How to insulate an 18th century attic?

I have a 1790 stone house near Philadelphia. I need to replace an asphalt roof (on plywood sheathing) with white/black mold observed on plywood sheathing visible from unimproved attic space. There is a ridge vent for the warm air to exhaust at peak, but no air intake at soffit because space between rafters has mortared stone in place. I think heat/moisture under roof is poorly managed. Roofer to install new roof will install (asphalt or cedar shake shingles). Is there a recommended system or method to retrofit a moisture/heat barrier to protect roof?
GBA Detail Library
A collection of one thousand construction details organized by climate and house part
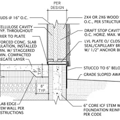
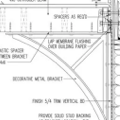
Replies
The heat/moisture barrier you need should be installed at the attic floor, not the roof. You want to keep your warm air in the house instead of letting it into the attic to rot the roof. Spend some time on this site searching for how to air seal and properly insulate an attic. If you seal the attic floor well enough, you can significantly reduce the need for attic ventilation, to the point that the ridge vent and the naturally leaky attic walls will be enough.
+1 on reducing air leakage.
You should also add some under-shingle vents down low to increase ventilation (and better manage pressure).
https://dciproducts.com/smartvent-eave-installation
User-7210329,
First of all, can you tell us your name? (I'm Martin.)
I agree with Peter and Jon. The type of mold you are seeing is almost always a sign that your ceiling isn't airtight. (When air leaks out of your ceiling into your attic during the winter, the air carries moisture with it. This moisture later condenses or accumulates on the underside of the cold roof sheathing.)
You don't need better ventilation. What you need is air sealing work.
Here is a link to an article describing the required work: "Air Sealing an Attic."
Here is a link to an article explained why ventilation isn't a solution: "All About Attic Venting."
Thank you for your input. Things are more complicated than how I first described them. Only about a third of the space under the roof is unfinished. There is a plaster wall that separates the unfinished from the finished 2/3 portion. The space under the roof is a 3rd floor. Access to the 3rd floor is via an stair case, which is open from the 1st floor hall to third floor. At the top of the stairs, a hall runs from one side of the house to the plaster wall, about 25', running parallel to the ridge. The finished side of the 3rd floor consists of this hallway and two front rooms - tucked under the eaves. A previous owner had cellulose blown between the 2nd floor ceiling and third floor floors. The cellulose by itself is ineffective in stopping moisture, but if a barrier at the top of the stairs to the third floor were erected (wall & door), it might be my best move to reduce moisture buildup under the roof. What do you think?
Dan,
You wrote, "The cellulose by itself is ineffective in stopping moisture." That's true, but remember -- you're trying to stop air movement, not vapor diffusion. The key is stopping air leakage.
This type of attic can certainly benefit from a wall and a door at the top of the stairs. But that's just the beginning of the air sealing work you need to perform.
Your house needs a well-defined thermal envelope. That means that you need to know where unheated space ends and where heated space begins; and it means that this envelope needs code-minimum insulation levels adjacent to (and in contact with) a leak-free air barrier.
In many cases, you really need a blower door to perform this kind of air sealing work. I suggest that you review these resources:
"Air Sealing an Attic"
"Blower-door-directed air sealing"
Martin, Thank you for your advice. I am having difficulty finding someone who can come on-site to advise me. Can you point me toward a reputable advisor in the Philadelphia Western suburbs?
Dan,
You want to find a contractor who owns a blower door -- someone who uses the term "home performance contractor" or "weatherization contractor" or perhaps "energy auditor." A contractor who performs home energy ratings should be able to help.
You might want to search for local contractors on the RESNET web site.
Martin,
Thank you for your suggestions. With your help I was able to find an home performance contractor in my area who has advised me on a design solution for my complex attic/3rd air-envelop problem. After a thorough exploration of the problem, the consultant suggested tightly filling the cavity between the 2nd floor ceiling & 3rd floor flooring with loose fiberglass for unimproved/unheated 3rd floor spaces. For the heated 3rd floor spaces: insulate walls, door & ceilings with a variety of materials: open-cell spray foam, rigid foam panels and fiber-glass bats.
To ensure ventilation at roof sheathing, and prevent moisture getting trapped under the roof, the consultant suggested rafter vents with baffles installed underside the roof sheathing between roof rafters. Also install a ridge vent at top and a single edge vent under the first course of shingles. (To open the soffit for venting was rejected as an option as the historic soffit is very small and ventilation is blocked with stone masonry). One remaining concern is specification of roofing materials. We are seriously considering a synthetic cedar shake shingle product.
Question: Can you recommend any sheathing products that will last as long as possible - matching the 50 year guaranteed life of Brava singles?
Dan,
Q. "Can you recommend any sheathing products that will last as long as possible - matching the 50 year guaranteed life of Brava singles?"
A. I've use board sheathing (rough 1x6 or 1x8 spruce boards from local sawmills), plywood sheathing, and OSB sheathing. Barring a roof leak that is ignored for a long time, any one of these three sheathing products should easily last 50 years. In general, plywood is more tolerant of moisture cycles than OSB, and board sheathing is more tolerant of moisture cycles than plywood -- so all other factors being equal, board sheathing is hard to beat. The main disadvantages of board sheathing are: (a) building code enforcement officials often reject board sheathing because it lacks a grade stamp, and (b) board sheathing is hard to make airtight.
Thanks, Martin for the tip on board sheathing.
As I wrote earlier, this house has an open stairway plan - stairs that run from the 1st floor central hall to the 2nd central hall to the 3rd floor central hall. One element of my planned thermal envelop for the attic/3rd floor space is to install a wall and door at the top of the steps at the 3rd floor hall. I hope this will trap heat rising up the stairway from leaking into the 3rd floor attic space. Much of this heat will collect at the space at the top of the stairway - below an old plaster 3rd floor stairway ceiling. Above the ceiling in the hidden space between the ceiling and the roofing, my insulation contractor plans to install as good a thermal barrier as possible - spraying about 3 inches of closed cell foam (leaving 1" of air space below roof sheathing). The walls of the stairway will be insulated too, and the whole system will be taped and joined together to maintain what we hope will be as effective a thermal barrier as possible.
The old 3rd fl hallway plaster ceiling is "keyed" to lath, which is nailed directly to roof rafters, leaving just 3-4" of space for insulation between the plaster and the roofing system. We are installing a new roof. During the new roof install, we plan to do the foam spraying - after the old shingles and sheathing are removed and before new sheathing is installed, the hidden side of the ceiling plaster will be exposed - a good time for the contractor to spray the foam.
Question: I want to provide some "reversibility" to the foam against the historic wood & plaster structures, so before the insulation is sprayed, I want to cover the roof rafters and ceiling joists and hidden sides of plaster walls with a fabric such as tyvek. What do you think about laying tyvek or some other fabric between the old materials and the foam insulation?
Dan,
Nothing wrong with laying the Tyvek into the bays, something similar is done when spray foaming metal utility buildings.
The item to watch is to only run the Tyvek an inch or so up the studs, this way the foam can still adhere to the studs and create a proper air barrier.
Don't leave out:
http://ecostarllc.com/product/majestic-slate/
It may look good with your place. All you should need is a good plywood sheathing. Weathershield on top, then mock slate/shingle. We love ours even after giant 3" hail storms and 3 tornadoes in 5 years, it hasn't touched a single shingle.
Paul,
Thanks for the tip, but the original roof is most likely to have been cedar shake. Slate roofs on houses built 1750-1800 were exceeding rare and costly. My house was originally built by a local miller: who, evidence abounds, was not wealthy enough to afford a slate roof. Here's a nice summary of roofs of old houses in America: http://www.oldhouseweb.com/how-to-advice/types-of-historic-residential-roofing.shtml.
I agree with Paul.
Clearly the house has not been moldy for 200+ years, somebody changed something and with the unintended result being mold.
While I am sure the changes were made with the best intentions, if this mold is not stopped it will become rot and put the house at risk.
The real question is… what changed? And are you better off undoing the changes?
I agree keeping the warm air in the house is a low risk change. This house is likely to be very leaky; it will take days and days of work to seal it. Anyone with a professional blower door is unlikely to want to stay long enough seal all the leaks, so I say put a fan in a window so it blows out seal around the fan. On a cold day the back of your hand will tell you where the leaks are. Seal up the leaks and repeat and repeat. If you are going to pay someone to do this work do not let them bid the job as a $xx for the job, pay by the man hour with an estimate of hours.
This link has good ideas.
https://www.builditsolar.com/Projects/Conservation/BlowerDoor/BlowerDoor.htm
Walta
If I attach plywood sheathing to underside of all roof rafters throughout. Then have closed cell foam spray installer add/build up to 10" of foam applied to the underside of this new sheathing, to get R-62 of under roof/attic insulation (HDD about 5500 - here near Valley Forge, PA), would such a design provide all necessary barriers (air/insulation) between conditioned space and roof above? Why not spray into rafter bays? I don't want foam applied to old rafter beams because it's not easily reversible.
A continuous R62 is WAY over code minimum performance, which is under U0.026 (=
over R38.5 "whole assembly", including the R values of the roofing, air films, roof sheathing, etc. )
And 10" of closed cell foam is about the most expensive (financially and environmentally) way to get there.
10" of OPEN cell foam hits the thermal performance required, but the stackup and venting under the roof deck has to be up to snuff. Plywood sheathing fairly vapor retardent and moisture susceptible- using more vapor open and less susceptible MDF, asphalted fiberboard, or exterior grade gypsum board instead of plywood would be far less problematic, assuming the rafter bays are all vented soffit-to-ridge.
Dan,
Q. "If I attach plywood sheathing to underside of all roof rafters throughout. Then have closed cell foam spray installer add/build up to 10" of foam applied to the underside of this new sheathing, to get R-62 of under roof/attic insulation (HDD about 5500 - here near Valley Forge, PA), would such a design provide all necessary barriers (air/insulation) between conditioned space and roof above?"
A. Yes, but R-62 of closed-cell spray foam (about 9.5 or 10 inches of spray foam) is expensive, and not particularly green. (Most brands of closed-cell spray foam use a blowing agent with a high global warming potential.)
Note also that most building codes don't allow foam insulation to be left exposed -- it has to be protected with a layer of 1/2-inch gypsum drywall for fire safety.