Help needed from hydronic experts: Xpress Trak and other foam underfloor heating panels- Solid performance or low-performing shortcut?

Greetings all! I need a low profile underfloor heating solution in a planned ICF build in southern Colorado with a good amount of passive solar gain, but with lower parts of the building in heavy shade. It will be 4 stories, with a small footprint (28×22 ft). Right now I’m focused on the floor system. Floor system thickness needs to be minimal to pull off 4 stories under 40 ft total height. The ground-level concrete slab floor will be well-insulated and will have embedded hydronic heat. But for the upper 3 floors I’m thinking 6 inch steel C joists (12 gauge, wood will not span 12.5 ft with decent deflection), with 3/4 advantech or similar, then maybe Xpress Trak with 5/16ths pex, 1/4″ cement board, thinset, and porcelain tile (2cm thick maybe?). HRV ducting will be done through an interior service wall.
Question for the underfloor hydronic experts:
1. I know Xpress Trak and similar foam panels with thin aluminum foil facers are less effective at pushing heat from the pex to the flooring, but I don’t have a good handle on all the data out there covering that topic, and can’t really compare in any meaningful way- plus I don’t have any personal experience with hydronics. Just how bad are those foam/foil products at transferring heat, on a scale of 1-10 with 1 being the worst possible hydronic system and 10 being the best?
To answer a few possible follow-up questions: Why would I want to use Xpress-Trak instead of WarmBoard or another panel with thick aluminum? Cost. Xpress-Trak is less than $1.50 sq/ft, while WarmBoard is $8-$10 (CORRECTION- I mis-read the package specs for Xpress-Trak, it’s actually comparable with WarmBoard in cost). Also, I would much rather use hydronic instead of thin resistance electric (for obvious efficiency reasons) and because we will have solar panels, which I would like to use to heat water during winter days, and store that heated water until night, for use by the hydronics. I figure this is a much cheaper way to store solar energy than using batteries. Also I don’t want to pour concrete or gyp-crete on the upper levels because I don’t want to have very long temperature arcs on those levels, even though I know the additional mass would be more efficient overall. Finally, I like the fact that a low-mass system like Xpress-Trak would give me lots of flexibility since there’s no real way to know how ICF, climate change, passive solar, and other x-factors will affect hourly heating comfort until we are in the house. In other words, seems like it would be good for the system to be able to respond quickly to unexpected heat gain, and if we don’t need it at all on some level(s), the wasted investment would be minimal. So basically I’m trying to find out whether that type of system is so inefficient as to be “pointless”. Thanks!
GBA Detail Library
A collection of one thousand construction details organized by climate and house part
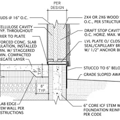
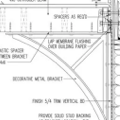
Replies
Are these being heated by a heat pump?
Yes
Great. Will it have cooling?
That would be great. I'm still trying to figure out if I could run chilled water through the underfloor system to get at least some cooling during the summer, but I do plan on mini splits as the backup for both heating and cooling. The trick with the cooling will be whether I can work in components that will cooperate with switching over to chilled water, and also whether I can keep the chilled water above dewpoint using the right sensors. The high-desert dry air would work to my advantage for once in that calculation :) I know there are companies that make panels for that exact purpose, but they are crazy expensive. What do you think? Chilled water in regular hydronic underfloor Uponor tubing?
The Idronics journals cover this well. I think you’re well on your way to the most expensive HVAC system with this much complexity. Why not just use ductwork?
Minisplits is a confusing term nowadays, so let’s avoid that. Your plan is air-to-water with infloor heating and perhaps cooling, and then ductless heads for more heating and cooling? And the same air to water heat pump for both? It would work, but what’s your budget?
I would go about it the other way: figure out how much minisplit you need for your cooling, then how much underfloor you need to supplement that with to reach your whole-house goal. Then decide on the areas where the underfloor will have the most impact, like bathrooms. You can do a little more but there's no point in doing the whole house in underfloor.
Hey Paul, Ok thanks I'll check that out. You asked why not use ducted. The answer is that if I use hydronic, I can heat the water using PV when the sun is out (300+ days of sun a year), and use it for heating at night/morning. That will give me free, clean heat for 30 years (I should say: it'll be free after about 8 year break-even, if I do the labor). In the summer the PV can help run the mini split ACs. In the high desert it's rare to run the heat during the day if a house has decent passive solar gain.
Reply to #14:
On my local Craigslist I can get solar hot water collectors for free. The reason people are giving away is that they don't work well. In particular, they don't produce much when you need heat and when they do produce you don't need much heat. In most cases, if people had modeled their performance before installing them they would have seen that they don't pencil out.
I think you'll be better off taking the money and roof space that water heaters would require and dedicating it to photovoltaic panels.
Hey Paul, Budget is what I'm working on now. That's why I'm asking about Xpress-Trak, which is much cheaper than most other options. I'm trying to determine whether I can make the system I want for a reasonable cost. Once I get the Manual J done, I'll see if the system will work for those numbers. Trying to do as much research as possible before I start spending money on engineers, filing for permits (with expiration dates), and trying to source materials in our new supply-chain reality.
Hey DC, I'm definitely not interested in solar hot water collectors. I agree PV is far superior these days. I haven't run the numbers yet but I'm thinking an option is PV powered heat pump water heater and buffer tank for the hydronic. They can store water hot for a long time, with no new energy input. Depends on a bunch of factors- I'm trying to figure it out one step at a time. Before I get to that I need to figure out the hydronic system requirements.
Reply to #6
If you go to 26:30 of this Youtube video you can see a new cooling product by warmboard that is not listed on their website yet ...
https://www.youtube.com/watch?v=jcjTkU1tOfE
The video shows a fan coil unit (FCU), which is what you're going to want for cooling. It's basically analogous to a mini-split head, the one shown is analogous to a ducted mini-split. The difference is that it's pumping water into the coil instead of refrigerant. I feel there is a big technical benefit to doing that, because you can serve very low loads with no penalty. You can get hydronic FCU's that are as small as 3000 BTU/hr, I'm not aware of any minisplit heads that small. A 3000 BTU/hr head in a bedroom works really well. Hydronics also scale a lot better than minisplits, you can put a head in every room and run them all off of one heat pump no problem.
The Warmboard product is interesting because the big issue with FCU's is that there aren't a lot of choices available in the US right now, and the ones that are available aren't the most aesthetically pleasing. Which frankly, is a problem that minisplits have as well. The other issue is cost, I don't know what the Warmboard product costs but hydronics typically costs at least twice what comparable minisplits cost for the equipment.
Whether you go with minisplits or hydronic FCU's, my advice is the same -- size the air handlers for cooling, make up any shortfall with floor heating.
If you really want to go down the rabbit-hole, look at the hydronic equipment available on Alibaba. This is one FCU that I have in my house that I would recommend:
https://www.alibaba.com/product-detail/Ec-motor-Plastic-FCU-Ultra-Slim_1600352446965.html
Buying from Alibaba feels like buying a pig in a poke, and there were a couple of things I had to work around. Hydronics are much more popular in other parts of the world so it's wired for 220V and the plumbing uses British fittings. But adapters are readily available on Amazon.
The warmboard unit is cool. I wonder if they developed it themselves or it's a rebadged unit? The Jaga units have a similar install. Being warmboard, I'm guessing it isn't cheap at all!
" I know Xpress Trak and similar foam panels with thin aluminum foil facers are less effective at pushing heat from the pex to the flooring, but I don’t have a good handle on all the data out there covering that topic, and can’t really compare in any meaningful way- plus I don’t have any personal experience with hydronics. Just how bad are those foam/foil products at transferring heat, on a scale of 1-10 with 1 being the worst possible hydronic system and 10 being the best?"
Let's talk about what that means. It took me years to realize this, which is why I consider it an important realization, but the heat output of a floor -- or any surface -- is entirely determined by the temperature difference between that surface and the surrounding air. With floors, you care about more than just heat output, you want them comfortable underfoot, which means you don't want hot spots and you don't want cold spots, you want an even temperature. Since the need for heat can change quickly, you want a surface that is capable of changing temperature quickly so it can respond to changes in the demand for heat.
So what you want is something with high heat conductivity -- so the heat is spread evenly -- and low heat capacity, so that changes in the heat flow quickly result in changes in temperature, which will result in changes in output. Low heat capacity is particularly important in houses with high solar gain.
What Warmboard prides itself on is that it achieves those two things. I've seen videos on their website where they show side-by-side IR images of their product with a competing product. Both products start out cold and then heat is applied, and the Warmboard reaches stable temperature much more quickly, and at temperature the surface has a more even distribution of heat.
I'm not familiar with Xpress Trak, but if it's aluminum and foam that sounds like low heat capacity. Aluminum has good conductance, what makes Warmboard work is that it's basically a continuous sheet of aluminum under the floor, that's where its excellent conductivity comes from.
Note that the choice of finish flooring can completely overwhelm the properties of the underlayment.
Have you done a Manual J? A system like this has to be designed in concert with the rest of the house. Under-floor heating is compelling in high-performance houses. A typical house built in most of the 20th century might have had a heating load in the ballpark of 40 BTU/hour per square foot. Houses built to modern codes or better end up typically in the 5-10 BTU/hour/sqft range. A rule of thumb for heated floors is that the heat output is 2 BTU/hr/sf for every degree in difference between the floor surface and the air. So in a modern house the floor only needs to be 2.5 to 5 degrees above room temperature. My experience is that the floor has to be between 75 and 80F before you start even noticing that it's warm, so this level is essentially imperceptible.
With modern construction, particularly air sealing, floors are much warmer, except for stone or ceramic tile -- which have high conductivity and are effective at drawing heat away from your feet -- they're not noticeably cold on bare feet.
Almost everywhere in the US is going to need air conditioning.
My recommendation is to install air handlers to meet the air conditioning needs. Put heated floors under tile floors in the bathrooms, put enough heat that you can get them nice and warm to the touch, like 85F. Use a multi-stage thermostat so that the floor heat comes on first, and the air handler comes on when more heat is needed. Depending on your balance of heating and cooling, if you still need more heat, think about where to strategically locate it to supplement the air handlers.
Note that while concrete has excellent conductivity, it has rather high heat capacity so it's not a good choice for a heating surface in a highly-efficient house.
This is the video I was talking about:
https://www.youtube.com/watch?v=kqlFML2QnQ0
I know you didn't ask about this, but reading your description of the construction I have several suggestions.
First, find out for absolute sure how your locality measures height when it comes to the height restriction. You might think this is a simple question but it often isn't, and since so much of your design is oriented around meeting the height restriction you want to be sure what you're dealing with. I work in two jurisdictions that have height restrictions, both measure in completely different ways.
In one, the measuring point is the center of the front facade from either the existing grade before construction or the post-construction grade, whichever is lower. You can often choose which side of the house is considered the front, and the location of the center of the facade, in order to meet the height restriction. The distance is measured from there to the underside of the drywall on the top inhabited floor.
In the other, the measuring point is the threshold of the front door. You can put the front door at the top of a 20' flight of stairs if you want. Height is measured to the highest point of the house, usually a chimney or plumbing stack.
Those are very, very different standards.
I think that if you use metal joists you're going to be finding yourself wishing you hadn't. They're going to complicate construction at every step from framing to plumbing and electrical to installing stairs to insulation. A 2x8 will span the space you have, a 9.25 I-joist on 24" centers would probably be even better, find the couple of inches somewhere else.
You should probably start another whole thread on this, but ICF construction isn't generally well-regarded here.
Ok thanks, I'll confirm the height measurement method. That one method you mentioned is pretty odd! I'm hoping somebody who frequents these forums has a good "feel" for the heat transfer characteristics/data of the foam/foil systems relative to the others. I know even distribution is key for high temp hot spots, but I'm planning to keep water/floor temps low. No Manual J yet but it will be done. Still in early planning stages. Also I know even distribution is crucial for natural wood floorboards, but with tile it's less of an issue. I'm willing to sacrifice optimally even distribution in exchange for almost $8 per sq/ft price difference. However, what I really want to know is whether the foam/foil systems are going to transfer the heat into the room above well enough to make the system worthwhile. And yes, I agree, for this thread I don't want to get into the usual debate regarding whether ICF's initial carbon footprint is offset by it's longevity when compared to higher maintenance materials. Let's leave that to another thread :)
I have used their Quicktrack and was pretty easy to work with. No issues with stripping (this was with tile over it). About the only issue is your loop flow rate is much smaller so even a small space will need multiple parallel loops, adds a bit of extra manifolding cost and labor.
Overall, tile is bad idea in heating climates. Even with floor heat, it will not be hot enough to be comfortable plus it is pretty hard on bare feet.
+1 on skipping steel floor joists. I've built with megajoists which have big punch-outs and plumbing and ventilation was still annoying. Even simple things like screws for the subfloor have to be special, regular self tappers won't work. I would say compared to a wood floor system, about 3x the labor and about 2x the material.
One way to get thinner floors is to split up your 28' into 3 section with beams and run regular wood floor joists along 28' direction. This will be less cost and simpler plus allows you to skip any interior load bearing walls. Even going with LVL/LSL joists is better than steel.
Ok thanks. Quick trak uses a heavier aluminum plate, so it has better distribution and costs a lot more. Xpress Trak is new so I can't find much real world feedback- That's why I'm asking here. There are other, similar products that have been around longer, but haven't been able to find real-world info about them either. It's cheap because it uses a foil, rather than a plate. Ok I hear you and DC regarding steel joists. I haven't used them before but have done framing and drywall- The inconsistencies and twisting inherent in today's wood creates a huge headache factor for smooth floors. I wish there were TJI joists in 6 inch depth, but I don't think that exists. I'll look into LVL/LSL once I get an engineer involved. For some reason nobody wants to post span tables for using LVLs or LSLs as joists.
"That one method you mentioned is pretty odd!"
I'd say they're both completely arbitrary. Which is the point I was trying to get at, these kinds of rules are hyper-local and there's no agreed-upon standard.
(replying to #17)
I think if you do the math on how hot a heat pump can get water can effectively get water (about 115f), how cool the water can be and reasonably transfer heat (about 90f) and how big a tank you'll need to hold a reasonable amount of heat, and what that will cost, I think you'll be disappointed.
I'm ok with letting the heat ramp down overnight, and could set the thermostat accordingly. I have run the rough numbers and it would supply the required heat 80-90% of the time. I agree you can't store enough heat in a practical amount of water at say 130F to run the same set point all night, but with say 200 gallons at 6 gpm it's possible to start with a floor temp of 80 and let it ramp down to about 70 (room temp from 70 down to whatever minimum temp we set where the grid would kick in, or the mini-split heat would kick in if needed, whatever makes the most sense). It's definitely a bit of an experiment- many of the factors can't really be nailed down in theory- especially when it comes to thermal mass of the walls and floor covering, and passive solar. Btw not sure what you meant, but a heat pump water heater can get water to the same temps as a regular water heater (150f).
Just to clarify, you can’t use a heat pump water heater (like a Rheem, AO Smith, etc) to heat a house but you can use an air to water heat pump that extracts heat from outside to heat a house (Nordic, LG, Mitsubishi, etc.).
A 2400 sqft home, with roughly a 24,000 Btu/hr heat loss would need: 24,000* 16/24 / (8.34 * 20 delta t between max stored temp - min delivered temp) = 2300 gallons of water to cover 2/3rds of the coldest day of the year.
I think it’s a cool project. Have you looked into phase change materials? One product would be sunamp - by using the latent heat capacity of a salt solution, you could probably get that 2300 gallons of water down to a more manageable volume of PCM. I know on the cooling side of things, 1 lb of 32F ice that melts to 32F water is worth 144lbs of 33f water that warms to 34F water.
To get a floor temperature of 80F you need water at at least 95F.
Yes, you can get 130F water out of a heat pump, but the efficiency and output both fall dramatically. Looking at my favorite heat pump, the Chiltrix (https://www.chiltrix.com/CX34-air-to-water-heat-pump/ ) at 17F, the COP at various water temperatures is:
86F COP 2.95
95F COP 2.66
104F COP 2.45
113F COP 2.23
122F COP 2.03
131F COP 1.82
And max output:
86F 22.4K BTU
95F 20.6K BTU
104F 18.9K BTU
113F 17.2K BTU
122F 15.5K BTU
131F 14.1K BTU
So unless the nighttime electricity is dramatically cheaper it doesn't make much sense to run at a high temperature and low efficiency to store heat.
The plan is the opposite of that though- run during daytime excess solar electricity production, so get the benefit of producing heat when it’s most efficient and cheap. It’ll also add capacity to the heat pump which is a perk. With a lot of sophistication, you could try to time weather daily and weekly fluctuations, basically buying low and selling high. That’s why the phase change material is appealing - don’t store 130F water, store 100F salt.
Right, but instead of making 95F water all day long, you're making 130F water for eight hours during the day so you can get 95F water at night.
But you do have a point that during the day the outside temperature is higher so the COP is higher. So let's look at the Chiltrix numbers:
Outside temperature 32F, water temperature 95F, COP = 3.43
Outside temperature 17F, water temperature 95F, COP= 2.66
Outside temperature 32F, water temperature 131F, COP = 2.21
So let's say you have a really simple choice, either run all day at 95F, with 12 hours of 32F outside and 12 hours of 17F, or run eight hours at 131F with an outside temperature of 32F. Same number of daily BTU's in both scenarios. In the first scenario your average COP is 3.05, in the second it's 2.21. That's a 38% difference. So the daytime electricity has to be 38% cheaper before it even begins to make sense -- not counting the cost of the storage apparatus.
Depending on your net metering or TOU rules, electricity could be much more than 38% cheaper during the day. Mines about 75% cheaper during winter day vs winter peak
OK. I'm reading that the fully-loaded long-term cost of battery storage is about 10c per kWh, so rate shaving would make sense in that scenario. Battery packs seem to cost about $150 per kWh, you'd need about 50 kWh with a 20k BTU/hr heating load to run for 16 hours, which might cost $7500. I think you'd find that just storing the energy in batteries is a better use of that $7500 than trying to build the 2300 gallon tank that you calculated above or even a smaller phase-change tank.
I still haven't received a reply to my original question. If anyone has a reply please post it. Thank you!
It looks like xpress trak costs the same as Warmboard, which makes the comparison less important. Otherwise, DC did answer the question: aluminum is great for radiant panels, but what you put on top is also crucial.
I think that's about as much as you can say without having actually used it. I did read their website, and here's what I came away with:
The panels are thin, 5/8". They do this by using 5/16" tubing. The smaller tubing means runs can't be as long. The smaller tubing has a tighter bending radius, so the runs can be closer, which is good for heat distribution, but it means more tubing to cover the same amount of floor. So you're going to have more loops than with 1/2" tubing on 8" centers, which means more manifolds and valves, more expense. The 5/16" tubing is a non-standard size which means special tools and a harder time finding fittings, you won't be able to run out to any hardware store to get that last elbow.
The "board" itself is 5/8" molded XPS foam. This is good in that it has extremely low heat capacity and provides R2.5 insulation to the bottom; one of the things that can go wrong with floor heat is the heat going down rather than up. The foam has to be glued down, which would seem to be a slower installation. Tile requires 1/4" backer board, and they recommend gluing it to the foam.
Overall, I like the sound of the product. It does seem to be a bit much to be charging $10+ a square foot for molded foam that would be less than $.50/sf for the plain foam.
I'd like to think that the folks at Uponor have done their market research, and that if they've introduced a product that is comparable in price to Warmboard it is competitive in performance.
Deleted
Deleted
Where are you seeing Xpress Trak at under $1.50 per square foot? I'm seeing it at around $10:
https://www.ferguson.com/product/uponor-xpress-trak-radiant-panel---6-o.c.---4-runs-ua5070641/10109365.html
It's about $2.50 sq ft. That link says $80 for 4 pc of 2x4 ft, which is 4x8', 32 sq ft. True, it's not $1.50 (I didn't do the math before), but still much cheaper than warmboard or quick track, which are more like $8-$10 sq ft I think.
You know what? I may be wrong- When they say "4 runs" they may be referring to 4 runs of tubing, rather than 4 runs of panel. $80 for a 2x4' sheet of 5/8" foil-faced polyiso...wtf? haha
The Warmboard and similar products work fine by all reports, but they are pricey. Really meant for someone doing a bathroom or something.
GO to heatinghelp.com for more product specific hydronic heat advice
I found it too expensive so when I did my last house I 'made my own' because I had more time than money.
Tablesaw set to 5 or 10 degrees
5/8 plywood
rip baby rip
screw it down using ~2 inch pieces of 1/2OD pex as spacers.
Rubber hammer to pop the pex in
Look, there is literally no one on this site that loves radiant heat more than me, but seriously, in a modern well insulated[these days, even code compliant] house the attraction of not needing a boiler is huge.
My boiler install was 14k 15 years ago, and I still have 3 minisplits.
If hyper heat ducted units had been ready for prime time at that point. one more unit and I save more than 10 grand
My house is not even to current code, but is tight enough and insulated enough that even though I ran all the tube for radiant in my downstairs and in my upstairs baths, I have never connected it!
I no longer feel that with an insulated slab, good glass and decent insulation that radiant shows a real improvement.
Is it possible there is an economic driver that if I had to get rid of my boiler that I might hook up those radiant loops; yes. Because I already put them in, it might make sense to use a A/W heat pump to satisfy the heat in every room requirement.
Even in average US homes, almost no one uses hydronic heating. The allure of AC is powerful!
I think there are a ton of' no ones' out there
I personally think hydronic has significant advantages, but only compared to fossil fueled forced air.
If you are going all electric, hydronic just adds a cost layer that seems pointless to me.
Yes, with climate change and the increase in AC installation, hydronic heat will become the steam heat of the future, but there is a significant installed base
Including steam, only about 7% of residential buildings use any kind of water as main heating delivery system. It’s millions of units, but a small percentage.
https://www.eia.gov/consumption/residential/data/2020/hc/pdf/HC%206.1.pdf
Hey Paul, What do you think about using the same hydronic system for cooling, like is done in commercial systems? Don't newly available air-water heat pump options make that more feasible for residential systems? I'd like to see if I can make hydronic work for both because I like the idea of being able to store excess PV production in water for heating 2/3rds of the year. If I can also use the system for some level of cooling, that would be great. I read a lot in the Idronics texts that seem to say it's doable... But I'm a noob
It can 100% be done if you’re motivated! If humidity can be handled some way, you can use radiant cooling.
The reason they call it "air conditioning" and not just "cooling" is that you have to dehumidify the air as well as cool it. In order to do that you have to have some way of capturing condensation.
At the risk of repeating myself (yet again), what you want to do is have air handlers, size them for cooling, then supplement with floor heat. Once you accept that you'll be happier.
I have an open mind about it for sure. Dehumidification is not a problem is southern CO. Air is bone dry, and there would be an HRV and fresh air involved. Could always work one in as needed. If the system cost turns out to be on par with batteries, then I'll probably go with the batteries- Assuming the equipment lifespan is similar. I enjoy figuring this stuff out, and will work the numbers and see what happens.
"Dehumidification is not a problem is southern CO. "
I realize Colorado is a big place, but I recommend this thread:
https://www.greenbuildingadvisor.com/question/independent-hydronic-heating-and-cooling-designers
In particular, this comment from the OP: "one firm told me they don't do radiant cooling in the front range of CO anymore because of condensation problems."
I can't find it but recently there was a thread about how 99th percentile dew point statistics are now available, which would help with design.
Hey Gus, Yes a diy built panel system makes a lot more sense now that I realize the xpress trak is $80 per 2x4' panel, not $80 for 4 pc 2x4' panel. Not to get a whole different thing going but I was also messing with the idea of radiant ceiling instead, using nail-up steel/galvalume ceiling tiles (decorative type) instead of drywall, covering diy hydronic radiant panels that are in contact with the tiles. Then also run cooling through that. Seems like that would transfer heat nicely!
Hi Gus (replying to#33),
Not to hijack this thread, but thanks for the writeup on your DIY radiant floor. I'm thinking about doing the same for a 10'x13' mud room in my house, currently unheated. The 5° or 10° bevel on the plywood rips to hold the pex is genius, I hadn't thought of that.
Did you use any other sort of clips to hold the pex in place? And, did you use any of those aluminum heat emission fins?
Paul
It occurs to me that if I was looking at an A/w heat pump for hot water, some radiant panels or vintage radiators or whathaveyou for meeting the heat in every room requirement might start to make sense.
A/W heat pump, buffer tank, circulators as an add on to heat/ac minispits and ducted splits
Replying to Tim_O #32
"The warmboard unit is cool. I wonder if they developed it themselves or it's a rebadged unit? The Jaga units have a similar install. Being warmboard, I'm guessing it isn't cheap at all!"
Jaga unit (I looked at them today) it is 4.7" deep so won't fit in an interior 2x4 wall cavity!
If you could do cooling with the warmboard FCU, why not also heating with the same unit?
Maybe they should look at the Messana – Ray Magic® NK Radiant Ceiling Panels ...
https://source2050.com/product/messana-nk-radiant-panel/
The warmboard unit also is setup for 2x6 studs, not 2x4. I almost wonder if it is a rebadged Jaga. I don't know that warmboard manufacturers much other than the flooring.
Ok thanks everyone! Lots to chew on here. Couple of quick things: Yes the idea is the get the "flywheel" of hot water spinning when the excess solar is being produced (since net metering rates are not great), then supply minimal energy to keep the heat level up through the evening heating time. During that time, the system would not be heating the water from 50-60F, it would only be adding smaller increments, also the system and the building should have it's own mass "flywheel" holding that energy in. Also, it would be fine to let the house temp go down over the night, which would further reduce the amount of new energy required. So I'm skeptical that 2,300 gallons would really be needed. Trouble is, the x-factors involved are very very difficult to quantify. Anyway, I appreciate the input! Idronics is really a great resource- thanks for pointing me in that direction. Please feel free to continue discussing this since you all have a lot of useful info to share.
>So I'm skeptical that 2,300 gallons would really be needed. Trouble is, the x-factors involved are very very difficult to quantify.
Paul actually did a very good job of quantifying them in post #25.
The one piece missing from the analysis is the heat capacity of the house. I've come to believe that for a typical house it's in the order of magnitude of 50,000 BTU's per degree F. So let's say we have the 24,000 BTU/hr heat loss that Paul stipulates, if you turned the heat off at, say, 11pm, the house temperature would start dropping by about half a degree per hour. Presumably you don't want to wake up to a cold house -- you're investing all of this money in an elaborate heating system. So you want the house back up to temperature by 7am. If you let it cool for four hours, you then have to heat it at double the rate for the next four hours to get back to temperature -- 24K per hour to replace the heat that was lost, plus 24K per hour for the regular heat loss. You will save a little bit of energy because the heat loss won't be 24K all night, it will be slightly less. But only slightly-- the house only gets 2F cooler, and only for a couple of hours. Meanwhile, suddenly instead of needing a 24K heating system you need a 48K heating system.
Note that all of that heating has to be done before you wake up, before the sun is cranking. So it all has to come from either stored heat or grid electricity.
There's a reason set-back thermostats have fallen out of favor. They worked a lot better in 20th century houses where heating loads were large compared to the heat capacity of the house, so the house would cool off quite a bit overnight, and heating systems were typically oversized by a factor of two to three.
You may think that the extra heat capacity of your ICF walls will help, but it actually makes the problem worse, the more heat capacity your house has the less energy you save by setting back the thermostat. And the ICF's probably don't add that much to the heat capacity anyway, a typical house has plenty just in the drywall.
It somewhat depends on what you’re willing to accept. If you want it 70F 24/7, you’ll need a lot of storage. If you can run up the interior temp to 80 during the day, let it cool overnight below 70 and start all over, in effect you’re using the house as part of the battery too. However, then I’d ask…if the heat isn’t stored in the water, then why bother with the air to water heat pump? You could then just run a regular heat pump to “over” heat up the house in the daytime to charge the battery that way. A plus of radiant systems is thermal storage can be added, but controllable storage is what you want (ie not a slab). If 2300G is a high estimate, you’re still looking at several hundred I’d suspect.
If you read the Idronics on wood gasification boilers, they use huge water tanks. They also have an advantage you don’t, wood can heat water to a high temp with no loss of efficiency, so storing 180F water with a min supply of 100F gives you 3x the capacity per gallon. An air to water heat pump can’t go that high, and even if it could, efficiently would plummet. It’s a hard, and fun, problem to try to solve.
>It somewhat depends on what you’re willing to accept.
Comfort isn't the main thing, it's the only thing. The only reason for HVAC is comfort.
That's a bit of an exaggeration, you don't want your pipes to freeze. But anything beyond keeping your pipes from freezing is just for comfort.
Of course, but comfort is so subjective. If one never notices a temp change, did it happen?
If you really want to save, look at Alibaba:
https://www.alibaba.com/product-detail/Hydronic-Heating-Floor-Insulation-Board-Floor_1600953616267.html
For a 2'x4' piece:
$1 for just the foam
$4 for foam with foil coating
$10 for foam with aluminum sheet
Nice! How much cancer is it made with? haha JK.
I think you and Paul were right about the cost of Xpress Trak. Crazy they are charging $80 for a 2x4' sheet of 5/8" foil-faced routed polyiso. gimme a break!
When people say hydronics is expensive this is the kind of thing they have in mind. You can get a complete minisplit on Amazon for less than $500.
Just as an aside - I ordered a sample set of these and they just arrived. I ordered the EPS with basically aluminum foil and the XPS with stamped aluminum. The XPS/Aluminum version is actually quite substantial. The aluminum thickness is about 0.02", the same as the Warmboard samples I have. XPS thickness is 1". Cost before shipping is about $0.50/sqft. Shipping will likely double that, depending how much you order, but I am about to find out.
The EPS is basically just a sheet of EPS, grooved for radiant and a piece of thick aluminum foil over top. Just sliced for the grooves, it doesn't even lie inside the grooves. It probably would work fine, but the XPS version is nicer. I think the issue would be that you cannot nail your floor to foam. It would be a waste to install these and then have to put another layer of subfloor over them to do wood floors.
On another note, I am speaking with the supplier that provides the heat pump for ArcticHeat (Macon). For the smallest version (~2 ton), and a 100L buffer tank, it will be about $2500 shipped to my door in Michigan. There is another user on Reddit who imported an R290 unit for about $1900 shipped from SunRain Solar. He just received it and is quite happy with it. Technically that is not yet legal to use, so if you are reading this and decide to follow this route, be aware that R290 is not yet legal in the states.
Good to know, those are interesting data points. I've ordered a couple of things off of Alibaba and I always wonder about a lot of their listings.
I would also worry that a direct-import heat pump wouldn't be UL-listed, which could cause problems. Even if it's the same as the model that ArcticHeat is selling and they've paid for listing, that listing isn't going to transfer.
If I were distributing in the US I'd be mad as hell if my supplier was selling direct.
Yes, the UL listing is something to look into.
On the flooring, I was wrong on the pricing. The aluminum is priced separate and has a 100% antidumping tariff. So the total is closer to $1.10/sqft. For my small floor area, more likely I do a second layer of plywood cut into strips with some eBay aluminum heat transfer strips.
On the Arctic side - Macon's unit is ETL listed. Some on Alibaba are that. Many are CE listed, so maybe ETL is coming soon.
The 2300 gallon storage tank being bandied about has a heat capacity of slightly over 19,000 BTU per degree F. If you accept my estimate of the heat capacity of the house itself at 50,000 BTU/F, then with a 20F swing in the tank you store the same amount of heat as with a 7.6F swing in the house.
So if you're willing to accept, say, nighttime temperatures of 67 F and daytime temperatures of 74.6 you don't need any additional equipment. Just set the thermostat for 75 when the sun is shining and 67 when it's not.
I am also looking at my different options for boards. But I got to thinking - Quiktrak places the aluminum heat transfer plates under the 1/2" plywood. If you have 3/4 or 7/8 subfloor, using staple up with aluminum heat transfer plates should net similar results I think? Has anyone used staple up with 95-105* heat pump water temps?
This is the hardest part about radiant planning, trying to predict floor temperature from water temperature. The problem is that small variations in the construction of the floor can change its characteristics.
That makes sense. It seems like mostly what you are doing is changing how quickly the floor responds. The heat is exiting the PEX in all cases. Insulate below and that heat should be going up.
The surface temperature of the floor entirely determines the heat output. The amount of insulation between the pipe and the surface, the heat flow, and the pipe temperature determine the surface temperature. If there is too much insulation in the floor -- or not enough conductivity in other words -- then you won't get the surface temperature you want and you won't get the heat output you want.
Usually when people are disappointed it's because the floor isn't as warm as they had planned for. With a combustion boiler it's an easy fix, you just bump the water temperature up. If you're using a heat pump and you're already all the way up there is no easy fix.
I have Warmboard running with 95F water here in zone 6A, with a design temp of -8F. Very comfortable. Remember part of the install is to place insulation under neath the heat emitter. Warmboard typically uses R19 batts underneath the floor joists and to insulate the rim joist. Increasing the resistance creates an upward flux.
For Quick track , you have more resistance — so you need to calculate the R value for the floor assemble. A lot of installs forget to insulate under the QuickTrack. We had QuickTrack under our sunroom floor..it was removed and replaced with Warmboard to avoid having multiple water temperatures. (115F vs 95F).
Our Warmboard system uses water coming off the DHW tank and then runs through a heat exchanger, so the 80 ga tank acts like a buffer tank. I would avoid using anything larger than 80 gallons.