over block wall, and down block wall to ceiling 2x6 framing)?. this setup would allow some vapor permanence thought that area i would think, but no air permanence. should I be as concerned with vapor permanence through those openings between rafters and top of block wall?
Im wondering if solely blowing sufficient open cell there will suffice
Thanks again, Jon
Don't use 1" polyiso on the under side of the roof deck- only closed cell spray foam. Foam board can't be made reliably air tight, and leakage around the foam board can create problems in the roof deck. Foil faced polyiso is also extremely vapor tight, creating a moisture trap.
A 1" layer of 2lb spray foam is about 1-perm, on the edge of class II & class III vapor retardency- enough to protect the roof deck in your stackup while still letting it dry, and it's glued continuously over the entire surface to the roof deck, with no possibility of air leakage. (In Canada 1 US perm qualifies as a "vapour barrier" under the National Building Code.)
Why not just ignore the 2" foam on the roof deck and put a foot of cellulose on the 2x6 rafter ceiling, leaving the attic vented? Cheap and easy, and you don't have to worry about the vents, cantilevered rafter details and all of that complexity.