Heat loss calcs to cfm?

What is the best way to translate heat loss calculations to CFM needs per room?
I have used HVAC-Calc Residential to identify the heat loss for finishing my basement and now need to turn those calcs into cfm to determine duct sizing.
For the HVAC-Calc experts, the “HVAC-Calc CFM report” does not seem to be helpful in this situation as it wants me to designate the CFM of the equipement for the house. The furnace that will service this zone also services the rest of the house.
GBA Detail Library
A collection of one thousand construction details organized by climate and house part
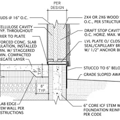
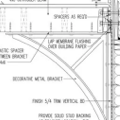
Replies
Bob,
OK, you've performed your heat loss calculation. Now you need to design your duct system.
The usual advice is to use a method from ACCA (using software) called Manual D. For more information, see these two articles:
All About Furnaces and Duct Systems
Trouble-Free Forced-Air Heat
Taking it to the crude fundamentals:
Most condensing hot air fossil burners will deliver 120-130F air, and the presumptive return air to the furnace is usually 65F, so it's a ~60F temperature difference.
Every cubic foot of dry air has a thermal mass by volume of ~0.018 BTU/cubic foot per degree F, so at a 60F temperature difference that's
0.018 x 60F= 1.08 BTU per cubic foot.
every cfm = 60 cubic feet per hour, x 1.08 BTU/ft^3 = ~65 BTU/hr per cfm.
So a room with say, a design load of 2800 BTU/hr the room would need a minimum of 2800 / 65 = 43 cfm.
That is assuming it's a lossless duct system with no leaks, magical R-infinity duct insulation, and outdoor temps that never exceed design conditions. Real ducts leak and have real world insulation, and heat loads sometimes exceed design conditions, so if you're doing stick in the dirt or lipstick on mirror type system design, add ~15%, call it 50 cfm, or go hog wild and design for 55cfm, and put a balancing vane in it for dialing it back a bit.
Oversizing the ducts is generally preferable to undersizing, but gross oversizing ends up with lower velocity with less predictable performance so don't go TOO crazy on that. As long as your duct oversizing cfm is consistent throughout the system, the room to room temperatures will still have reasonable balance, and the amount of tweaking can be minimal.
Heat pumps often have exit-air temps in the 100-110F range, for a ~50F nominal difference rather than 60F, which requires 60/50= 1.2x more cfm to deliver the same amount of heat.
Minimum-legal efficiency "scorched air" fossil burners typically deliver temps in the 150-160F range, for a nominal temperature difference of ~90F, and can get by with (60/90=) 2/3 the cfm in the condensing furnace example.
Flex duct of any significant length that isn't stretched tight has unpredictable duct impedance, and is the bane of the industry. Hard-piped duct work mastic-sealed on every seam and joint does a lot better.
Bob,
A common duct guideline is that a 6-inch round galvanized duct can deliver 100 cfm and 7,400 Btuh of heat. That corresponds fairly well with Dana's calculation. My rule of thumb is 74 Btuh/cfm, while Dana's is 65 Btuh/cfm.
As outlined 74 BTU/cfm rule of thumb works for 82-86% efficiency non-condensing equipment, but not for heat pumps or condensing gas furnaces due to the lower output temperatures.
Don't use rules of thumb, even with a stick-in-dirt cowboy design. This is why rules of thumb should be avoided:
74BTU/cfm is 23% more BTU than the 65 BTU/cfm derived from the 60F nominal delta-T, which implies an nominal temperature difference of 1.23 x 60F= 74F. With 65F return air that means 65F + 74F = ~140F, which is at the very low end of the output temperature range for non-condensing equipment, which makes it reasonably conservative for non-condensing equipment.
But 140F would be a the very HIGH end of the output temps for condensing equipment, some furnaces simply can't deliver that temperature, and thus it has no margin at all, even negative margin for many equipment models. If using 74 BTU/cfm (even when upsized by 15% per the recommendation in my prior post) it can still come up short with condensing equipment. It depends on the model, and the whole-system cfm passing through the heat exchanger.
Furnace manuals typically provide a minimum & maximum delta-T at one or more air handler speeds. I used a middle of the road 60F nominal delta-T condensing furnace in the prior analysis. Some 98% efficiency furnaces set up for only a 50F delta-T, with 115F-120F output, so clearly YMMV. The manual still needs to be referred to as part of the duct design to be able to design conservatively, even on a hacked (rather than fully engineered) design. The napkin-math version of the design doesn't lie, even if it's not the whole story.
Gentlemen, as I'm learning about this process I have a question regarding the math above.
Dana, you based your BTU/hr calculations on the DeltaT across the furnace heat exchanger (supply air temp - return air temp). Would it not be better to consider the minimum desired room temperature instead? Taken to the extreme, if my desired minimum room temperature was 120F, the same as the exit air temp of the furnace, then the furnace would be incapable of heating the room regardless of the DeltaT across the furnace heat exchanger.
More practically, if my minimum desired room temperature is 70F and my furnace air temp at the register is 115F (after duct losses), that's a DeltaT of only 45F and would require ~33% more airflow to cover the same heat load compared to your 60F example above.
Would this be a better approach, or is it too conservative?
BTUs are BTUs, and the delta-T is what is is. If you're intending to heat the place to 120F you WON'T be able to get there with condensing equipment- the return temp would be to high, and the safety temperature limit sensor on the heat exchanger would shut it down. It could be a challenge even with non-condensing furnaces for similar reasons- they're not designed for return air temperatures anywhere near that high.
But back in the 70F room temp reality, as room temp rises the return air temp rises too, and the delta-T across the heat exchanger remains pretty much the same when heating to normal space heating temps (south of 85F.) Furnaces don't regulate to an preset output temperature, (they only have a hi-temp limit, for safety) and the as-used delta-T is based on the cfm & firing rate.
Using the crude fundamentals from Dana (thank you for the write up) I am getting the following which is much lower than I expected based on other ducting in the house. Pretty much the whole hose is 6' with a mix and match of flex and solid as it is distributed through the ceiling of the basement. Supplies into the first floor get the 6" all the way to the boot, while 2nd floor supplies go into mostly solid oval duct. A couple of 2nd floor supplies likely leverage rigid (post oval) based on how they ducted branches in the basement.
I am working through a Manual J spreadsheet from acca.org now.
The Manual D spreadsheet from Acca.org is blowing up on the Friction Rate tab as it does not like the external static pressure of .15 in. W.C. that Carrier publishes as the ESP. Also it is clear the Manual D won't like the fact that I am not performing calculations on the entire house (there is a lot duct buried in walls & floors that I cannot see). Providing info on my furnace/ac while only running calculations for the basement's projected ductwork is likely not going to work unless I am missing something.
Bob,
Another data point is the BTU output(of heat source)/blower rating in CFM. For most mini-splits that works out to be 50BTU/CFM. You should be able to get those "numbers" from your existing system. Apparently that existing system is set up for 0.15" WC static pressure on the blower. You will/ may need to change the blower speed to accommodate the added CFM (depends on the blowers characteristics). Weather you'll need to re-balance the whole system depends an how closely your manual J coresponds the actual heat losses in the rest of the house.
75K/1085=69.12 . Changing the blower speed sounds to be a challenging task based on a few Google searches. The Manual J I currently have is based only on the basement.
Found more data on the blower cfm and IN. W.C., table attached.
The "Direct expansion refrigerant coil" value is based on standards I could find online. The table from the Carrier (attached) did not go up to the 1800 cfm rating that the furnace blower is set to use.
In the manual D I can now use .4 as the external static pressure and receive a friction rate that appears to be within acceptable limits (based on Notes in the Friction Rate worksheet). Table attached.
Does my friction rate table look correct?
Drawings of the basement, current hvac (pink & orange), and proposed (blues).
Existing main trunk based on cfm appears to be maxed out based on it's branches. The builder uses 6" rigid & flex duct for all branches (orange) off all trunks despite varying distances from furnace. The main trunk line (pink) does not step down as it gets further from the furnace (main run is 34', not factoring in the 5' from the furnace plenum to the trunk).
The blue proposed ducting is based on perceived cfm needs (not Dana's info as this drawing was made prior to that) and what the framing will allow. The 8"x10" trunk will actually have to be 10" round to allow for 90* bends.
Returns are not draw in, but are planned to be equal to supply on a per area basis. The rest of the house is on a central return based on the main floor. Not sure if that impacts if I need to do the same in the basement, but my plan is individual returns per space.
Bob,
You really don't know the current operating condition ie. what static load the existing ducts are giving. I'd buy a manometer and measure the static pressure between the blower and the AC coil.
However, from the data on the blower it could be any thing up to 1". It's VERY likely that the blower is set at the factory default settings still the current system flow rate is ?. But by using the coil data we can narrow the options to anywhere from 1090 CFM with no duct loss (very unlikely) to 765 CFM with ducts taking 0.89" WC. Because of the blower characteristics, when you add the new ducts the static pressure will fall and the total flow will go up. Just do it!
Once I have the correct static pressure, will i still be able to move forward without all the details of the ducting in the rest of the house?
Do I need to get a specific type of Manometer? Or fancy tips for it? It looks like locally I can only buy/rent the kind that uses a tube with fluid. Amazon seems to have some decent looking digital offerings at a reasonable price.
Bob,
Please ignore my desire two own a manometer!!!! You don't need one either!
In you initial post you said the existing duct work is " maxed out" WHY? IMHO you have a much simpler & cheaper alternative, forget adding.the big blue duct and simply add taps to the light magenta duct., at worst you'll have to re adjust some registers to re-balance some of the existing system.
Jerry,
I have one ready to buy in my Amazon cart. Just waiting to confirm if I need any accessories. If I am going to learn this much, I should at least get to buy some tools. :-)
I would not mind taping off the magenta trunk. I was told based on cfm calculations of the branches summed they are equal if not greater than the capacity of the magenta trunk.
Putting previous cfm assumptions aside, the idea of having the basement trunk completely separate is nice since in the summer I will want it completely blocked for AC. But maybe I am overthinking that value.
Cockpit error! Please ignore duplicate post
Bob,
I agree, you have earned a new toy (tool?)!
"Capacity" (better called flow rate) of any duct segment is changeable! If you need more "capacity" the price is more friction loss (measured as pressure drop) in that duct segment which is why you may need to " re-balance" the flows. The "no blue duct" summertime solution is close, or block, the individual registers.
So save the cost and space of a separate trunk and tap into the magenta trunk because if more capacity is needed it would be accomplished by balancing dampers (the ones at supply boot) throughout the house. And if more capacity is needed throughout the house, then we would be talking about increasing motor speed...which would be done with delicacy as to not reduce the temp of the heat exchange outside of specs. Right?
My other "thought" is that the separate trunk could allow for a separate heat supply if needed in the future as it will never get easier than today to add that separate trunk. Plus if adding these runs completely throws off the rest of the house and balancing the house does not achieve desired results, I could shut the damper the "basement trunk" and only open it when needed. All that said, gaining 10" of ceiling space back from the soffit would be fantastic.
Anyone else agree that I should use the large main magenta duct for the basement? I need to start framing the soffit asap.
Bob,,
You cannot and MUST NOT change blower taps! The tap you're on is the highest allowed for heating, the only tap change you can do would ONLY be necessary if you had a much smaller load,. Your furnace will simply burn hotter and keep the same output temperature, it's as I recall, running at under 75% of capacity. Hopefully someone else will wade trough the data and come to the same result.
By blower taps I am assuming you mean the manual set speed (not an ECM). The manufacture indicates it be increased, for heating, from the low-medium setting it is on. There are two more speed before full power, which is what the AC uses.
I do agree the speed cannot be lowered. Doing so will likely cause the heat exchange to overheat which would shut the furnace down and risk cracking the heat exchange.
No I am not trying to change the speed right now. Just looking to confirm my options if I choose to skip the extra trunk (which seems like a perfectly fine idea).
Bob,
Your furnace's ratings & characteristics are in a note on your duct layout ( the color coded one). What that rating says is: the upper capacity limit is 1080 CFM, less flow is fine, more is NOT! This is because the furnace control system adjusts the fuel input to maintain a constant temperature of the output air. More flow means more fuel in and more heat out but the air temperature is the same.
"I do agree the speed cannot be lowered. Doing so will likely cause the heat exchange to overheat which would shut the furnace down and risk cracking the heat exchange"
.
IS BACKWARDS! The speed can safely be lower to completely shut off! The lower speed tap could be used, the TWO higher speed taps NO! Above 1080 CFM too much fuel would be needed and efficiency would drop and pollution would rise!!
The Carrier 59SC2A is single stage gas furnace, sometimes coupled with a single-stage heat pump as a "dual-fuel" unit. Neither the heat pump nor the gas burner modulate to control output temperature- they're either on or off:
https://www.astardfw.com/files/5-8377.pdf
Lowering the blower speed below some point will cause a safety shut down, running the blower at maximum is not a problem. The higher speed would lower the overall temperature of the heat exchanger, but a lower speed doesn't deliver a significant blow to efficiency- the incoming return air is still well into the condensing range at any blower speed.
It's not clear why the 80KBTU version was selected- what is the design whole house heat load?
.15 wc on the diagram is wrong. The WC from the table is correct.
Measured esp, I am seeing about .55 in wc when heating.
Dana, house was projected by builder to have a heat loss of 61,159 btuh.
A design heat load of ~60K certainly calls for an ~80K furnace rather than a 60K furnace, but is on the high side for most IRC 2015 code-minimum houses of average size. Most 2500' code min houses of reasonable air tightness will come in under 40K.
So the question is whether the Manual-J has credible input parameters. The tendency of most HVAC contractors is to skew heavily to the conservative side, which often ends up with numbers 1.5-2x reality.
Is there an AC or heat pump coil using the same ducts?
AC coil on top of furnace. Carrier CNPVP3617ALAAAAA . 3 ton.
static pressure drop rated dry @ 1000 cfm, .189 in. W.C. I measured it at .23 in. W.C. at unknown cfm while heating (assuming that is "dry"). Based on the static pressure and Carrier's info, my cfm is likely just below 1000.