How to insulate a stackboard house?

I have an old house, built in 1840, and with an addition put on around 1900 or so. The original house is stone, and the addition is made from stackboard. Stackboard is a technique locally popular in lumber towns, where you take rough cut 2x4s, stack them on their flat side, and chink in between with 1/2″ chunks of wood. Essentially your entire wall is solid wood and you renovate using a chansaw (my grandfather actually did this apparently, as even the interior walls were done this way. it’s wierd). The house is pretty much uninsulated other than the thickness of the walls (R1?)
I’m putting my own addition on, and when i do so, the chintzy vinyl siding on the stackboard side of the house will go away and be replaced with wooden siding. I plan on putting 3 or 4″ of rigid insulation on the outside of my addition, so it will stick out past the original house unless i do the same there (and hey, ACTUAL insulation would be a nice change!).
My question is this: if i put rigid insulation on the outside of the stackboard (probably with a layer of plywood first so i dont keep hitting holes with the fasteners), will the dewpoint be an issue and give me moisture inside my wooden walls? I’ve had no problems up to now (since theres no air barrier presently) but if i add the insulation and tape it properly does that put an air barrier in the wrong spot? There would be a furring layer for support and air flow between the insulation and the siding of course.
I’m in ontario, around zone 7, so its cold in winter and hot and humid in summer. (-35 C to +35 C)
Thanks.
GBA Detail Library
A collection of one thousand construction details organized by climate and house part
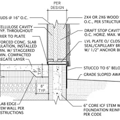
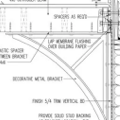
Replies
Terry,
Q. "If I put rigid insulation on the outside of the stackboard (probably with a layer of plywood first so I don't keep hitting holes with the fasteners), will the dewpoint be an issue and give me moisture inside my wooden walls?"
A. No. As with all types of wall construction, pay attention to airtightness, and you'll be fine.
Most species of coniferous wood runs about R1 to R1.3 per inch, so a full-dimension 4" solid wood wall is good for at least R4-R5 "whole wall", or about half the performance of a milled 2x4 / R13 wall.
Putting 3-4" of foam (any type) on the exterior would only help, not hurt the moisture content of the stackboard wood. In zone 7 as long as at least ~40% of the total R value is exterior to the wood, the coldest wood will have an average winter temp above typical ~+4C indoor air dew points, and won't grow mold. With 3" of EPS (R12.5-ish) and 4" of wood (R5-ish, worst-case) the cold side of the stackwall would be plenty warm in winter, and would not accumulate mold-potential levels of moisture.
There is no such thing as a wrong location for an air-barrier in a wall stackup, but it's possible to incorrecly place VAPOR barriers. Keep any interior side finishes at least semi-permeable to water vapor. (Latex paint is fine, vinyl or foil wall papers would court disaster.)
Thanks Martin and Dana for the quick replies. So essentially as long as i dont go putting a poly vapour barrier up willy nilly (inside or out), then this ought to be a pretty good solution. Good enough for me. Thanks!
Just a quick clarification question, as I'm actually at this point now in my renovation. I will have 2 layers of 2" thick rigid insulation (SilveRboard) on top of the plywood I put on the outside of the stackboard. First layer held on with 3" cap nails, second layer held on with... something. Either 5" screws with washers or just foamboard glue, until the strapping for the siding holds it all together with 6" deck screws.
Either way, do I need a housewrap product (typar) for a WRB on top of the taped up foamboard layers or is that overkill? I wasn't going to but im having second thoughts now.
And either way, how do I seal up the foamboard for the existing windows? Im having the windows reflashed, when the windows company puts new windows in elsewhere, but they will still be set back into the wood part of the house, not brought out into the foam. Is that a problem? Do I just rely on the window flashing to deal with it? housewrap around the windows only? housewrap everywhere?
thanks
Terry,
Every wall needs a water-resistive barrier (WRB). You can use rigid foam as your WRB if you want, or you can use housewrap as your WRB. Most builders find it easier to use housewrap as a WRB than rigid foam as a WRB.
It's essential for you to know what your WRB is, since your WRB has to be integrated with your window flashing.
If you are installing new windows, you have a great opportunity to do a good job of window flashing. Every rough opening needs to be flashed before the window is installed, and the window flashing needs to be integrated with your WRB.
I suggest that you read these articles carefully:
All About Water-Resistive Barriers
Using Rigid Foam As a Water-Resistive Barrier
Installing Windows In a Foam-Sheathed Wall
Hi Martin, thanks for the quick response.
Firstly these are not new windows, they are old windows in the old opening with new foam added on around them and new flashing. Just getting the flashing and the layering right is the challenge here.
Secondly I've got half of the first layer of foam on already, thinking the WRB would either be the foam or it would go on after. The 'innie' example in the last article (the only one I hadn't found yet) wants me to put the house wrap over the plywood (which admittedly makes more sense from the fastening perspective - I don't know how I would attach house wrap to 4" of foam), but I'm not sure how it works when I have a vendor coming to do the flashing partway through the process.
So to do it right would it be best to pull off my rigid insulation sheets, then house wrap it (with the loose flap above the window), then have the vendor show up and flash, with the understanding that 4" of foam is to go on later, then once they are gone fix the loose flaps of house wrap (if they didn't already) and put on the foam? Trimming it further I suppose is mostly cosmetic since its outside the WRB, yes? Or maybe the window vendor's sheet metal trim will handle that as long as they know what the foam thickness is. Would I place some offcuts on the bottom and sides for them to work with just so they can trim it out, then pull them off and put on the full sheets later? Maybe I just need to talk to the window vendor.
I don't particularly want to pull off 6 or 7 sheets of rigid and all those ring nails, but since its only the inner layer I guess it doesn't matter if it has a few more holes. And frankly I suppose I'm more likely to finish what I need in time for the vendor to come, since my task list changes from lots of foam plus house wrap to house wrap plus a little foam removal
Terry,
Your comments refer to a "window vendor" who will be coning to your house to install "sheet metal trim."
It's time to consult with this "window vendor" to determine how he or she will be flashing these window openings, so that your WRB installation will meet the vendor's needs.
In an ideal world, the vendor will be an expert at flashing window rough openings, and will be knowledgeable about methods for preventing water entry into walls, and will understand the need to integrate the WRB with the window flashing.
This is not an ideal world, unfortunately, so there is a high likelihood that you will be talking to sheet-metal person who knows how to use a brake to bend metal, but doesn't know much about preventing water entry or flashing windows. If you discover that your "window vendor" fits this description, you are not in a good situation.