How much to worry about moisture from air leaks?

I live in zone 4A (virginia). We live in a house built in 1972, so overall it’s not super efficient. I’m redoing a finished basement and adding insulation (it doesn’t have any currently), and I already have a plan for most of it. I’m going to use foamboard insulation on the walls.
I’m trying to figure out what to do at the top, however. The foamboards will be 8′ high, but there are 2×10 joists so there is ~9″ between the top of the foamboard and subfloor. There’s also a lot of piping, wiring, and more so it’s not simple to throwing some foam boards up there (can’t use caulk to seal up the seams).
Two of the walls are exterior (not underground, the ground slopes down so these walls face open air). One of them is the garage wall so the air seal is even worse; there’s no siding or barrier at all. I can feel a draft.
I could stuff fiberglass insulation all up in there, in addition to using a can of spray foam to seal any open holes. However, there will be no vapor barrier for those 10″ across the entire wall. It’s very humid here in the summer, should I be concerned about humid air coming in? Even if I sealed all the holes, humid air would find a way in (wood or concrete is not a vapor barrier). Won’t that humid air cool down as it comes in and condense? Would fiberglass insulation without any barrier eventually break down due to moisture problems?
Summed up my question is: is fiberglass insulation always doomed if humid air gets in, or is a little bit OK? I’m considering getting a Froth Pak 200 and spraying the whole top area with 2″ of foam to form a vapor barrier.
GBA Detail Library
A collection of one thousand construction details organized by climate and house part
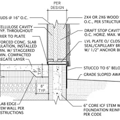
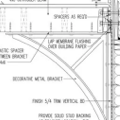
Replies
Wood and concrete are not vapor-closed but they are airtight, so they won't allow humid air in directly. Moisture movement by diffusion is much slower than moisture movement on air leaks, and in some weather conditions, the air leaks provide drying, but more often they introduce moisture into the assembly.
Fiberglass does not stop air flow; it hardly slows it down, so stuffing it into the joist bays will help a little against heat flow but not a lot, and when it's cold outside the fiberglass will slow indoor heat from reaching the rim joist so it will be cold and more likely to accumulate moisture trying to get out from the interior. In hot weather, outdoor air trying to get inside will condense on the first cool surface it finds, likely to be the interior portion of the fiberglass.
Fiberglass is literally made of glass fibers, so moisture won't break it down any more than it breaks down window glass. But when saturated, the fibers can mat together, eliminating the air spaces between fibers that do the actual insulating.
I avoid foam when reasonably possible but rim joists are one area I don't feel much guilt about using it, since it provides air-sealing, vapor control and thermal control all in one material, in what are finicky, small spaces to deal with in other ways. But if you want to avoid foam, on several occasions I have worked with builders who seal the bays with a variable permeance, airtight membrane and insulate with blown cellulose or fiberglass. There's no reason you couldn't do the same. But foam is easier.