How best to integrate utility/furnace space into basement with mechanical ventilation?

Greetings!
I’m pulling together plans to finish our basement with the intention that the basement will have mechanical ventilation and mini-splits for cooling/heating. There is a utility room in the basement that houses our gas water heater and furnace/AC unit for the 1st floor. I’ve thought of a couple approaches on how best to integrate this utility room with the finished basement and would welcome input:
1. Route one of the mechanical ventilation fresh air ducts into the utility room, thus supplying the combustion units with the fresh air they need to do their job – in this case the utility room would be a part of the basement air circulation space. This would also require a vent in the door so air can exit out when the combustion units aren’t operating and thus creating a draft in their exhaust vents, or maybe some of the air would always be going up and out the exhaust flues. (probably not good)
2. Practically ‘seal’ off the utility room in terms of both air and thermal insulation from the rest of the basement – this would require a fresh air duct routed directly to the utility room from outside.
One possible concern I have with approach 1 is that when the combustion units are operating (or maybe even when they’re not!), they might slow or prevent the return air flow to the mechanical ventilation exhaust.
A concern I have about 2 is the utility room will then get quite cold in the winter.
FYI – we’re in Zone 5 (Utah, so it’s fairly dry here most of the time)
Right now I’m leaning towards option 2 since I don’t like the idea of open exhaust vents in the utility room that might potentially break the otherwise controlled/closed air ventilation space that the mechanical ventilation manages, though it would be a pain to try and insulate that room since there are pipes, wires and ducts a plenty (it also houses the main electrical panel for the house)
Thanks in advance for any tips or advice.
GBA Detail Library
A collection of one thousand construction details organized by climate and house part
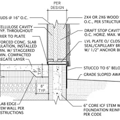
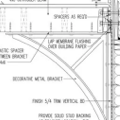
Replies
>"I’m pulling together plans to finish our basement with the intention that the basement will have mechanical ventilation and mini-splits for cooling/heating."
Unless it's an unshaded hillside walk-out basement with a lot of west-facing glass sliders the sensible cooling loads of a basement will be near zero or negative in zone 5.
You're thinking "..mini-splits..." as in plural? The heating load of a code-minimum basement is well within the output of just about a SINGLE 3/4 ton mini-split, or even a cold climate half-tonner like the Mitsubishi -FH06NA.
If the basement is currently unfinished the foundation walls should first be insulated to the IRC 2012 & later R15 continuous insulation (see: https://up.codes/viewer/utah/irc-2015/chapter/11/re-energy-efficiency#N1102.1.2 ) before the finished walls go up, and run a Manual-J load calculation. If the basement is being broken up into multiple doored-off spaces, a small ducted mini-split is likely to prove more satisfactory and more efficient than multiple ductless heads endlessly cycling on/off with insufficient load.
The mechanical doesn't really need "ventilation air", but it does need MAKE-UP air. If the mechanical room doesn't currently have ducted make-up air for the furnace & water heater, it won't need to be added. Unless you have Utah's most LUDRCROUSLY oversized furnace burner it can usually be provided by a louvered door. Utah's code (based on IRC 2015) calls for a square inch per 1000 BTU (input) for combustion appliances:
https://up.codes/viewer/utah/irc-2015/chapter/24/fuel-gas#G2407.5.3.1
So a ~40KBTU/hr burner on the water heater and a ridiculously oversized 100KBTU/hr burner on the furnace would still be just slightly under one square foot of free area.
Yes, there would be 24/7 convection up the flue in winter, but unless the system already backdrafts when the clothes dryer, bath fans and kitchen fan are running simultaneously there isn't much point to going with option 2.
The option #2 of sealing up the mechanical room and installing a permanently ducted outdoor combustion port to the mechanical room doesn't need as big a hole, but represents a localized heat loss in winter. Ducted make up air only needs be an square inch per 4000 BTU:
https://up.codes/viewer/utah/irc-2015/chapter/24/fuel-gas#G2407.5.3.1
In the 140 KBTU (total input) example that would only need to be (140K / 4K=) 35 square inches- a 7" round covers it. If the furnace is a more reasonably sized 50K unit and the total is 90K it only needs (90K / 4K=) 22.5 square inches, and a 6" round has margin.
It would still convect air up the flue 24/7 and the room would be colder in winter, but as long as the foundation walls were a continuous R15 and the partition walls to the rest of the basement are NOT insulated it won't get TOO cold in there. The duty cycle of the furnace goes up when the incoming make-up air is colder, and the jacket and flue-piping losses go up with duty cycle, adding more "waste heat" into the room. It's only risky if the exterior walls are NOT insulated, and/or the partition walls ARE insulated.
Of course the problem goes away if the furnace gets replaced by a right-sized sealed combustion condensing furnace (which is comparable in installed cost to a single 1-ton mini-split), or a right sized cold climate ducted mini-split (more expensive, but greener than a fossil-burner). To better estimate the ideal size of the main heating system, use the existing furnace to MEASURE the heat load using this methodology:
https://www.greenbuildingadvisor.com/article/out-with-the-old-in-with-the-new
@Dana appreciate your detailed response.
It is an un-shaded walk-out basement with the walkout on the south side. We have 2 large windows on the south side, and a large one on the west side that will get sun in the afternoon/evening, so we expect at least some heat-gain in the summer. Glad you mentioned a J load calc - I'll do that to make sure I'm properly sizing heating/cooling mechanical. Can anyone point me to a good calculator or formula for just calculating the basement? The basement has 1600 sq. ft. The HVAC unit in the mechanical room is servicing about the same amount of space on the 1st floor above (ca 1600 sq. ft. ). Probably worth mentioning that the current furnace/AC unit was probably sized with the intention of servicing both the 1st floor and basement (ca 3200 sq. ft total); when it's replaced it should be re-sized for just the 1st floor. This mechanical room DOES currently have a large 'make-up' air duct bringing in air directly from outside (looks like it's 6-9" diameter)
Your mention of a "ducted mini-split" is intriguing; my original intention was to get a 'multi-zone' mini-split that has a single unit outside and then 4 wall units in the main areas of the basement, but sounds like it might be overkill. In the case of a single 'ducted' mini-split, how would conditioning for separate zones be managed; vent flaps? Sounds like I need to research different mini-split configurations/setups.
I find your last point particularly interesting: I installed grid-tied solar last year and have been considering replacing our aged gas water heater with an efficient electric water heater. If I then replace the furnace with a sealed furnace, or mini-split the whole question effectively goes away.
For now though, to try and capture the gist of what you've said, it sounds like at a minimum to move forward:
*if the basement is properly insulated to IRC 2012+ requirements, and
*if mechanical ventilation is regularly providing air change through the basement, and
*if the minimum volume air in the basement requirement of the IRC code is met ( G2407.5 (304.5) Indoor Combustion Air) - which it should be even taking your extreme example of 140 kBtu/h: roughly 1100 sq. ft of open space x 10' = 11,000 cubic ft. > 140kBtu/h needs 140 x 50 = 7,000 cubic ft.
*then a top to bott0m louvered door into the mechanical room should suffice to meet the current combustion devices 'make-up' air needs (a direct vent to the outside shouldn't be needed), and as I replace the water heater and/or current furnace with a sealed furnace or mini-split, the situation only gets better.
High solar gains would skew a fuel-use based load calculation to the low side, but run those numbers anyway. Unless you have a whole south wall of glass sliding doors or something it's not going to undershoot by a large amount.
An online freebie/cheapie registered Manual-J tool that can give good numbers if you're suitably AGGRESSIVE (rather than conservative) on R-values, air tightness and window specs is CoolCalc:
https://www.coolcalc.com/
A somewhat less-flexible but still OK Manual-J-ish online tool is LoadCalc:
https://loadcalc.net/
With a fuel use load calc you can sanity-check, the whole-house heating load numbers of a DIY CoolCalc. If CoolCalc or LoadCalc is giving you a whole house load more than 50% higher than the fuel use numbers indicate you're not being aggressive enough (or the solar gains in winter are just TOO good.) Look at the output charts & graphs to figure out where the tool might be overestimating (air leakage and ventilation are often wildly overstated).
When the whole-house load numbers are starting to get close to what the fuel-use numbers are (within 35%) it's reasonable to assume it's close enough to look at the room-by-room loads for the basement, and the load for the first-floor zone.
The room-by-room numbers for the basement will dictate whether a room can actually use an individual head, or whether you'd be better off going ducted.
Don't be surprised when the heating & cooling loads of the whole house (including basement) are under half the output of the existing AC, or less than 1/3 the DOE output of the furnace.
If you're keeping the existing furnace & AC through the summer, on days when it will be hitting around the 1% outside design temp, try measuring the duty cycle on on the AC compressor. Then...
nameplate cooling BTU x duty cycle= actual load
... and that load number includes any parasitic losses of the ducts, etc. Try not to oversize the replacement equipment by more than 1.5x the actual measured load at the 1% outside design temp, even if it's modulating or multi-stage equipment. The duty cycle of the compressor may not be the same as the duty cycle of the call for cooling from the thermostat (but it can be). The ideal place to measure the duty cycle would be sensing current at power leads to the compressor in condenser (outdoor) unit. See:
https://www.greenbuildingadvisor.com/article/how-to-tell-if-your-air-conditioner-is-oversized