How to stop a Cathedral ceiling from sweating

Newly constructed home in upstate New York (Cold Climate) with cathedral ceilings throughout. R38 paper faced batts with Sheetrock and T&G pine cover the entire ceiling. After the long winter months have past the warmer weather causes water to come streaming down the inside of the valleys and down the walls for at least 5-6 hours. A roofing contractor said it was caused by ice damning so I replaced the shingles, s&i guard etc. in both valleys and I had a leak this past Sunday afternoon (no rain or snow). I don’t know what to do besides rip down the ceiling and spray foam. Would a bad insulating job at or near the valley allow enough water diffusion to cause this kind of leak? I also have can lights which may be contributing to the problem, however, I have known leaks above and beyond the lights. In the one spot where I was able to access the bottom of the roof sheathing it was wet in both cavities. On average the RH in the peak is between 45% and 55%, a little high but I don’t think it is the cause.
I also installed styrofoam baffle vents in the valleys from the ridge to the LVL valley rafter, which if anything is probably hurting the situation but I really don’t know.
I’m beside myself, if anyone can help it would be greatly appreciated.
GBA Detail Library
A collection of one thousand construction details organized by climate and house part
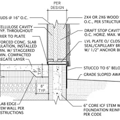
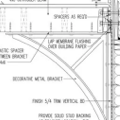
Replies
Scott, are you in the Adirondacks?
Ajbuilderny at gmail dot com
Certainly sounds like a condensation problem to me. Curious that it doesn't happen in the colder weather--perhaps the drier air reduces condensation potential, or the condensate is freezing on the underside of the roof. You need to figure out where all the air leaks are into your ceiling, and stop them. The can lights are almost un-solveable in my experience.
I 'm in the catskills
I believe its condensating all winter long and freezing on the under side of the sheathing, the first warm spring day causes it to thaw an leak 4 months of condensation at once
Scott has the right answer. This phenomenon is common. The condensation builds up as ice; warm weather causes the ice to melt.
The problem is an imperfect air barrier. Recessed can lights obviously contribute to this problem. Does the roof include a ventilation channel? The valley is obviously difficult if not impossible to vent, so using fiberglass batts was a mistake.
The ridge is vented using a cobra vent system, I just recently sealed off the section above the valley as it was not doing anything or at least I don't think it was. The cavities are vented with styrofoam baffles, even in the valley.
Scott,
You're not getting any airflow above the insulation in the valley, obviously. Fiberglass batts are always risky in a cathedral ceiling, and only work if the air barriers are perfect and there is a good vent channel above.
More information here: How to Build an Insulated Cathedral Ceiling.
Thanks for the link, very informative. Knowing that I constructed and insulated my ceiling incorrectly what are my options if any?
Scott,
In your case, I recommend an unvented roof with a tight air barrier. That means you either need to install rigid foam on top of your roof sheathing -- a solution that requires the removal of the existing roofing -- or you need to install spray foam against the underside of the roof sheathing -- a solution that requires the removal of at least some of the existing ceiling.
You might try a halfway measure: remove all your recessed can lights, and seal up the holes to make them airtight. Then you can install surface-mounted lighting fixtures elsewhere.
Should the insulation on the exterior of the sheathing be foil faced or not? If faced, which direction should they be installed? I don't want to create a double vapor barrier!
If I were to install foam board on the exterior of the roof sheathing, could they be installed over the existing shingles and then shingled over?
Q. "If I were to install foam board on the exterior of the roof sheathing, could they be installed over the existing shingles and then shingled over?"
A. No. The shingles should be stripped. Then rigid foam should be installed, followed by another layer of sheathing. Alternatively, you could install a layer of nailbase (rigid foam with OSB adhered to one side). If you go this route, don't forget to seal the openings and the exit channels of the ventilation chutes.
Q. "Should the insulation on the exterior of the sheathing be foil faced or not?"
A. It doesn't matter. Either type is fine.
Q. "If faced, which direction should they be installed?"
A. It doesn't matter; either way is fine.
Q. "I don't want to create a double vapor barrier!"
A. Hopefully, you don't have an interior vapor barrier -- only a vapor retarder. Regardless of your desires, the foam layer will be a vapor retarder. That's fine, so don't worry about it.
I appreciate your input, I wish I would have found this site a few months ago it would have saved me a ton of headaches. But I do have a few more question if you don't mind:
- If I understand your article correctly I need to install enough rigid foam insulation to create an exterior R value of 25 or better ( Upstate NY) in order for this method to work?
- Also I don't have to create air chutes on the exterior of the foam , do I?
You are correct I only have an vapor retarder on the face of the existing insulation, not a barrier.
Scott,
1. Yes, in your climate you need at least R-25 of foam above the sheathing.
2. Ventilating above the foam is optional, but many people like the idea because it reduces the chance of ice dams. You can buy nailbase panels with integrated ventilation channels between the top of the foam and the OSB, if you want to go that route.
When my roof was originally installed I had the GC cover the entire thing in Ice and Water guard, do you think this could be contributing to the sweating of the sheathing? Is it acting as a barrier and not letting it breathe?
Scott,
It's possible -- although not much drying to the exterior, if any, happens when your roofing consists of asphalt shingles. (The question of whether wind action can allow some drying to the exterior through asphalt shingles is a matter of debate among building scientists.)
In general, you made several decisions that, working together, pushed your roof assembly in the direction of failure:
1. Your roof shape is not conducive to venting because of the valleys, and yet you chose a type of insulation that needs venting.
2. You chose a type of ventilation baffle that isn't air tight.
3. You chose a roofing underlayment -- Ice and Water Shield -- that is vapor impermeable, and you installed it over your whole roof.
4.You didn't create an interior air barrier, and you punctuated your ceiling with leaky recessed can lights.
5. You chose a type of insulation -- fiberglass batts -- that is notoriously permeable to air flow.
If you had made only one of these errors, your roof might be OK. But taken together, this collection of errors was a recipe for failure.
I also did some quick calcs using the unvented roof assembly (R25 rigid foam followed by an additional layer of sheathing etc...) and my numbers suggest that the inside temp of the sheathing will still be below the dew point in the winter months. I neglected the thermal resistance of the interior finishes, exterior cladding and the effects thermal bridging, if I reconstruct my roof I want to guarantee success. Is this issues being addressed with the vapor retarder of the fiberglass insulation?
Scott,
I'm not sure which method you used to perform your dew point analysis. Here's more information on that topic: Are Dew-Point Calculations Really Necessary?
I'm fairly you sure you either made an error in your calculations or used a dew-point calculation method that is too conservative. Trust me: if you install R-25 of rigid foam on top of your roof deck, you won't have dripping ceilings, unless you get a roof leak.
If your roof sheathing accumulates a little moisture during the winter, it will still be able to dry to the interior, as long as you don't have any interior polyethylene.
I used the exact method as described in your article.
Ave outdoor temp 23 F
Inside temp 70 F
R cavity 38
R sheathing 25
R total = 63
TS = 70-47(0.603) = 41.66 F
From Chart @ 45% RH and 70 F the dew point is 46.4 which is greater than TS
It's not that I don't trust you its just that I want to make sure that what I'm doing is correct.
Scott,
Looking at your numbers, the main reason I think you'll be fine is that your R-38 fiberglass layer won't keep your sheathing as cold as you think -- because it isn't really performing at R-38, due to all of the air leaks through it and (probably) around it.
I see your point, thanks for the input. I'll probably attempt to tackle the roof in the spring. I'll be sure to take pics and post the outcome, Thanks again.
Would it be possible to remove the existing shingles, sheathing, vents and fiberglass insulation from the exterior side of the roof and spray the cavity full of closed cell foam? I would then re plywood and shingle the roof.
Would this be a feasible solution to my problem?
Scott,@ post #21......I am not sure that it would be the best solution...but it has been done
see Peter Yost's comment #4 at this blog
https://www.greenbuildingadvisor.com/blogs/dept/musings/how-build-insulated-cathedral-ceiling
Scott,
Yes, the work you describe is feasible.
Scott, hopefully you got your problem solved. My situation is almost identical except I do not have the sheetrock under the T&G. Please refer to my post on 1/27/13. I am wondering how you fixed your situation.
(Note to GBA - if Scott is not still active on this site perhapes you can tell me what he did or put me in contact with him)
What if you were to install lets say a waterproof material such as sheet vinyl made for flooring, but you glued it to the ceilings onto the drywall. My thought is that would seal out the air from getting thru the drywall and into the cavity. I actually used this method to make a tub surround in a rental. I glued sheet vinyl that looked like tile to the drywall around the tub and it looked great too. The new vinyl they make now looks like real wood flooring. Just an idea that might solve these problems of sweaty ceilings without tearing apart the roof.
Brian,
This is an old thread, so it's probably too late to provide advice that is useful to Scott Davis. But there are several objections to your suggestion:
1. There is no drywall on the ceiling to glue the vinyl flooring to, as you suggest. And if you think that drywall on the ceiling is a good idea, why install vinyl flooring? Just make the drywall airtight instead.
2. No one wants to look at vinyl flooring on their ceiling.
3. Your suggestion doesn't address air leakage through the recessed can lights.
4. Even if there were no recessed can lights, gluing vinyl flooring to the ceiling wouldn't necessarily be airtight because of air leakage at the perimeter of the ceiling.
5. Your solution still leaves a poorly insulated ceiling assembly that will contribute to high energy bills.
My suggestion was more a question if it would work to stop the sweating if you used an airtight and watertight membrane on the inside surface (such as vinyl flooring but it could be anything, maybe even ceramic tile that looks like wood which is very popular now). Or would you still get sweating on the surface of the membrane due to the temperature and dew point etc? I read a post where you said it was very difficult to make drywall airtight (not just can lights). So this is not really a suggestion its a question of what would happen if all the surfaces on the inside were perfectly sealed would this sweating still happen due to air getting into the cavity from other places like soffits etc above this theoretical perfectly sealed ceiling?
Brian,
The answer to your question is that the moisture transport mechanism at work here is exfiltration, for the most part, with a very small contribution from vapor diffusion. So in theory, a perfectly airtight ceiling will prevent condensation on the underside of the roof sheathing. Perfectly airtight ceilings are quite difficult to achieve, however, unless you are talking about new construction.
It's quite possible to make the field of a drywall ceiling airtight, as long as there are no penetrations (can lights, for example) or partition top plates. The tricky air flow paths are at the perimeter of the ceiling, through partition top plates, and through electrical and plumbing penetrations.
Solving this type of problem by recommending that ceiling leaks be tightened up almost never works, because of hidden air flow pathways.
Even if an airtight ceiling is achieved, this solution doesn't solve the basic thermal performance problems -- the ones surrounding poorly installed fiberglass batts subject to wind-washing from ventilation air and thermal bridging through the rafters.
Deleted
(1) What kind of insulation do you pack the rafter bays with? All the advice from GBA experts says that only insulation that will work in unvented cathedral ceilings is an air-impermeable one of closed spray cell foam.
(2) I have an attic ventilated by gable-end vents, minimal soffits with no vents, no ridge vent, and > 18" of blown in cellulose. I want to cathedralize the ceiling but want to avoid foam in the rafter bays.
Deleted
Joel,
1. This is a 7-year-old Q&A thread. I'm not sure why readers are reviving it.
2. The original poster, Scott Davis, described the insulation between his rafters as "paper faced batts." Sounds like fiberglass insulation to me.
3. For more information on this issue, see these two articles:
"How to Build an Insulated Cathedral Ceiling"
"Creating a Conditioned Attic"
Deleted
Frank Lloyd Wright's houses are also legendary for water and structural problems, though I hope the people at Taliesin have learned something about engineering and building science in 100 years. You may have wasted some time trying to answer the issues raised in a 7 year old thread, but if you want to learn more about the building science, the links Martin posted, and many others on this site provide excellent guidance.
Deleted