Help me design a small building heating/cooling solution

Hi Folks,
My wife and I have just bought piece of property outside of the Boston, MA area (Zone 5a), and we will be building a home there next year (hopefully…just going through the close process). Currently on the property is an existing structure that I am planning on rehabbing, to use as a detached home office and workshop.
The current building is approximately a 250 Sq ft stick framed building (which I will be completely gutting and reinsulating, siding, roofing etc etc…it needs a LOT of work). The structure includes a little sink currently…a capability I will retain. It also has an additional roughly 18′ x 30′ foundation (attached to the framed structure/foundation) atop which sits a greenhouse currently. I will be removing this greenhouse and using the existing poured foundation to build a little workshop.
I’m working on all the framing plans etc, but I also need to start thinking about the heating system for this little structure. We expect to have natural gas for the new/main house, and this existing structure will be about 30-40ft from the main house. From a use perspective, I work from home, so I expect to be in the home office a good 8 hours a day throughout the year. The workshop will be a weekend only type of thing (not an industrial workshop), and I plan on insulting that as well. There will be a door that goes directly from the office, into the workshop. So, my thinking is to install something that can keep the office warm in the winter efficiently (probably 68-70 degrees), as if it were any indoor space. When i want to heat the workshop, I’m hoping to just open the door to the office and let the air in there circulate and heat the insulated garage. Since it’s a workshop, if I can get that area up to the 60’s, that should be quite comfortable. As I said, I plan on insulating the garage area, but it won’t be a space we will be using for ‘living’, so I just need to keep the chill out of the air.
My main concerns are probably the standard you hear…Upfront costs (we are building a house, so there is already lots of money flying out of the bank), usage costs (don’t want this little building to put me in the poor house every month during the winter), and environmental friendliness.
So, Green Builders, what do you think?
1) Is it worth piping gas out to this structure? As I said, it’s probably 30-40ft away from future main structure. Or is it more economical to go with an electric solution?
2) What would be some good options here? Maybe a mini split system for heating and cooling, and a little point of use water heater for the sink? I’d be interested in solar, but it is a snowy area and I have to think about upfront costs also.
Right now I’m very much in the planning stage, so just about every option is on the table…what would you do?
Any help would be much appreciated. Thanks!
Jon
GBA Detail Library
A collection of one thousand construction details organized by climate and house part
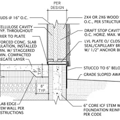
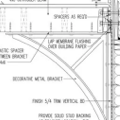
Replies
Jon,
At this stage of the game, you're emphasizing the wrong details. Planning a good thermal envelope is much more important than deciding on which kind of heating equipment to install.
Hi Martin,
Like I said, I'm very much in the planning stage, haven't even closed on the property yet, so I'm just trying to do my due diligence to look at options I have for heating...it will need something.
I didn't mean to imply I'm not thinking about the thermal envelope. Far from it...I'm looking at that at the same time (for both this building, and the main structure). For purposes of this discussion, you can assume this will be a well insulated structure (with likely a combination of rigid foam, and either closed cell-spray foam, or wet-spray cellulose, augmented with spray foam to stop air leaks first...depending on my budget, etc, etc, etc). I'm more of a pauper than a prince, so budget will influence everything at some level.
Mostly, I've never looked into such a small heated space such as this...everything I've read tends to be on systems sized for a full home, not a detached 250 sq ft space. I certainly don't want something grossly oversized, or something outrageously expensive if it's not needed. I also need to understand how much these options (roughly) will cost. $2,000...$4,000 etc? The amount of money I can spend on the thermal envelope will be influenced by the potential range of cost for the heating system and vice versa.
Not trying to put the cart before the horse, but right now...the cart is on blocks and the horse is just roaming the field ;)
JP
Jonathan,
You might want to read this article: Heating a Tight, Well-Insulated House.
Jonathan, I'm working on a similar renovation project, still in the design phase. If we can get the envelope tight and well-insulated enough, we will use an air source heat pump. For various reasons, including the up-front budget, I am not confident that we will get there. The backup plan is to use a small Rennai direct-vent space heater.
In order to make the decision you need to know what the energy use will be. If you don't know how to do an energy model, hire someone to help you. The model won't be 100% accurate but it will give you a good idea of the heating load. In a cold climate, air source heat pumps work best when they have plenty of time to defrost between heating cycles. A super-insulated and air-sealed structure is key, and a bit of south-facing glass, if at all possible, will help.
You also have to decide whether or not you want to burn fossil fuels on site. With natural gas available at the street it's tempting, but it's not necessary. With a heat pump you can plan to add PV panels in the future when you have some spare cash available; the ROI can be pretty reasonable but it can be phased in if cash isn't available right now.
Even building to a MA residential code min for insulation and air tightness you'd be able to heat a place that size with a 3/4 ton mini-split. Most 3/4 ton ductless will put out about ~14-15KBTU/hr at +5F, which is below the 99% design temp for the Boston burbs. (+5F exactly the 99% number for Worcester.) If you get a good one (HSPF > 10) the heating costs would be about the same as with natural gas, and you'd have air conditioning.
If you have reasonable shading factors and can orient the pitch of the roof optimally for PV, at the current MA and Federal combined subsidy (including the SREC market kickback) the simple payback is under 10 years for 2-5kw systems. With even a 4:12 roof pitch snow will glide off the smooth surfaces of PV panels on the first day of sunshine- you don't lose much wintertime uptake due to snow. The real PV bonanza is in June-July anyway, which hasn't been a very snowy part of the year lately... ;-)
If you want to go better than code-min on the building think about putting 3-4" of reclaimed rigid insulation on the exterior of the structural sheathing. It's pretty easy to hit R40 with a cellulose-insulated 2x6 wall and 3" of iso that's been removed from a commercial building, and it's about the same money or cheaper than going with 1" of virgin-stock goods. There are a handful of outfits trading in that stuff in eastern & central MA. (Some advertize in the materials section of craigslist- search for "rigid insulation". You can always get something from The Insulation Depot in Framingham if you have your own truck- see insulationdepot.com.) With an R40 walls and south facing windows optimized for passive solar, and < U0.25 on all the others the place will all but heat itself.
Dana,
I'm surprised at your statement: "With even a 4:12 roof pitch, snow will glide off the smooth surfaces of PV panels on the first day of sunshine." That's certainly not true for Vermont -- although it may be true (sort of) in the warmer climate of Massachusetts.
When it's 0 degrees and sunny, snow doesn't slide -- even when PV modules are almost vertical.
BTW: You can also insulate the foundation with reclaimed roofing foam, but it has to be EPS or XPS, not iso (unless it's on the interior side of a full-basement.)
Martin: In the Boston area the mean January highs are above freezing- it doesn't take much solar heating through even a foot of snow to get it moving there. I agree that it could stick for an entire winter in VT with a 4:12 roof. At anything much over 6:12 it will naturally slough and avalanche just from weight fo the snowpack eventually, but it could still take awhile. PV is a slicker avalanche surface than shingles (any type), but sticker than some enameled steel roofing.
I get to watch this process on the PV installations & I pass on my daily commute. There's one PV installation on a ~2:12 roof (Sudbury Senior Center, if you want to look it up) that sometimes takes 3-4 days to clear after a nor'easter, but almost all others are done in a day.
Thanks Dana,
That's exactly the information I was hoping for. I'll look at the 3/4 ton ductless systems. I like the fact that it would be heating AND cooling.
And what a great tip on the rigid insulation! I certainly want to use rigid foam, because I know bridge that the studs create in the wall...if I can get reclaimed for a fraction of the cost, that certainly helps! Cheers.
JP