Gothic arch cabin, roof/wall layers?

Hello,
I plan on building a 20ft x28ft gothic arch cabin in two years. Imagine the building like a A-frame cabin, only with a ballooned/curved roof/wall.
My plan is to install 3×6 inch curved beams at 24inch center as studs/rafters. On the interior I would install a poly vapor barrier, covered by horizontal tounge and groove boards. I was going to fill the cavitys with fiberglass batt insulation, topped with housewrap. Next, I would install 2 inch thick vertical furring strips on the studs/rafters, followed by plywood over the entire surface. On the plywood I would install underlayment and shingles. On the ridge I would install a ridge Vent along the whole length so the air can ventilate between the housewrap and the plywood. (There would be a air inlet vent at the bottom between each beam.) I hope my description is understandable.
Here are my questions:
Do the layers make sense?
Is there a major flaw in my thinking?
(I would be located on the Westcoast of BC, climate zone 7b and air conditioning is not planned)
The difficulty for me is that the surface is a fluid transition, from roof to exterior wall and traditionally, when build separately, they are also layered differently. The plywood that provides most of the shear strength would be in my case part of the roof layer instead of being under the housewrap. Is that feasible? Is housewrap enough of a layer to keep the fiberglass insulation safe and secure in place? I would like to avoid two layers of plywood to save time, money and weight.
Any help or thought would be much appreciated!
Cheers!
GBA Detail Library
A collection of one thousand construction details organized by climate and house part
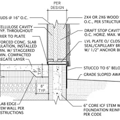
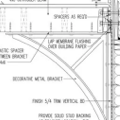
Replies
Daniel,
- I don't see any problems with your layering, which would work both on walls and roofs.
- The plywood as shear-wall is fine, as it is directly connected to the hybrid stud/rafters by the continuous vertical furring.
- The house-wrap will work to contain the batt insulation.
Two code complications:
- The 6" of insulation isn't adequate for either walls or roofs in Climate zone 7b.
- Falling outside the prescribed methods of framing in part 9, the arches will require engineering.
attaching poly to the underside of curved framing seems like a big constructability challenge. i can imagine the movement of the slack plastic to negatively affect the long term durability of the air barrier. You could use battens over the plastic attached to the curved framing but still seems challenging. i'd consider thin plywood or osb screwed to the framing to conform to the curve. tape seams and use a liquid applied air barrier under the T&G.
Thank you guys for the reply! I should have mentioned that the property where this cabin would be build in the future, is very remote and has no zoning. That is the only reason why I consider a gothic arch cabin, it would be too much of a headache for me otherwise with engineered arches, inspections and the financial aspect of all of that. I love the look and I have experience in glue laminating large arches, so I feel comfortable to build the framework. I just realize that I got the zone completely wrong. It is actually zone 5. Is the 6 inch fiberglass insulation still not enough?
I agree that installing a poly vapor barrier on the interior of the arches would be very challenging and I love the idea of a liquid applied barrier on sheet goods. I wonder if I could use 3/8 beaded plywood instead of tongue and groove boards, with the barrier applied to the exterior facing surface, tape the seams from the exterior and cover them with decorative beams or strips on the interior?
Daniel,
"Is the 6 inch fiberglass insulation still not enough?"
Practically, any amount of batt insulation works to keep the assemblies safe. It's on the low side, meaning you will use more energy heating, but with good air-sealing it should be fine for an occasional use cabin. It won't meet code, and it's worth noting that the BCBC is enacted province wide, whether there are inspections or enforcement in an area or not. Lot's of people build non-conforming houses in remote areas not realizing that.
Thanks for the reply Malcom. I might have to consider to increase the R value somehow. Also, thank you for pointing out that I technically do need to build to code, no matter how remote it is, I had no idea. Some properties I looked at have been even advertised online by real estate agents as "no permit needed". I guess in reality, it never will be a problem where I plan to build, but I do believe using the code as a guideline is important since they have been put in place for a good reason.
Daniel,
In most remote areas I'm not sure it matters much. I have a few friends with hunting cabins up by PG, and none of them are anywhere near code compliant, but it seems like there has been an uptick in stories about regional governments cracking down on non-conforming structures recently.
Deleted
The plywood over furring strips won't work as bracing. You need the sheathing directly attached to studs. There are other ways of bracing walls though.
My suggestion would be to go with say 1" interior foil faced polyiso instead of the poly. You can tape the seams of it to form a solid air and vapor barrier plus you can still nail the T&G up with 2.5" nails. In the corners, put interior plywood to brace the walls and 1/2" interior insulation over that.
This would get you at least close to code min R value assuming you use HD batts in the walls.
Akos,
I'm not seeing an appreciable difference between the plywood being directly nailed to the arched structure, and it being nailed to the vertical furring which is nailed to the arches, as long as there is an aggressive fastener schedule.
I haven't checked that part of the code in detail, I just always assumed the bracing needs to be attached directly to studs. The furring does add an extra hinge point, don't know how much that matters. I guess if ZipR can work, this is not that far off. I'm not sure if it pass prescriptive code though without an engineers stamp.
Akos,
I guess the devil is in the details. You are right - if the 2" deep strapping isn't at least that wide, it would have some instability. I'd be interested to hear how Daniel plans to build the furring to match the arched shape.
My plan is to glue-laminate the furring strips as well. In my experience 1/2 inch thick strips work well with arches that size. Since the arches are fairly big, I have to connect two strips with finger joints. Using four 1/2 inch strips for the lamination will allow me to overlap the joints. As this discussion makes clear, it should provide a strong enough base considering the intended use. I believe the width and thickness will achieve that. As pointed out, an aggressive fastening schedule is mandatory. Additionally I would varnish the strips. This might sound like overkill for something that is not even visible but I think it would help a great deal with longevity.
I am really thankful for all the constructive input, it is a rare pleasure to communicate with intelligent individuals!
Daniel,
Sounds like a fun project. I've stayed in arched units in Tofino years ago. I liked the feel. It's a shame you couldn't expose the glu-lams inside, but that becomes more complicated.
I actually think about increasing the dimensions of the arches to be able to accommodate more insulation from 3x6 to 3x10. Since the glue-up process is already quite complicated and time consuming, it might be worth to consider to go the extra mile and add 1.5 x 1.5 inch strips on each side of the arches, set back from the inside about two inches or so. That would give me something to nail the paneling on while keeping the beams visible. And in that scenario, I would have two more inch depth for insulation. It does add complexity but could be worth the look.
Speaking of building the arches. I am used to work with spruce, pine and balsam fir when it comes to framing. As of right now, I live in PG. I never worked on the coast. I know the mentioned species are not very rot resistant without treatment. The humidity is much higher on the southern west coast of BC, therefore a higher risk of rot and mold, I would assume. Do people still frame with SPF on the coast?
Daniel,
"Do people still frame with SPF on the coast?"
Yes. Although it is damper here than most places, the only threat to the framing in a well designed wall is water intrusion from the outside. If the walls were experiencing enough moisture that you couldn't use SPF lumber, the rest of the assembly would be in big trouble too.
I've renovated a lot of houses here of various ages. When I do see rot or mold, the source is always apparent. It's mainly poor exterior detailing of the cladding, especially around openings, or less commonly lots of air-leakage from the interior coupled with a poor drying path. We have had rain-screens here long enough that I've had the chance to open several walls that had them, and they looks brand new.
Ensuring the housewrap is correctly installed to protect against moisture, especially in BC's climate, is key. Opting out of a second plywood layer for cost and weight savings makes sense, provided the structure stays solid and dry. A quick check with a local building pro could offer extra reassurance. Sounds like an exciting build!