Minimal Thermal Bridging and Adequate Ventilation in Insulated Cathedral Ceiling

In march My wife and I plan to break ground on our home build. As a music educator/novice GC, I am trying to decide on our roof assembly. We are leaning away from SIPs and Nail base. We would like to use wool–batt or blown. We are building in Zone 6.
We will have exposed Post and Beam frame on the interior. Above that will be tongue and groove. It seems like most of the blog posts I’ve read on cathedral ceilings have to do with people that have made the wrong decisions or have a complicated roof. Our roof is 8/12 pitch over a 44Lx24W floor plan with 2 foot overhangs on all sides. No Skylights or dormers, planing on a continuous ridge vent.
The plan is to use rafters above the T&G and then fill the bay with wool. I am worried about condensation in an unvented cathedral ceiling. I think batts would allow for simpler ventilation (baffle-less?) in the rafter bay. Would I need to put some type of barrier on top of the wool to reduce convection?
My first question is if I have an adequate ventilation gap above the wool, below the sheathing, what ventilation do I need above the sheathing? (below the steel roof) Should I follow the double (90 degree) 2x furring that I have read about here and on 475, or would nailers parallel with the rafters be adequate?
My 2nd and main question is about how to mitigate thermal bridging through the rafters. The answers I have found here and elsewhere involve exterior rigid foam. (at thicknesses that would be similar to just using Nail base or SIPs to start within the first place -forgoing the rafters) Or spray foam inside the rafter bay. I really don’t want to use spray foam.
I am wondering if it is possible to use 1 1/2″ or 2″ EPS or another more stable rigid foam under the rafters-xps/polyiso. (I would be even happier if I could use a natural material-like rock wool, but I don’t think it would like the compression) I’m guessing that putting insulation under the rafters would break the thermal bridge before it makes it way to conditioned space and also not cause condensation on the sheathing? … if we can soundly attach the rafters.
So from inside- Post and beam frame>1x8T&G>6mmPoly>?rigid foam?>2x12ish Rafters and Wool batt>Sheathing> WRB> ?Nailers/furring?>steel roof
*sequence pieces in question marked with ?question marks?*
I will be having the engineer that works with the Timber framer draw up the final plan, I just want to be able to tell him exactly what we want the first time we talk.
Am I on the right track and asking the right questions?
Thanks for your time, GBA’rs,
Nels
GBA Detail Library
A collection of one thousand construction details organized by climate and house part
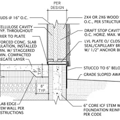
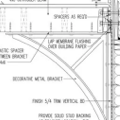
Replies
First, I'm a little confused because you mention you'll have a continuous ridge vent, but you're also concerned about condensation in an unvented cathedral ceiling? If you're putting in a ridge vent, you should be building a vented ceiling. There is no need for a ridge vent (or any kind of vents) with an unvented roof assembly.
That said, I wouldn't build an unvented roof with anything other than closed cell spray foam. There are others who have successfully built unvented roofs with other types of insulation, but I personally don't trust them. Since it sounds like you're probably planning on a vented roof assembly, this shouldn't be an issue for your project though, and you have a steep enough roof that the vent channels should perform pretty well.
Exterior rigid foam isn't useful if it will be installed ABOVE a vent space. If you're building a vented roof, then exterior rigid foam, at least as it's usually installed above the sheathing with another layer of plywood or OSB on top as a nailer for shingles or other roofing), isn't really an option.
The usual solution to convection currents in roof insulation is to just make the insulation thicker. If you're planning on using mineral wool batts (not sure if you're thinking of mineral wool or natural wool, but I have no experience with natural wool insulation), the higher density material also helps to minimize convection currents. Convection current issues are worst in walls anyway.
I think you're probably planning on a vented roof assembly. Code minimum vent channel is 1", but I'd try for at least 1.5" and ideally 2" for a little extra safety if you can make it fit. Put your batts under that, filling to whatever is needed to get the overall roof up to at least code minimum (you didn't mention your rafter size here, which will dictate how much insulation you can fit in there). I'd use foil-faced polyiso under the rafters with seams taped. This will give you the thermal break you're looking for, and will also give you the air barrier that you NEED above your T and G ceiling to avoid moisture issues in the roof assembly. The vent channel will take care of any moisture that might find a sneaky way in, so you should have a pretty safe assembly here. Since the interior polyiso isn't there for dew point control, you aren't locked into any particular thickness -- even 1/2" polyiso will work, but you only get a bit shy of R3 that way. I'd probably go with 1" polyiso for R6, or thicker if you need to get the overall assembly up to code minimum due to the rafters being too shallow for thick enough batts. Remember that over about 2" or so it can be tricky to set fasteners to support a finished ceiling beneath the polyiso.
You can also try things like dense pack cellulose here with netting, but you need something to keep your vent channels open so you have some added complexity if you try that material. Batts come in specified depths, so you don't have to worry about overfilling the cavities and blocking your ventilation with them.
Bill
Thanks, Bill for the tips! And Yep, I’m wanting tips on a vented ceiling. Above I was stating that, in general, I am worried about an unvented cathedral ceiling- so I don’t want any tips on that course of action.
Great, Your telling me I can put foam under the rafters and it’s not to hard to fasten the rafters so long as the foam is 2ish inches or less.
Is polyiso the only way to go? I know it is on the more stable end of foam products, but also less environmentally friendly.
Polyiso is the MORE environmentally friendly rigid foam. XPS is the worst in that regard. EPS is in between, but less R per inch, which means more energy use over time in your home which is something else you should be considering when considering green products. I've often said that you need to look at the entire system, and not just any one particular piece, when trying to build a green home. This means factoring in product lifetime concerns as well, such as energy savings over the life of the structure.
In your particular case, it's very important that you have a good air barrier under that tongue and groove ceiling, and polyiso is the easiest to seal since you can easily tape the foil facer and get a reliable long-term seal that way. It is much more difficult to get a reliable tape seal to EPS or XPS foam.
Bill
So Polyiso IS the best option, foil facing down toward interior? Thanks
Foil-faced polyiso typically has a foil facer on BOTH sides, so which way it's installed doesn't matter much in that regard. SOME polyiso is marked which side goes "up", which I've always thought is for "top of the roof" applications, but I've never worked with it for that so I can't be certain. In your case, you won't have an air space, so no radiant barrier benefit, and you won't have any force from things like guys walking around on top of it, so if one facer is tougher than the other, that doesn't matter much either.
Bill
The big problem with post and beam is continuity of the air barrier across the timbering. This is something you have to design in from the start. Even a small gap say 1/16" of an inch times a couple hindered feet of timbering makes for a very large hole in your envelope. This is very common in these types of buildings and can create problems with condensation dripping down your ceiling down the road.
I would put 1/2" CDX flanges over your timbers and extended them say 2" on either side before any exterior walls or roof go up. You can then tape your air barrier to this (1/2 drywall or 7/16 OSB is the cheapest air barrier) for a simple and solid connection.
A simple check or air barrier continuity is the pencil test. Take any cross section of your house and be able to draw a line along the air barrier from foundation to foundation without lifting the pencil.
For your roof, if you want less thermal bridging use I-Joist instead of dimensional lumber. Because of the thin OSB webb these are significantly better. Alternatively you can use rigid insulation as your warm side air barrier instead of drywall or OSB. You can easily nail up T&G through 1" of foam with 2.5" nails.
So this tip is about the wall build? Let me see if I understand you correctly, air barrier continuity across timber is tough because of timber shrinkage? or something else?
This issue is for both walls and ceilings. Walls are generally a bit more forgiving as air leaks there create less issues. All these air leaks add up on energy cost and comfort.
The way typically timber framed houses are built is that timbering is put up first then stud walls/roof is built over it. Finally the interior finish is applied. Typically, this just means the drywall is butted up against the timbering and mudded. This means the interior surface (warm side air barrier) is interrupted by the timbering. There is no practical way of air sealing this joint, it will always crack from the movement of the structure just from seasonal changes.
My suggestion is to put a layer of plywood behind the timbering which your warm side air barrier can be connected to. Even if the timbering swells and shrinks from moisture, the plywood will stay put and won't effect this joint.
Thanks for the clarification! Great Idea!
What you described is how we plan to build the exterior walls- Studs and rafters, after we build the post and beam frame. I still haven't quite wrapped my head around the sequence for the stud walls/ceiling. I like this plywood flange idea. I assume it will make all the connections concerning the envelope more stable and easier to attach.
Deleted