How to Insulate/Ventilate Dormers and a Curved Roof

We are designing/building a cape cod-style home with three dormers and a curved roof. How do we insulate and ventilate the roof and especially around the dormers, or do we? Per the article below, it is suggested to bring the space behind the knee wall into the conditioned envelope and insulate up the rafter at the bottom of the roof. What happens at the top attic above the ceiling joist? Is this all conditioned as well or vented? Is the bottom half unvented and the top half vented?
Additionally, what do we do for ventilation/conditioning at the dormer roofs? They seems so small I don’t know how we will approach those.
For reference we are in climate zone 6/7 and aiming for 10/20/40/60 R-value goals. The side walls are 2×6 with 5.5” of closed cell and a continuous Zip-9 sheathing around. Budget is tight right now and cost is considered in any option.
First time post. Thank you in advance for any insight.
BD
GBA Detail Library
A collection of one thousand construction details organized by climate and house part
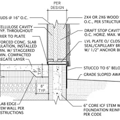
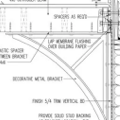
Replies
BD,
I think this may be one of those designs were you want to use closed cell foam or a combination of closed cell and air permeable insulation. Just may sure your rafters are deep enough to install the amount of insulation you will need.
If your budget is tight, the first to cut is the 5.5" of closed cell foam (btw, most installers don't do 5.5", the most you'll get is 5" since it is very hard to trim flat). The 5" of cc SPF will give you impressive center of cavity R values, but because of the thermal bridging of your studs it barely budges the assembly R value.
Assuming standard cladding plus drywall, the 5" of cc SPF+ZipR9 has an assembly works out around R28, same wall with R24 batts is and R26 assembly. Since you already need to tape ZipR, you don't need the air sealing ability of the SPF.
The better use of the SPF is in your roof plus dormers as Steve suggests. Since you have a complicated roof with knee walls and dormers, this is really the best way to seal it up. This will also make the mini attics behind the knee walls a conditioned space so you can run your ducting there or use it for storage.
If you want to save a bit of extra cost, only run the SPF up to ceiling of the 2nd floor. The top attic can stay vented and insulated with cheap fluffy insulation.
You can insulate the whole roof with combination of fluffy and batts but it will take a lot of care to ensure air barrier continuity as there are a lot of transitions.
Akos, thank you.
I don’t follow the math on the R-values. 5” cc SPF is 6/in so = 30 + ZipR9 = 39. That should be close to the goal of 40 or are you accounting for the thermal bridging somehow? My builder and architect have never done exterior insulation and are leery.
My architect and building science consultant were planning on a full unconditioned attic and not running any duct work through it. They said unvented attics were usually done in the south (I’m climate zone 6/7) and they were just going to use a lot of blown in cellulose. Given the limits of the dormers I think trying to maximize cc SPF would be helpful here but I don’t know how they are planning on it.
The transitions worry me. I would also love to keep a continuous envelope and not have the eaves constantly cutting through where the walls meet the roofs, but my architect and builder are unsure about this. For the main roof, is it possible to have a continuous envelope with, say, a zip system that then cuts across halfway up the roof so the bottom half of the top story is all conditioned and the top half not?
Thank you for your time.
The
You can browse through here for some of the assembly R values:
https://cwc.ca/design-tools/effective-r-calculator/
They don't have all options, but you can see how things compare. Thermal bridging does really hurt when using closed cell inside walls. Even though you are installing ~R32 of spf, you are only getting an R19 assembly.
This is pretty close to your assembly but has only R7.2 exterior rigid. With Zip R9 just add on the extra R1.8.
http://effectiver.ca/calculator/wall.php?id=2440
R40 walls make sense when you are using cheap and low embodied energy insulation such as cellulose. There is no ROI or CO2 benefit with an R40 SPF wall.
Your 2x6+ZipR9 is a great wall. If you skip the SPF and go with batts, the only thing you need is an interior warm side vapor retarder. Going up to Zip R12 would let you skip the vapor retarder but this is much harder to install as it require a special framing nailer that can shoot 4" nails.
My suggestion was to only go for an unvented assembly for the bottom half of the roof, only the section bellow the 2nd floor ceiling. You can carry the spray foam down along the roof and down to the top plate of the exterior walls to ensure air barrier continuity. You might need to staple some backing by the eves to contain the SPF if you have large truss members there.
It is very important to get that area well sealed both your floor joist as well as truss members intersect, making it a very complicated area. Make sure the SPF installer pays attention there.
It is also a good idea to do a preliminary blower test after the SPF is in and the 2nd floor ceiling vapor barrier is installed and fix any air leaks.
I don't know the best way to handle a complex roof like this -- other than avoiding it at the design stage, but that ship has sailed -- likely an unvented assembly would be the safest here. One other thing stood out to me in your post though:
>The side walls are 2×6 with 5.5” of closed cell and a continuous Zip-9 sheathing around. Budget is tight right now and cost is considered in any option.
You could definitely cut cost without sacrificing much else by going with a different type of insulation in the walls. Three of the big benefits of closed-cell foam are high R-value per inch, air sealing, and vapor impermeability, but these come at the cost of, well, significant monetary cost as well as high environmental impact. In your walls, the high R-value per inch is wasted due to the thermal bridging of the studs, and the air sealing and vapor impermeability are both unnecessary thanks to the Zip-R. (In your roof assembly, the vapor imperability of a layer of closed cell foam *would* be necessary, however.) Using mineral wool batts or dense pack or damp spray cellulose gets you an assembly R-value of something like R-27+/-; closed-cell foam gets you to maybe R-34+/- but at probably 4x the cost (you can play around with assembly R-values here: https://www.ekotrope.com/r-value-calculator).
EDIT: Looks like Akos posted just before me, with probably better assumptions on the actual achieved R-value in the walls. Another idea: Could you use some of the money saved by not using ccSPF in the walls to bump up to zip R-12, or change to regular sheathing plus continuous exterior foam?
I’d like to do R-12 and/or exterior insulation but my builder and architect have never done that and are hesitant. I have no idea how difficult that is.
Thank you for your time.