FPSF – Superinsulated slab
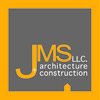
I’m finalizing the details on a build I’m starting at the end of the month using a FPSF and super-insulated slab.
Project is in climate zone 6B. I previously posted when this project originally began (before it got shelved for awhile) regarding Alan Gibson’s details and the vapor barrier under the slab.
Attached is the detail of the footing/slab and sub-slab insulation. My question is regarding the wings of insulation at the attached (unheated) garage. Do they really need to be as wide as prescribed by the NAHB guide? Does anyone have any experience with attached garages and providing less wing insulation?
I’ve gone through the NAHB revised FPSF guide for a heated & unheated building in my area with the Air Freezing Index & Mean Annual Temperature. Using the unheated approach the guide recommends I have 49 inches of wing insulation @ R6.8. I’d much prefer to just continue my R24 of insulation 24″ beyond the slab/footing edge. I didn’t see anything in the guide really giving advice on how to reduce the width of the wing insulation if you are using a higher R value of insulation.
My plan around the heated portion of the house is 6″ of R24 EPS continuous under the slab (and out beyond the slab/footing by 24″) connected to 4″ of vertical R16 EPS. The 4″ of insulation will be continuous between the house & attached garage but on the exterior edges of the garage I won’t be doing any vertical insulation. My plan was to just extend the 6″ of EPS under the entire attached garage and extend out 24″ all the way around just like the house. It’s not that big of a deal to go out another 24″ but it just feels like overkill to me and the way the layout works best it would mean lots of rip cuts in 6″ of foam (no thanks).
I already know that it’d be way easier to just detach the garage so it wasn’t connected to the house (believe me I tried to convince the client over and over again) but that’s not an option.
Any advice or guidance is much appreciated.
Thanks.
GBA Detail Library
A collection of one thousand construction details organized by climate and house part
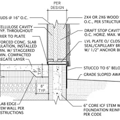
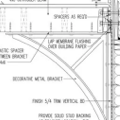
Replies
JMS,
You'll probably have to consult an engineer, who may be unnecessarily conservative.
I have built thickened-edge garage slabs in northern Vermont with 2 inches of sub-slab foam, 2" of vertical rigid foam at the perimeter going down 2 feet, and no wing insulation. In my experience, these foundation work well, as long as they are built on lots of crushed stone (8 or more inches) and have good drainage in all directions -- no standing water or problems with uphill slopes.
The problem with an attached garage is that it can't settle one inch or heave one inch like a detached garage can, without causing problems. Detached garages are more forgiving. You're going to have to assess the risk yourself, or with the help of an engineer.
JMS, I have been in the same situation a few times, as a designer, and have always ended up recommending either following the NAHB worksheet recommendations or just using a frost wall. In one recent case the builder decided to go with an approach like Martin suggests, which does not meet code but will probably be fine as long as the substrate drains well. In the other case I'm not sure what the builder did but I think it was something like you are suggesting.
On another note, the G•O Logic (Alan Gibson's) foundation detail is great, but you should be aware that it is patented.
Thanks Martin & Michael. I appreciate both of your responses.
Martin - I have the exact same worry about the garage settling or heaving just a slight amount which would probably end up wrecking the air seal between them. I'll probably end up just following the guidelines with a less density foam to extend the wings out to 49" and I'll at least have peace of mind.
Michael - If building a frost wall didn't mean having footings sit in water during seasonally high water season I probably would have looked at something like that. The first reason I headed toward the FPSF system was that the property is in the river bottom and it's not uncommon during high water years for the ground water to get ~36" below the surface of the ground. Thankfully though we have incredibly well draining gravels everywhere under the topsoil. In regards to the GO Logic system I'd say that my foundation doesn't quite match either of the systems they detailed in the JLC article you are probably also thinking of. Their website shows the patented system but it looks like more of a foam slab edge form work system to me.
JMS,
Are you including perimeter (French) drains? If so I'm curious as to where the best place to situate them is in a FPSF like yours.
Malcolm - No plans for perimeter drains on this project. Since the EPS will be the lowest item below grade (and really only 18-20" deep) - I don't see any need. We'll be built-up from all the adjacent grade and will have positive drainage away from the building everywhere. We built a barn on this property last year so we know what our subgrade looks like and standing water just doesn't exist since it just flows right through the top soil and into the gravel layers. For example we dug in drains for all the barn downspouts and just ran a solid 4" pipe about 2 feet out from the building and 18" deep into the existing gravel layer and have had no issues whatsoever with the water just draining away.
I'm not sure there would be much point to a perimeter drain on an FPSF unless you were building on a slope (and then would a FPSF make sense anyway) where you would possibly have water draining from high ground toward your building.
JMS, I'm using a FPSF on a current project for the same reason of a high water table.
At the NESEA conference last week, David White presented an interesting, cost-effective alternative: pole building construction, with a raft slab floating inside the structure. The presentation was for low-cost Passive House construction, but my immediate thought was that the same system could be used for attached garages. (I believe Martin was in the same presentation.)
I'm not aware of the JLC article on G•O Logic; I live near them and used to work for a competitor, so I am familiar with some of their details. The key to their system is the one-piece perimeter, but if you read their patent verbage (I have but can't locate it right now) it also covers similar systems. I don't think you need to worry (but I'm not an attorney either).
JMS,
Thanks for the reply. I know you are here to get answers, but if I could ask you one more question:
Most of the FPSFs I've seen posted here have an integral thickened footing on the perimeter of the slab. Is there a particular reason you decided to separate the two? It would seem a lot easier to form and compact doing it your way, but I wondered if there were other reasons too.
Michael - We did a post-frame building for the barn but we went with perma-columns on the bases of the columns because I just didn't love the idea of building an expensive barn and having the columns submerged for part of the year. The perma-columns are basically a concrete base with a steel connection on top and they worked out great but added a little extra labor and about $200 per post extra. Needless to say they got expensive quite fast. It's an interesting idea for an entire house....
Malcolm - I worked with my engineer and talked with my subcontractors about what they thought was best before I came to the detail that I attached. Basically my concrete sub doesn't like to pour huge monoslabs if he can help it so that they can better control the finish. We're also using integral color so not coloring the footings is nice. I also have quite a few interior footings. In the end I liked the idea of being able to pour a more conventional footing over the foam (with really tall anchor bolts) and then do all the sub-slab plumbing and other sub-slab work inside of that footprint. I have an alternate detail to pour it like a monoslab and am still in discussion with my concrete sub about what will work best. I'll post again once we have fully determined which direction we're going.