I am doing exterior insulation on an existing building in Western Massachusetts. Two layers of 2 inch foil faced insulation,

about a r-28 then vertical strapping and siding. The original studs are full 4″ with 1″ board sheathing. The existing plaster wall have been gutted so the bays are open. My question is should I insulate the existing studs? I was trying to avoid fiberglass and was thinking of wet spray cellulose. The attic floor has 2 layers of 2″foil faced and layer of plywood for a new attic floor. The attic floor joists are 6″ and I was thinking of spraying the ceiling also. The house will have a hrv and I plan to do a blower door test. before we close in the walls. Any thoughts from the experts. Thanks
GBA Detail Library
A collection of one thousand construction details organized by climate and house part
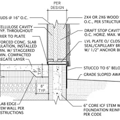
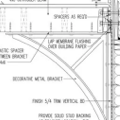
Replies
If you're opening up the walls, then certainly insulate that space. The sheathing will remain above the dew point with that much "outsulation" so there's no worry about condensation as long as you're controlling the indoor humidity with general ventilation and source removal.
Cellulose is far superior in every way to fiberglass. You can use damp-spray as long as you give it time to dry before closing in, but you might consider a dry-blow behind insulweb. Do not use an interior vapor barrier, since your wall cannot dry at all to the exterior and it's essential to allow it to breathe to the interior. Same with the ceiling. Just make sure the ceiling plane is air-tight.
Many hardwood installers in my area are using rosin paper under hardwood floors instead of the roofing felt.
THats a lot of labor and materials.. I would suggest a few options- SPray closed cell foam into the wall studs (r-value of aproximate 7 per inch) then add 2" polyiso board on either the inside or the outside.It would keep the cost down and do a better job. 4 inchs on the outside makes a nightmare for siding and trim. Put the foam board on before spraying the foam would seal all the exterior sheathing seams and bond everyhting together. Thats what I would do and have done.
Dan- A+Energy
Sprayed closed-cell (2 pcf) polyurethane foam offers about R-5.9/inch (not the 7 claimed by Dan). Only foil-faced polyisocyanurate has that high an R-value.
And I would certainly advise against using vapor impermeable spray foam in the stud cavities and trapping the sheathing with foil-faced foam board on the outside. That would be a double vapor barrier and create a high probability of moisture problems in the event of a leak through poor flashing or other failure point.
Also, putting most of the insulation in the stud cavities would not guarantee that the sheathing remained above the dew point, which could create moisture problems if there should be any shrinkage or separation of foam from framing. Using less exterior insulation would reduce the quality of your thermal break, as well.
Reading all the horror stories here... makes me remember a sunroom remodel... 1" foil foam exterior insulation over 2x4 studs and fiberglass insulation infill. I had to reframe the walls for new 4 season windows the homeowner ordered too big... Lucky for her. Upon opening up the wall, I handed the studs to her... completely rotted out, gone... just wet sawdust. All that was holding up this wall was tiny parts of the studs... and the sheathings inside and outside... Wow...
Walls need to breath. Now that I remember this project.... I may never flash and insulate. One or the other seems much more sane.
aj
I tried to source wet spray contractors and haven't had any luck so I'm going to go with unfaced fiberglass. I was thinking of wet spray cellulose because it seemed like a practical application since with all the additional framing and straightening I had to do with a 1918 balloon framed house, all the bays are untypical sizes.
I went with the exterior insulation because I felt that it offered the most practical and effective way to insulate an existing 2x4 wall house. By using the exterior foam the sheathing and framing will stay warm and dry. The procedure is straight forward and not complicated. If you are smart with your housewrap and vycore it is not difficult to create a water resistant exterior barrier to rain and moisture. The vertical strapping creates a rainscreen for the siding which allows it to dry out when it gets wet. This is the part of the wall that "needs to breath". With no interior vaper barrier the wall can dry to the inside.
Also this method was great for the timing of this renovation. We were able to complete the exterior insulation and siding before the cold weather set in. With the new boiler in place and the first floor baseboards in place (very little because of the low heat loss) the workplace was comfortable for the subs to work. Even with the temp in the single digits. They were all amazed how well the insulation worked. No drafts or cold spots. I had thought about spray form but had concerns about the quality of istallation (everybody and their brother now installs foam) and thermal bridging of the framing. So I more than pleased with the results and would recommend it. Just be sure to follow the 1/3 2/3 r-value rule.
To A from upstateny I think your rotten stud problem was not caused by the exterior insulation, more likely poor exterior detailing that allowed water to infiltrate into the stud bays and then the foam did not allow it to dry out quickly enough to prevent rot. Wait I guess you're right the insulation caused the problem. Simple answers to complicated problems are easy to vocalize but seldom correct.
Gerry... you may be right, time has passed... water may have been able to enter edges of foam, in window areas.. also.... there were a roomful of plants, watered often and lots of sun to keep all that water coming and going. My idea at the time was indoor moisture driven through the fiberglass faster than it could get back out. I bet there would have been less rotting if the stud space was empty and there was just the foam.
And as to complicated, I wouldn't dare build a pool building enclosure without some engineered plan with oversight along with them taking responcibility for the projects outcome.
aj
Gerry,
It's going to be a PITA to fill irregular framing spaces with fiberglass batts. I would suggest looking into dry cellulose blown behind insulweb. Not only will you get a superior thermal barrier, but the cellulose is insect-proof, rodent-resistant, mold-resistant, fire-resistant, and can safely absorb and desorb moisture while protecting the framing from saturation.
I'm in a similar situation...I have a house in western mass built about 1900's that I'm gutting and I want to re-insulate. I'm debating between polyisocyanurate, Spray Polyurethane Foam, cellulose, or fiberglass. I'm concerned with the potential fire issues with cellulose, environmental issues of fiberglass, and chemicals associated with polyisocyanurate and Spray Polyurethane Foam. What do you recommend I use? Also, please consider there are not many green builders in our area so finding supplies might be difficult. If you have any tips on finding a supplier that would be much appreciated. In addition, what do you think the cost range is for whichever ones you suggest? Thank you so much for your help.
Melissa,
I don't think it's accurate to say that "there are not many green builders" in western Massachusetts. In fact, your area is a hotbed of green building activism. I think if you do some Googling and make a few inquiries at local lumberyards, you'll come up with many green builders.
When it comes to choosing insulation, remember that all of these products are green, because they all serve the important function of reducing energy use for the life of the building. If you haven't seen them yet, you may be interested in visiting these GBA pages:
https://www.greenbuildingadvisor.com/green-basics/insulation-overview
https://www.greenbuildingadvisor.com/green-basics/insulating-roofs-walls-and-floors
https://www.greenbuildingadvisor.com/green-basics/insulation-choices
https://www.greenbuildingadvisor.com/green-basics/batt-and-blanket-insulation
https://www.greenbuildingadvisor.com/green-basics/blown-or-loose-fill-insulation
https://www.greenbuildingadvisor.com/green-basics/rigid-foam-insulation
https://www.greenbuildingadvisor.com/green-basics/spray-foam-insulation-open-and-closed-cell
Melissa,
I have to completely disagree with my colleague, Martin. Saving operating energy is perhaps the least important element of "green". There is also the embodied energy and environmental life-cycle impacts, recyclability, the toxicity to both humans and the rest of the biosphere, and the overall impact on the function of the home and occupant comfort.
Cellulose insulation, treated with non-toxic borate fire retardant, is perhaps the least flammable of all insulations (other than cementitious materials). The borates also kill most household insects, repel rodents, and resist mold growth. Additionally, cellulose has one of the highest sound attenuation coefficients, resists air movement, and is 85% recycled material. It is one of the greenest of all building products commonly available and one of the best manufacturers of cellulose insulation is National Fiber in Belchertown MA (available at most lumberyards and used by most insulation contractors in your area).
It is not the ideal insulation for every project, but it is far more "green" than almost any other option.
Melissa... Robert didn't totally answer your question. If you like the idea of cellulose... I agree with Robert that it is a good green safe economical choice for you. To insulate your walls more than they are... you could build out your walls so they can hold more insulation to the interior. That is a job someone like myself could do for you on a contract basis... and someone there could too.
aj